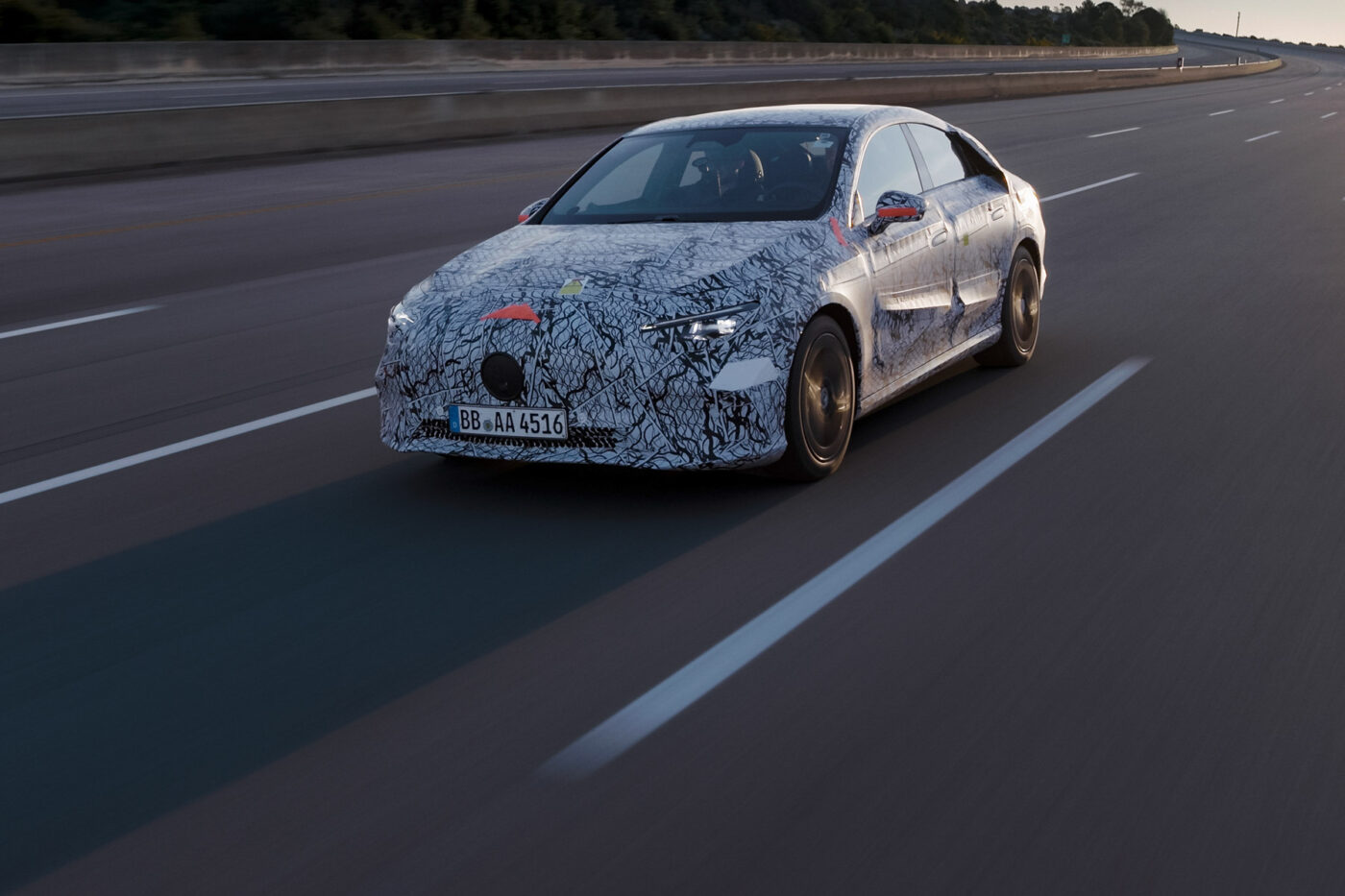
Inmersión profunda MMA: Cómo Mercedes quiere ganar puntos a la eficiencia con el CLA eléctrico
Es cierto que Mercedes ya ha hecho especial hincapié en la eficiencia con el EQS y su carrocería especialmente aerodinámica. Sin embargo, hablar de eficiencia en un vehículo de lujo de más de 2,6 toneladas con una potencia máxima de hasta 560 kW es relativo. También está claro que al concepto original del EQS no le fue bien en China, que es un mercado importante para las berlinas de lujo.
Se espera que el próximo CLA, basado en la arquitectura modular de Mercedes (MMA), tenga mucho más éxito. El año que viene, la berlina compacta será el preludio de la próxima familia de modelos compactos del fabricante alemán, llamada a generar unas elevadas ventas de unidades. Hay una sencilla razón por la que la MMA no hará su debut en una nueva Clase A: la cartera de modelos se está racionalizando radicalmente y no habrá sucesores de la Clase A y la Clase B. En su lugar, habrá el CLA, la Clase A y la Clase B. En su lugar, habrá el CLA, un shooting brake como familiar dinámico y dos modelos SUV: uno un poco más dinámico al estilo del GLA/EQA y otro más anguloso con más espacio y valor utilitario como el GLB/EQB.
Sin embargo, aún no se han ultimado los detalles de los cuatro modelos y Mercedes no está dispuesta a hacer más comentarios sobre los vehículos. En su lugar, el fabricante de automóviles organizó un taller tecnológico sobre la MMA en la planta de Sindelfingen (Alemania), concretamente en el "Electric Software Hub", donde tuvo lugar gran parte del trabajo de desarrollo de la nueva plataforma. Mercedes quiso compartir con el público información sobre los propulsores, algunas declaraciones sobre las baterías y cómo se desarrolló la MMA. Los detalles del CLA se desvelarán en el estreno mundial el año que viene. Sin embargo, ya podemos hacernos una idea de lo que habrá bajo el capó.
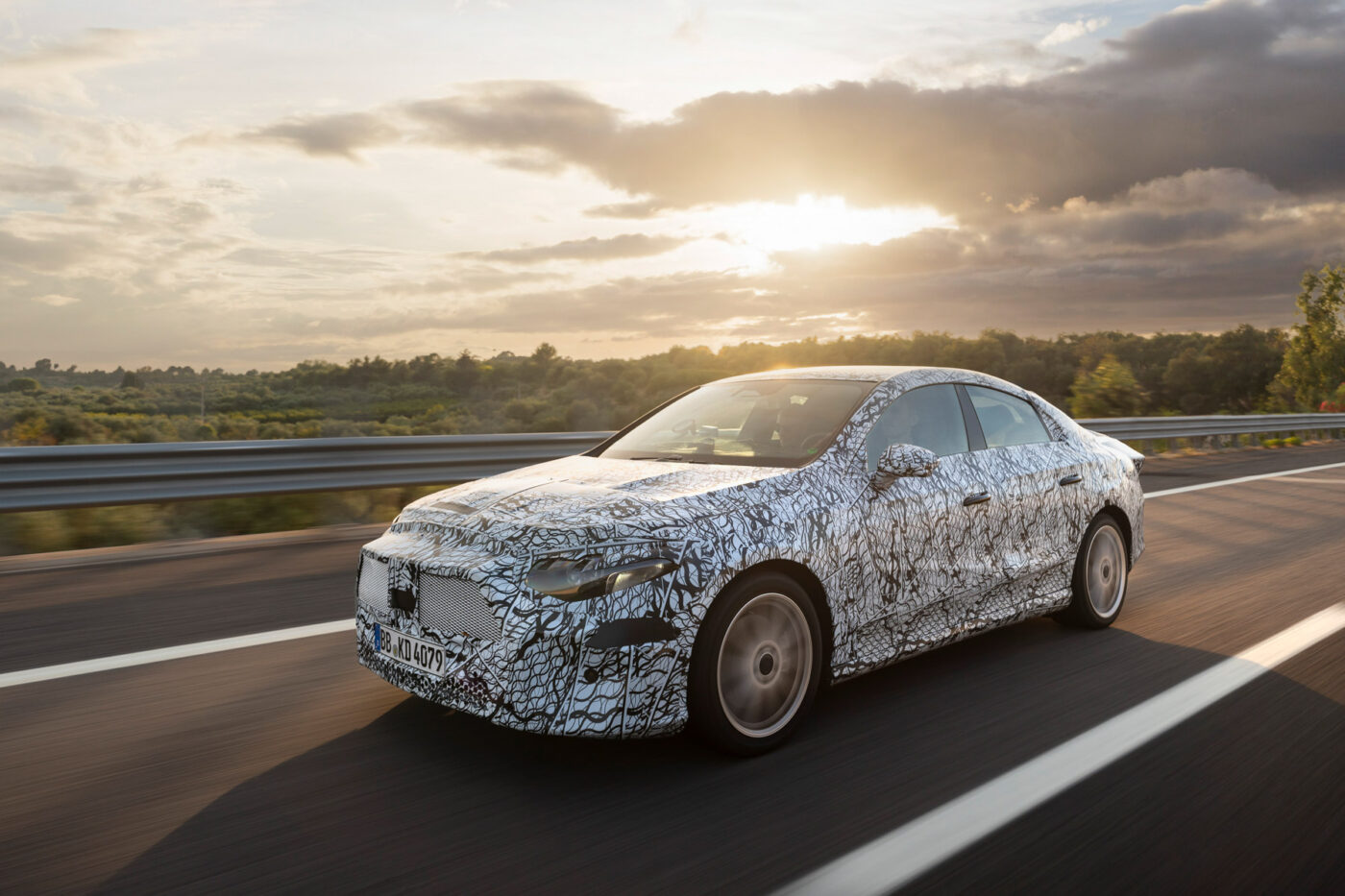
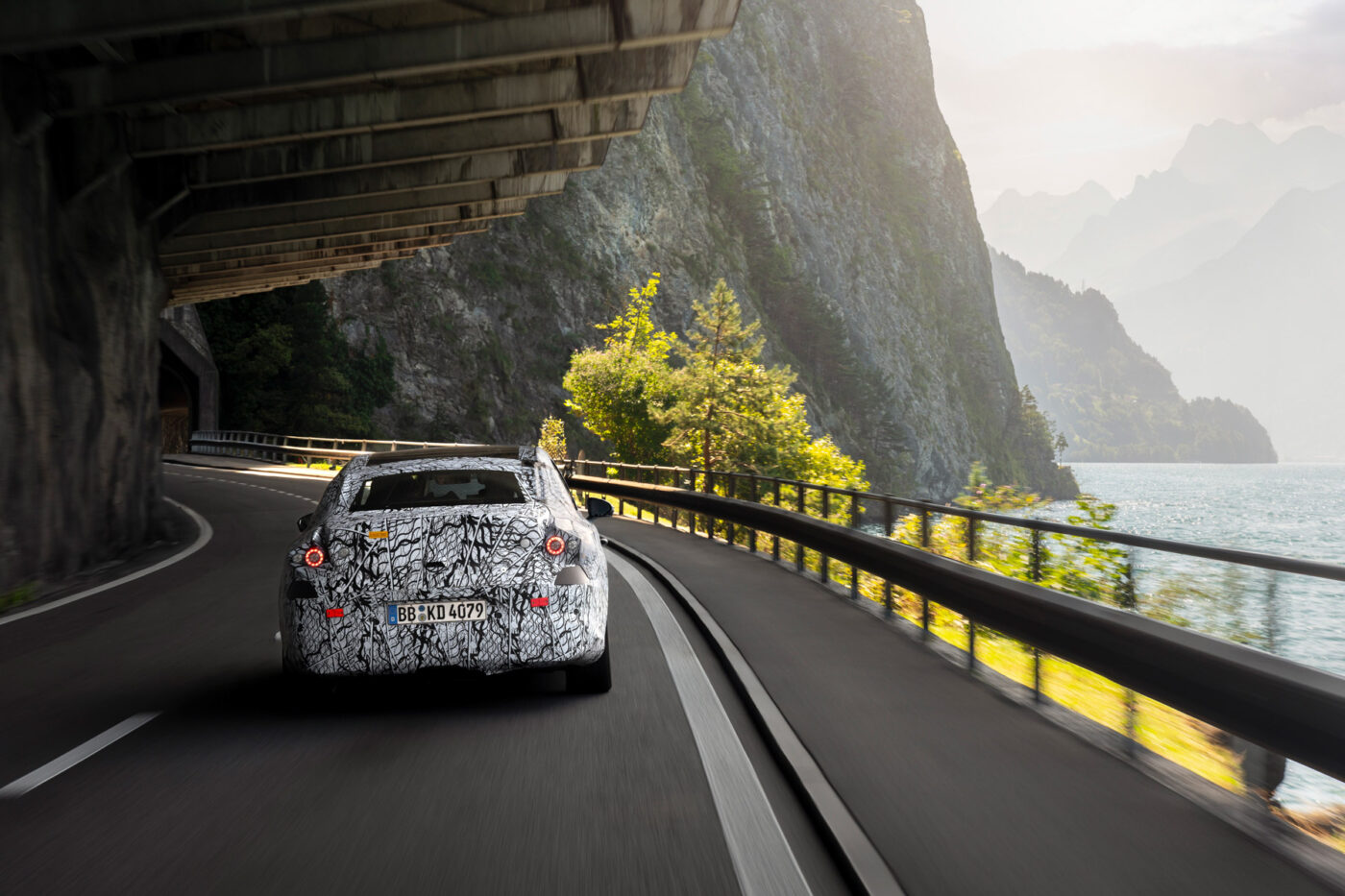
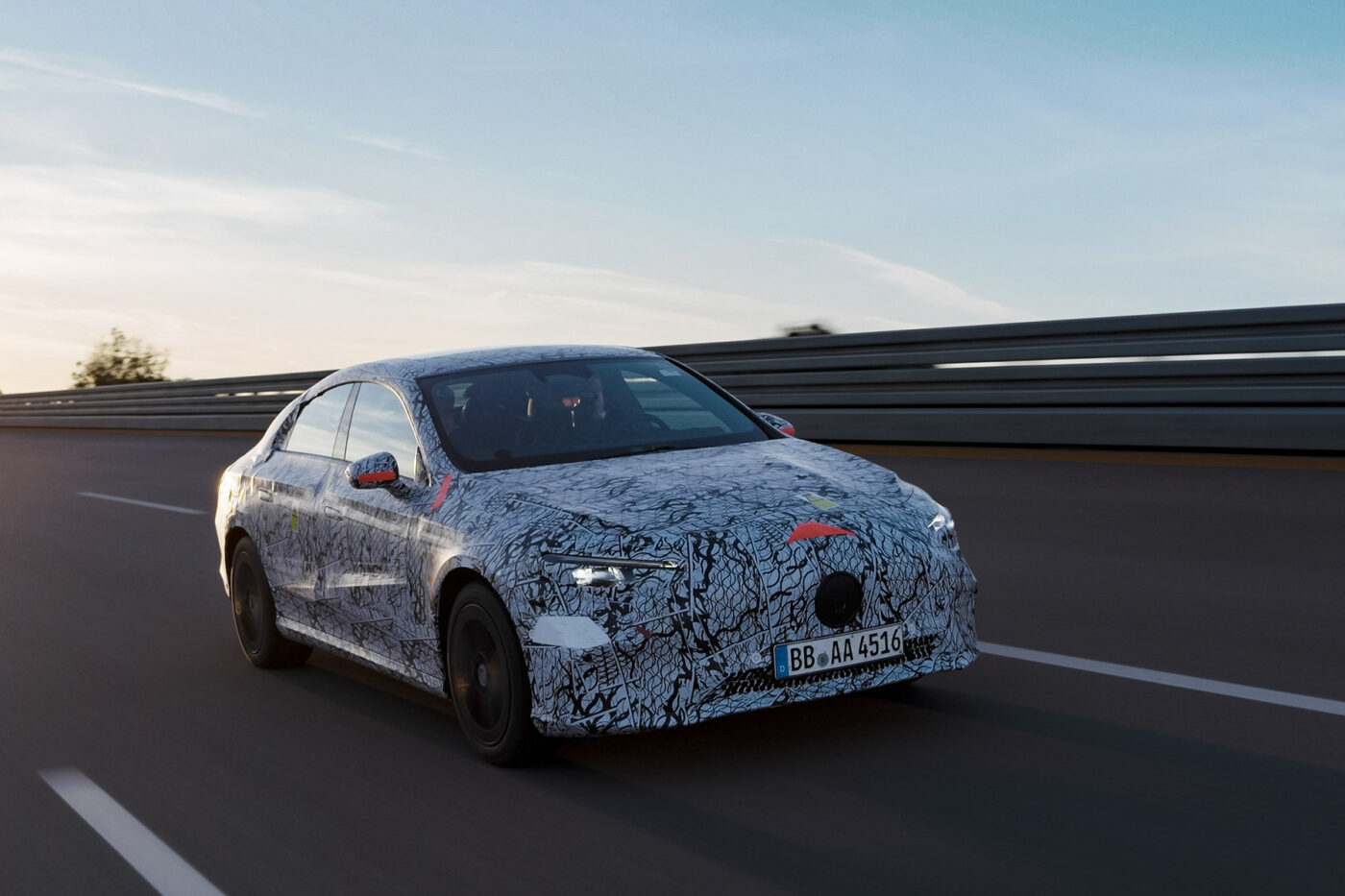
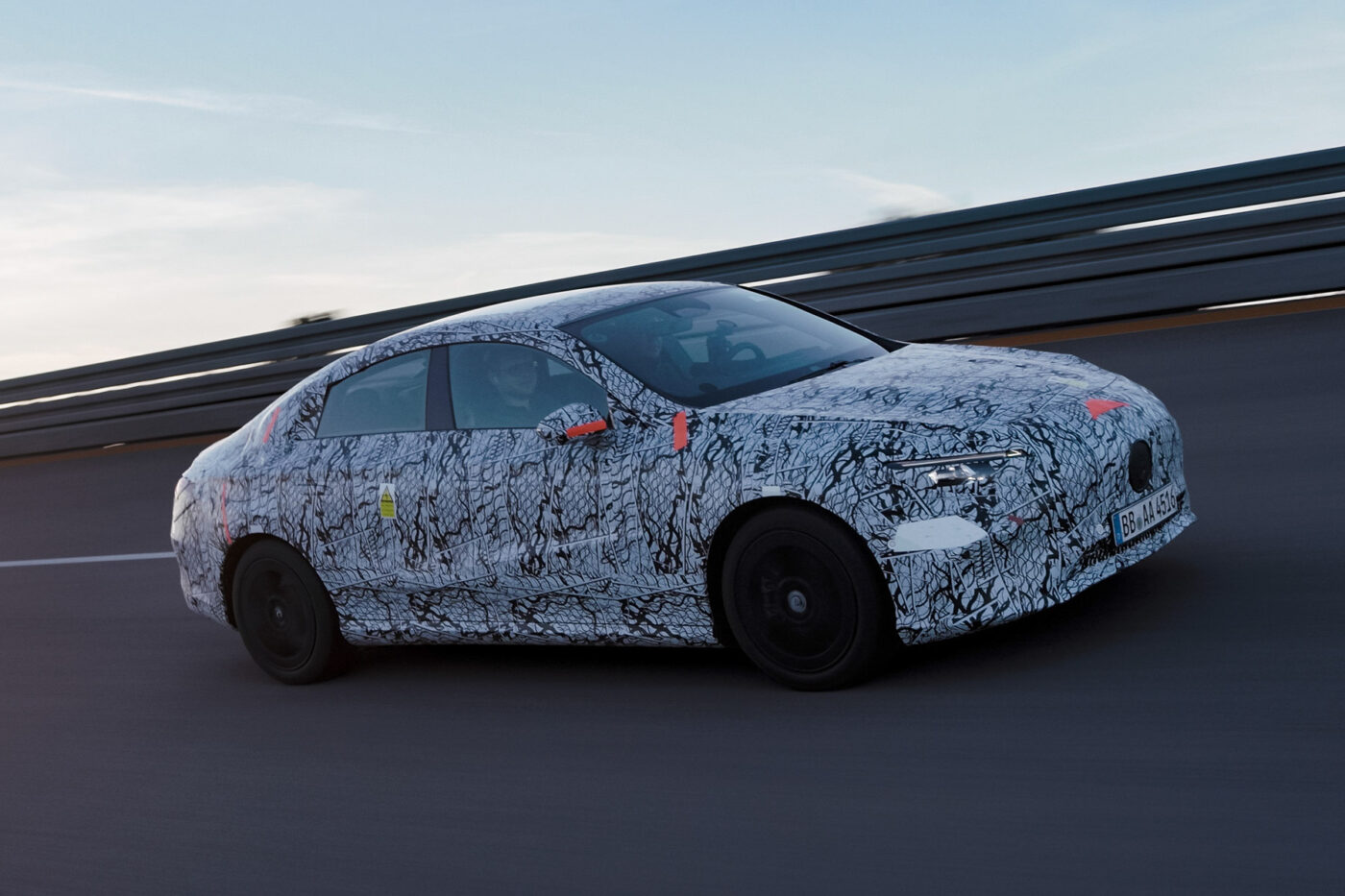
La eficiencia está en el centro del desarrollo. Como Torsten Eder, Vicepresidente de Desarrollo de Propulsiones Electrificadas, explicó en su presentación, su equipo no sólo se centró en la eficiencia energética clásica, sino también en lo que Mercedes denomina "eficiencia en el tiempo". Porque desde el punto de vista del cliente, de lo que se trata es de llegar al destino lo antes posible, ya sea gracias a una gran autonomía gracias a la conducción eficiente, a tiempos de carga cortos o a una planificación inteligente de la carga. Todo juega un papel.
