Kamenz: Una visita a la fábrica de montaje de baterías de Daimler
La planta de montaje de baterías de Daimler en Kamenz es la piedra angular de una red de producción de baterías que abarca un total de siete plantas de producción en todo el mundo. Nuestros colegas de electrive.net pudieron acompañar recientemente el montaje de las baterías de Mercedes Benz: una visita exclusiva a la fábrica.
Un zumbido de actividad rodea aún los nuevos pabellones de Kamenz. Los obreros de la construcción y los artesanos están realizando los últimos trabajos en el exterior del edificio. Además, la nueva cantina sigue en construcción. Las cosas están más tranquilas en el interior de las nuevas naves de la fábrica. Dado que en el momento de nuestra visita la zona de las naves aún no estaba llena de instalaciones y equipos de producción, al entrar queda especialmente claro el tamaño del edificio, de unos 30.000 metros cuadrados, incluido el espacio logístico. En términos de espacio, sólo es visible la mitad de la nueva Planta 2. Detrás de un muro de protección contra incendios, hay una segunda nave de idénticas dimensiones. La ampliación cuadruplicará la superficie de producción y logística de la fábrica de baterías de Kamenz hasta un total de unos 80.000 metros cuadrados. En la Planta 1 adyacente, la filial de Mercedes-Benz Deutsche Accumotive produce baterías de propulsión para vehículos híbridos y eléctricos en serie desde 2012.
Mientras los nuevos aprendices se reúnen en islas de aprendizaje en la nueva planta, algunos empleados se preparan para la llamada línea de lanzamiento. Las primeras baterías de producción en serie para la Mercedes Benz EQC pronto se ensamblarán allí. Según Erhard Schletterer, Director General de Deutsche Accumotive, la línea de lanzamiento iniciará la producción en el primer trimestre del año. En el segundo pasillo también se pueden ver más líneas de producción automatizadas que se pondrán en marcha paralelamente este año.
Montaje de la batería en dos partes
Daimler demostró todos los pasos del proceso de montaje de baterías en la fábrica 1. Aquí es donde la filial de Daimler produce las unidades para el Smart ED, la eVito y los sistemas de 48 voltios, entre otros. En principio, el ensamblaje de una batería consta de dos partes: la producción del llamado front-end (módulo) y el back-end. En el ensamblaje del front-end, las celdas individuales se convierten en bloques de celdas. Sus dimensiones dependen de la aplicación. En el sistema de 48 V, hay doce células en cada bloque, en una batería híbrida, son 50. Un paso de trabajo vital aquí es la producción de uniones soldadas. Por ejemplo, hay que soldar los polos o las unidades de conexión de las celdas. Por último, el bloque de celdas se ensambla completamente con otros accesorios.
