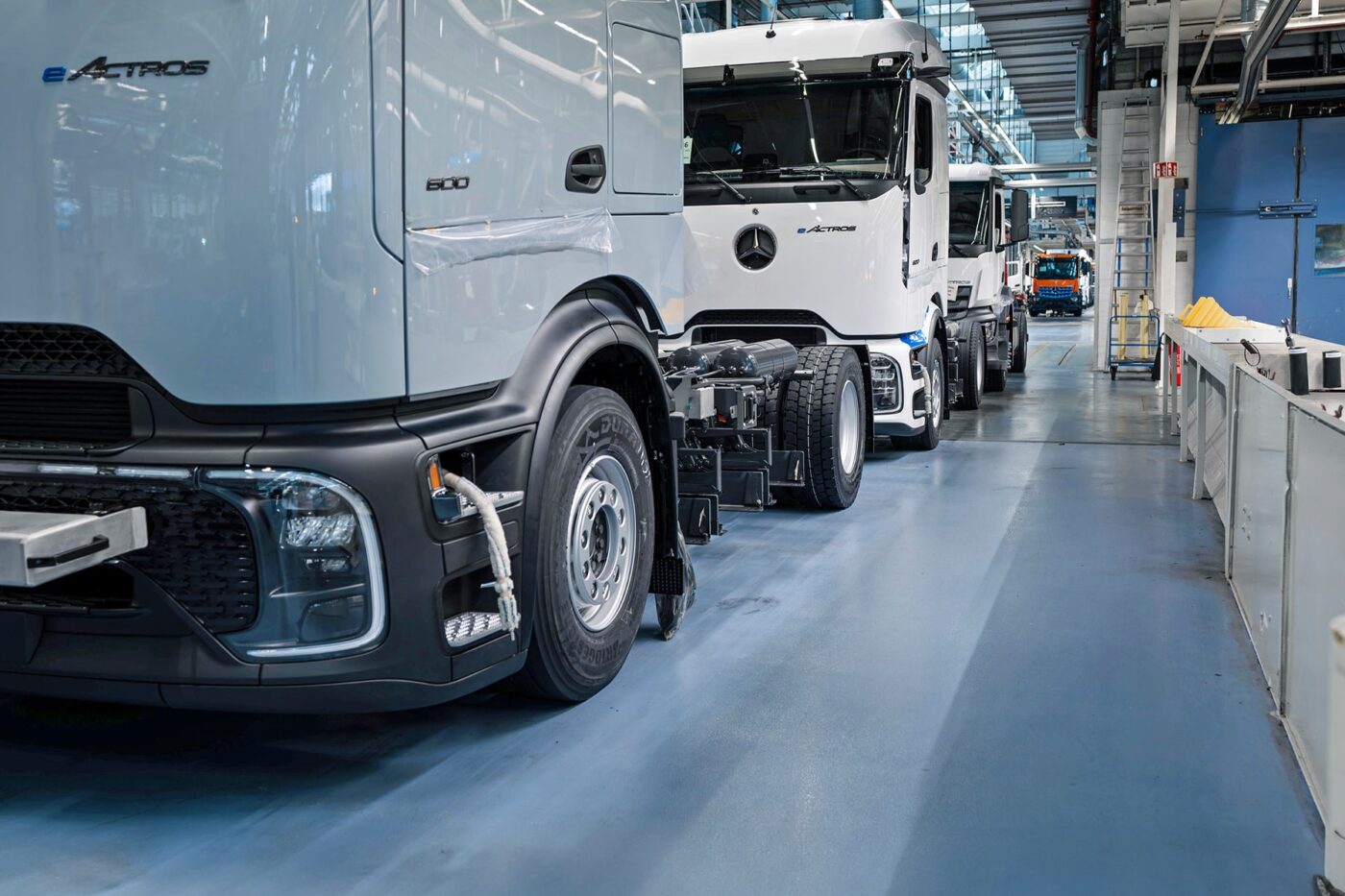
Daimler Truck sends the eActros 600 into series production
The first eActros 600 produced by Daimler Truck at the Wörth plant with series status is painted white, bears the number plate GER ZE 404 and goes by the name of Job #1. The electric 40-tonne truck is the main protagonist at the opening ceremony held on Friday in Wörth. Series production of the eActros 300/400 for distribution transport started at the same location in 2021. The similar eEconic for municipal use followed in 2022. However, the German truckmaker only intervened in its line production on a larger scale for the production of the new electrically powered long-distance truck. That is because the eActros 600 is built flexibly on an assembly line with combustion engines, making it the first electric truck from Wörth to be completely assembled in one production hall. The two smaller electric series with up to 27 tonnes have been and will continue to be moved to another hall for the installation of the electric components. The effort put into the 600 thus testifies to the market potential that the Group’s management sees in its new electric flagship.
Briefly about the eActros 600 itself: The vehicle celebrated its world premiere in October 2023 and owes its name to its battery capacity of over 600 kilowatt hours. The XXL electric vehicle also houses a new electric drive axle developed in-house with 400 kW continuous and up to 600 kW peak power and a so-called front box, which bundles control units, high-voltage components and the electric air compressor in the former engine compartment. The range of the electric beacon of hope is 500 kilometres. The eActros 600 can be charged via CCS with up to 400 kW, and the electric truck will also be capable of megawatt charging as soon as the MCS standard has been finalised.
Initial deliveries scheduled for this year
In addition to Wörth, the Daimler Truck plants in Mannheim, Kassel, and Gaggenau also play an important role in the production of the eActros 600. As reported, they contribute components such as the electric axle, transmission parts and the aforementioned front box. The first series-produced vehicles will initially be sent to branches and dealers as demonstration vehicles. However, the first customer units will also be produced and registered in 2024.