En Mercedes están seguros de que van por el buen camino. "En nuestra opinión, la eficiencia marcará la diferencia en los futuros modelos eléctricos", afirma Eder. Y "La eficiencia es la nueva moneda".
El CLA y todos los demás modelos eléctricos de Mercedes tendrán que medirse con esta frase. Se ha anunciado un consumo de 12 kWh/100 kilómetros para el primer modelo MMA. Los capítulos siguientes muestran cómo se logrará.
La unidad
El CLA utiliza el nuevo eATS 2.0. Como explicó Eder, esta "cadena cinemática eléctrica 2.0" (también conocida como MB.EDU 2.0) es una especie de familia de motores eléctricos: el primero de los cuatro "miembros de la familia" está instalado en el CLA. Se trata de un motor eléctrico altamente integrado que Mercedes ha desarrollado por sí misma y fabrica en su planta principal de Untertürkheim.
Un pequeño pero: sólo el motor eléctrico del eje trasero es un eATS 2.0 de este tipo. El segundo motor eléctrico, instalado en el eje delantero en la versión de tracción total, también se desarrolló según las especificaciones de Mercedes, pero procede de un proveedor.
La eATS 2.0 es una máquina síncrona de excitación permanente (PSM). La potencia máxima es de 200 kW. La unidad motriz es muy compacta y está diseñada para permitir un arranque amplio y profundo. La electrónica de potencia (se utilizan semiconductores SiC en la parte delantera y trasera) está situada aproximadamente en la parte delantera de la carcasa, ya no en la parte superior. A