BMW introduces sixth drive generation
Pre-series production of the drives has been underway since September 2024. The pre-series motors are being intensively tested and some of them are already being used in the Neue Klasse test vehicles from the Debrecen plant. Series production of the next iX3, the first series based on BMW’s ‘Neue Klasse’ vehicle family, is due to start there this year.
Although BMW had already developed highly efficient motors with the so-called fifth generation of its electric drives, which are used in the current model series from the iX1 to the i7, the Munich-based company is now talking about a ‘technological leap forward’ – not only with the drive systems, but also with the battery.
Let’s first take a look at the electric drives of the ‘Gen6’. Here, BMW is sticking to the concept of the SSM – the current-excited synchronous machine. The magnetic field in the rotor is not generated by permanent magnets, but by a winding energised with direct current. “On this type of synchronous motor, the magnetic field in the rotor is generated by windings fed with direct current rather than permanent magnets. In this way, the strength of the rotor’s magnetic field can be optimally adjusted to the prevailing load conditions. This results in both excellent levels of efficiency at customer-relevant operating points and constant power output at high rotational speeds,” writes BMW. However, the SSM has been further developed in order to be optimised for the new 800-volt architecture. According to BMW, the oil and water cooling systems have also been completely redesigned and the housing is lighter yet more rigid.