In Wörth, the heavy electric models see the light of day on line 2. Line 1 is reserved for lighter models, while line 3 is reserved for heavy combustion engines. In the centre, combustion and electric models share Line 2. One of the production managers tells us their construction is similar in many respects during the tour. A frame serves as the backbone for the axles; while the combustion engines then get their gearbox, tanks and exhaust devices, the electric models receive their e-axle, inverter and battery mounts early on. Orange cables stretching across the chassis are evidence of high voltage. All employees working on Line 2 have been extensively trained to work with these components.
The electric truck gets its batteries at the end of the line
As we make our way through the production hall, we keep coming across small self-propelled transport boxes that take parts from A to B. They make their sensor-driven way past the group of journalists. But our eyes return to Line 2: two or three stations along the route are particularly striking. At the ‘engagement,’ the combustion engine unit or front box floats in, depending on the engine, while at the ‘wedding’ the cab comes from above. For the fitters, it should “make no difference whether they are installing an electric axle or a diesel engine.” Initially, however, it is challenging to synchronise the installation of the electric components with the tight schedule of the slowly but steadily moving line.
Interestingly, the eActros 600 only receives the three 207 kW battery packs at the end of the line. They are inserted at the side. All units then roll onto the test bench for final acceptance, regardless of the drive.
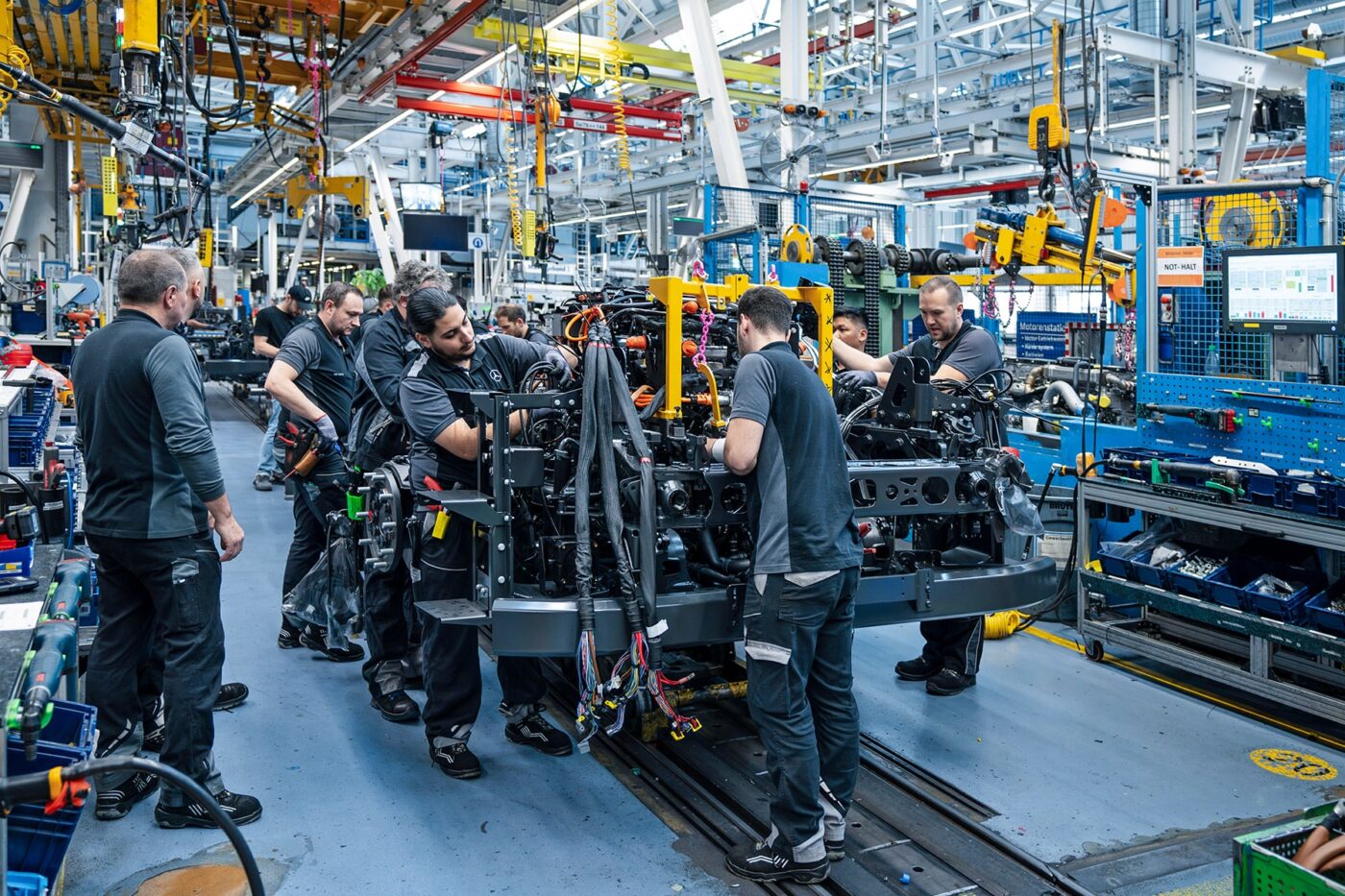
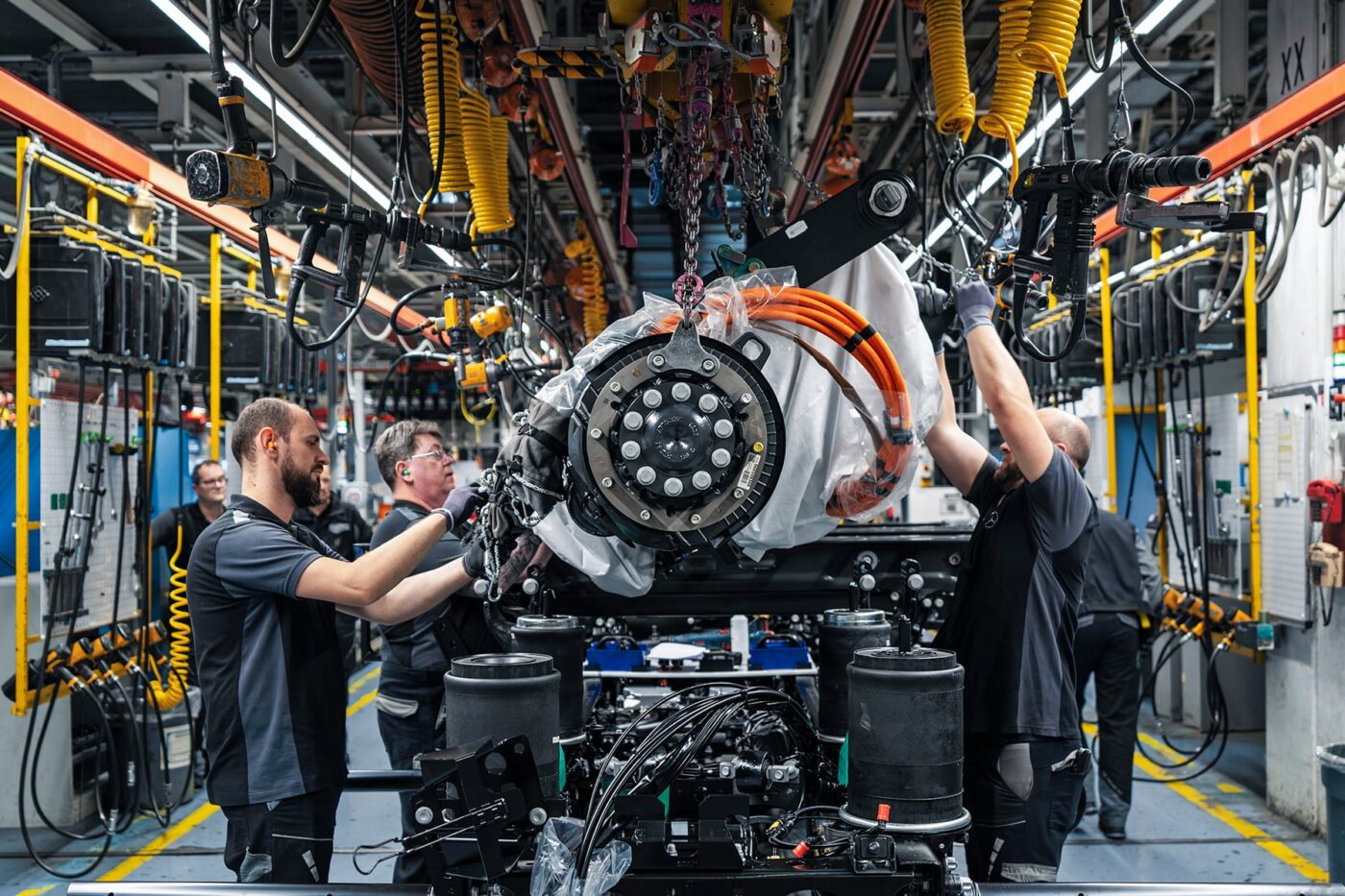
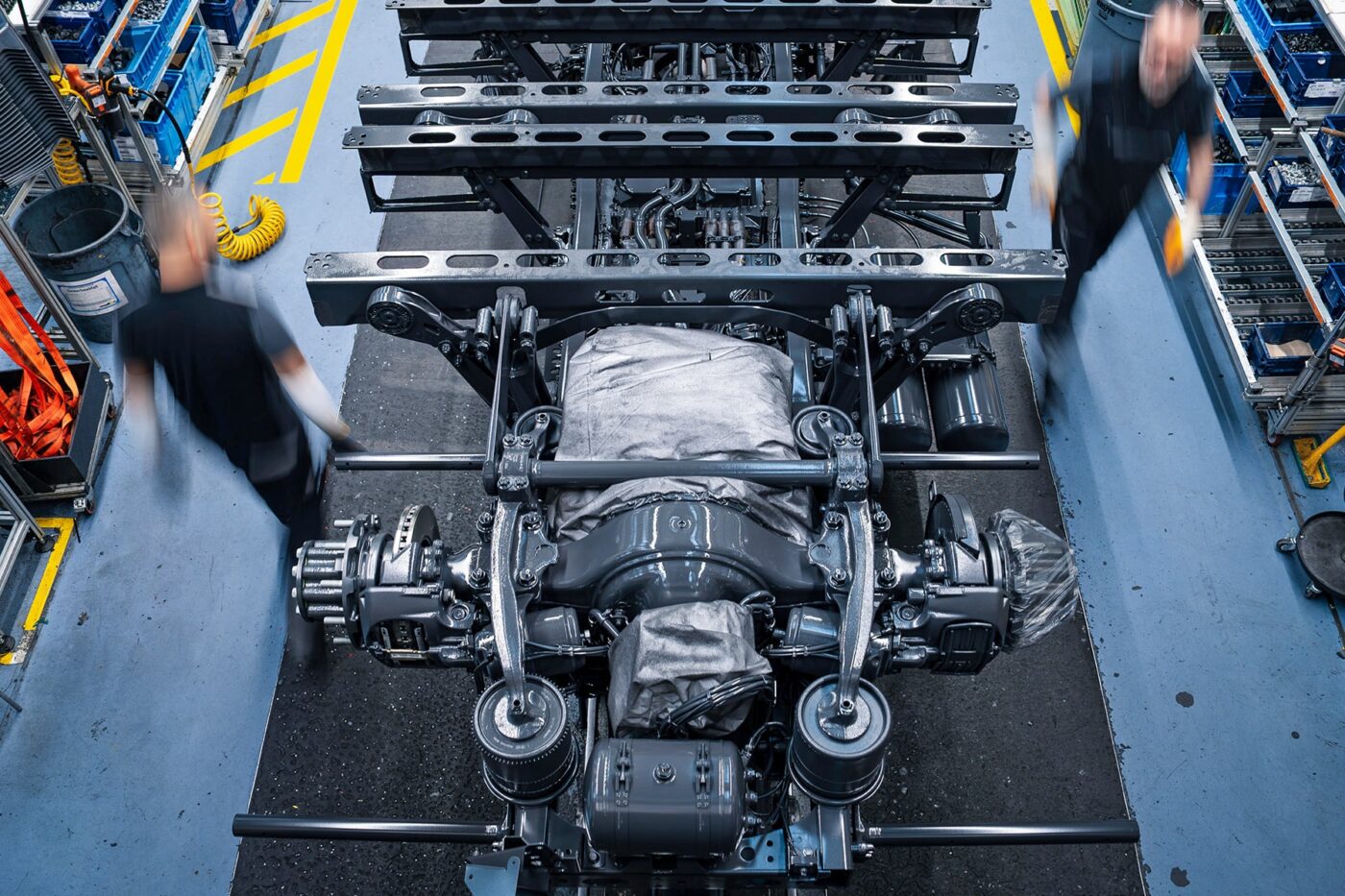