pesar de los imanes permanentes, el PSM se las arregla "casi" sin tierras raras, como explicó Christian Pfeffer, jefe de proyecto para el desarrollo en serie de la cadena cinemática del CLA. El fabricante de automóviles lo consiguió utilizando bobinados en horquilla en el estator y una disposición en doble V de los imanes permanentes en el rotor.
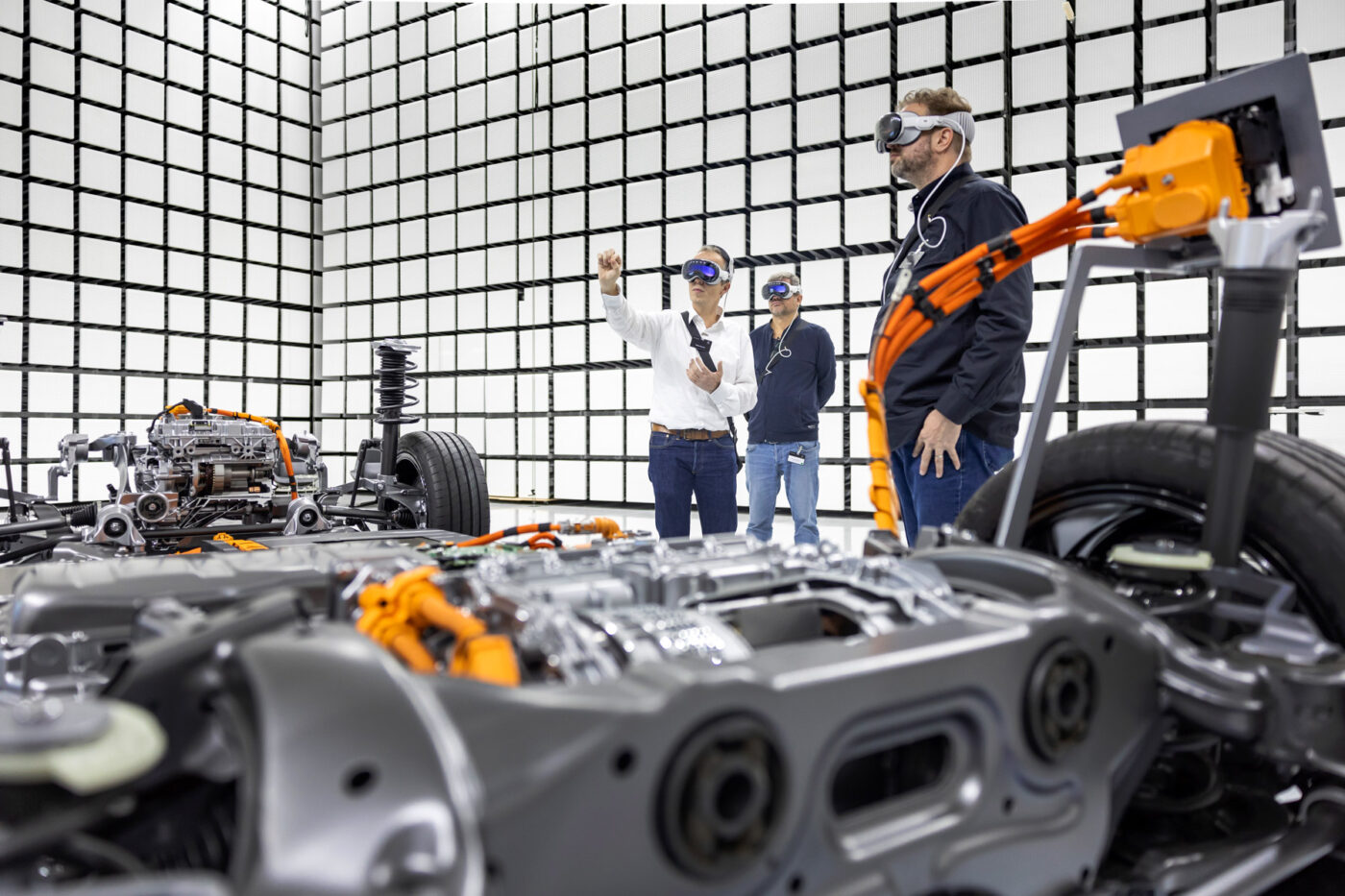
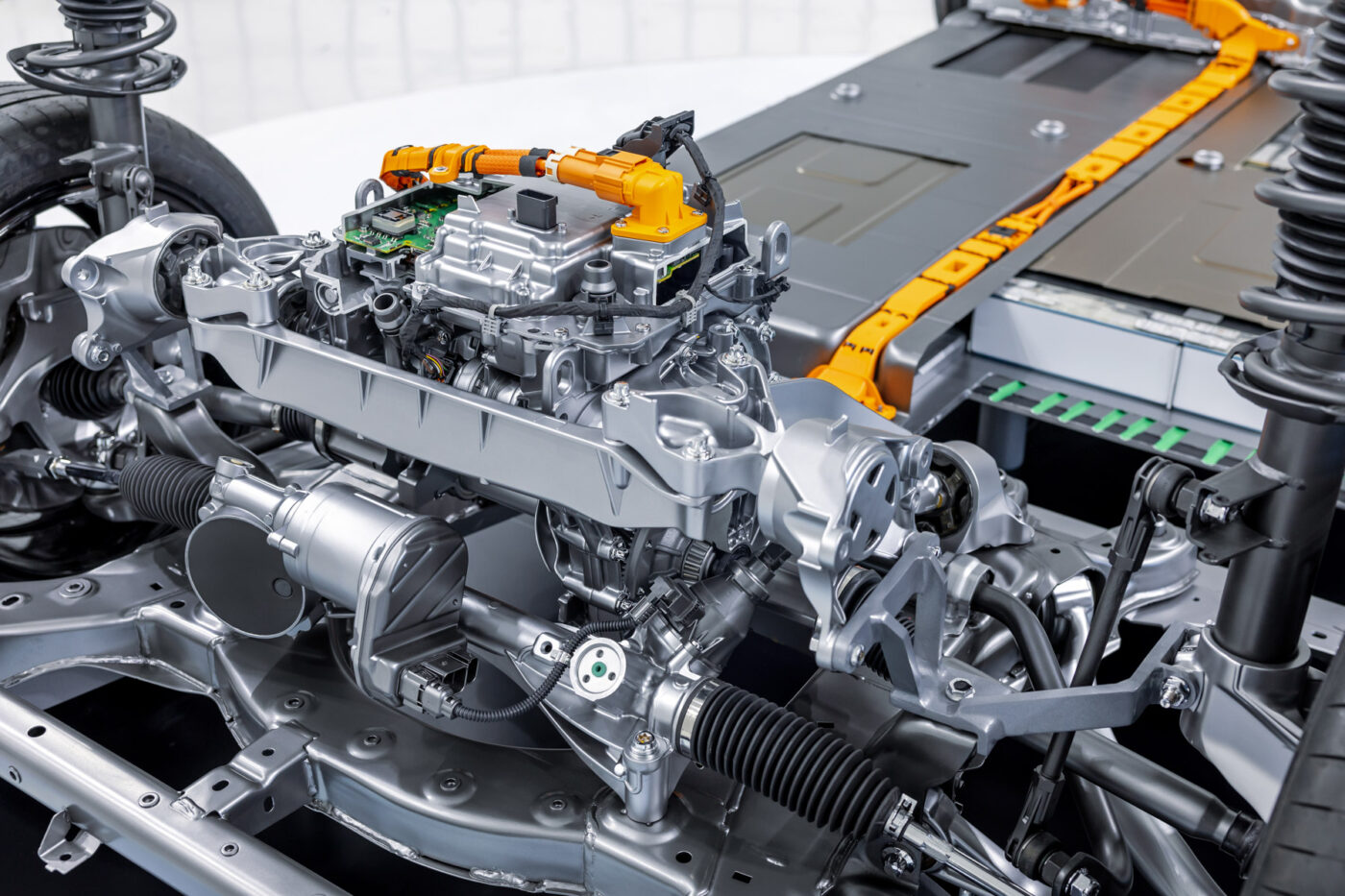
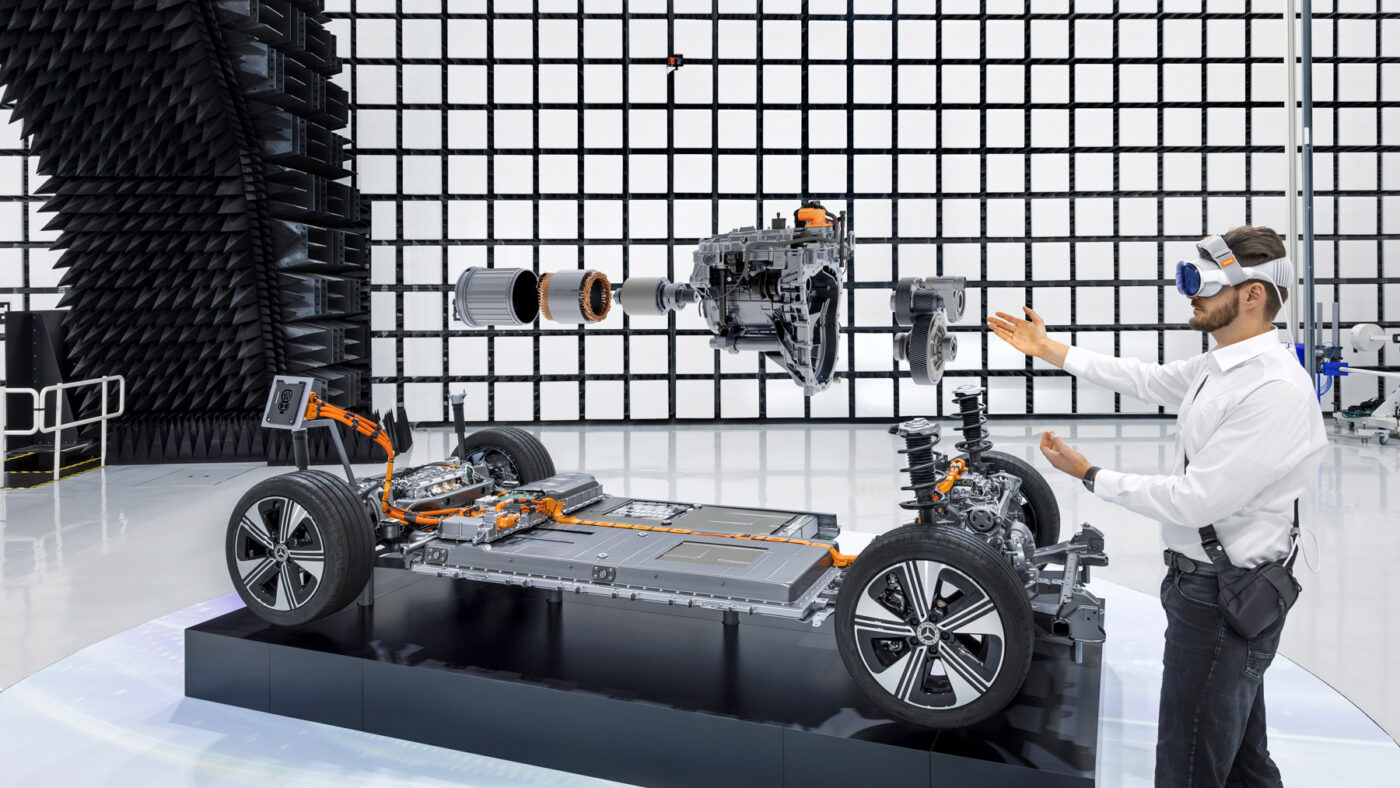
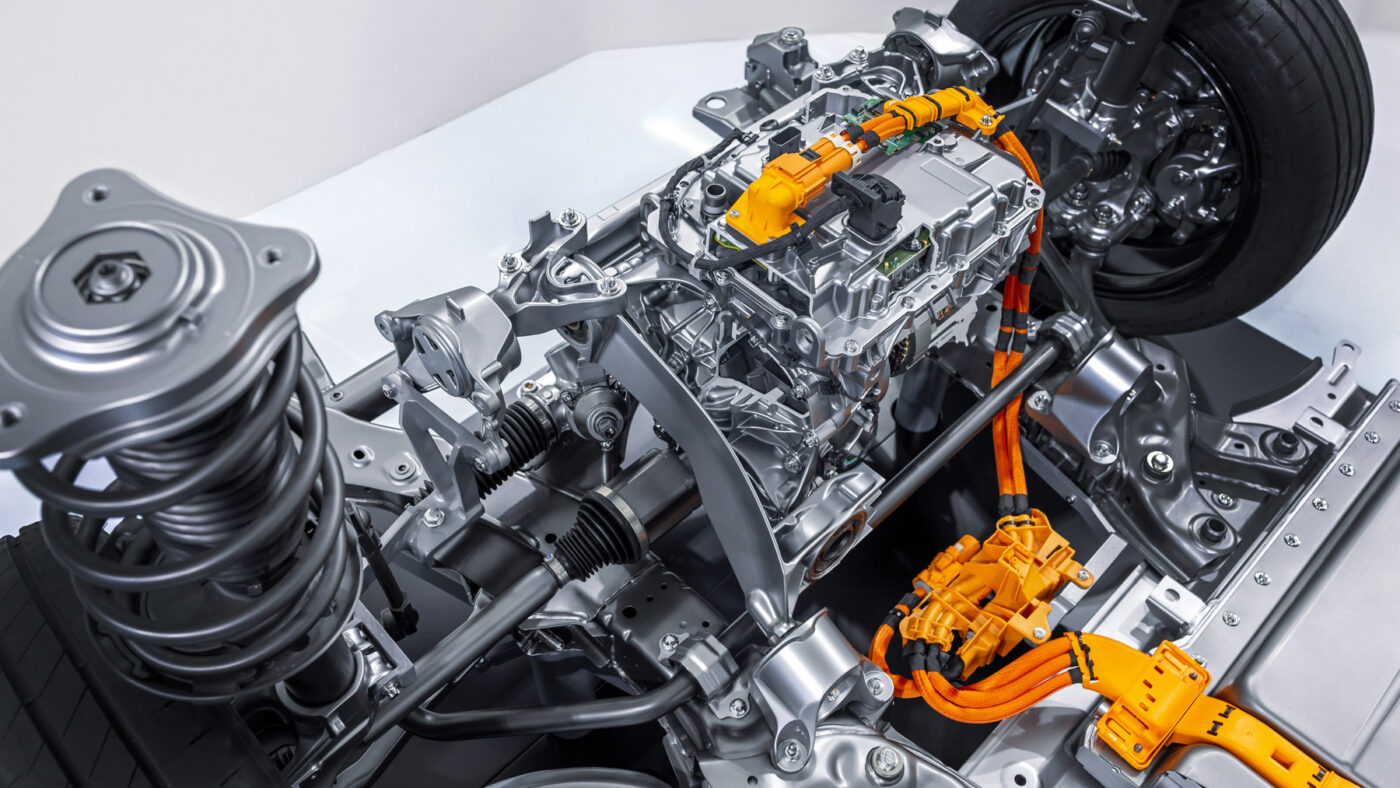
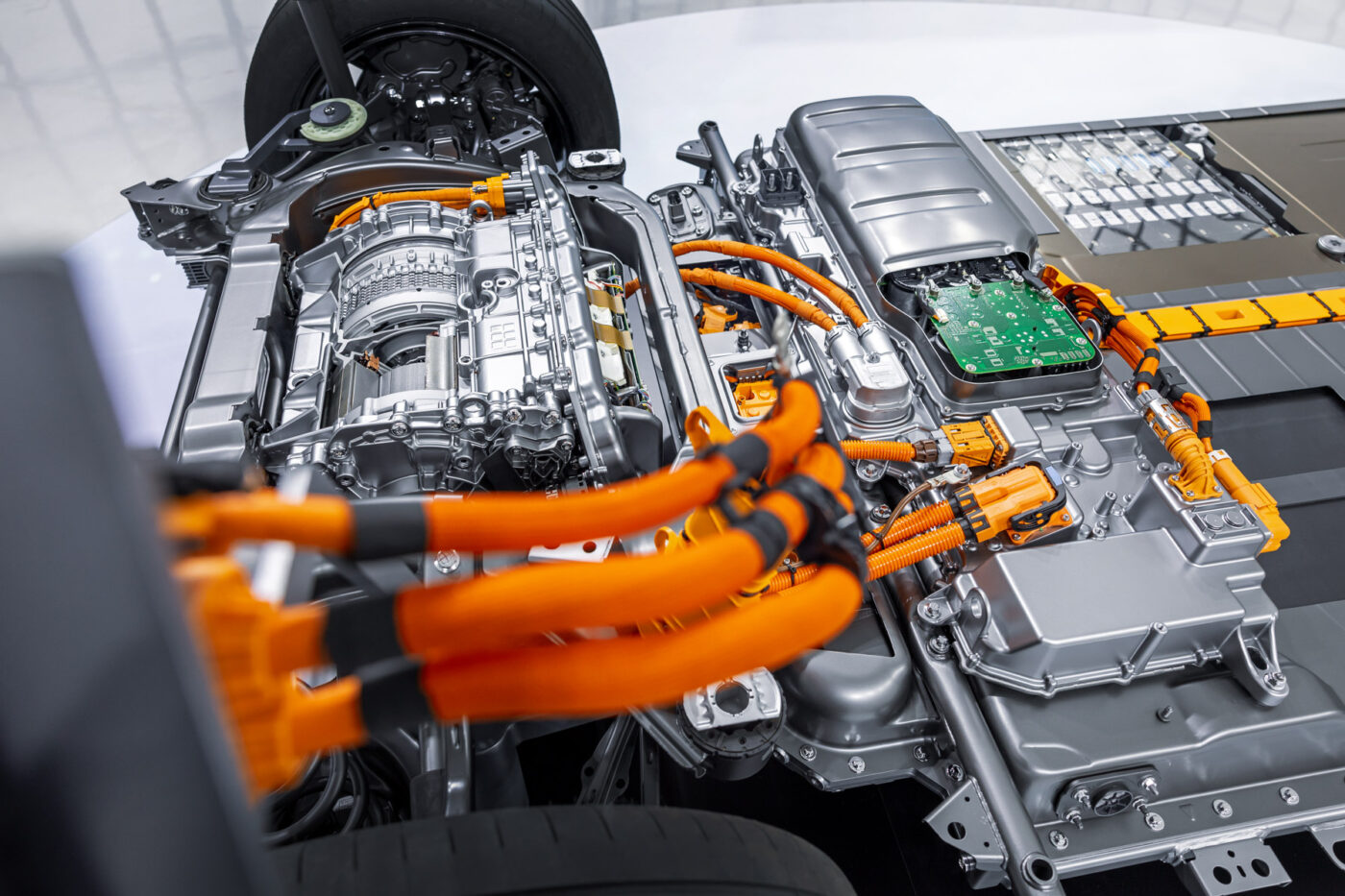
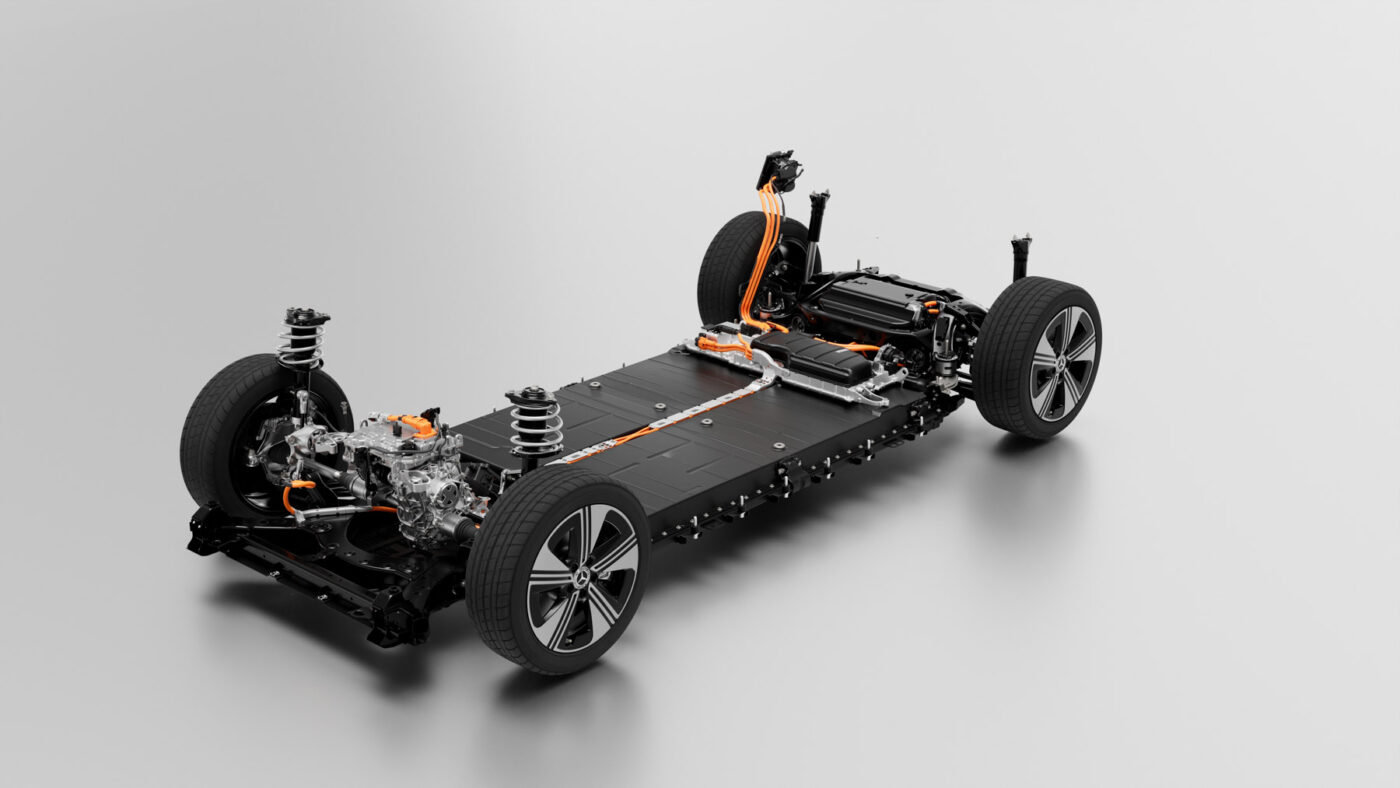
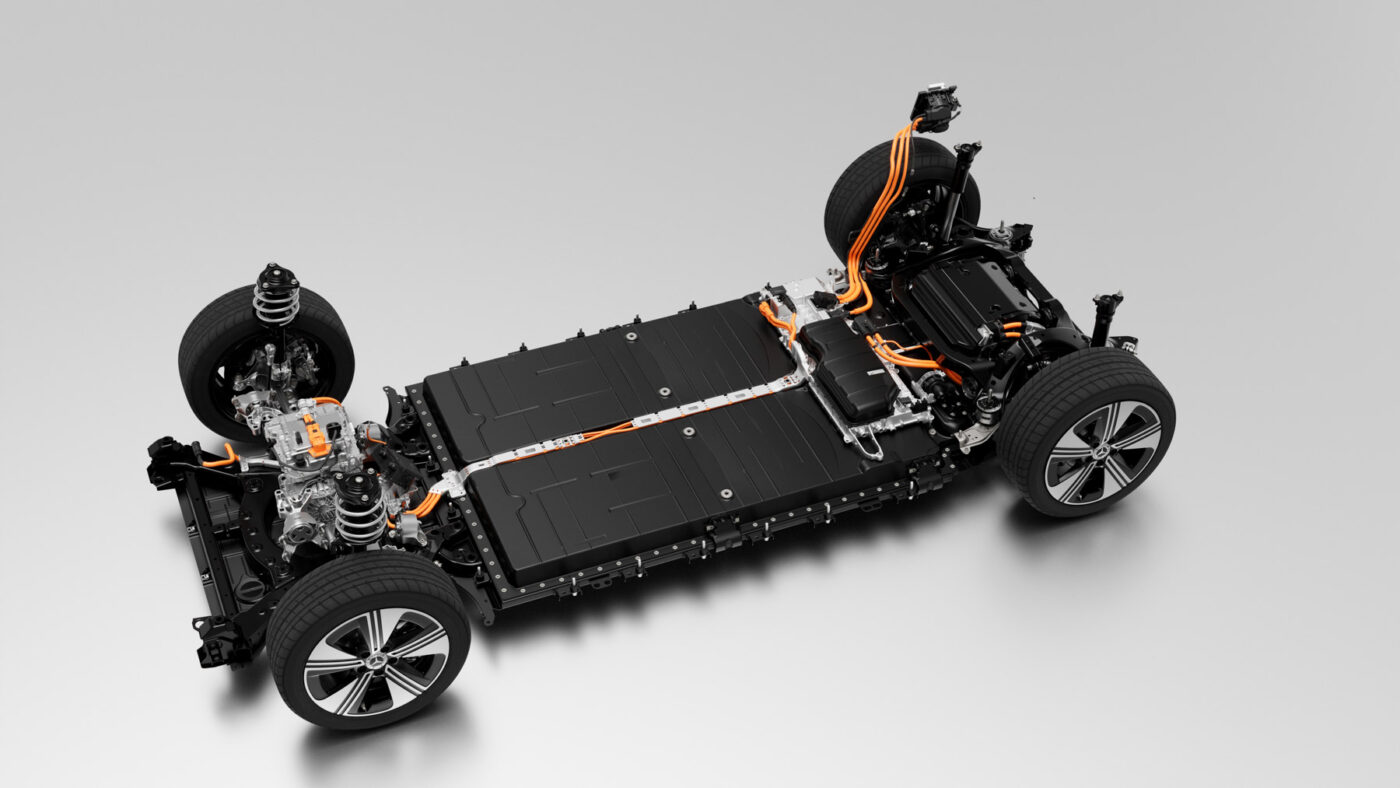
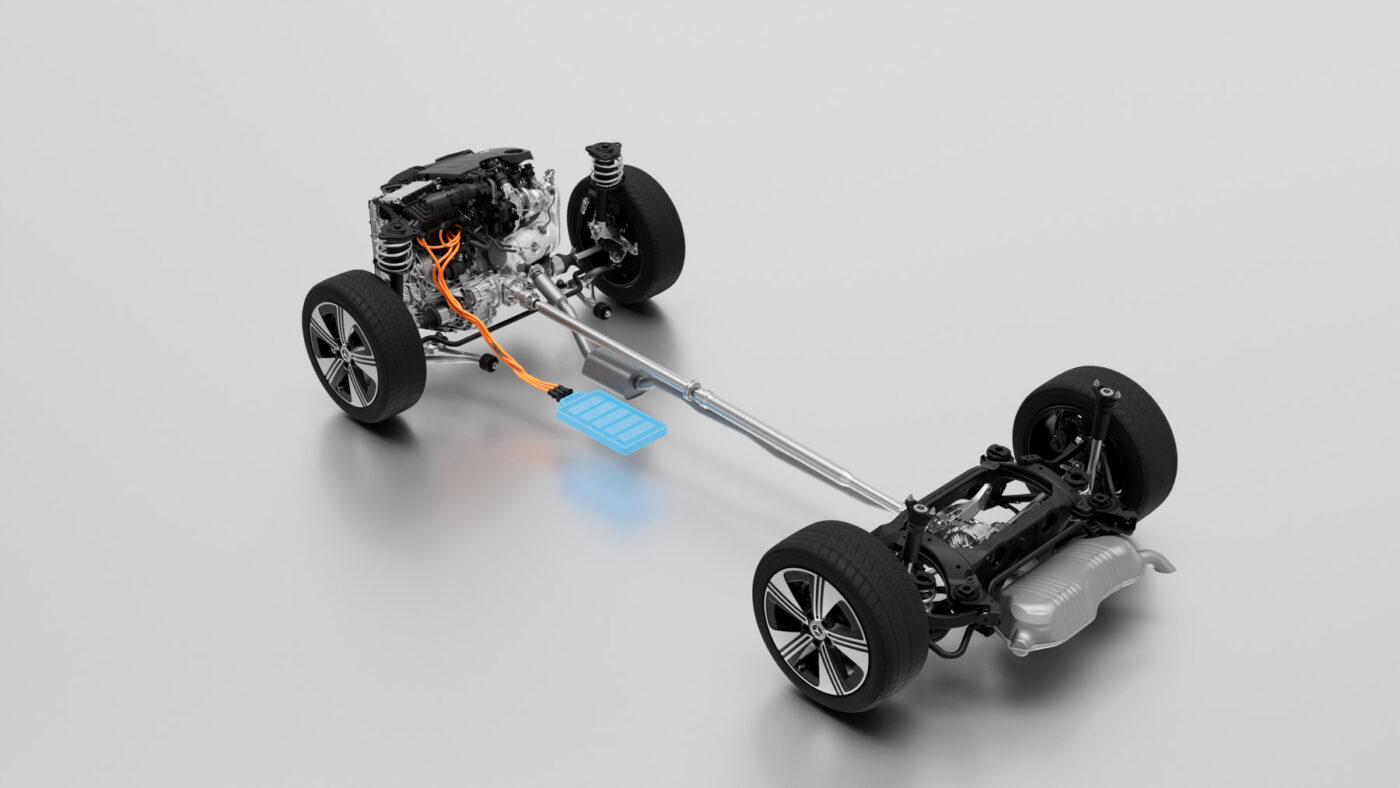
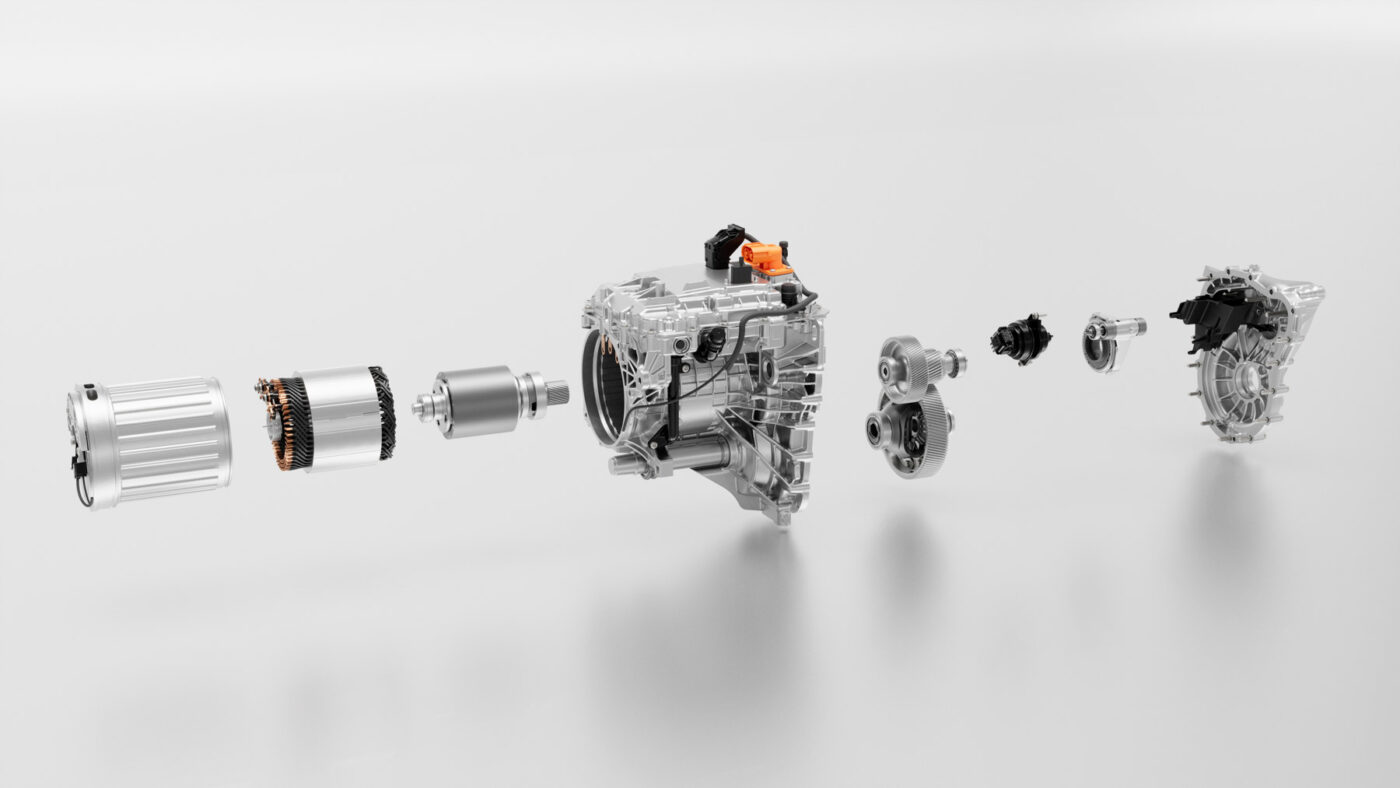
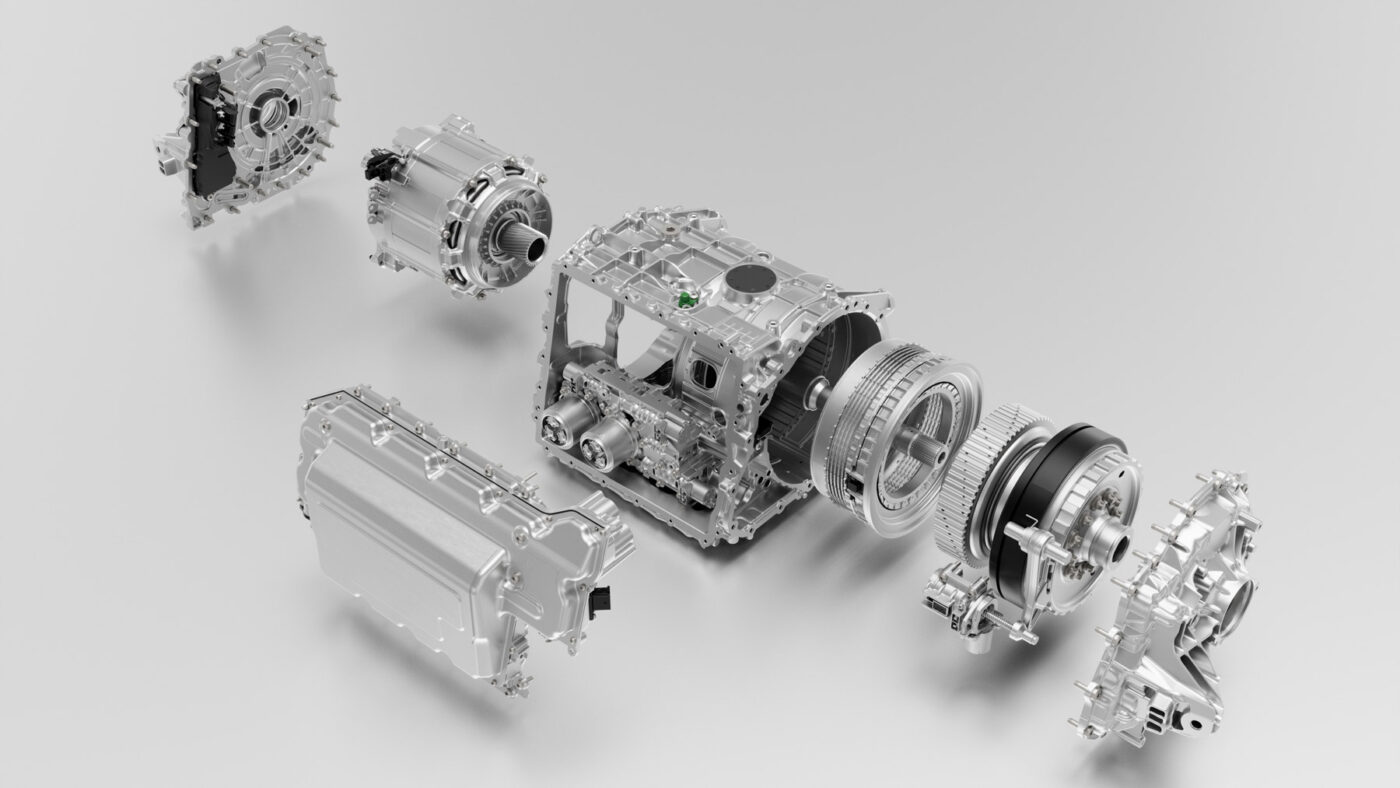
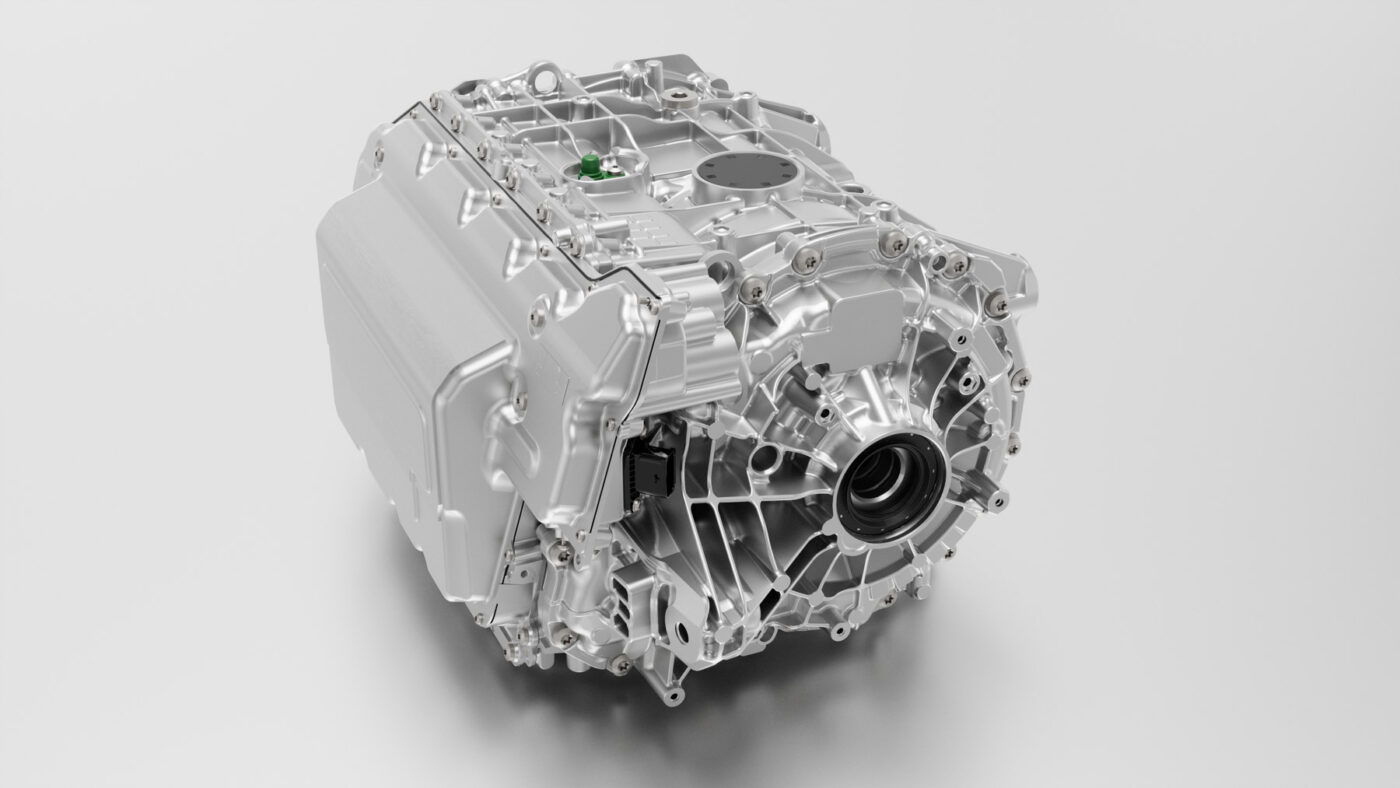
Probablemente la parte más controvertida de la propulsión eléctrica en el CLA es que la unidad motriz en la parte trasera tiene una caja de cambios de dos velocidades. Porsche optó en su día por una caja de cambios de dos velocidades en el eje trasero en el Taycan para armonizar la aceleración necesaria y la elevada velocidad máxima. Esto no ha encontrado muchos imitadores desde entonces, e incluso el Macan sólo tiene una marcha en la parte trasera. Para Mercedes, sin embargo, la atención no se centró realmente en la dinámica sino, sobre todo, en la eficiencia.
