PEM researchers analyse BYD and Tesla batteries
As to the motivation behind the analysis, the PEM writes that there is generally little detailed data and analyses on modern electric vehicle batteries. “Both players have only ever revealed little data about their batteries, so the cellsʼ mechanical structure and most of their properties have remained hidden to date,” says PEM Director Professor Achim Kampker on the choice of the two test subjects, Tesla and BYD.
The results published on 6 March in the journal Cell Reports Physical Science show, among other things, that Tesla’s 4680 cells focus on high energy density, while volume efficiency and more cost-effective materials are more important for BYD’s blade cell. According to the study, BYD’s battery is more efficient because it enables simpler thermal management.
For the analysis, the researchers at RWTH examined the mechanical construction, dimensions and electrical and thermal properties of the cells as well as the exact material composition of the electrodes. The costs of the cell materials and the processes used for assembly were also determined. For the sake of completeness: The Tesla cell was purchased by the chair from Munro & Associates, which originates from the teardown of a Tesla Model Y 2022 with the structural battery pack – due to its age, there were slight uncertainties regarding the exact State of Health (SoH) of the cell. The BYD Blade cell was imported online from a Chinese dealer with a SoH of 100% (in 2023).
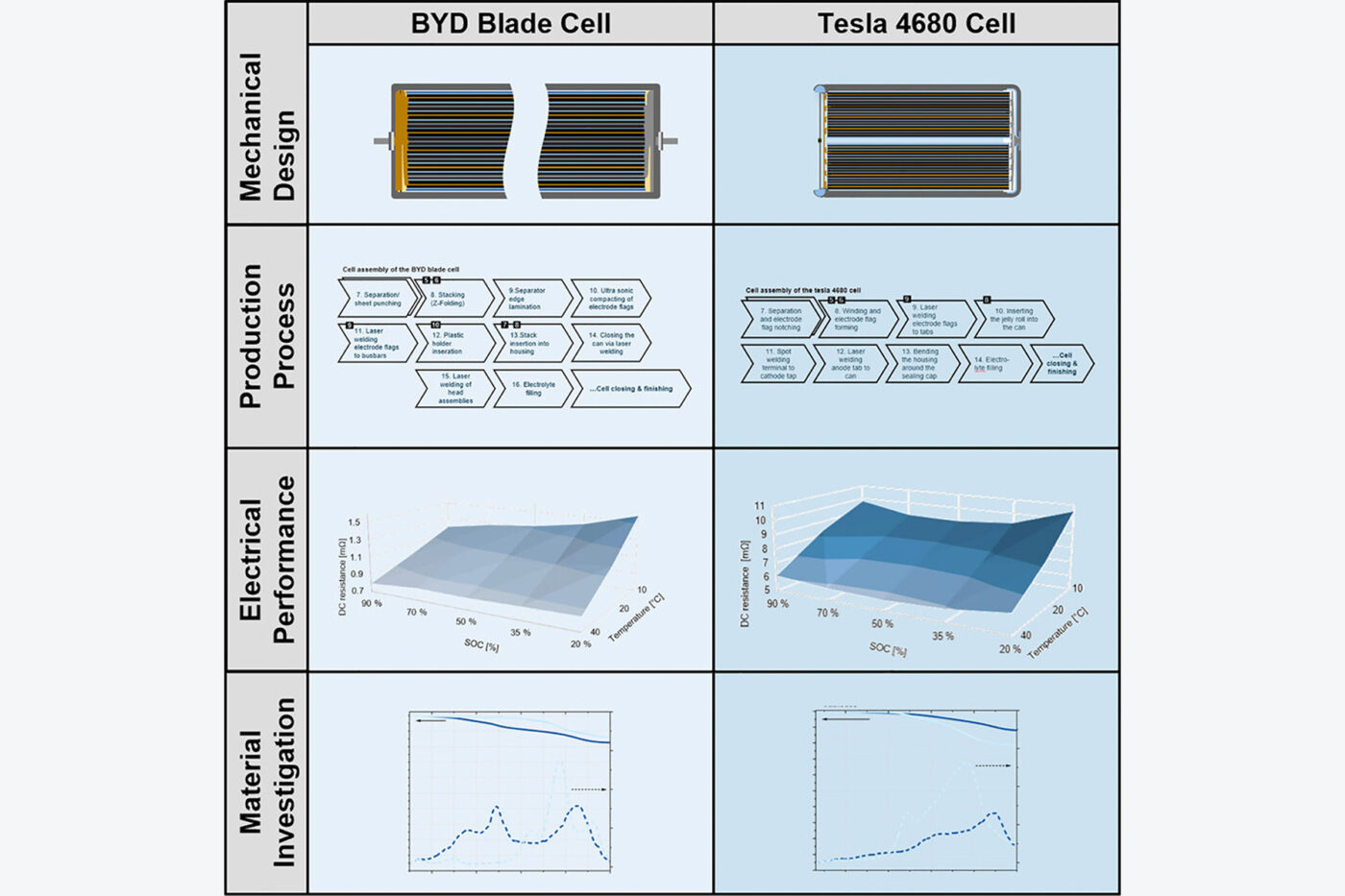
What the chair describes as “surprising results” is explained by PEM lead member Professor Heiner Heimes: “We were surprised that there is no silicon in the anodes of both batteries – especially in Teslaʼs cell, as silicon is widely regarded in research as a key material for increasing energy density.” The analysis also provides concrete figures on energy density: 160 Wh/kg and 355.26 Wh/l were determined for BYD’s LFP cell. Tesla’s 4680 cylindrical cell with NMC811 chemistry thus achieves 241.01 Wh/kg and 643.3 Wh/l at the cell level. The volumetric energy density, in particular, clearly demonstrates Tesla’s focus.
BYD’s blade cell is already characterised by its special and eponymous size, as the blade-like cells extend across the entire width of the battery pack – they are prismatic cells. Specifically, the Aachen-based company measured 90 millimetres in height, 14 millimetres in width and an impressive 965 millimetres in length – almost a metre. At Tesla, the cylindrical cells have increased in size over the years – from the 18650 cells in the early Model S to the 2170 cells in the Model 3 and Model Y to the 4680 cells with a diameter of 46 millimetres and a height of 80 millimetres. ‘In recent years, there has been a trend towards cells with larger dimensions, as this increases the energy content per cell produced and reduces integration complexity at the system level,’ says the study.