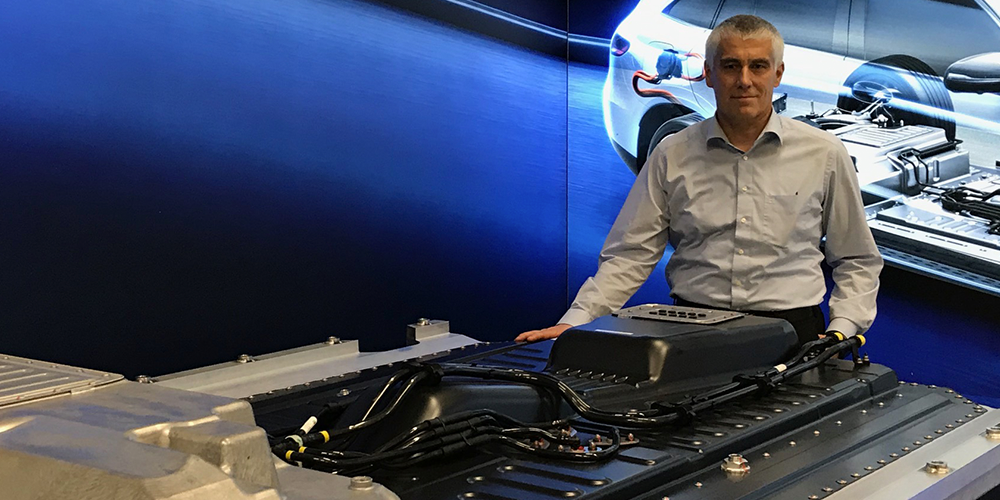
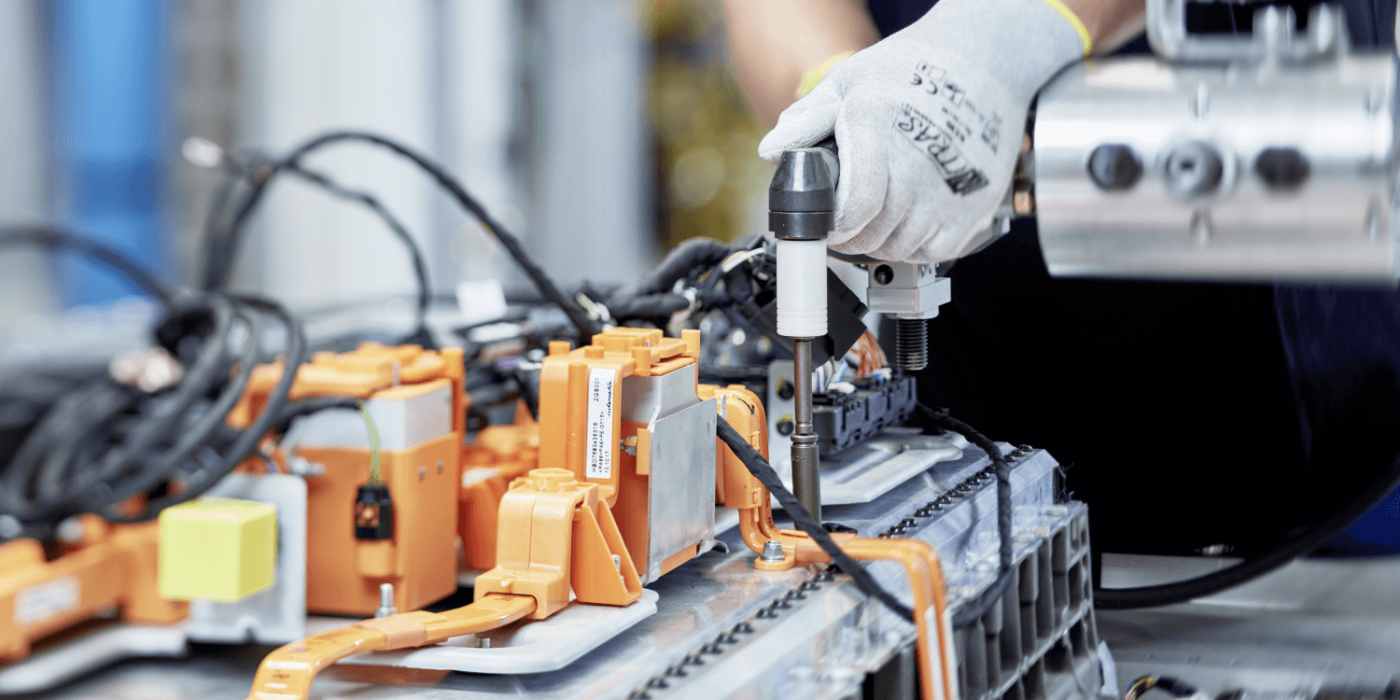
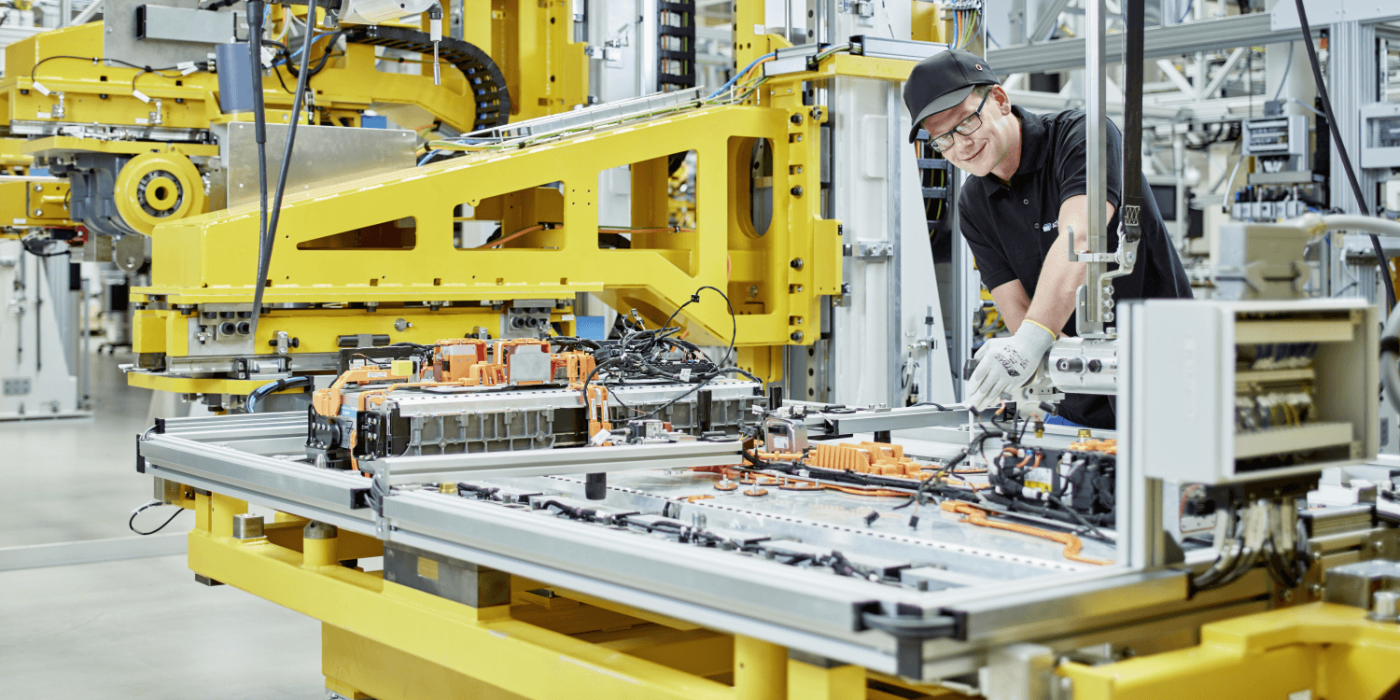
Durante el montaje posterior, los bloques se convierten en el producto final de la batería. En un paso, por ejemplo, se aplica una pasta conductora del calor a la parte inferior de la carcasa, mientras que en el siguiente se insertan los bloques en la parte inferior. A continuación, hay que fijar el cableado de alta tensión e instalar otros componentes, como el sistema de refrigeración, antes de poder sellar la batería con la parte superior. Por último, las unidades de almacenamiento de energía terminadas se someten a una prueba de fugas de helio y a una prueba de fin de línea para comprobar su funcionalidad eléctrica.
"En nuestra producción de baterías, tenemos una mezcla de actividades de montaje automatizadas y clásicas", explica Schletterer, quien, además de su cargo como Director General de Producción de eDrive en Daimler AG, es responsable de establecer y ampliar la red internacional de producción de baterías y de fabricar sistemas de pilas de combustible. Señala que, a pesar del considerable aumento de tamaño y peso de las baterías del EQC producidas en la Planta 2, las líneas del área frontal tienen un grado de automatización similar al de la producción de la batería inteligente.