"Con dos marchas, podemos lograr una alta eficacia en un rango extremadamente amplio", explica Pfeffer. No hay una velocidad específica a la que el embrague multidisco y las mordazas cambien de marcha. "Calculamos constantemente qué marcha es más eficiente", añadió el desarrollador. "Depende de la carga, del modo de conducción seleccionado y de factores como el voltaje de la batería".
Para completar: la relación de la primera marcha es de 11:1, y para la segunda, la relación es de 5:1. Por encima de 110 km/h, la segunda marcha se engrana siempre, mientras que la primera se engrana al arrancar - entre medias, la unidad de control decide.
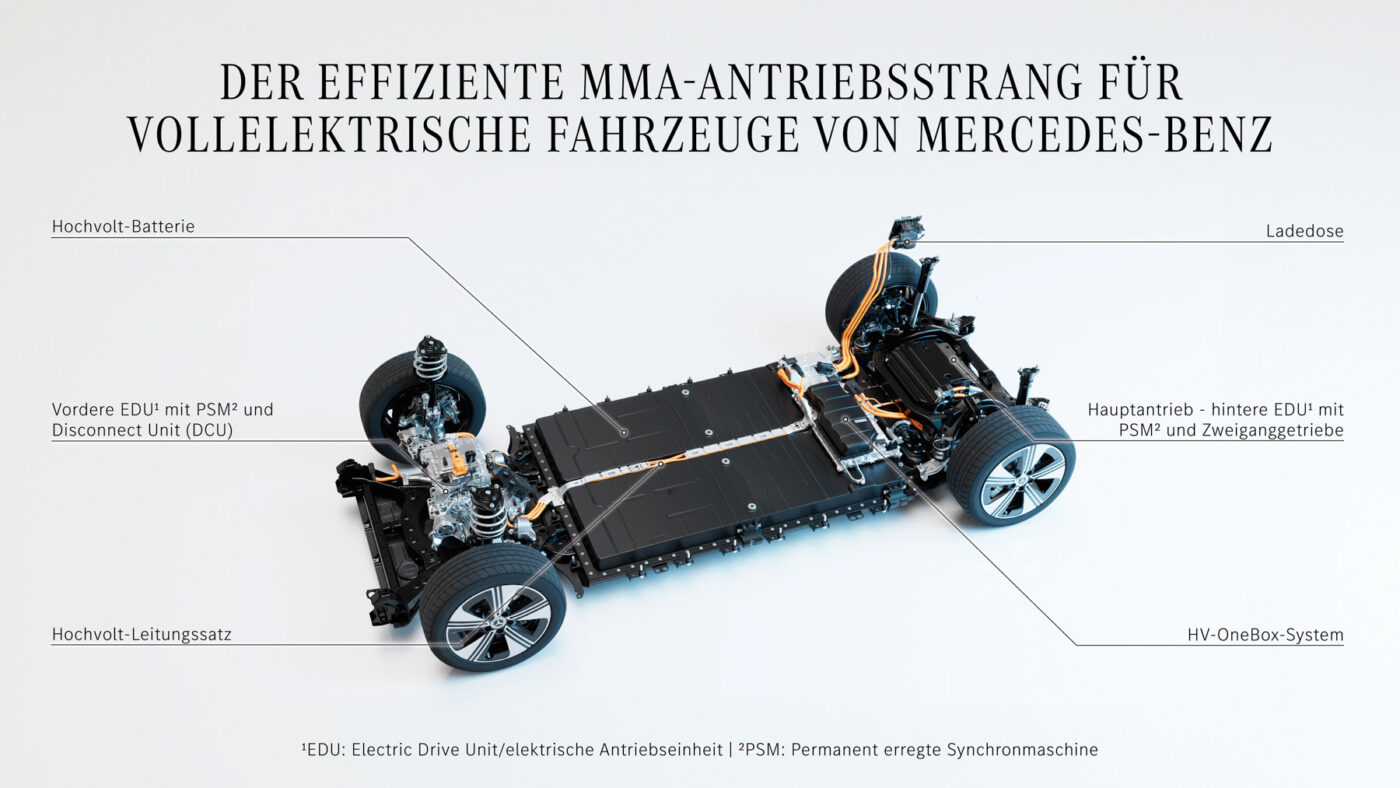

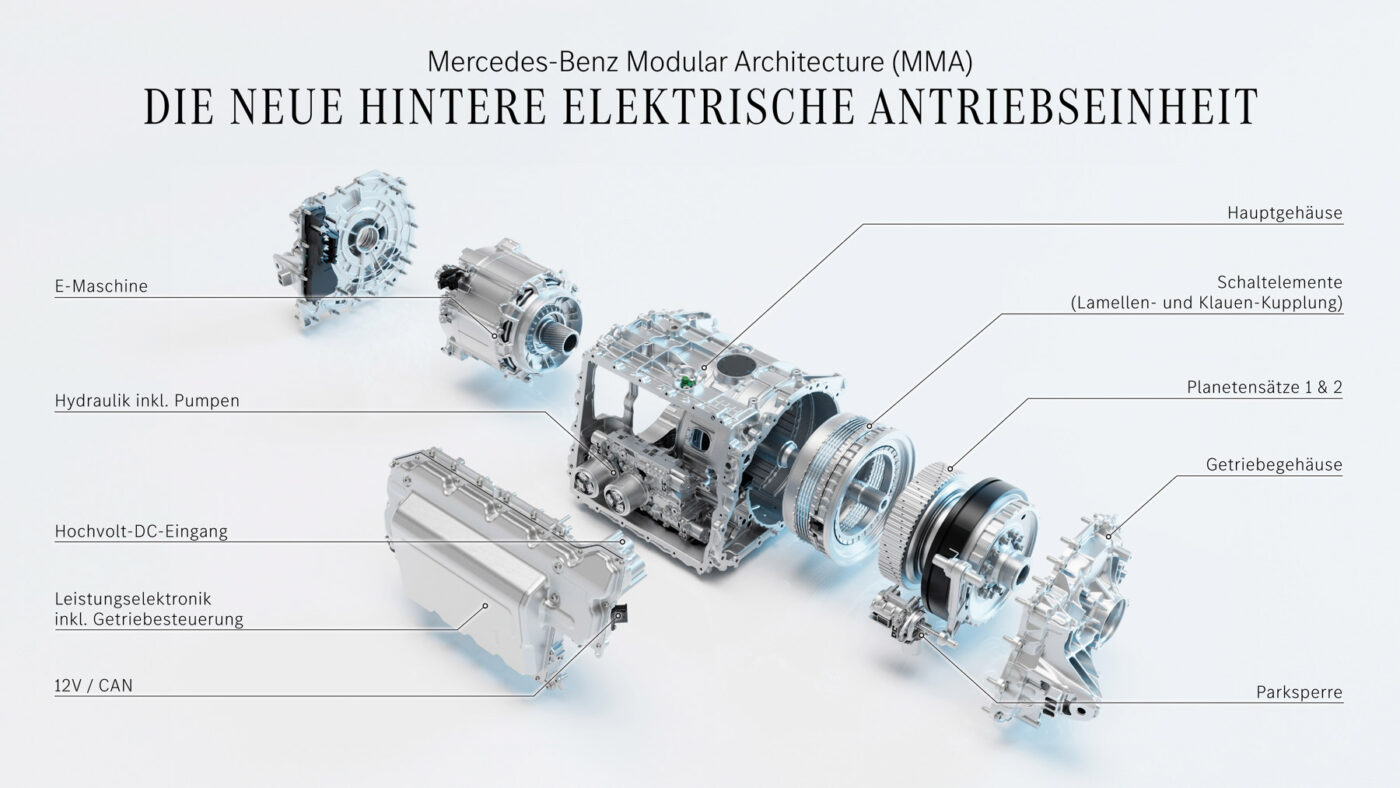
En los modelos de tracción total se utiliza un PSM adicional de 80 kW en la parte delantera. Se utiliza como unidad de sobrealimentación para el arranque y bajo carga elevada. Para la mayor parte de la conducción diaria a velocidad constante, este motor se desconecta mecánicamente mediante un embrague independiente en la denominada "unidad de desconexión". Esto ocurre en 0,2 segundos, por lo que el motor delantero también puede conectarse rápidamente para la recuperación. El CLA dispondrá de nuevo de cuatro niveles de recuperación, desde el One-Pedal-Drive hasta el control automático D-Auto. A pesar de su caja de cambios, el propulsor trasero no se desconecta. Incluso en marcha, el motor eléctrico sigue conectado mecánicamente a las ruedas y sólo se desenergiza. Pfeffer declaró que "se desconecta todo lo posible cuando está parada para ahorrar cada vatio".