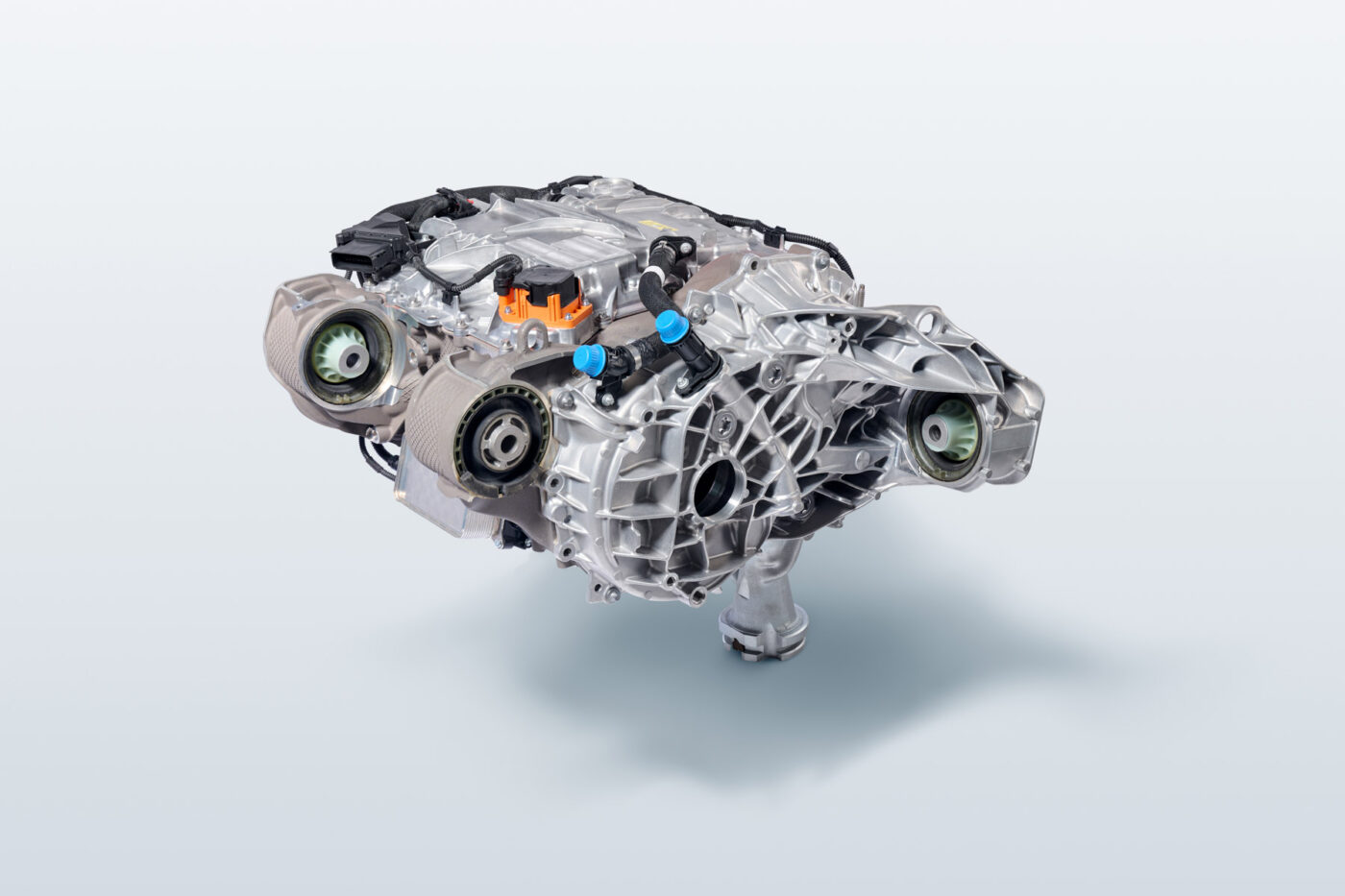
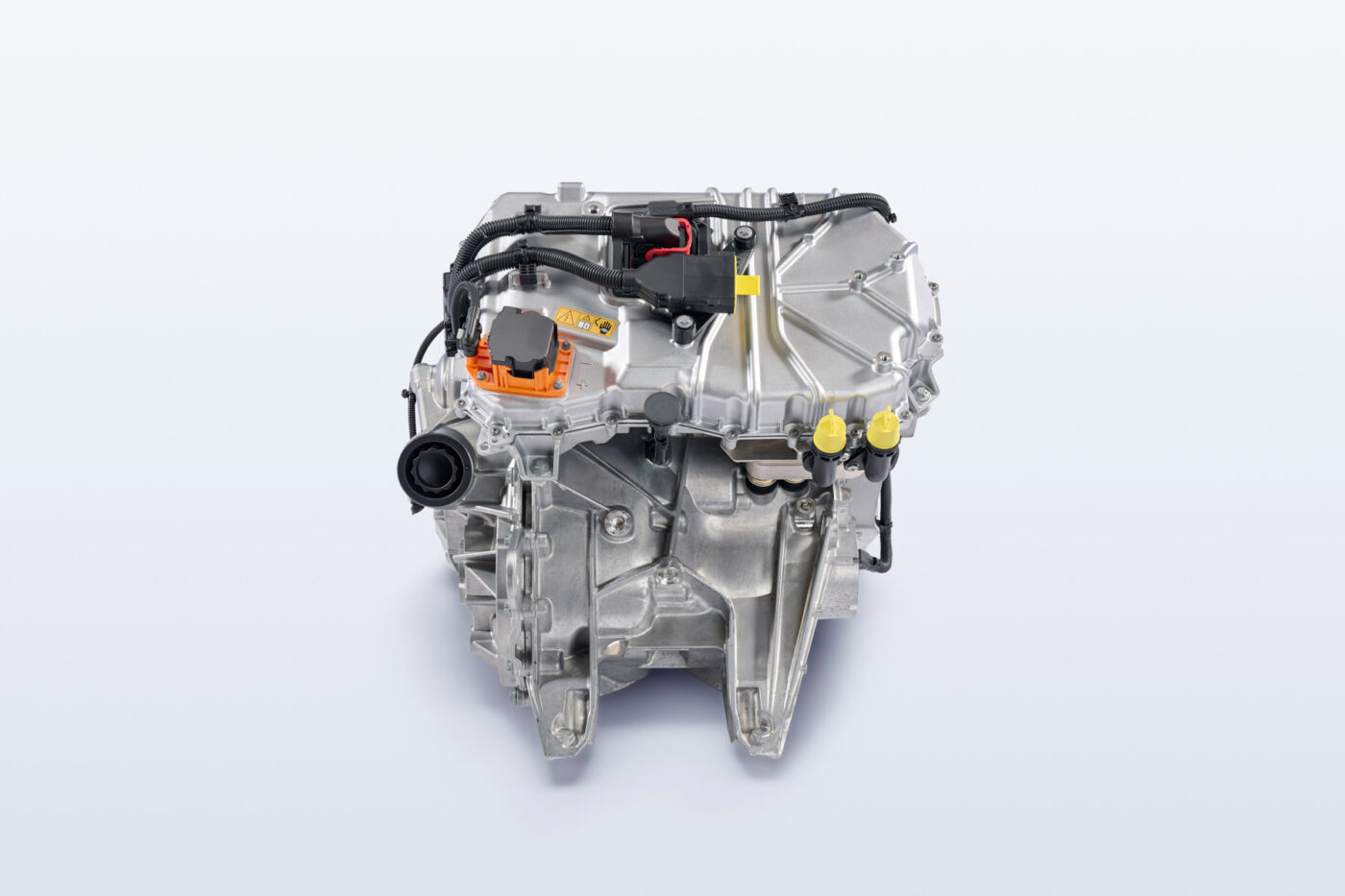
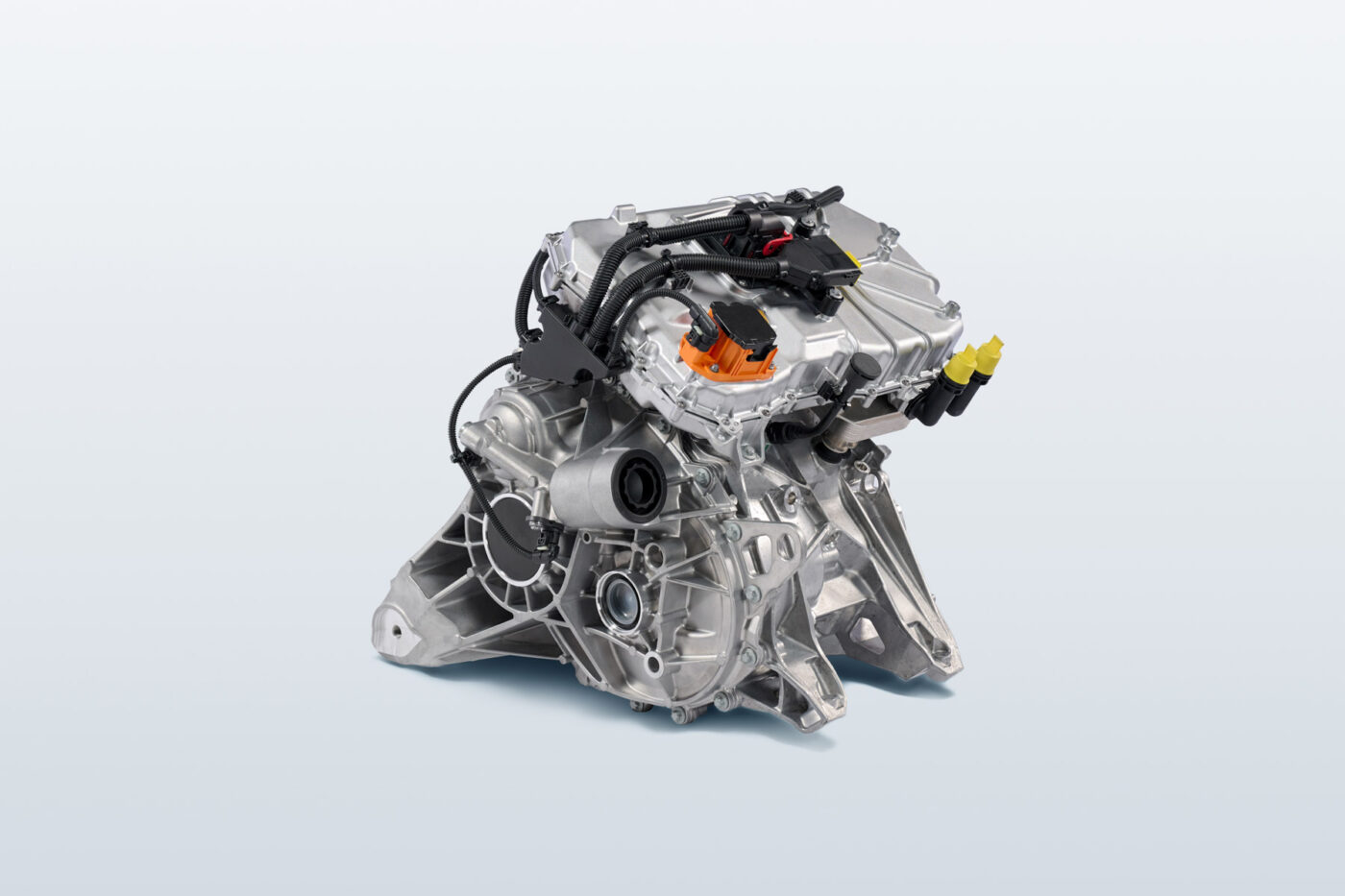
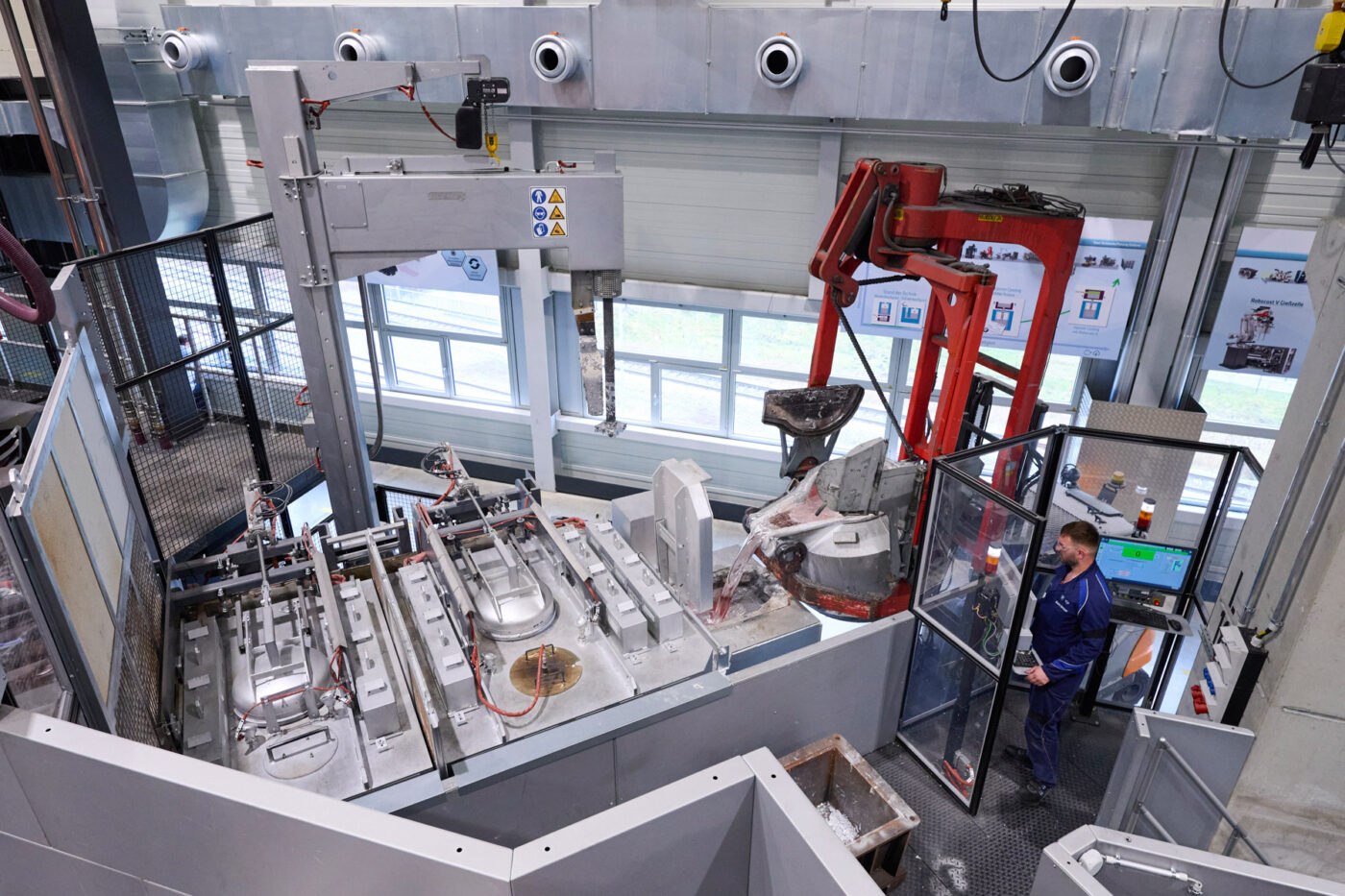
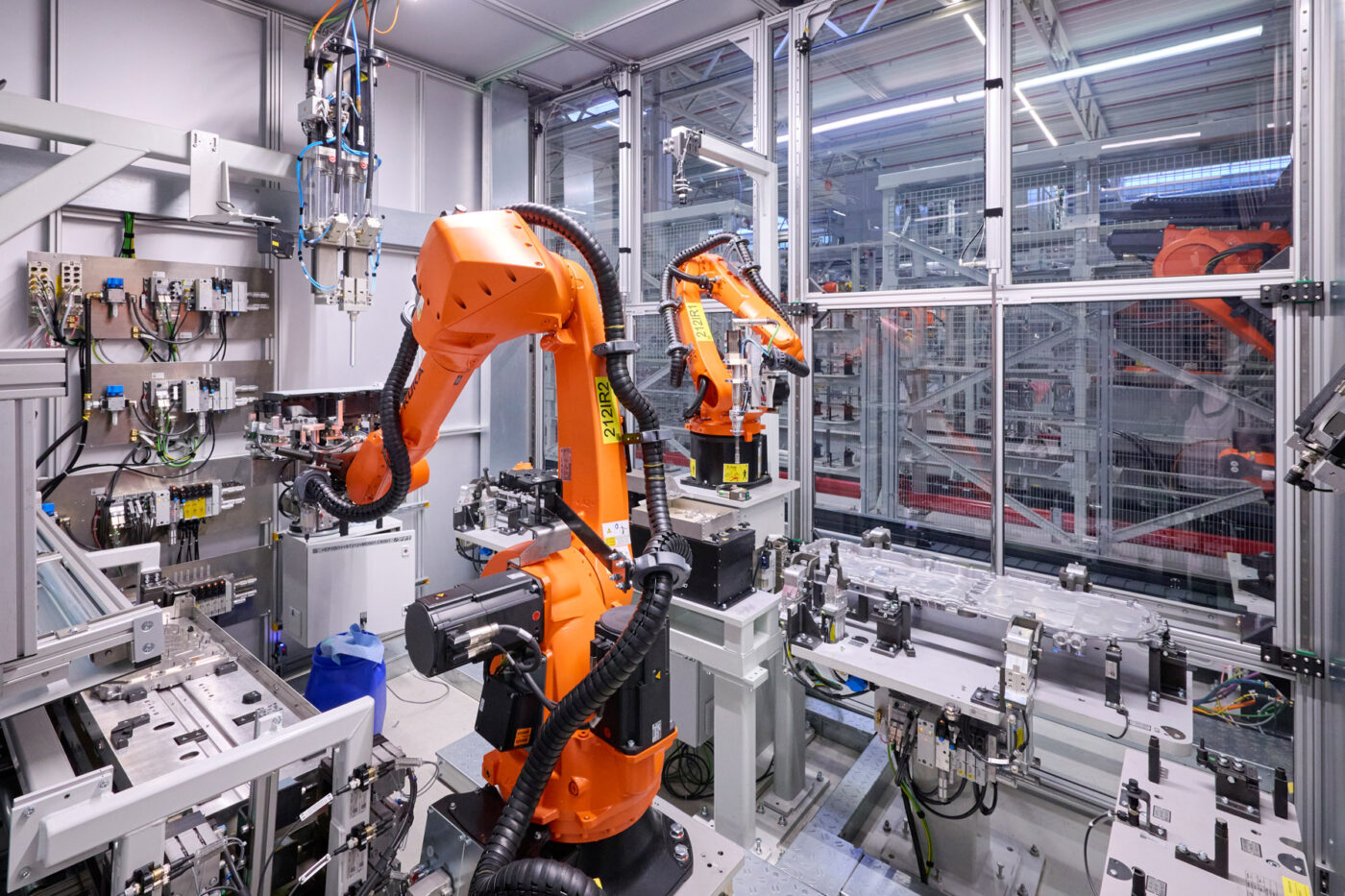
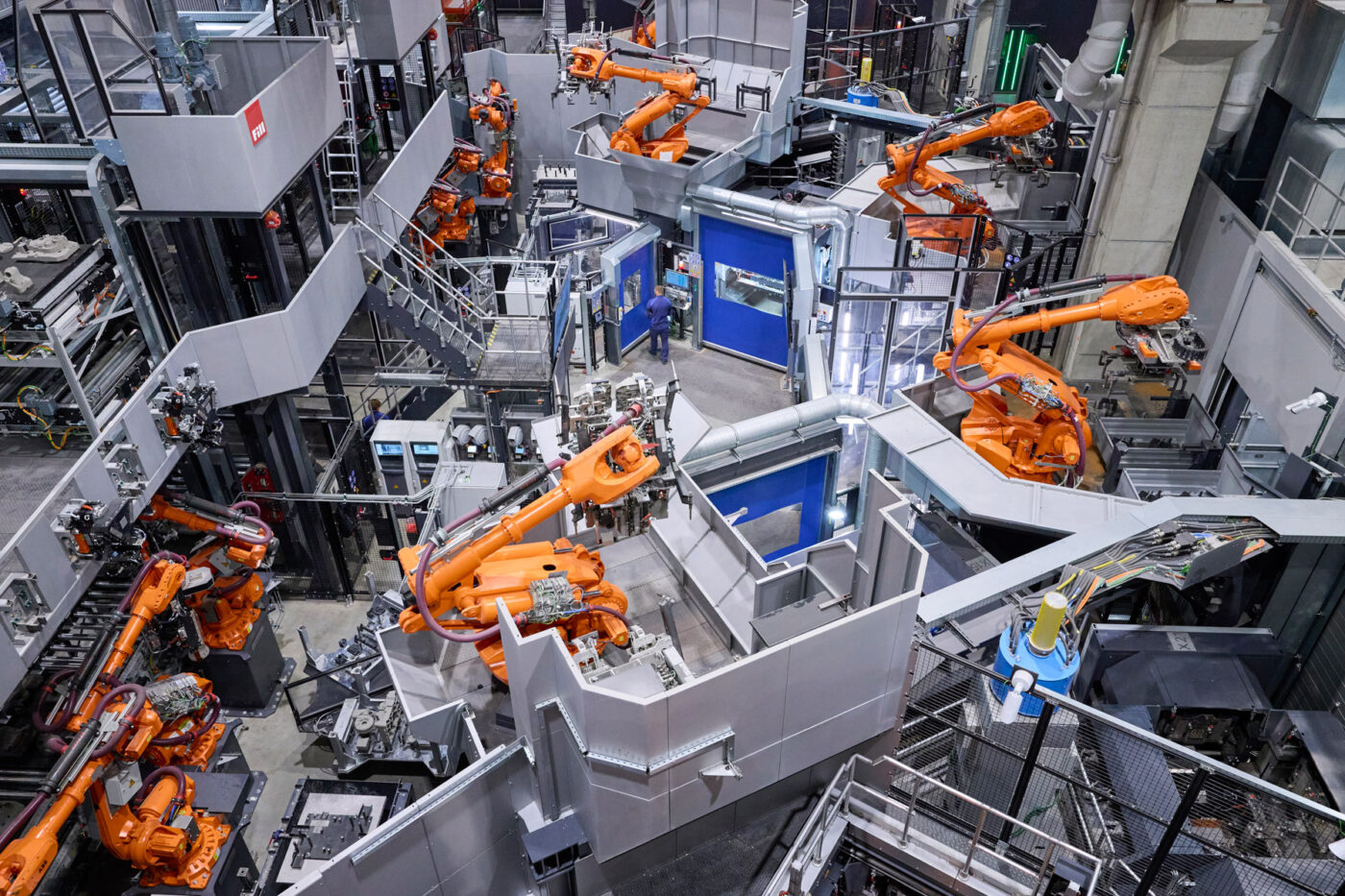
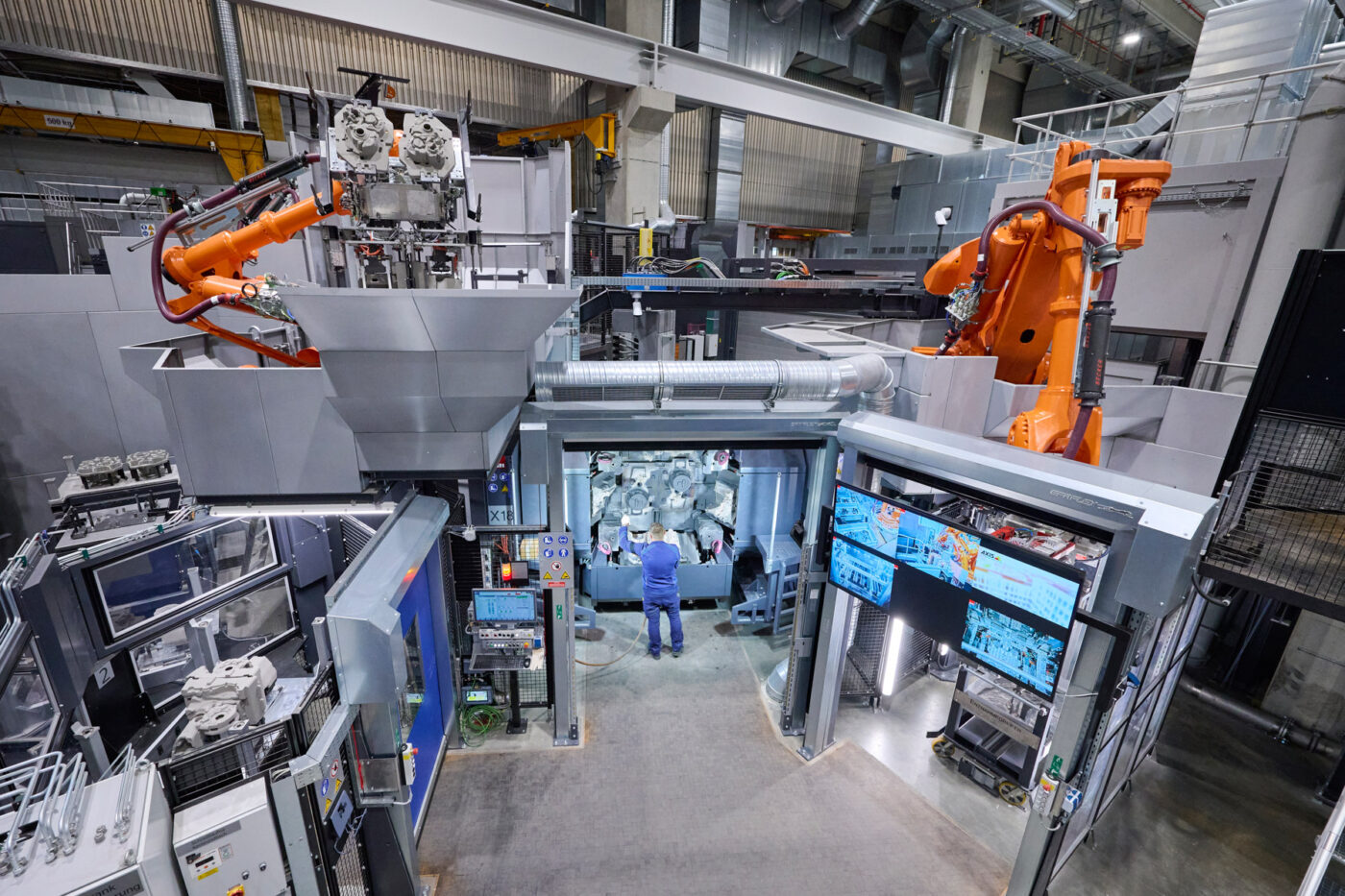
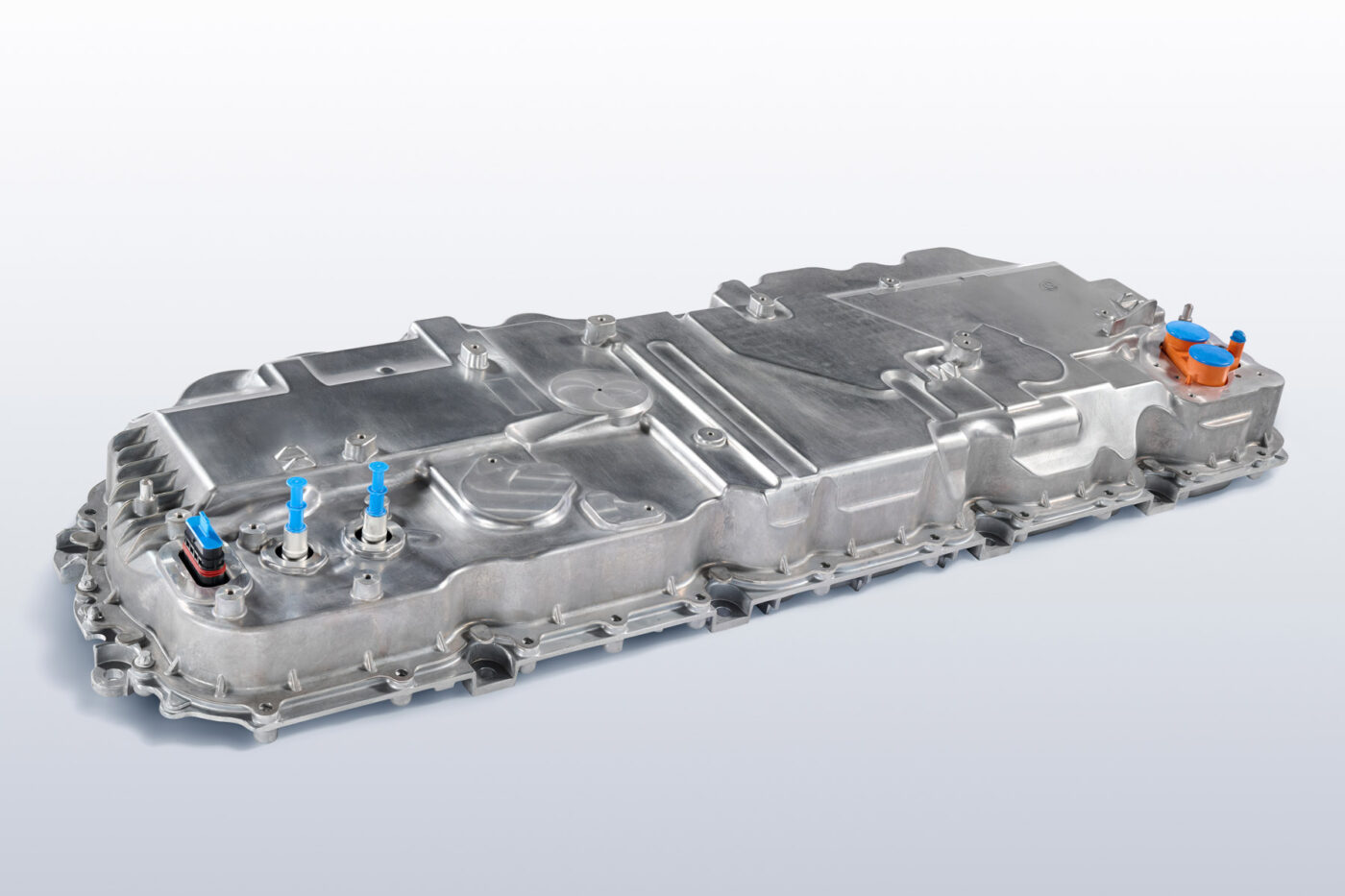
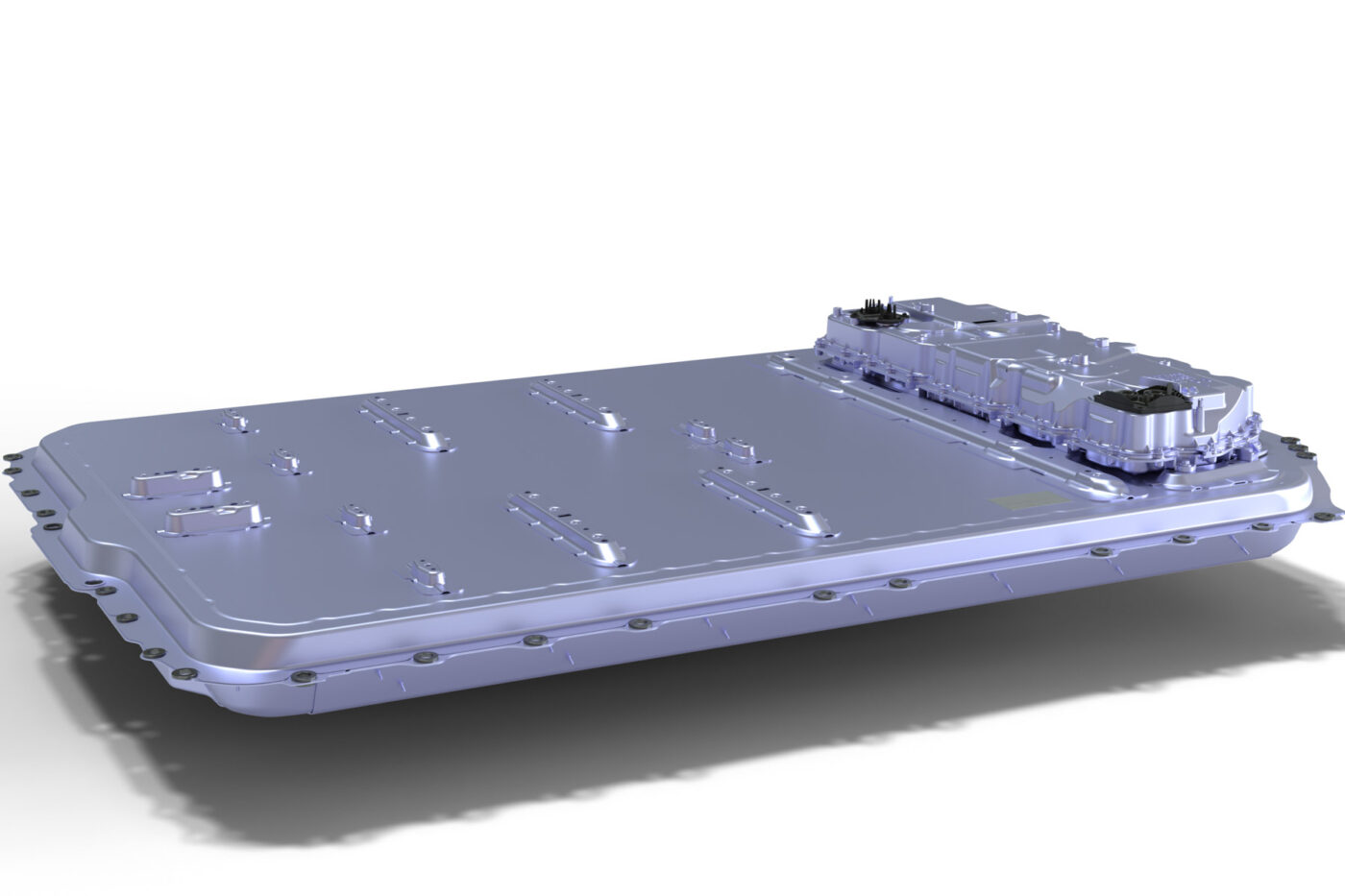
While the ‘Gen5’ relied exclusively on this SSM in different variants, only the drive units on the rear axle will work according to this principle in the Neue Klasse. For the all-wheel-drive models, which also have a second electric motor on the front axle, a different technology will be used in future. Here, BMW will use an asynchronous machine (ASM), in which the magnetic field of the rotor is generated by induction through the stator. In the press release, BMW only lists the advantages of this technology: ASMs are generally smaller and cheaper. BMW does not mention the usual disadvantages, such as higher consumption due to poorer efficiency in the partial load range. Audi and Mercedes used to rely on ASMs, but later switched to PSMs with permanent magnets in the rotor due to their consumption. So it will be exciting to see what consumption BMW can achieve on the road.