Nueva dimensión de la batería EQC
Merece la pena echar un vistazo a los datos del producto para averiguar qué pasos de desarrollo ha dado ya la tecnología de las baterías. La batería Smart, que se fabrica en serie desde 2016, tiene un contenido energético de 17,6 kWh y una potencia pico de 76 kW (potencia continua: 47 kW). La unidad, que pesa unos 170 kilogramos, contiene precisamente 96 celdas.
La batería instalada en el eVito tiene una capacidad de 41,4 kWh y consta de tres módulos híbridos enchufables con 100 celdas cada uno y un contenido energético de 13,8 kWh cada uno. Uno de estos módulos sirve de batería en la Clase S, por ejemplo. La batería, que se fabrica en serie desde junio de 2017, pesa 110 kg. Los valores de la nueva batería del EQC se mueven en otra dimensión: en el acumulador de alto voltaje de 657 kg se alojan 384 celdas. La capacidad de la batería es de 80,5 kWh, y la potencia máxima es de 320 kW (potencia continua: 150 kW).
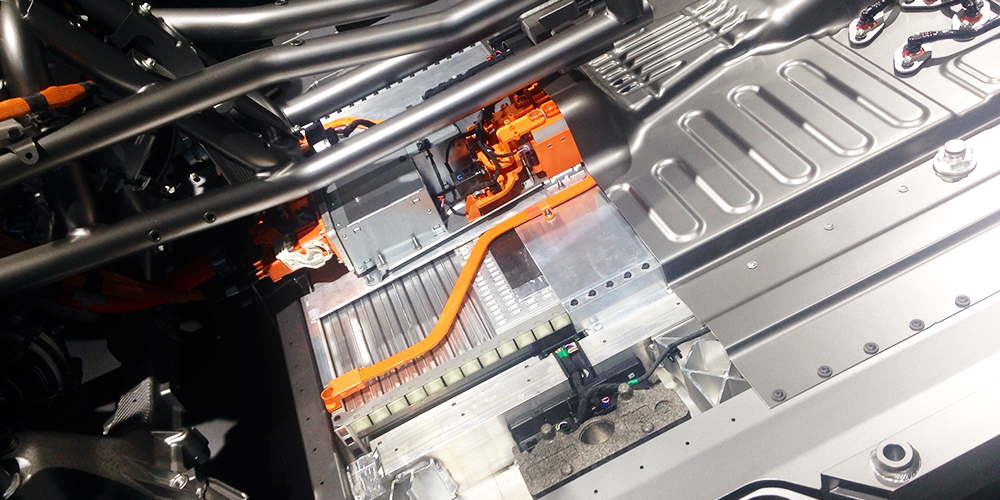
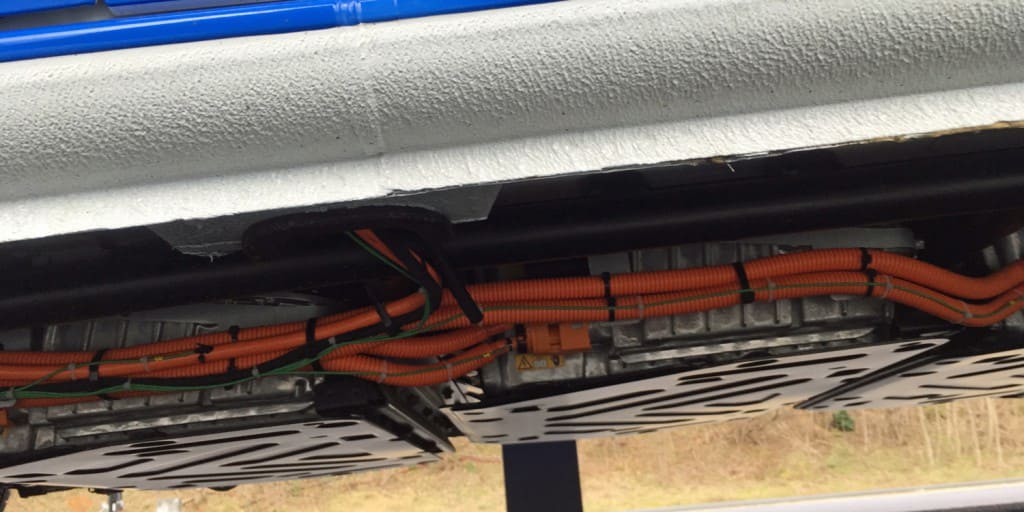
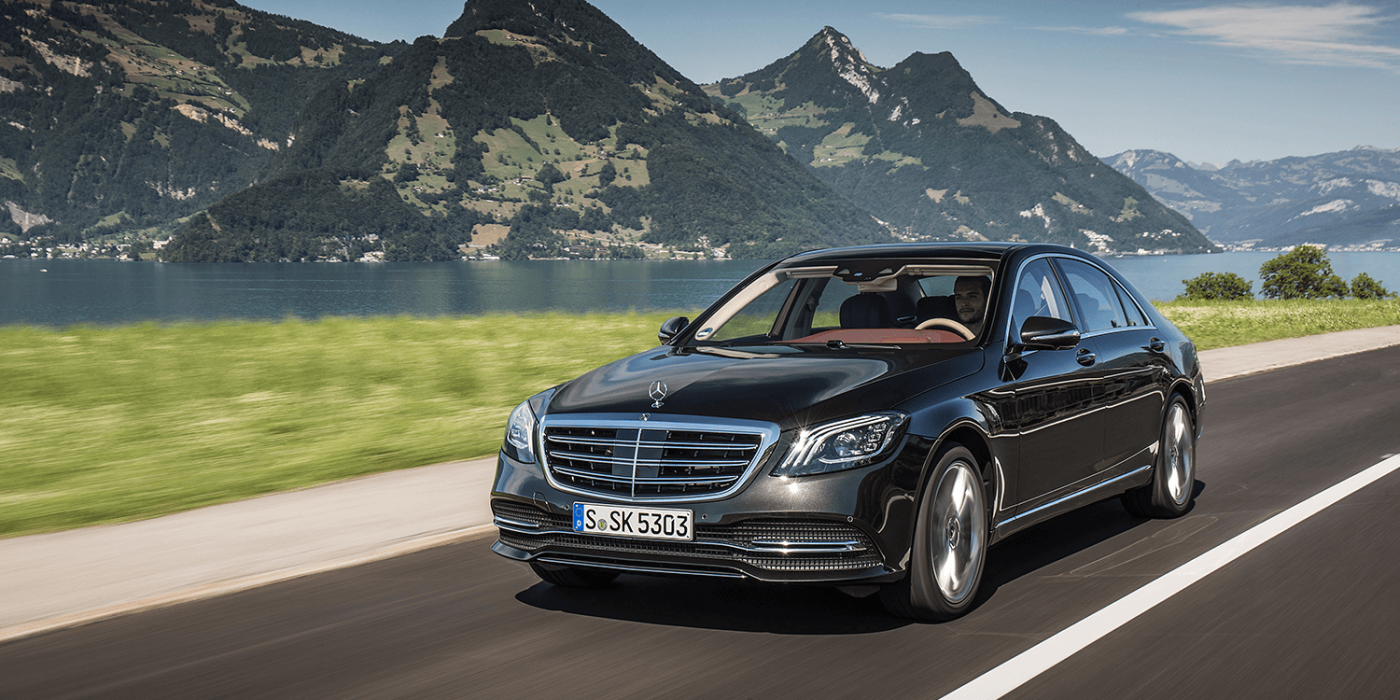
En la nueva producción de la unidad superior del grupo de Stuttgart se utilizan varias tecnologías nuevas, como una lógica de producción optimizada con producción en planta y en flujo, así como sistemas de transporte autónomos (AGV). Todo el diseño del edificio se basa en el flujo de producción y la disposición de las líneas. Además, un equipo especial de montaje pondrá las piezas a disposición de los trabajadores de forma ergonómica. No es de extrañar el uso de modernas tecnologías industriales 4.0, como el control digital y el seguimiento de los sistemas de producción. Esto garantiza, entre otras cosas, la trazabilidad completa de los componentes instalados en cada batería suministrada, incluyendo los datos completos de producción. Según Schletterer, la empresa es líder mundial en este campo. Pero estos no son los únicos puntos de venta únicos. También están trabajando en líneas muy flexibles capaces de producir varias series. Sin embargo, no se puede engatusar al director gerente para que revele más secretos de fabricación a este respecto.