Incluso cuando se le pregunta directamente, Mercedes no comenta todavía si están previstos otros niveles de potencia de la unidad motriz de 200 kW (por ejemplo, con la opción de batería más pequeña). Lo que está claro, sin embargo, es que siempre se instalará el mismo hardware de propulsión independientemente de la batería, con cualquier potencia. También está claro que este concepto básico aparecerá en otros modelos, no sólo en los cuatro vehículos eléctricos de MMA. "El sistema de propulsión que hemos desarrollado para el MMA es escalable, incluso en otras arquitecturas", afirmó Torsten Eder. "También podemos adoptar varias tecnologías en otras clases de vehículos y crear así sinergias".
La batería
Lo mismo ocurre con la batería: la MMA no presenta ningún desarrollo especial para la plataforma. Se trata de un sistema modular cuyas tecnologías también se utilizarán en modelos más grandes más adelante. Aunque la empresa de Stuttgart no dispone de una "célula unificada" específica como la competencia de Wolfsburg, sí tiene un concepto similar. Mercedes quiere controlar el escalado de las células a través de dos dimensiones: la química de la célula y el tamaño de las células, la altura en particular.
En el CLA, el pack de baterías con 192 celdas prismáticas es muy plano: en el taller de Sindelfingen se habló de un volumen total del pack "notablemente" bajo. Eso es algo más que el resultado del trabajo de los desarrolladores internos de baterías. "Nos pusimos en contacto con nuestros colegas de vehículos al principio del proceso de desarrollo", dijo Uwe Keller, Jefe de Desarrollo de Sistemas de Baterías.
Para conseguir una batería tan plana, Mercedes tuvo que hacer primero mucho trabajo de base. Se tomaron nuevos caminos para reforzar la experiencia y el desarrollo a nivel interno. Por ejemplo, Mercedes controla ahora todos los sensores y actuadores (por ejemplo, en el circuito de refrigeración) de la propia batería con su software. "Hemos adquirido a nuestros proveedores unidades de control prácticamente vacías", afirma Eder. Antes, Mercedes compraba el software, los sensores y las unidades de control correspondientes. Y con el e-Campus en Untertürkheim, la empresa también ha ampliado el desarrollo de baterías a nivel de célula.
Keller describe el propio desarrollo de la batería como "un decatlón". Un decatleta tiene que encontrar el compromiso óptimo entre sus disciplinas: un corredor excepcional puede sumar puntos en muchas áreas pero quedarse corto en el lanzamiento de peso, de jabalina o de pértiga si no se entrena de forma equilibrada. Aplicado a la batería, significa que a la hora de ponderar factores como la potencia de carga, la potencia de descarga para el accionamiento, el diseño/el envase, el peso, los costes y la autonomía, es posible establecer prioridades, pero siempre es necesario llegar a un compromiso. "La seguridad y la sostenibilidad, por ejemplo, no eran negociables para nosotros. Aquí no hicimos concesiones", afirma Keller.