BMW nevertheless anticipates noticeable improvements ‘through the intelligent use of new technologies in e-drive and the consistent further development of existing systems’. When comparing one of the future all-wheel-drive models of the new class with SSM at the rear and ASM at the front with an xDrive model of the ‘Gen5’, energy losses are to be reduced by 40 per cent, costs cut by 20 per cent and weight reduced by ten per cent. Overall, the overall vehicle efficiency in the Neue Klasse is set to increase by 20 per cent.
“By combining different types of electric motor, the BMW Group’s technology-open approach is therefore clearly in evidence within the field of electric mobility,” the press release states. Furthermore, there will also be all-wheel-drive vehicles with more than two motors: “In future, customers will be able to choose from models equipped with one, two, three or four electric motors to suit their individual preferences and requirements,” says BMW. BMW recently presented a test vehicle for the new central computer called ‘Heart of Joy’, which will have to coordinate up to four motors in the future.
While the electric drives, including the inverter developed in-house with silicon carbide semiconductors, are produced in Steyr and distributed to the plants, BMW is pursuing a different strategy for battery production. It is to be placed ‘local for local’ close to its vehicle plants. As reported, such a battery assembly plant is being built for the German plants in Irlbach-Straßkirchen (Lower Bavaria); other locations are close to the vehicle plants in Debrecen (Hungary), Shenyang (China), San Luis Potosí (Mexico) and Woodruff near Spartanburg in the USA. ‘The “local for local” principle continues in the supplier network for battery cells,’ says BMW. ‘To cover the demand for the Gen6, the BMW Group has contractually agreed five battery cell factories – spread across Europe, China and the USA – with various partners.’
But the battery in the ‘Gen6’ is also fundamentally new: as has long been known, BMW is switching from a 400-volt architecture to 800 volts system voltage and from prismatic cells to large-volume round cells with a diameter of 46 millimetres. The round cell alone is said to offer a 20 per cent higher energy density than the previous prismatic cells. The new battery pack dispenses with modules and also takes on the role of a structural component in the bodies of the Neue Klasse vehicles (‘pack-to-open-body’). This also ensures that more cells can be accommodated in the same installation space, thus increasing the energy density at the pack level. BMW also claims a 30 per cent higher charging speed and a 30 per cent greater range – “with certain models achieving even higher figures”.
‘BMW Energy Master’ comes from Landshut
The ‘BMW Energy Master’ will also be an important component in the new electric drive generation. This is a kind of energy control centre which, according to BMW, acts as an interface for the high-voltage and low-voltage power supply as well as for the data from the high-voltage battery. In other words: on the one hand, the Energy Master ensures ‘safe and intelligent operation of the high-voltage battery’ and thus its durability. In addition to the power requirements of the low-voltage applications, it also controls the power supply to the electric motors, i.e. it talks to the ‘Heart of Joy’ drive computer. Both the hardware and the software of the Energy Master were developed entirely in-house at the BMW Group. Thanks to the in-house development, BMW also wants to be able to implement technological developments and updates for the vehicles ‘independently and in real time’ by means of remote software upgrades.
The ‘BMW Energy Master’ is manufactured in Landshut and pre-series production is currently underway. Series production is scheduled to start in August, with a further expansion stage in 2026. When production starts, around 200 people will be employed in the production area of the Energy Master in Landshut, and up to 700 people after the ramp-up.
“For the BMW Group, electric mobility is the future and a key area of growth. We are leading the way with this drivetrain technology. At the same time, we are deliberately taking a technology-open approach, recognizing that mobility needs vary between different regions of the world,” explained Joachim Post, BMW Board Member for Purchasing and Supplier Network. “We want to offer our customers the best drive concept for every need. It is possible to do both: offer the best drive technology for every need and be at the forefront of electric mobility.”
0 Comments