Cualificación para trabajar bajo alta tensión
Un reto importante en Kamenz es el rápido crecimiento del personal: a finales de 2018, el número de empleados había duplicado a unos 1.000, un objetivo que se alcanzó un año antes de lo previsto inicialmente. "La mayoría de los empleados tienen formación en ingeniería eléctrica", subraya Schletterer. No obstante, en Daimler no se deja nada al azar. "Nuestras instalaciones de producción están diseñadas según las normas de seguridad más estrictas. Además, nuestros empleados se someten a programas especiales de cualificación en los que se les forma intensivamente en el uso de la tecnología de alta tensión en condiciones de producción", informa el director gerente.
La importancia de la ubicación también se desprende de la inversión total realizada. Del volumen de inversión de mil millones de euros destinado a la red mundial de producción de baterías, alrededor de la mitad se destinará a Kamenz. La red consta de nueve fábricas en siete emplazamientos de tres continentes. Al inicio de la producción en serie en la segunda fábrica de Kamenz este año le seguirá la producción de baterías en Pekín, donde ya se están montando las primeras instalaciones de producción. Además, la planificación incluye otras dos fábricas cerca de Stuttgart, una en el emplazamiento de Sindelfingen, y una en Bangkok y Tuscaloosa (EE.UU.). Daimler también construirá una fábrica de baterías en Jawor, Polonia. Cada una de las plantas producirá para el mercado local. Una norma de aplicación mundial para las fábricas de baterías en lo que se refiere a "ajuste y organización" pretende garantizar al grupo automovilístico suabo una calidad uniforme de sus productos.
Mayor desarrollo de la tecnología celular
Por supuesto, se presta especial atención al componente más crítico de una pila: la célula. Éstas se desarrollan previamente con los proveedores y se especifican según un pliego de condiciones de los componentes, que incluye parámetros como las características de rendimiento. "Al fin y al cabo, sabemos lo que el sistema global debe ser capaz de hacer", explica el director gerente Schletterer. El grupo automovilístico con sede en Stuttgart tiene previsto ampliar su experiencia en la evaluación técnica de células y actividades de investigación y desarrollo. Esto afecta tanto a la optimización de la generación actual de sistemas de iones de litio como al desarrollo ulterior de las células adquiridas en el mercado mundial, así como a la investigación de la próxima generación de los llamados sistemas post-litio-ion.
Poco antes de finales del año pasado, la firma de un contrato para la compra de pilas por valor de 20.000 millones euros causó una pequeña sensación. Según el comunicado de prensa correspondiente, el pedido, válido hasta 2030, garantiza el suministro de células con la última tecnología. El director gerente Schletterer explica la orientación estratégica de la siguiente manera: "Queremos ser tan flexibles en el aprovisionamiento que siempre podamos elegir al proveedor con la mejor relación precio/rendimiento". Independientemente de ello, su equipo de Kamenz tendrá mucho trabajo en los próximos años.
Informes de Michael Nallinger
1 Comentario