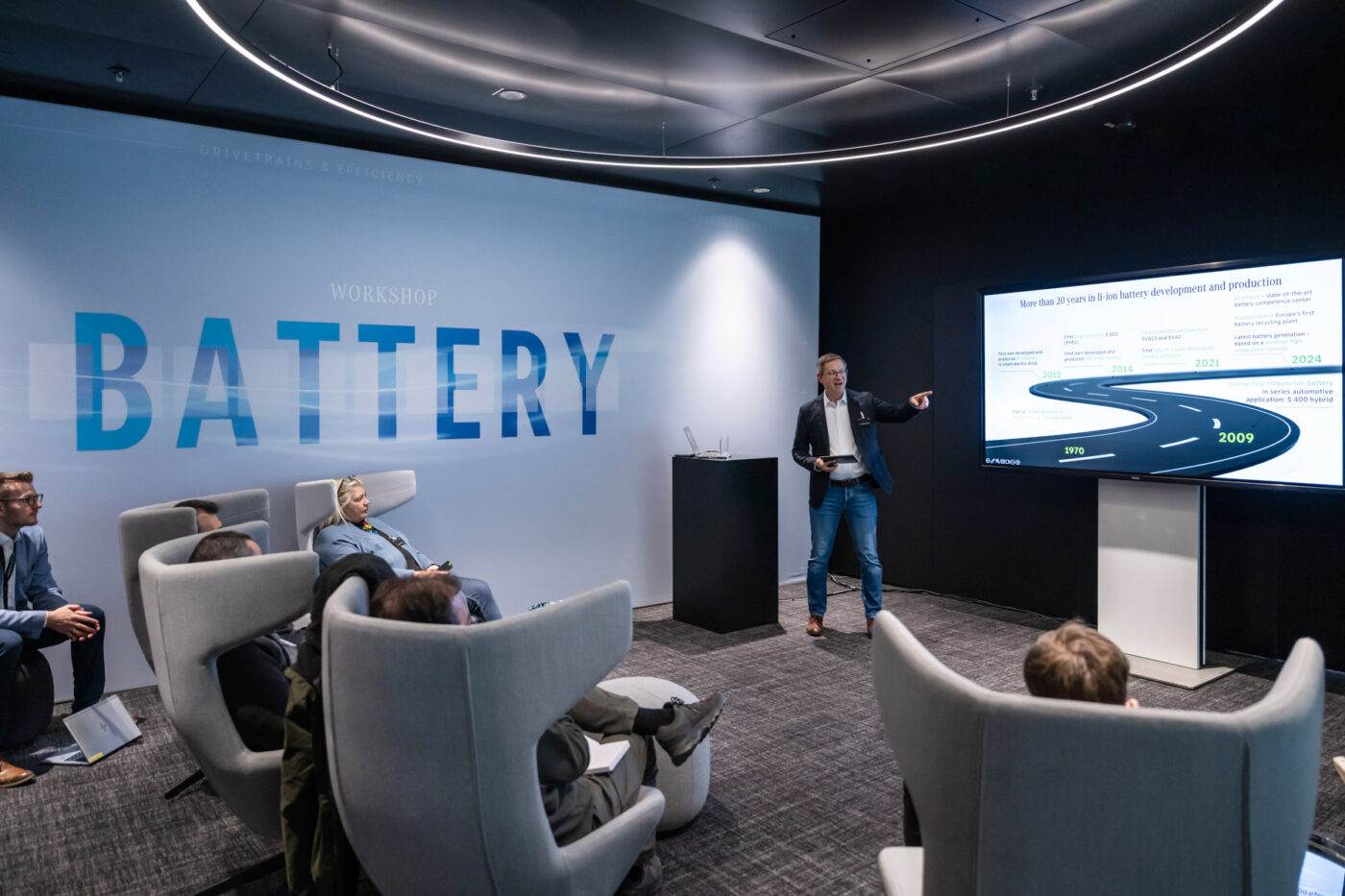
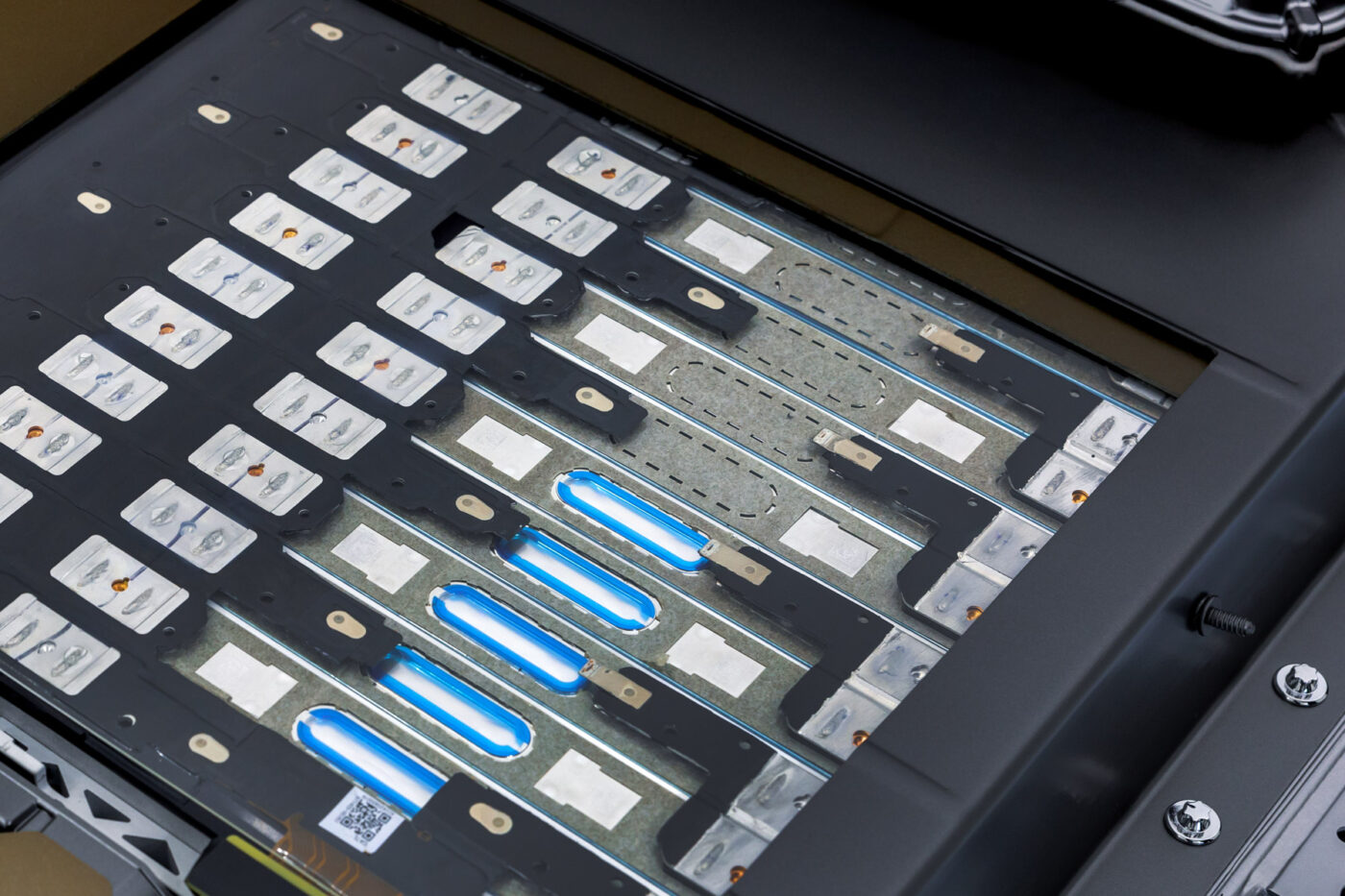
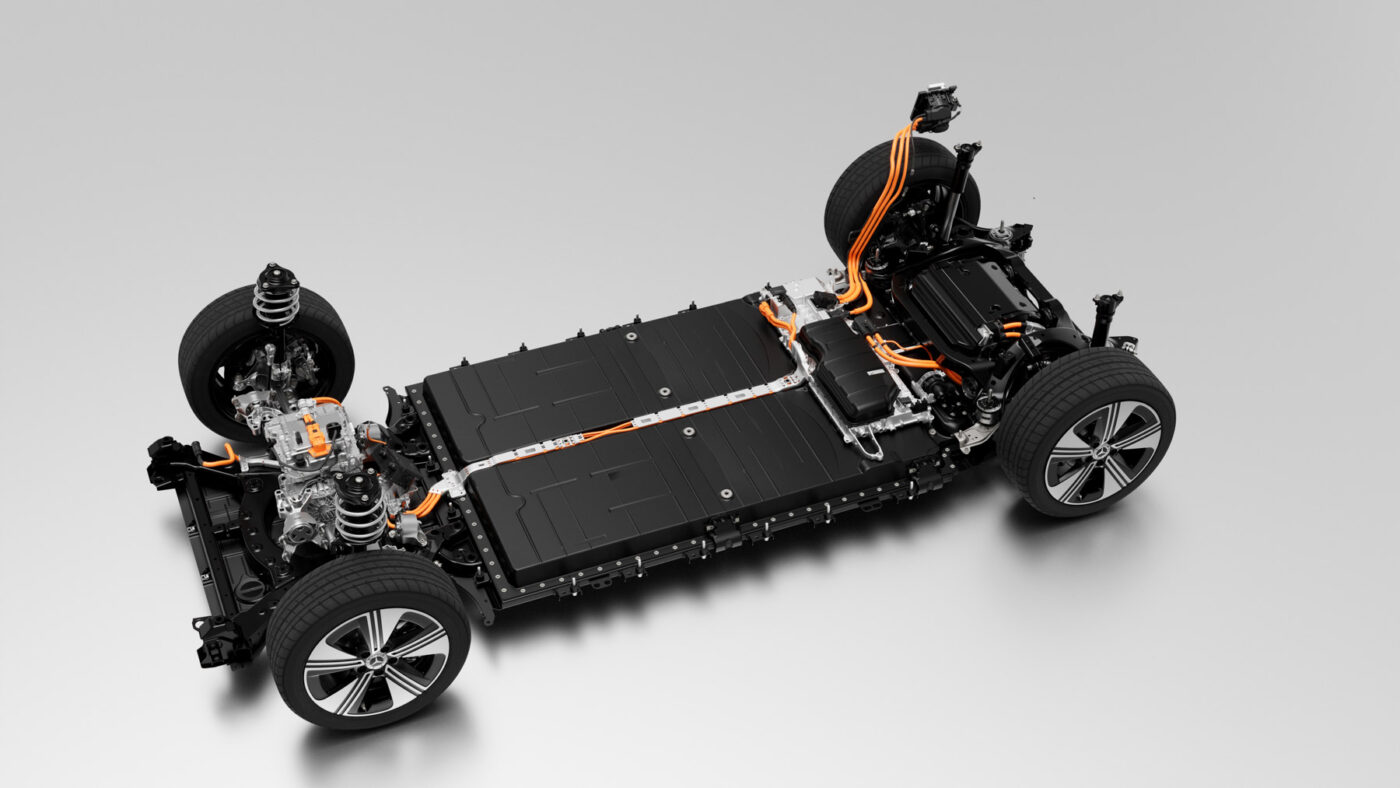
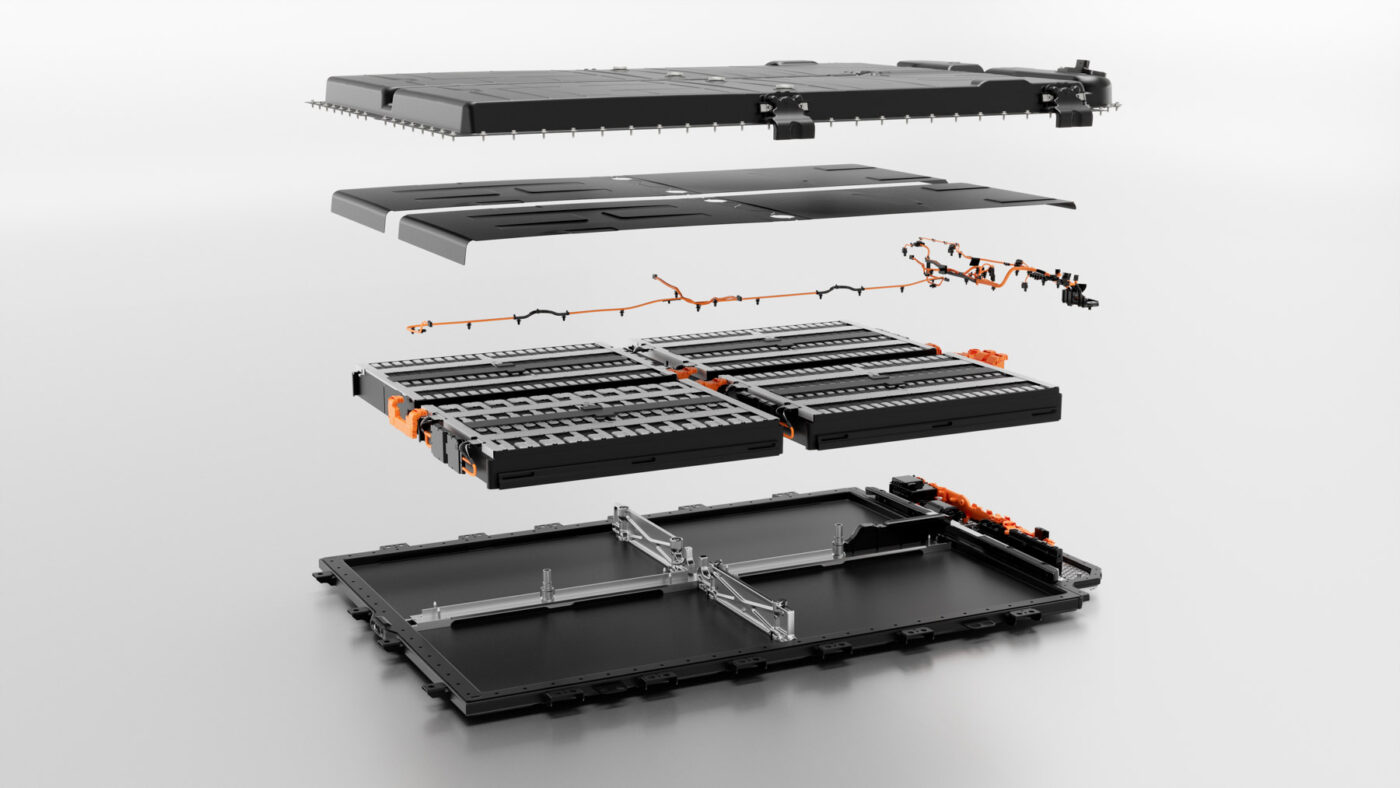
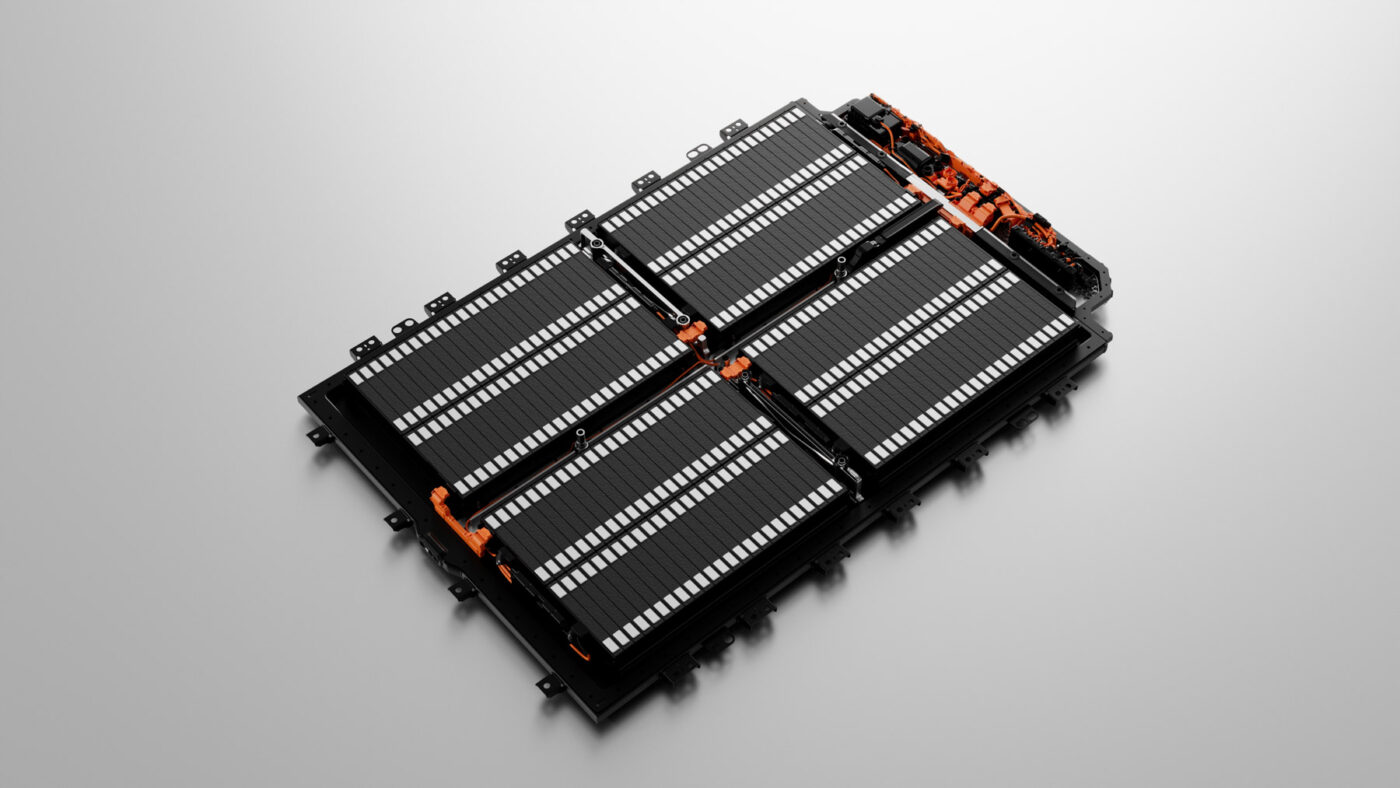
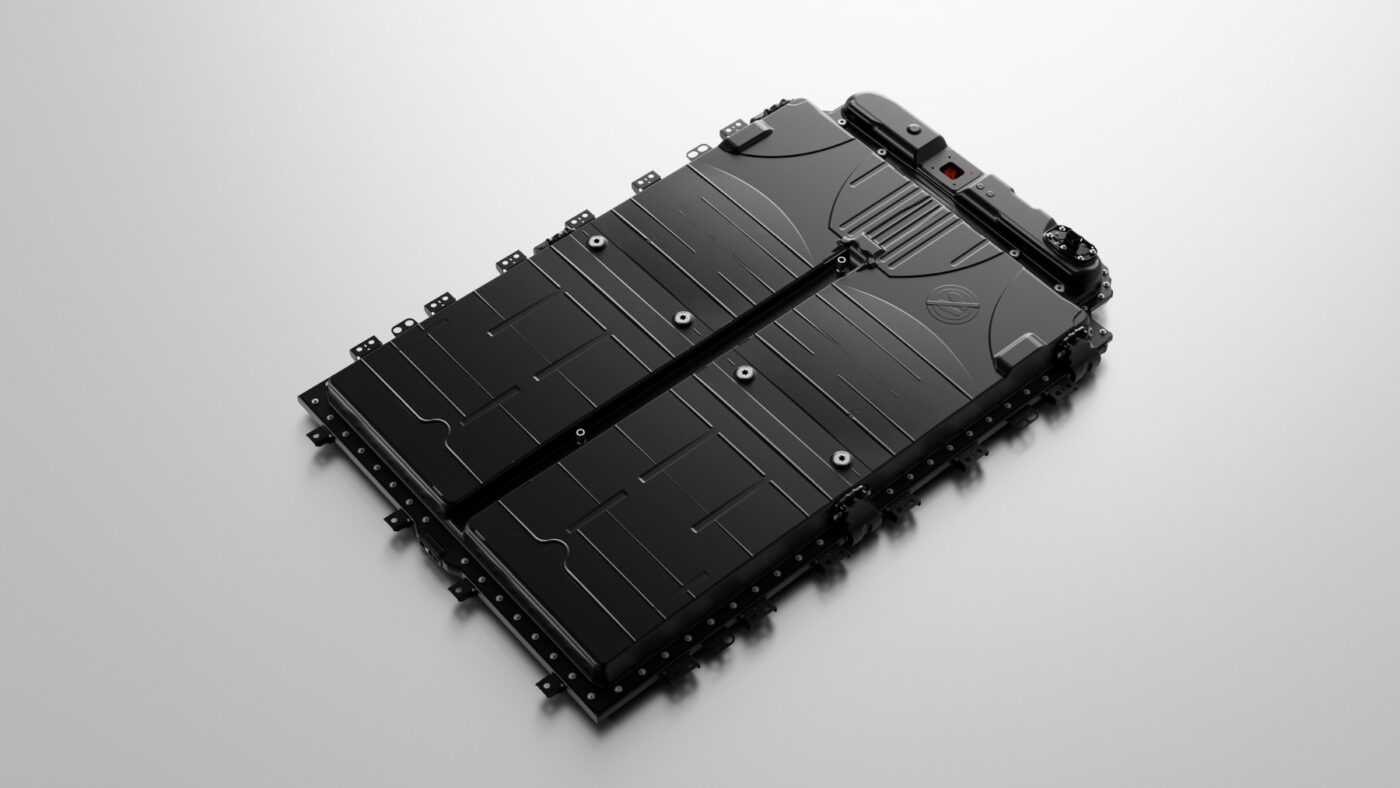
El resultado: habrá dos opciones de batería en el CLA (por el momento). Mercedes utilizará celdas LFP en la versión básica para ofrecer un precio más bajo. La versión de mayor autonomía (750 kilómetros es el objetivo) utilizará celdas NMC con un ánodo que contiene silicio, una primicia en Mercedes. Ambos paquetes de baterías tienen el mismo tamaño y pesan aproximadamente lo mismo. Con la mayor densidad energética, el pack NMC tiene 85 kWh y la batería LFP 58 kWh - ambos son valores netos, es decir, el contenido real de energía utilizable.
Mercedes declara una densidad energética de 450 Wh/l para la química de fosfato de hierro y litio y de 680 Wh/l para la batería NMC. Esto supone un 30% más que antes para esta última batería, y la densidad energética gravimétrica ha aumentado un 20% en comparación con las generaciones de baterías actuales. Y todo ello es un 30% más barato - Mercedes no da aquí los valores absolutos.
El desarrollador de baterías Keller tampoco quiso comentar la proporción exacta de silicio. Cuando se le preguntó repetidamente, sólo dejó escapar con un guiño que se trata de "menos del 50%" - pero no quiso comentar si era el 5%, el 10% o el 49,9%. Su colega Franz Nietfeld, de Cell Development, añadió que ya están trabajando en ánodos con alto contenido en silicio en el laboratorio, pero que aún no están listos para la producción en serie.
Así que atengámonos a los hechos conocidos: El pack se construirá en Kamenz, en el estado alemán de Sajonia -independientemente de la química de la célula- y se entregará desde allí a las plantas de vehículos. Inicialmente a Rastatt para el CLA, y más tarde también a la planta húngara de Kecskemét.
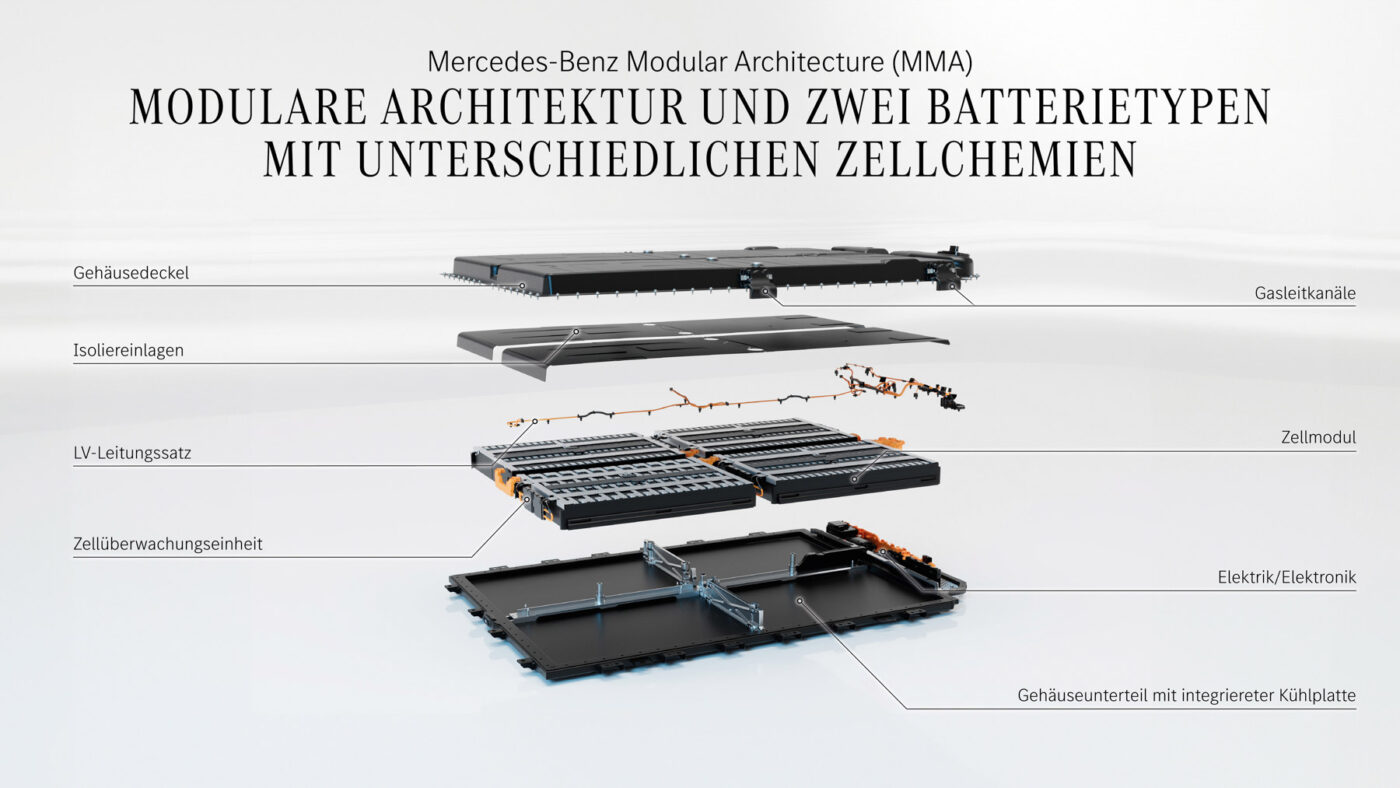
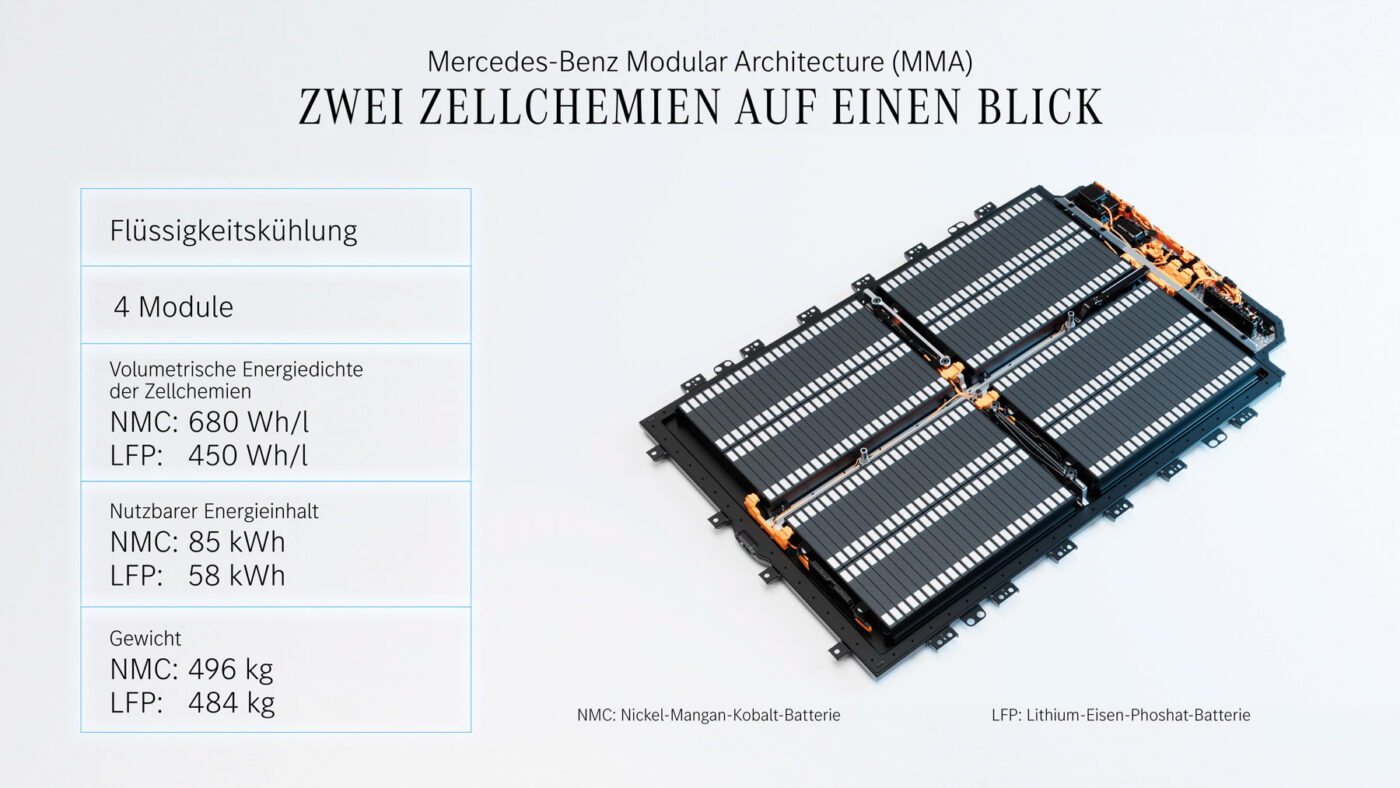
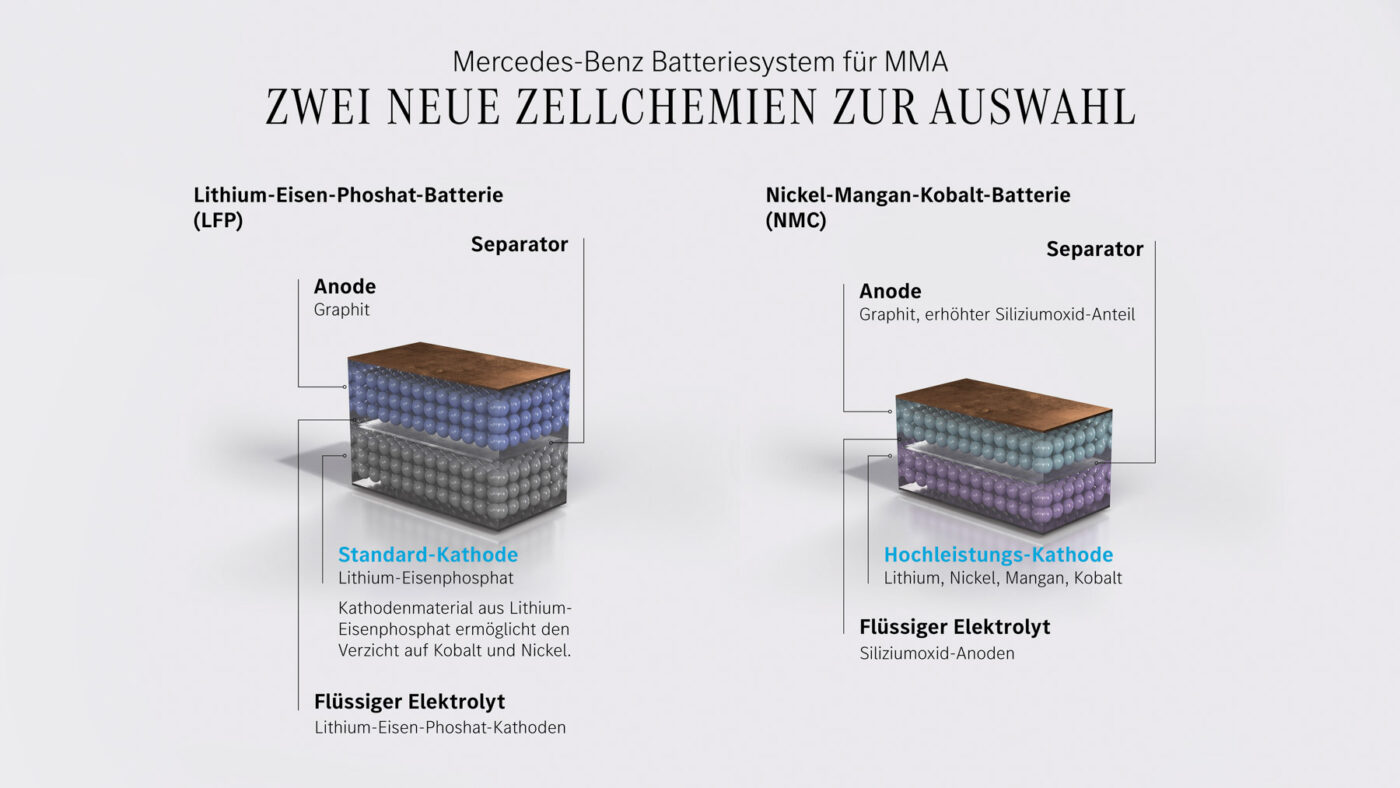
Las 192 celdas están combinadas en cuatro grupos de 48 celdas cada uno - 24 celdas están dispuestas una al lado de la otra. La base del pack de baterías consiste en un marco de acero con una bandeja de aluminio, donde también está pegado el sistema de refrigeración - por tanto, las células sólo se enfrían o calientan por la parte inferior. A continuación, los cuatro grupos de células se pegan en el pack. Esto tiene varias ventajas. En primer lugar, simplemente aumenta la rigidez y ahorra peso. En segundo lugar, no se producen virutas durante la producción, lo que contribuye a la fiabilidad y la estanqueidad.