Tesla 4680 | BYD Blade | |
---|---|---|
Dimensions | 46×80 mm | 965x90x14 mm |
Weight | 355 g | 2,700 g |
Volume | 133 ml | 1.216 ml |
Volumetric energy density | 643.3 Wh/ml | 355.3 Wh/ml |
Gravimetric energy density | 241.01 Wh/kg | 160 Wh/kg |
Nominal capacity | 23.125 Ah | 135 Ah |
Nominal energy | 85.56 Wh | 432 Wh |
Nominal voltage | 3.7 V | 3.2 V |
Voltage window | 2.5-4.3 V | 2.6-3.65 V |
Another similarity between the two batteries that the Aachen-based battery experts did not expect is the way in which the cells are assembled. For example, their thin electrode foils were joined together using the still-unusual laser welding method instead of the ultrasonic welding method commonly used on the market.
However, the differences outweigh the similarities; unsurprisingly, there is talk of “highly innovative” and “fundamentally differently designed” battery types. According to the report, there are “significant differences in the speed at which they can be charged or discharged in relation to their maximum capacity.” According to the study, BYD’s blade cell is based on a special method in which the anodes and cathodes in the electrode stack are fixed in an ideal position in relation to each other by laminating the separator edges. The Tesla battery, meanwhile, uses a new type of binder that holds the active materials in the electrodes together. And: “Although BYD’s cell is much larger than Tesla’s, the proportion of passive cell components such as current collectors, housings, and busbars is similar,” says Kampker.
The safety systems of the housings are also different. Unlike the aforementioned 18650 and 2170 cells from Tesla, which are installed horizontally in the pack, the 4680 cells are installed upright. This means that the cell vents downwards in the event of a fault. The blade cell, on the other hand, vents to the side (like the horizontally mounted Tesla cells). In both cases, the hot gases are vented away from the passenger compartment, but in the case of the 4680 cell, they are also away from the electrical contact system. Depending on the position of the cell in the pack, this could be damaged if it is vented to the side. While Tesla uses the entire container of the cell as the negative pole, BYD insulates both poles from the container.
