Nissan quiere fabricar las primeras pilas de estado sólido en 2025
En el comunicado de prensa, Nissan no ha facilitado ninguna información sobre la capacidad de producción inicial ni sobre el aumento previsto en la planta piloto. En su lugar, se anuncia la contratación de 100 trabajadores por turno a partir del ejercicio que comienza en abril de 2028 para aumentar la producción a 100 megavatios-hora al año. Actualmente está previsto que la producción en serie de baterías de estado sólido comience en 2029.
La planta de Yokohama aún está en construcción: en la actualización, Nissan publicó imágenes de las salas de producción aún vacías. Las propias células y los procesos de producción se mejorarán con las baterías de estado sólido que se producirán a partir de 2025. Por este motivo, Nissan no proporciona ningún dato clave sobre el estado actual de la tecnología de las celdas en el breve comunicado, sino que se limita a declaraciones más generales. Según la empresa japonesa, las celdas de estado sólido "tienen el potencial de ofrecer aproximadamente el doble de densidad energética que las baterías de iones de litio convencionales, tiempos de carga significativamente más cortos gracias a un rendimiento de carga y descarga superior y costes más bajos gracias a materiales menos costosos".
Según Nissan, tiene previsto utilizar baterías de estado sólido "en diversos segmentos de vehículos, incluidas las camionetas, para que sus vehículos eléctricos sean más competitivos". Tampoco en este caso la empresa entra aún en más detalles. Sin embargo, Nissan lleva varios años trabajando en la tecnología de las pilas de electrolito sólido. Cuando se anunció la planta piloto de Yokohama en 2022, aún se decía que entraría en funcionamiento en 2024 y que la producción en serie comenzaría en 2028; en ambos casos, ahora es probable que sea un año más tarde.