Keller también habló de "una mezcla de célula a módulo y célula a paquete". Sí, Mercedes también utiliza adhesivos, pero a diferencia del concepto célula-a-paquete, no todo está pegado. Con el MMA, por ejemplo, la tapa de la batería se puede desenroscar. En cuanto se retira la capa aislante de debajo, los módulos, el mazo de cables y todas las conexiones de enchufe son accesibles desde arriba - y pueden sustituirse individualmente en caso de defecto.
Cargando
Ahí es donde entra en juego la eficiencia del tiempo. Es bueno para la autonomía que la conducción y la carrocería sean eficientes. Sin embargo, si el cliente se queda parado en la estación de carga durante 40 minutos, no llegará necesariamente antes a su destino que con un coche eléctrico, que consume un poco más pero se carga mucho más rápido. En el acto celebrado en Sindelfingen, Mercedes subrayó repetidamente la influencia que el prototipo Vision EQXX, también desarrollado en el Electric Software Hub, tuvo en el CLA y el MMA. El motor eléctrico es "muy similar" (aunque sin caja de cambios de dos velocidades), al igual que el diseño de la batería. Mercedes no mencionó que el CLA se diferencia claramente del EQXX en lo que respecta a la carga. Al fin y al cabo, este último se fabricó para que no se cargara durante más de 1.000 kilómetros y, en consecuencia, el rendimiento de carga era escaso.
Por supuesto, esto debe ser diferente para un coche de producción que debutará en 2025. Los tiempos de carga cortos son importantes para los clientes. Por eso Mercedes optó por un sistema de 800 voltios para el CLA, a diferencia del gran EQS. Hay más factores a favor de los 800 voltios además de la potencia de carga: el menor amperaje para la misma potencia significa que los cables pueden ser más finos y ligeros.
La potencia de recarga que alcanza el CLA no sería fácilmente posible con un sistema de 400 voltios y la infraestructura de recarga actual: la ficha técnica indica 320 kW en el pico. "Lo que es mucho más importante para nosotros que la potencia máxima: cuánta autonomía puedo recargar en diez minutos", explicó Torsten Eder. "¡Podemos alcanzar los 300 kilómetros!" Sus desarrolladores añadieron después que el tiempo de carga del diez al 80% es inferior a 22 minutos. Con dos paradas de carga de diez minutos cada una, deberían ser posibles 1.200 kilómetros.
Todas estas cifras se refieren a la batería NMC de 85 kWh. En Sindelfingen no se dieron más detalles sobre la variante LFP con sus 58 kWh. Así pues, tendremos que esperar al estreno mundial para conocer información más precisa sobre el comportamiento de carga.
En términos de diseño, el sistema de carga lleva un cierto parecido con los EPI del Grupo VW: Toda la tecnología de carga (para CA y CC) está instalada en la parte trasera, encima del paquete de baterías - Mercedes denomina a este componente "One Box". Como la tecnología de carga está situada bajo los asientos traseros, al menos los vehículos eléctricos MMA tendrán la conexión de carga en la parte trasera - un modelo de patinete expuesto en Sindelfingen tenía la toma CCS encima de la rueda trasera en el lado del pasajero. Se está intentando que los cables de alta tensión sean lo más cortos posible por razones de eficiencia. Sin embargo, es concebible que el puerto de carga se coloque en otro lugar, por ejemplo, cerca de la luz trasera - aunque la posición clásica del tapón de la gasolina es más probable.
El híbrido
La próxima versión híbrida del CLA no debe pasarse completamente por alto. Aunque la MMA se diseñó para coches eléctricos de batería, también permite una propulsión híbrida. Se lanzará después de la versión BEV y merece la pena mencionarlo para la electrive por una razón: aunque sólo es un híbrido de 48 voltios, el CLA puede circular de forma puramente eléctrica.
En concreto, se trata de un híbrido P2, en el que el motor eléctrico (también PSM en este caso) actúa sobre el eje de entrada de la transmisión de doble embrague de ocho velocidades con el poco manejable nombre de 8F-eDCT. Esto significa que es posible conducir en las ocho marchas con apoyo eléctrico y recuperarlas. Como hay un tercer embrague instalado en la unidad compacta de motor eléctrico-transmisión, el motor de combustión puede desconectarse por completo. Los 20 kW del motor eléctrico pueden utilizarse entonces para conducir de forma puramente eléctrica, no sólo a baja velocidad en ciudad, sino también, según los desarrolladores durante las pruebas de conducción, a velocidades de hasta algo más de 100 km/h si la velocidad debe mantenerse constante.
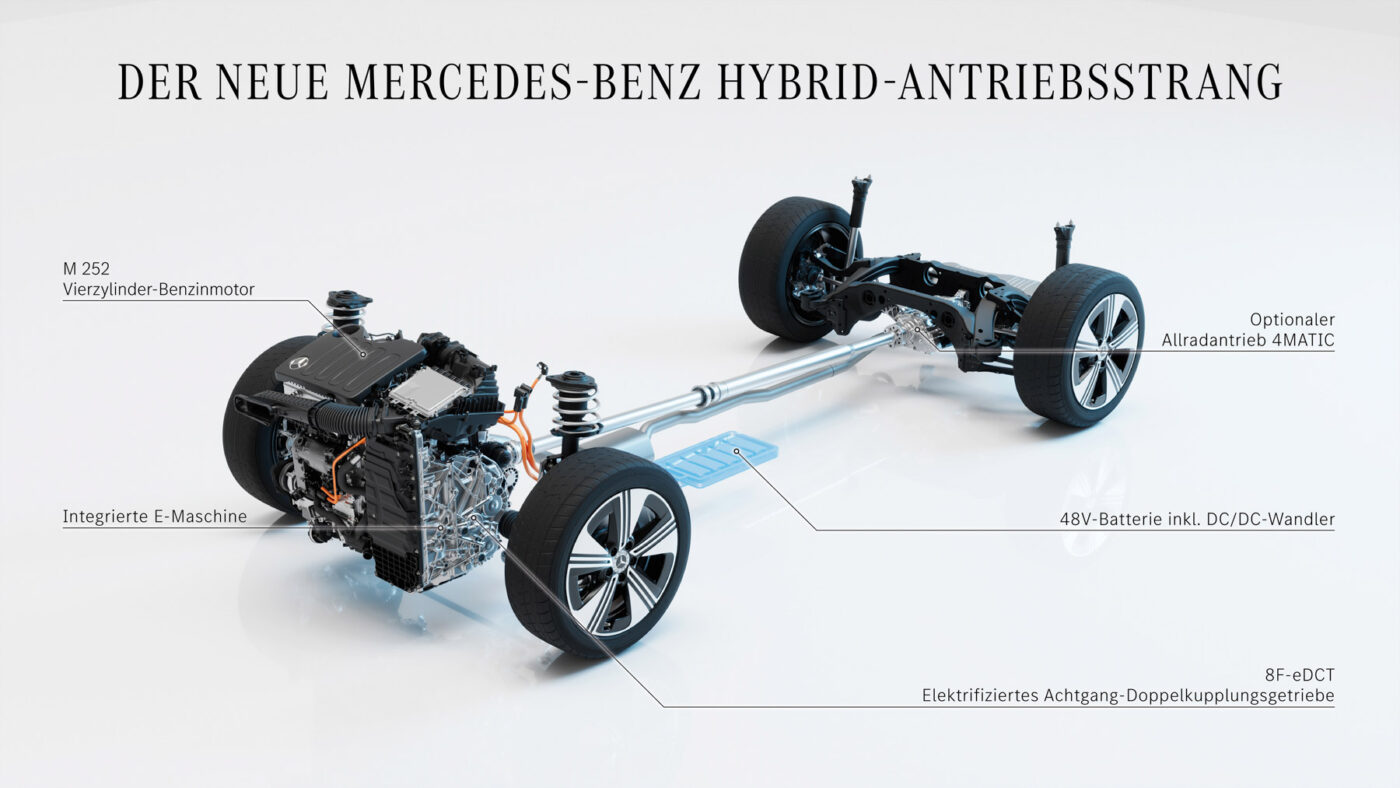

La batería tiene una capacidad de 1,3 kWh, de los que sólo 800 vatios-hora están destinados a la conducción. Mercedes no comunicará una autonomía puramente eléctrica ni la homologará.
El motor de combustión es un cuatro cilindros de 1,5 litros de nuevo desarrollo. Debido al limitado espacio de instalación diseñado para un pequeño motor eléctrico y un maletero en el coche eléctrico, todo el híbrido debe ser extremadamente compacto. Hay disponibles tres niveles de potencia con 100, 120 y 140 kW. Mercedes-Benz ha desarrollado el motor turbo de gasolina M252, pero no se fabrica en una planta de Mercedes. En su lugar, lo construye la filial de Geely, Aurabay China.
El centro de software eléctrico
El nuevo edificio, donde tuvo lugar gran parte del desarrollo, también contribuyó al CLA y al MMA. El ESH, como se le conoce internamente en Mercedes, es un centro de desarrollo interdisciplinar. No sólo trabaja en el software que da nombre a los coches eléctricos, sino que también lo fusiona con el hardware.
El ESH cuenta con varias plantas de oficinas y bancos de pruebas. Puede probar componentes de propulsión individuales o la arquitectura eléctrica completa con todos los componentes conductores de corriente, desde el pequeño sensor hasta el elevalunas eléctrico y la batería de 800 voltios, en diversas condiciones climáticas, y también vehículos completos.
"En el pasado, cada departamento desarrollaba sus propios componentes y, al final, todo se unía: motor, transmisión, chasis, bastidor, etc. Hoy en día, todo ha crecido conjuntamente", afirma el ingeniero de pruebas Philipp Werner. "En el Centro de Software Eléctrico, el software se desarrolla en las plantas superiores, y tenemos los bancos de pruebas de propulsores y vehículos en la planta baja. Si descubrimos un problema en el banco de pruebas de aquí, nuestros colegas pueden estar aquí con un portátil en cuestión de minutos".