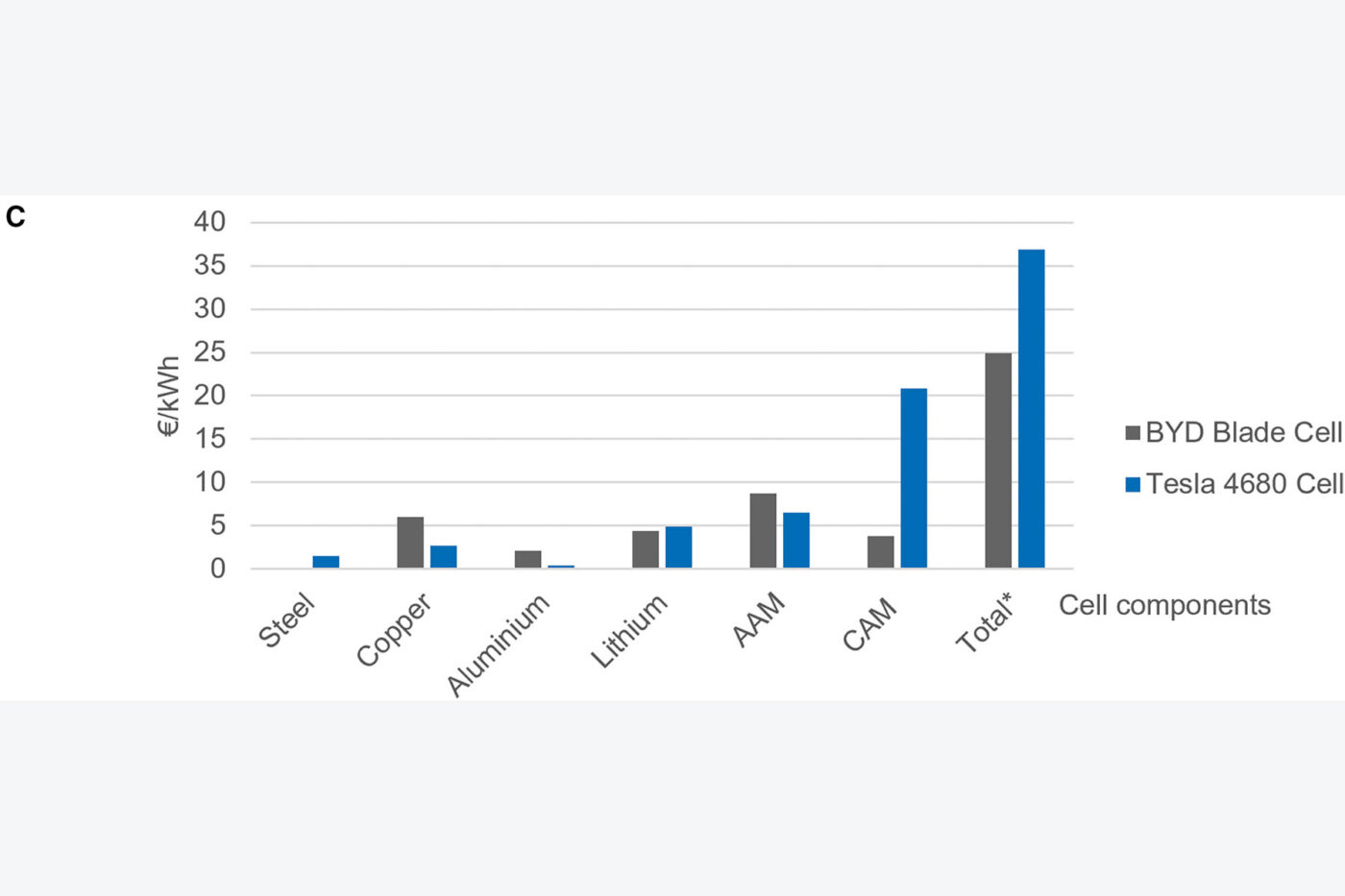
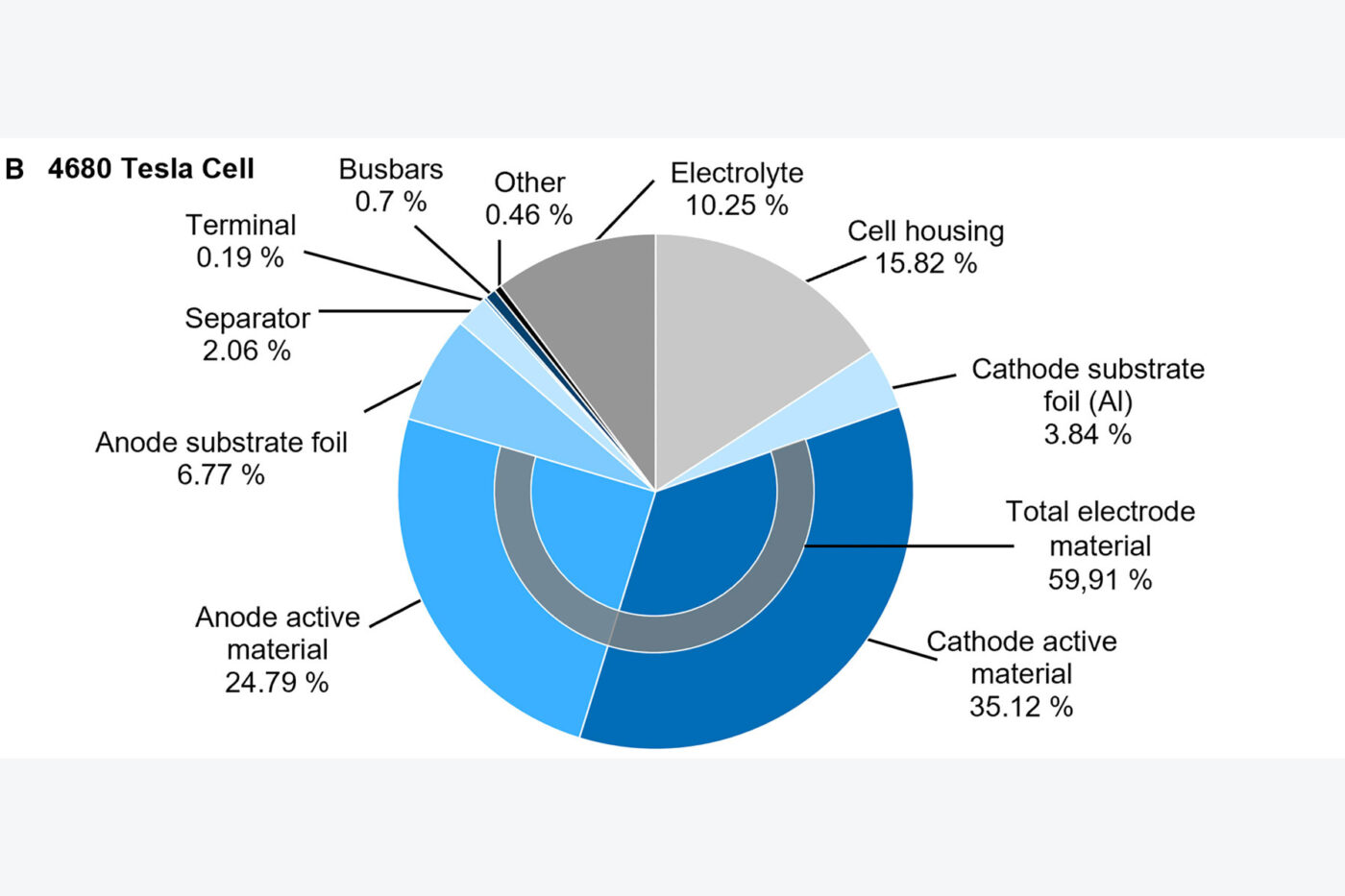
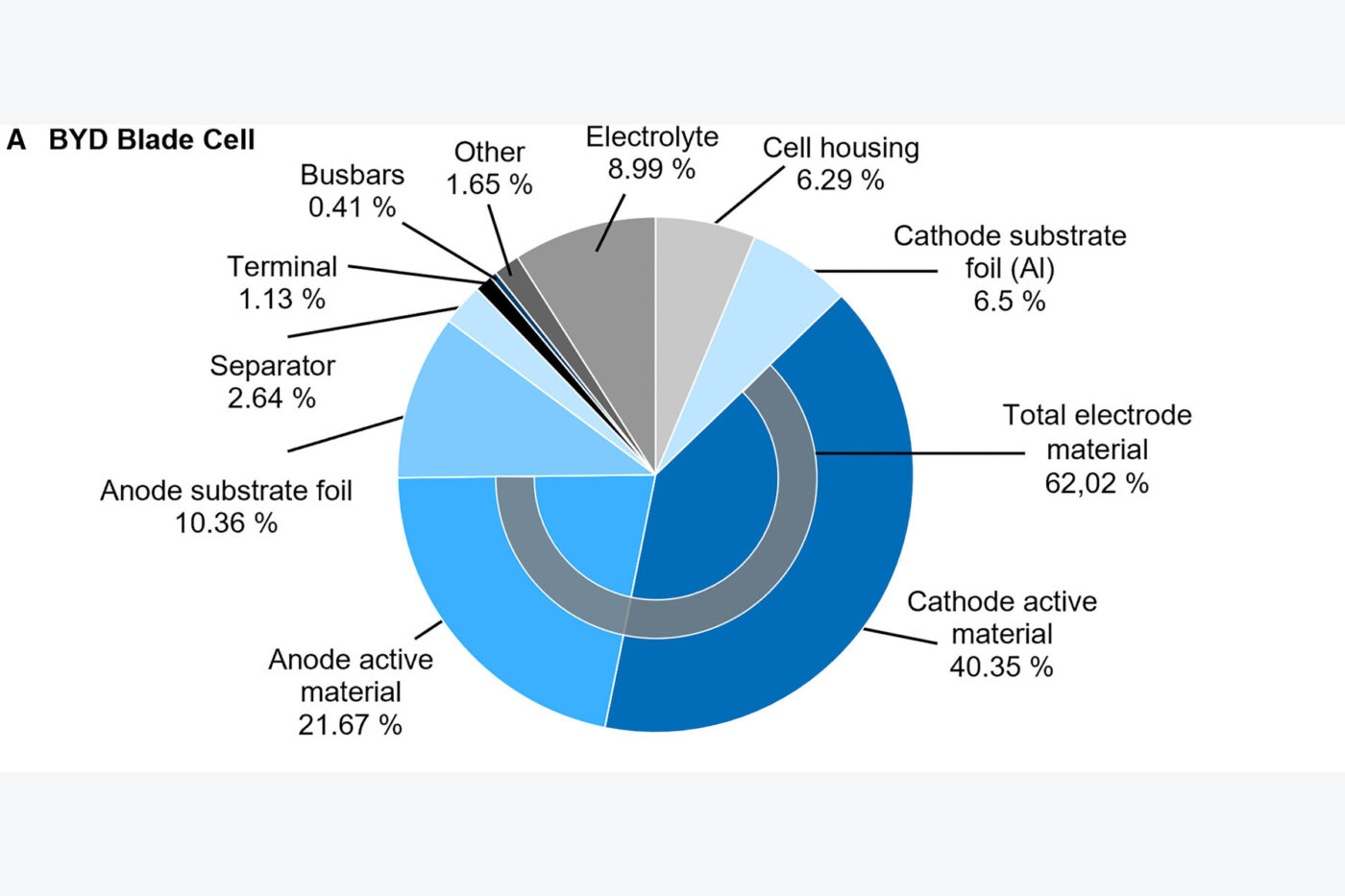
In order to determine the important factor of cost, each component of the cells was analysed and weighed separately. At around 60 per cent, both cells have a similar proportion of active material, but in different ways: the steel housing of the cell at Tesla weighs more than the aluminium container at BYD, but this weight advantage is lost again ‘due to the high weight of the substrate film’ of the blade cell. The material costs were estimated using freely available material prices as of August 2024. As a result, the BYD cell is more than ten euros cheaper per kilowatt hour at the current price level – at €25/kWh compared to over €35/kWh for Tesla. The difference is mainly due to the different cathode material – the BYD cell is even slightly more expensive for the anode and the copper used.
The study was produced with the support of Münster Electrochemical Energy Technology (MEET) and the Fraunhofer Institute for Ceramic Technologies and Systems (IKTS) as part of the FoFeBat2 research project and is available as a free download. In it you can read further details, for example, on the electrode arrangement in the cells, the contacting and also details on the electrodes themselves (such as the thickness of the coatings) as well as the expected process sequence during production.
rwth-aachen.de, cell.com (study as PDF download)
0 Comments