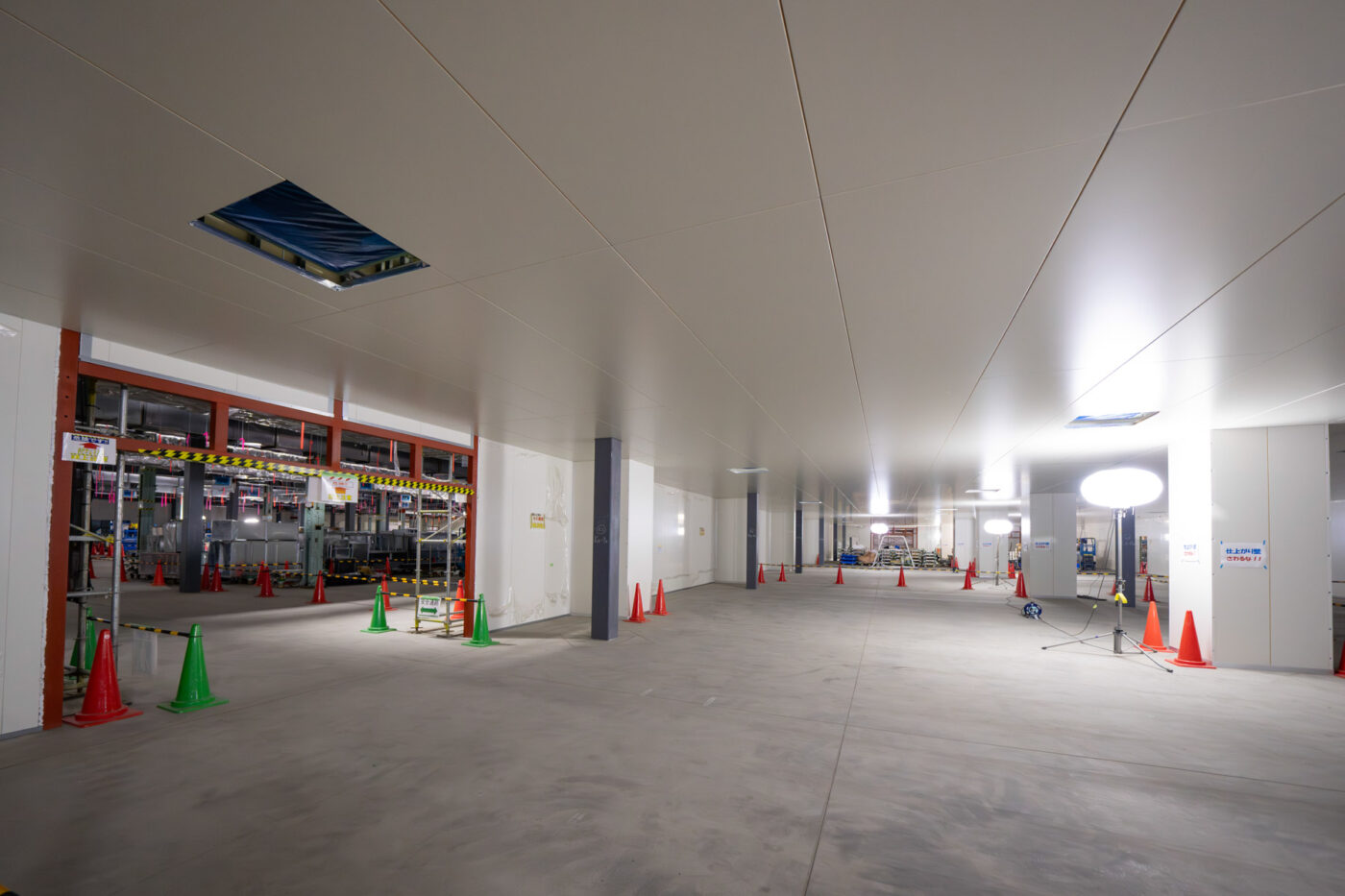
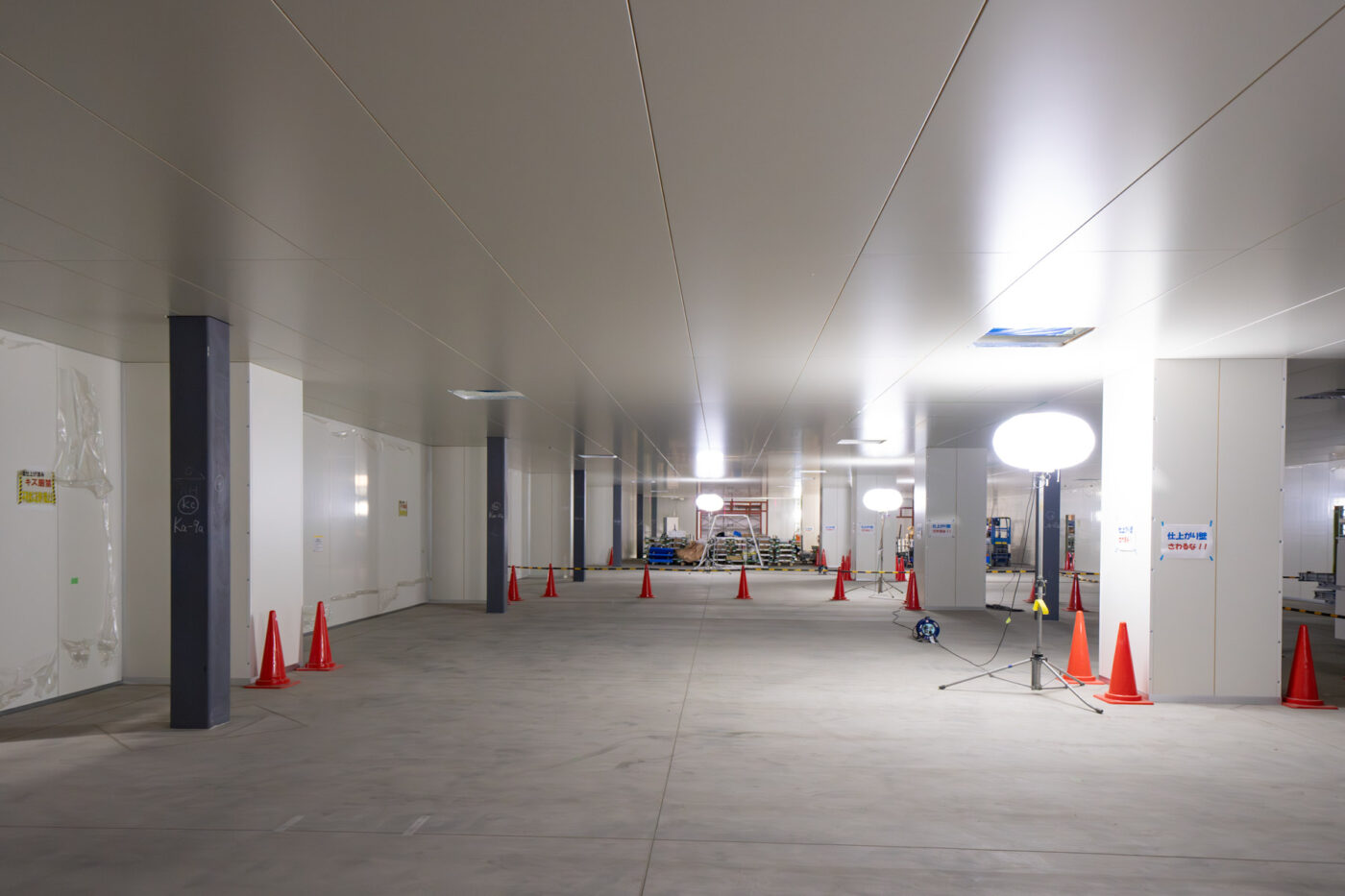
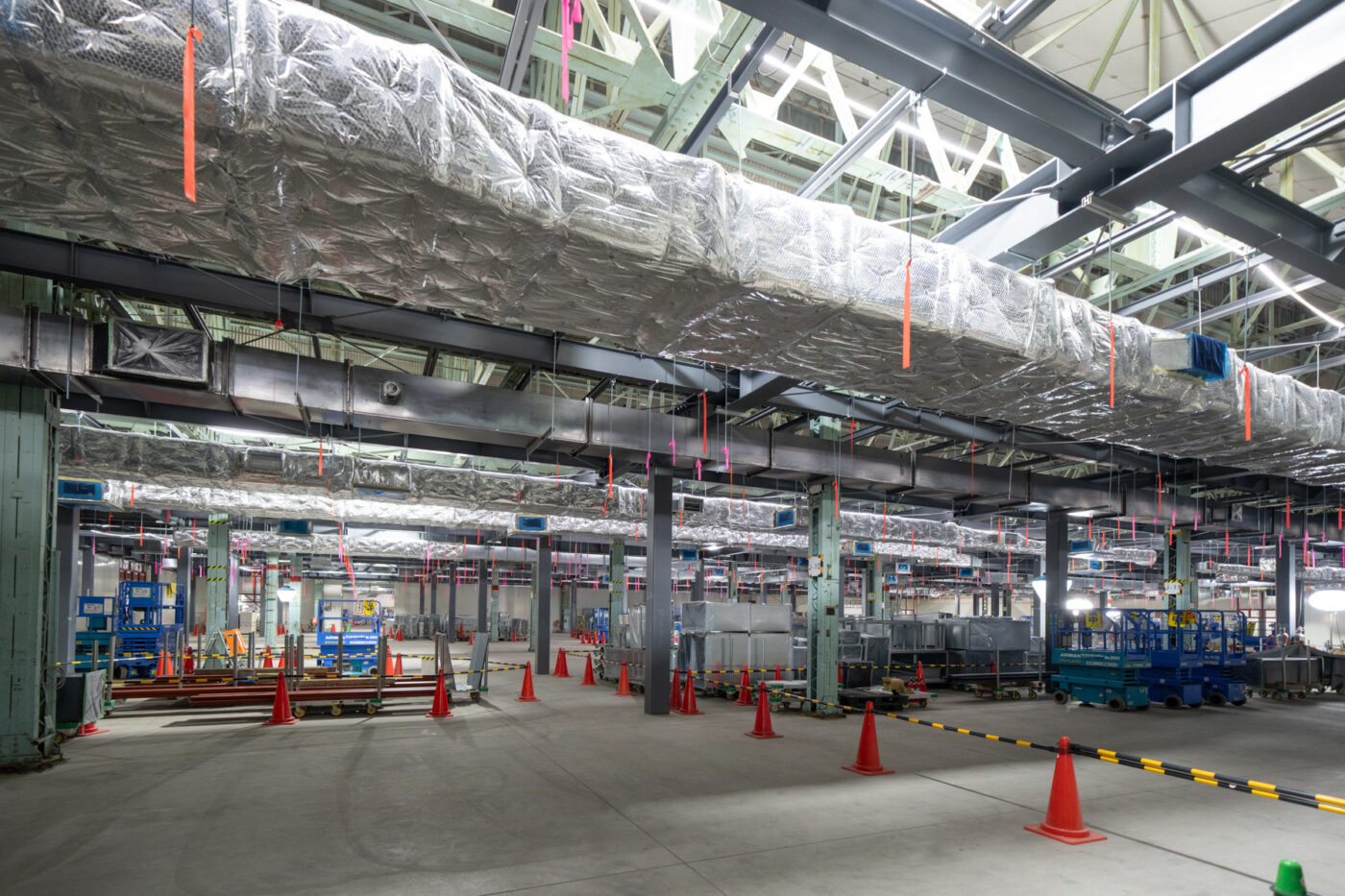
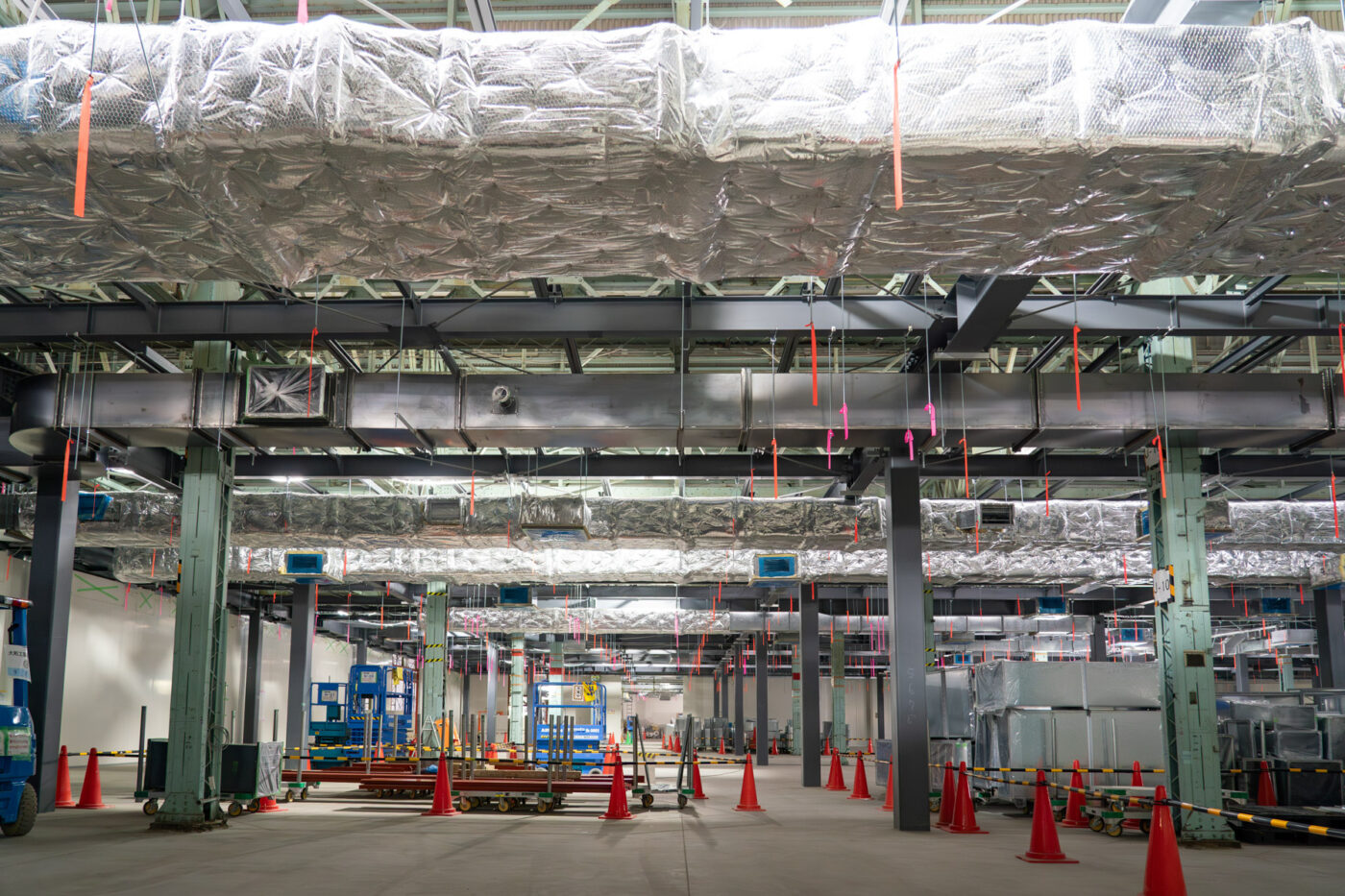
Sin embargo, Nissan no sólo quiere reducir costes en las baterías de sus futuros coches eléctricos: Según artículos de Reuters y Bloomberg, la empresa japonesa también quiere utilizar el proceso de gigafundición en la producción de coches eléctricos, es decir, para fabricar piezas de fundición de mayor tamaño en una sola pieza. En la planta de Tochigi se va a utilizar una máquina de gigafusión de más de 6.000 toneladas para producir la estructura trasera de la carrocería en forma de fundición de aluminio. Esto debería reducir los costes de fabricación en un diez por ciento y el peso de los componentes en un 20 por ciento en comparación con el proceso de producción actual, en el que se fabrican muchas piezas individuales y luego se unen.
Reuters cita a Hideyuki Sakamoto, Vicepresidente Ejecutivo de Fabricación y Gestión de la Cadena de Suministro, diciendo que Nissan "consideró varias cosas" para la producción de carrocerías. Sin embargo, al final se optó por la gran máquina de fundición a presión.
La producción de grandes piezas estructurales a partir de un único molde ha sido impulsada por Tesla en particular con sus proveedores de fábrica. Las ventajas (como también menciona Nissan) son el peso y los costes, ya que se ahorran muchos pasos de trabajo. Por tanto, la producción también es más rápida. Una desventaja es la reparación más costosa tras un accidente: las piezas individuales del bastidor ya no pueden sustituirse tan fácilmente si la estructura se fabrica a partir de un único molde.
0 Comentarios