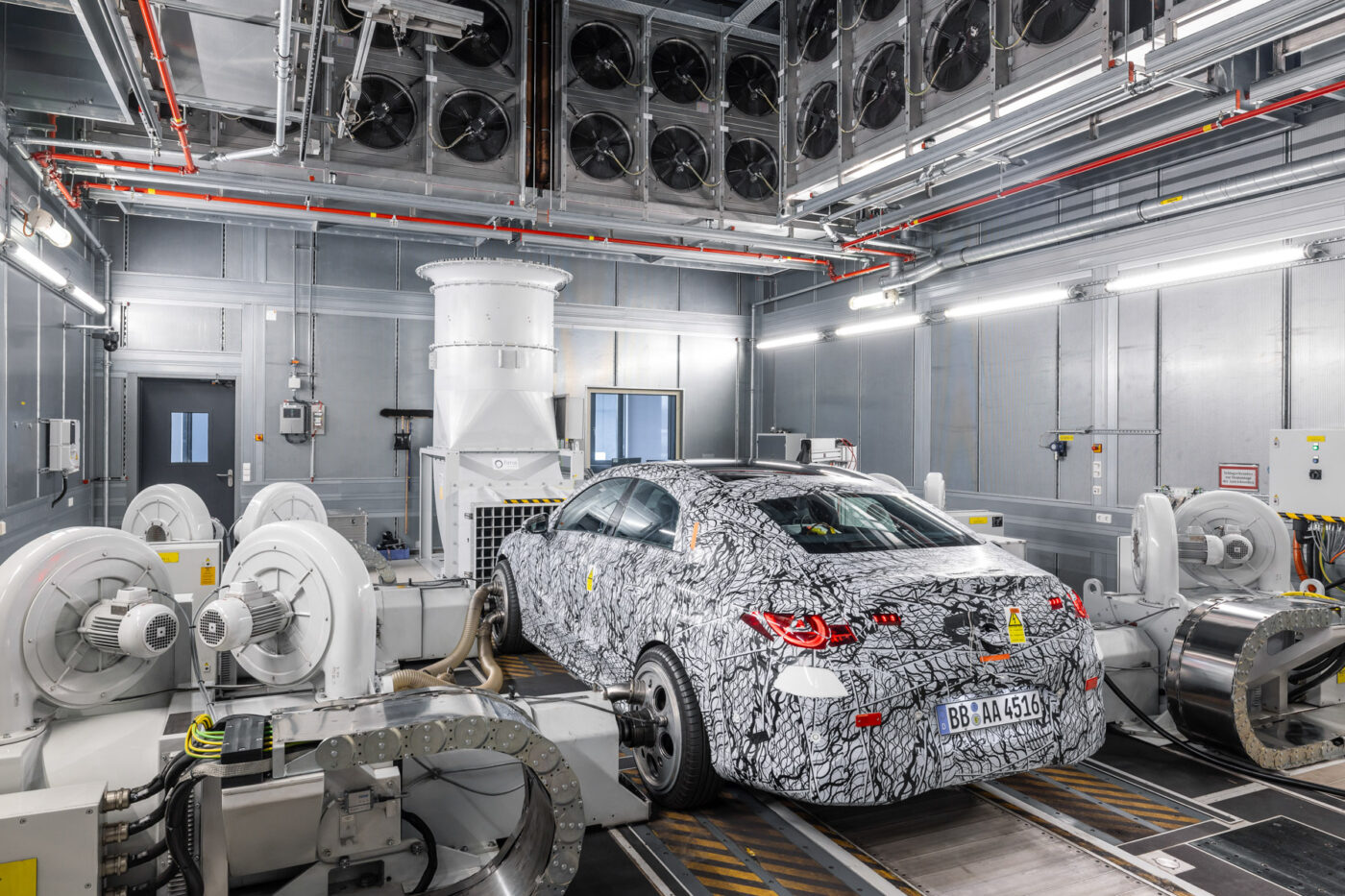
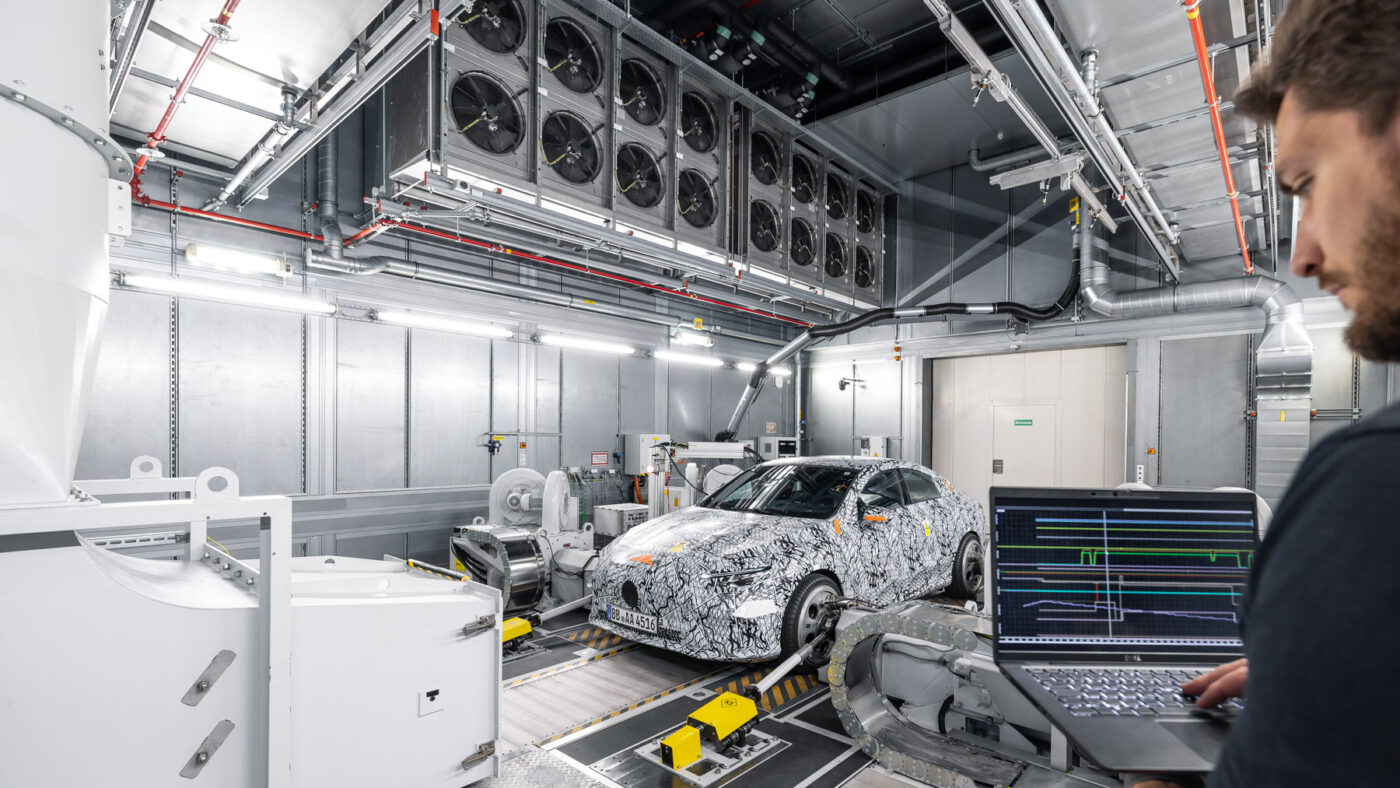
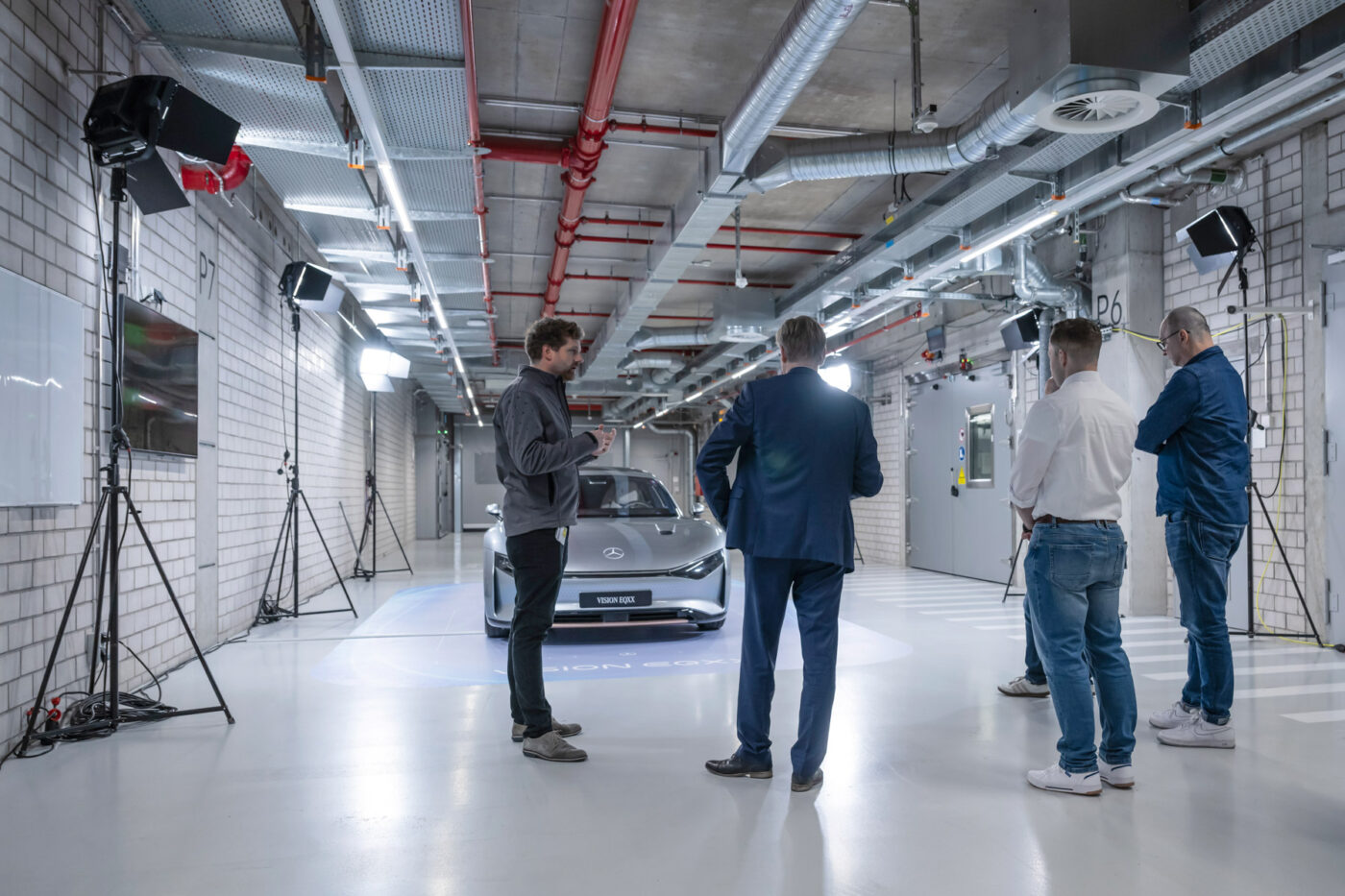
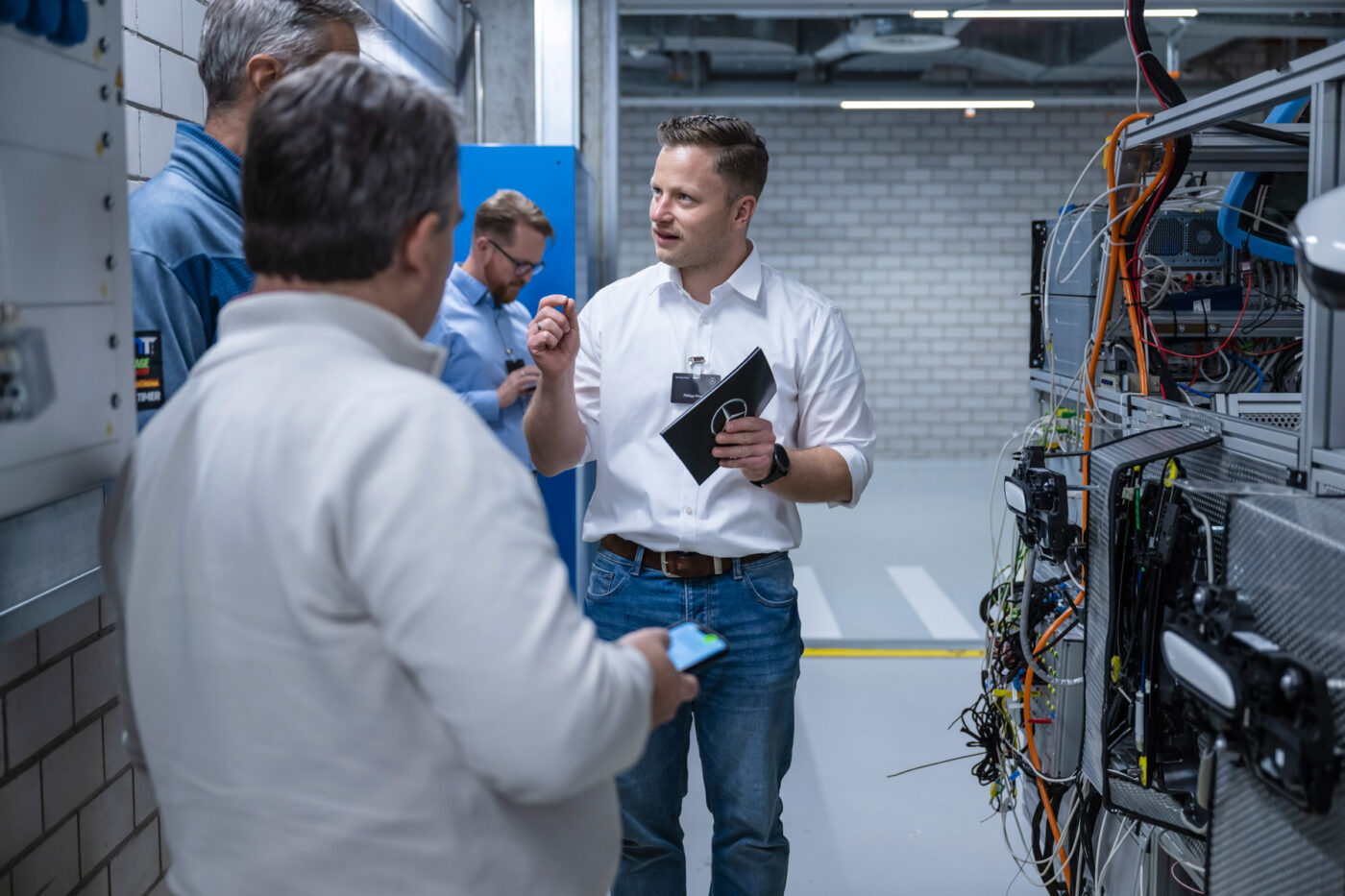
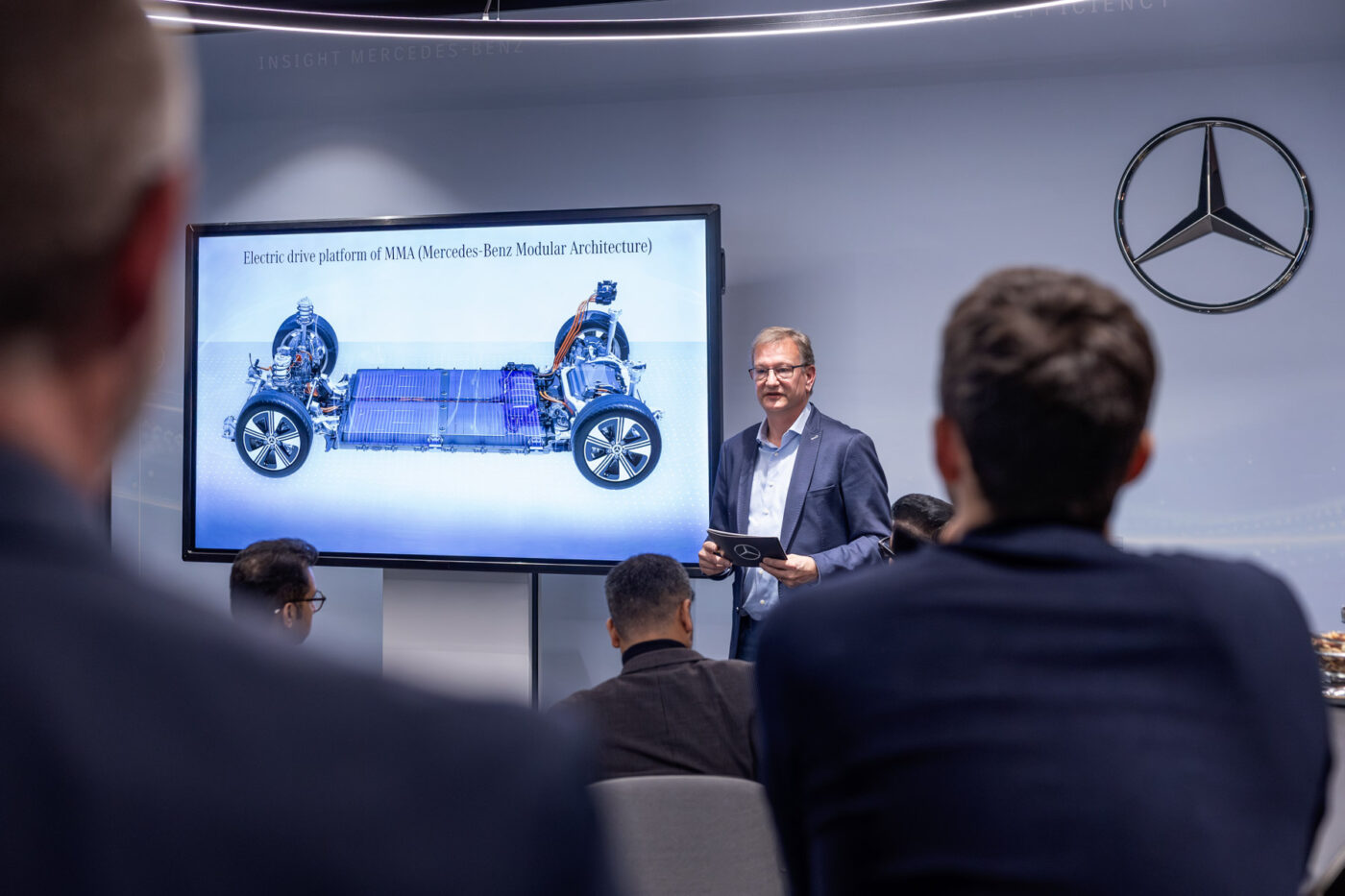
Los prototipos terminados pueden abandonar el "ESH" mientras permanecen conectados al lugar a través de la tecnología de medición. "Si nuestros colegas observan una anomalía en la carretera, ya sea en la Alb suaba, en el Círculo Polar Ártico o en el desierto, pueden pulsar un botón en el vehículo y se añade una bandera al registro de datos en ese lugar", explica Werner. "Entonces podemos acceder a estos datos en tiempo real y repetir este escenario exacto en el banco de pruebas hasta que hayamos resuelto el problema".
Los ingenieros también utilizaron los bancos de pruebas del ESH para preparar una conducción récord que demostrara el objetivo de "eficiencia en el tiempo". En la pista de pruebas de Nardò, en el sur de Italia, un vehículo de preserie del CLA recorrió la friolera de 3.717 kilómetros en 24 horas. El trayecto se planificó y supervisó desde el ESH, pero las simulaciones y los recorridos en el banco de pruebas son sólo una parte del trabajo: el hardware y el software también deben ser capaces de realizarlo en la práctica. Con una velocidad máxima de 210 km/h y 40 paradas de carga calculadas con precisión, el plan funcionó.
De hecho, ningún cliente del CLA se verá nunca en la situación de conducir más de 3.000 kilómetros a 210 km/h de un tirón. No obstante, el ingeniero de pruebas Werner ve un beneficio práctico para el cliente: "Por ejemplo, realizamos la comunicación habitual con la estación de carga en cada parada de carga, como hace cualquier cliente. Pudimos ahorrar unos segundos en este proceso". O como dijo Torsten Eder, Jefe de Desarrollo de E-Drive, mirando el panorama general: "La carrera de resistencia en Nardò demuestra que nuestras tecnologías también son fiables en la carretera".
0 Comentarios