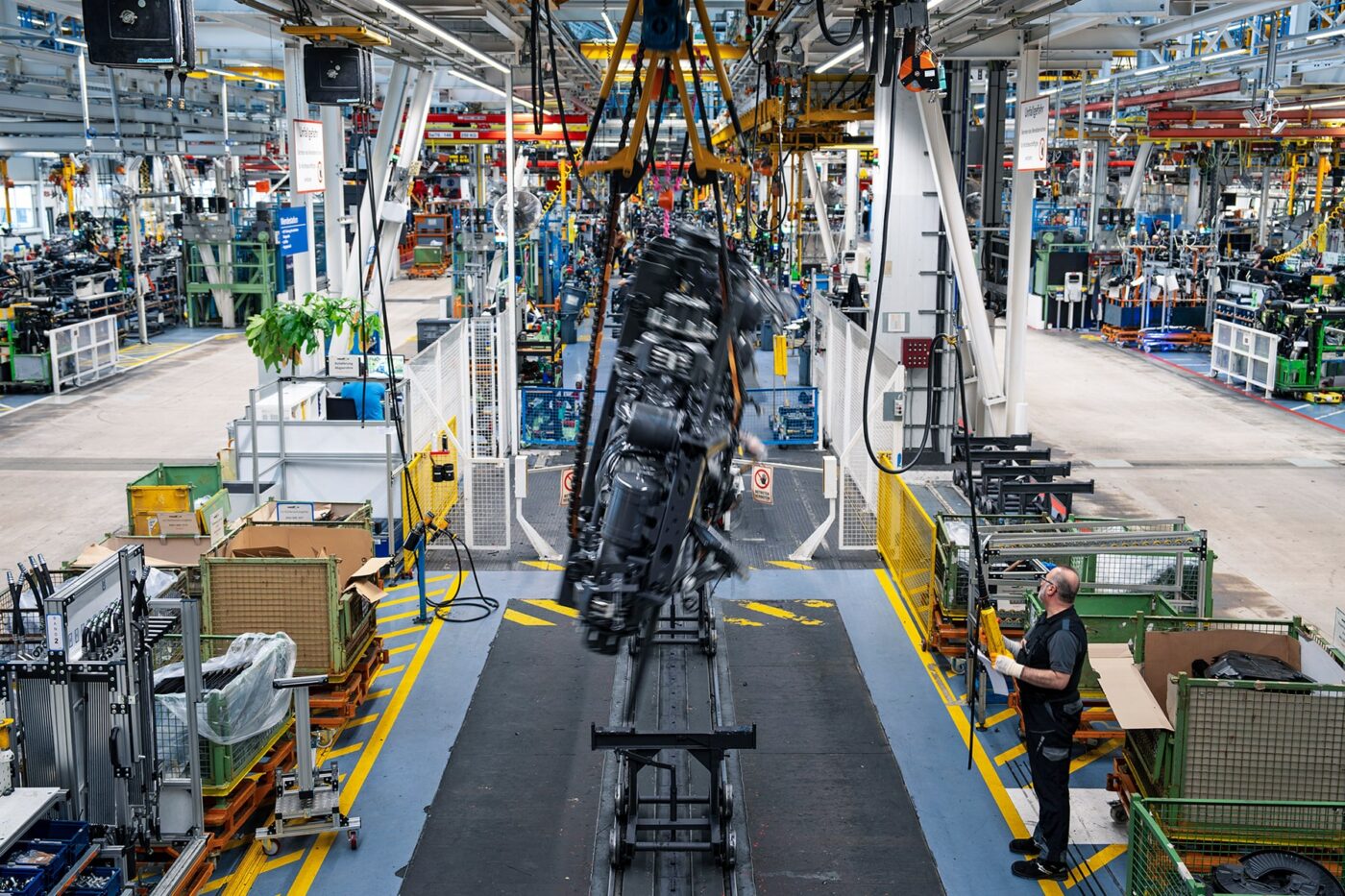
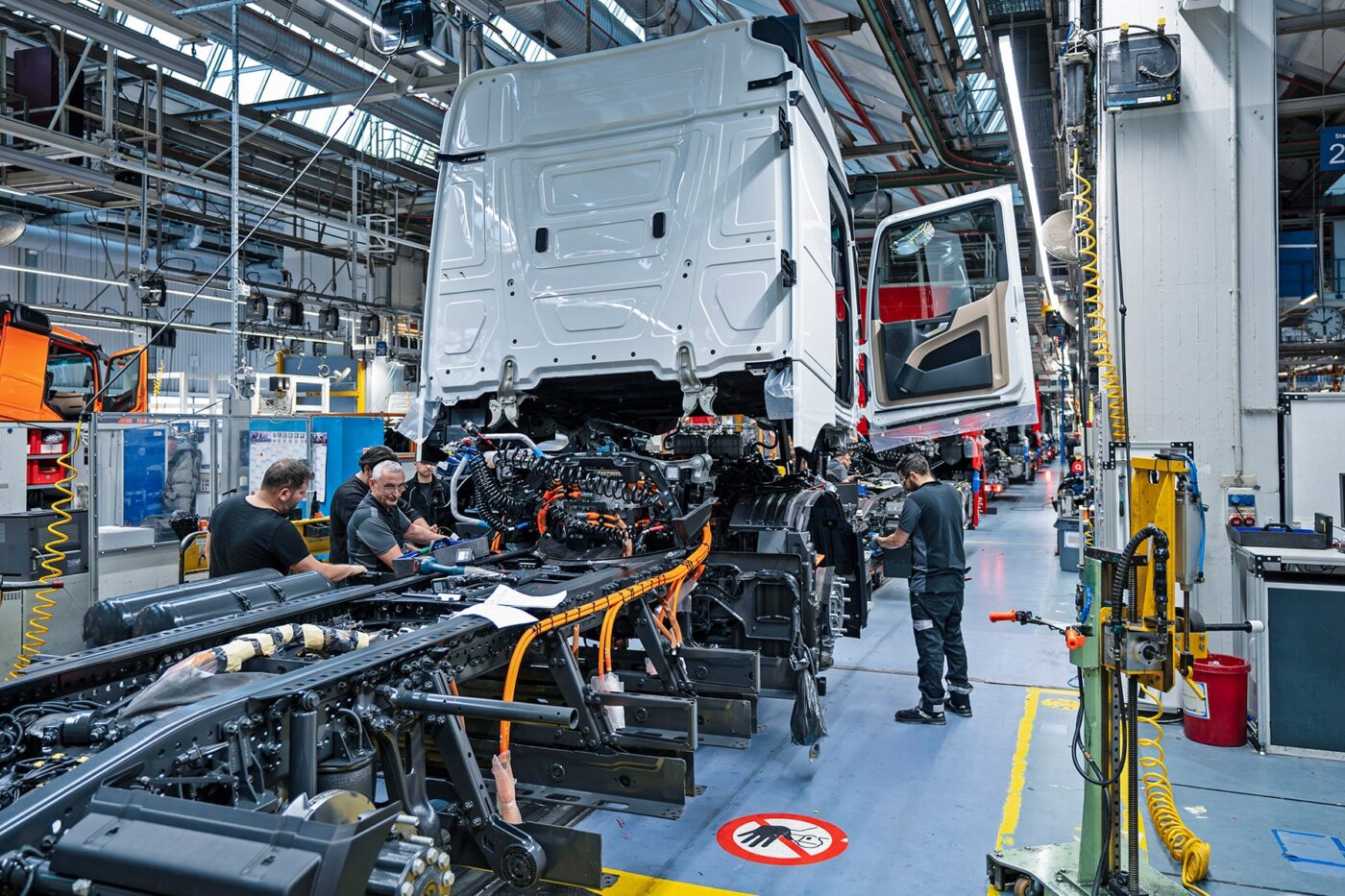
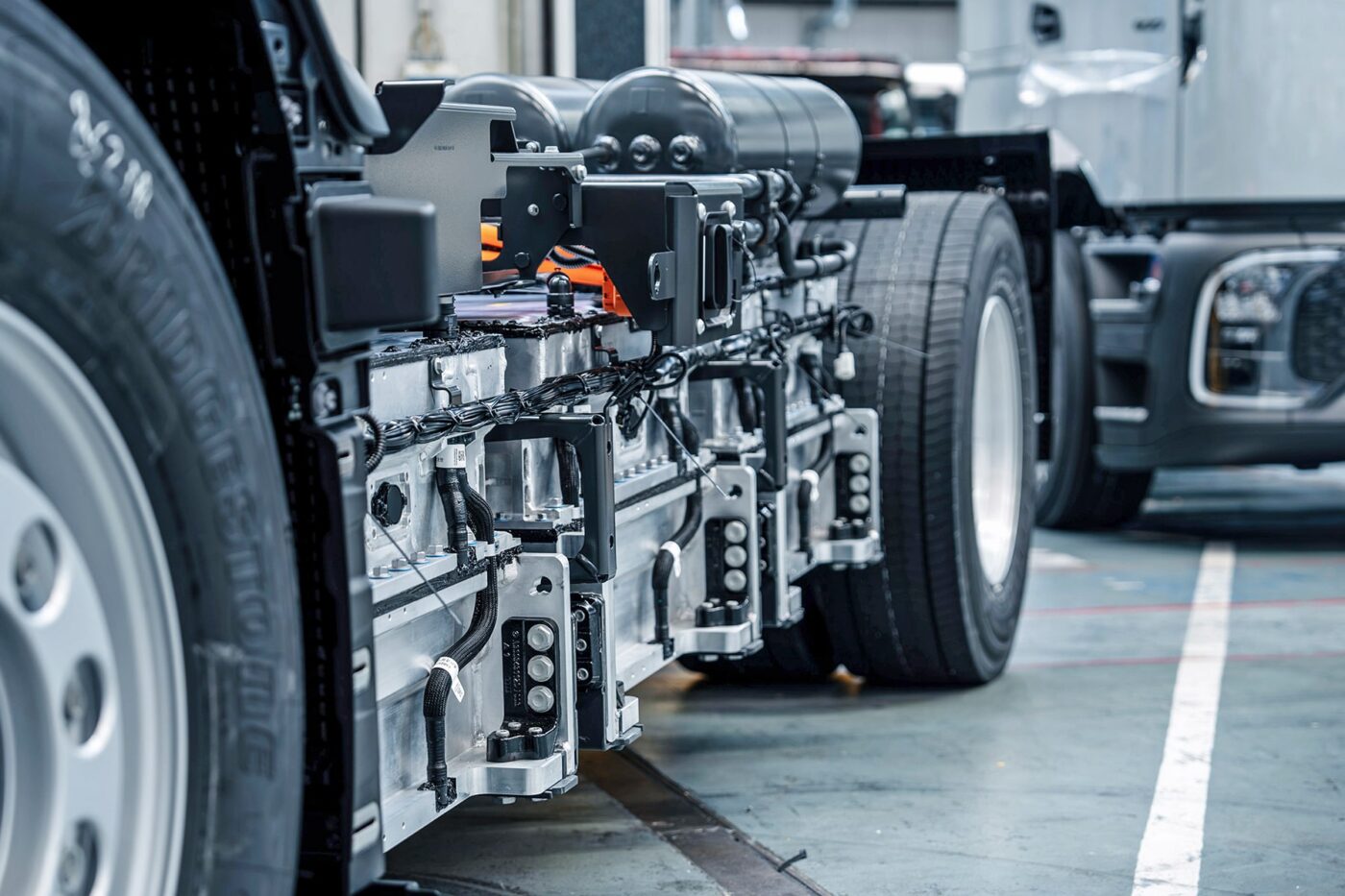
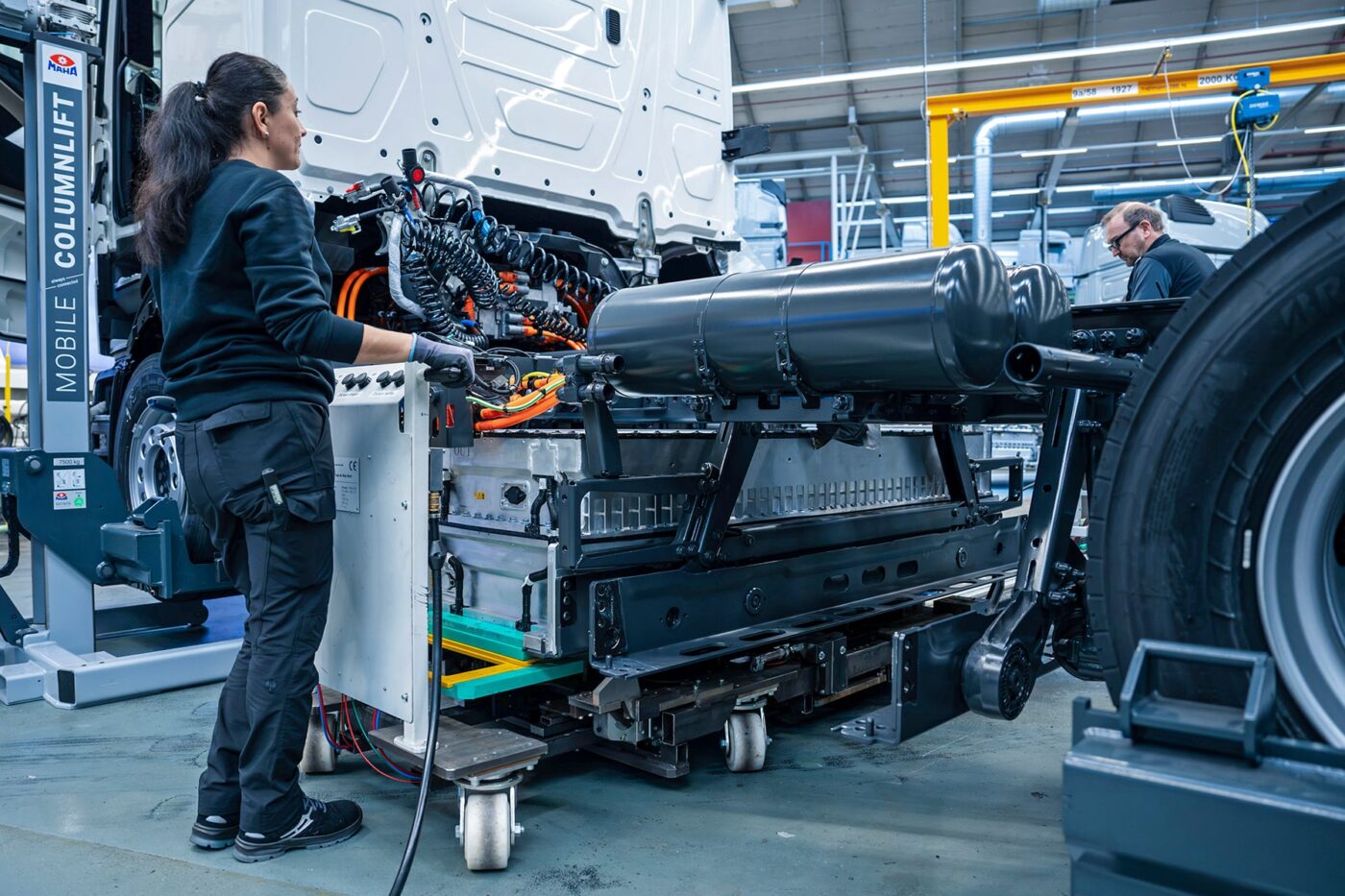
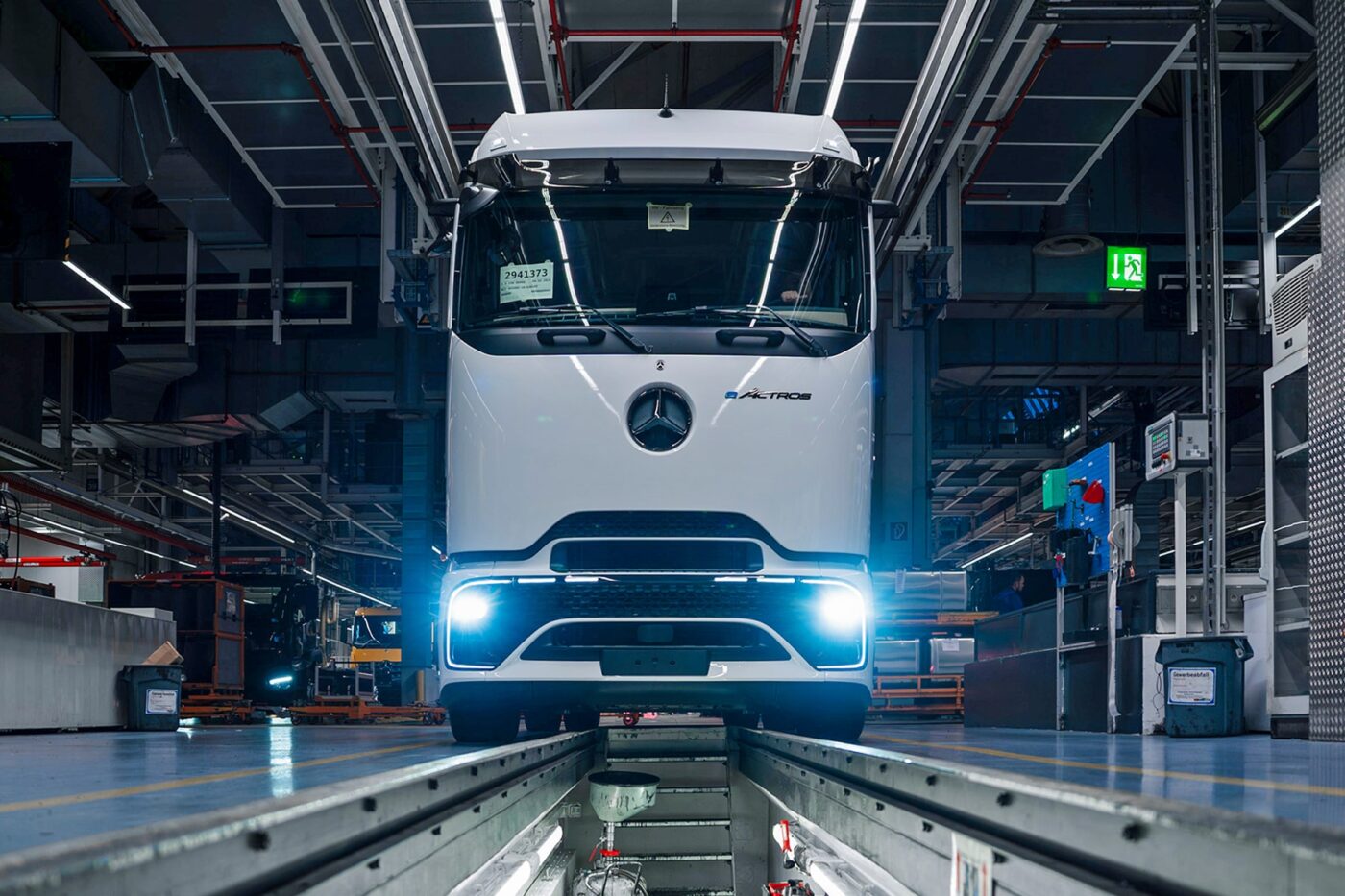
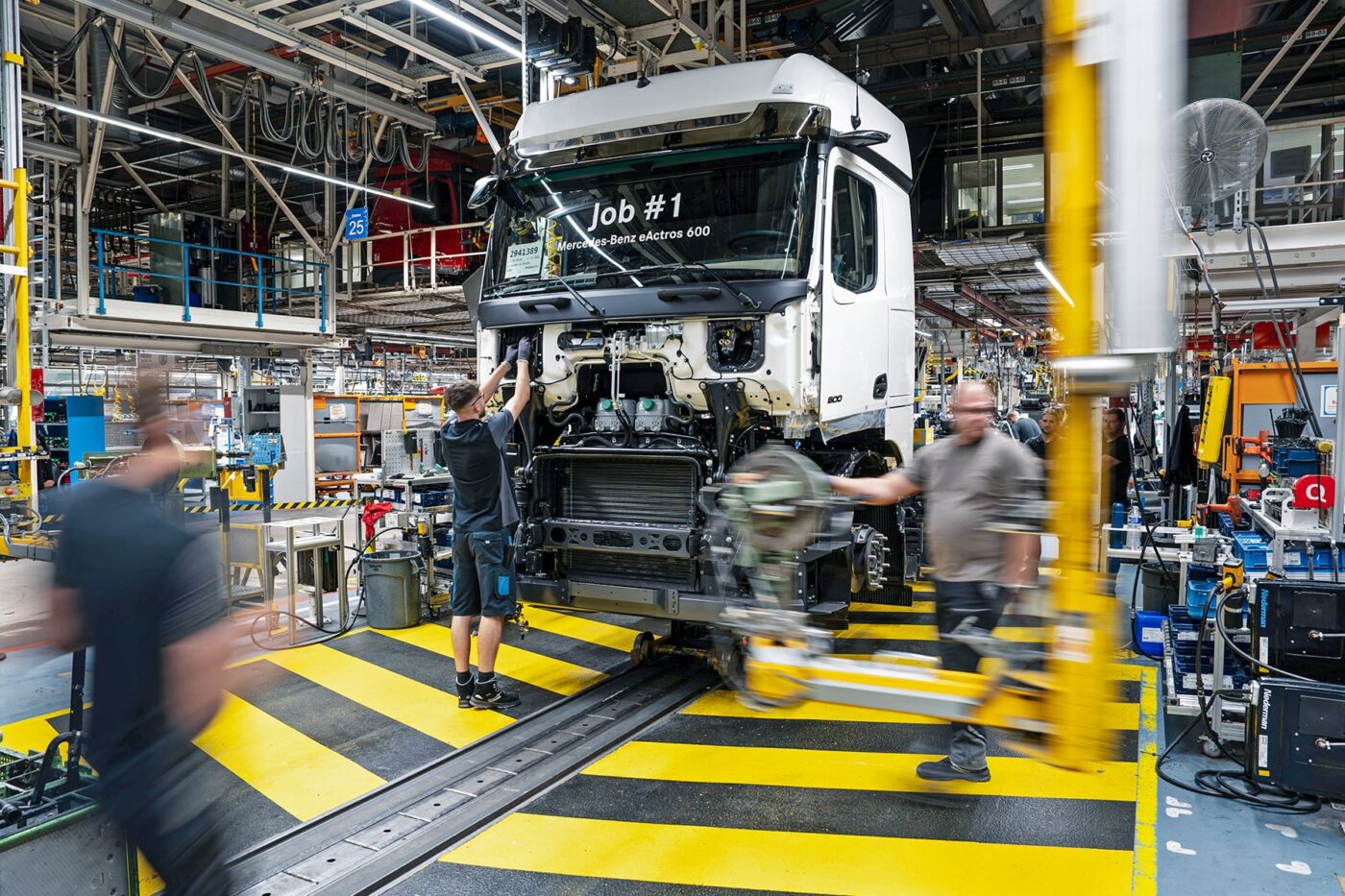
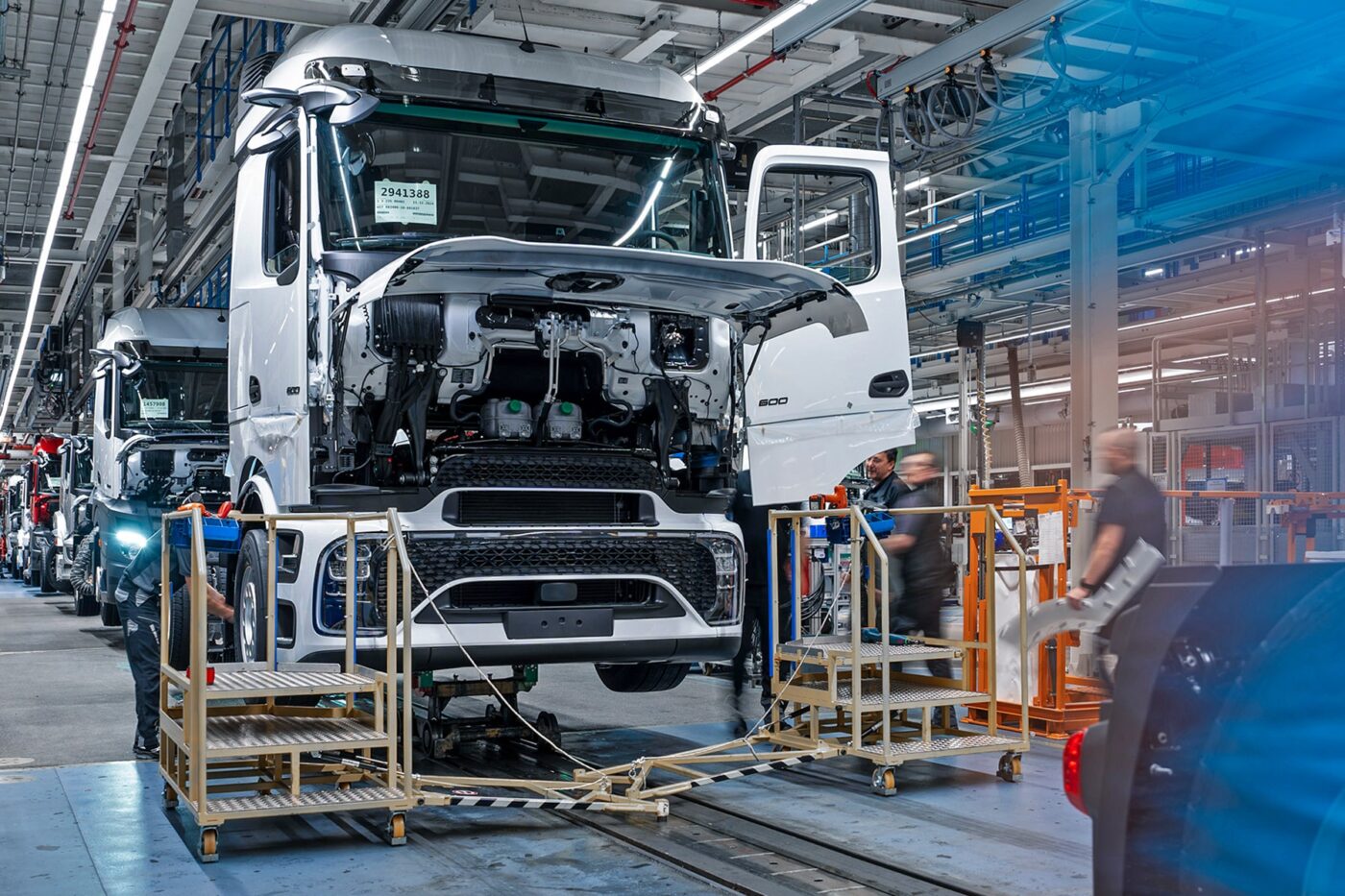
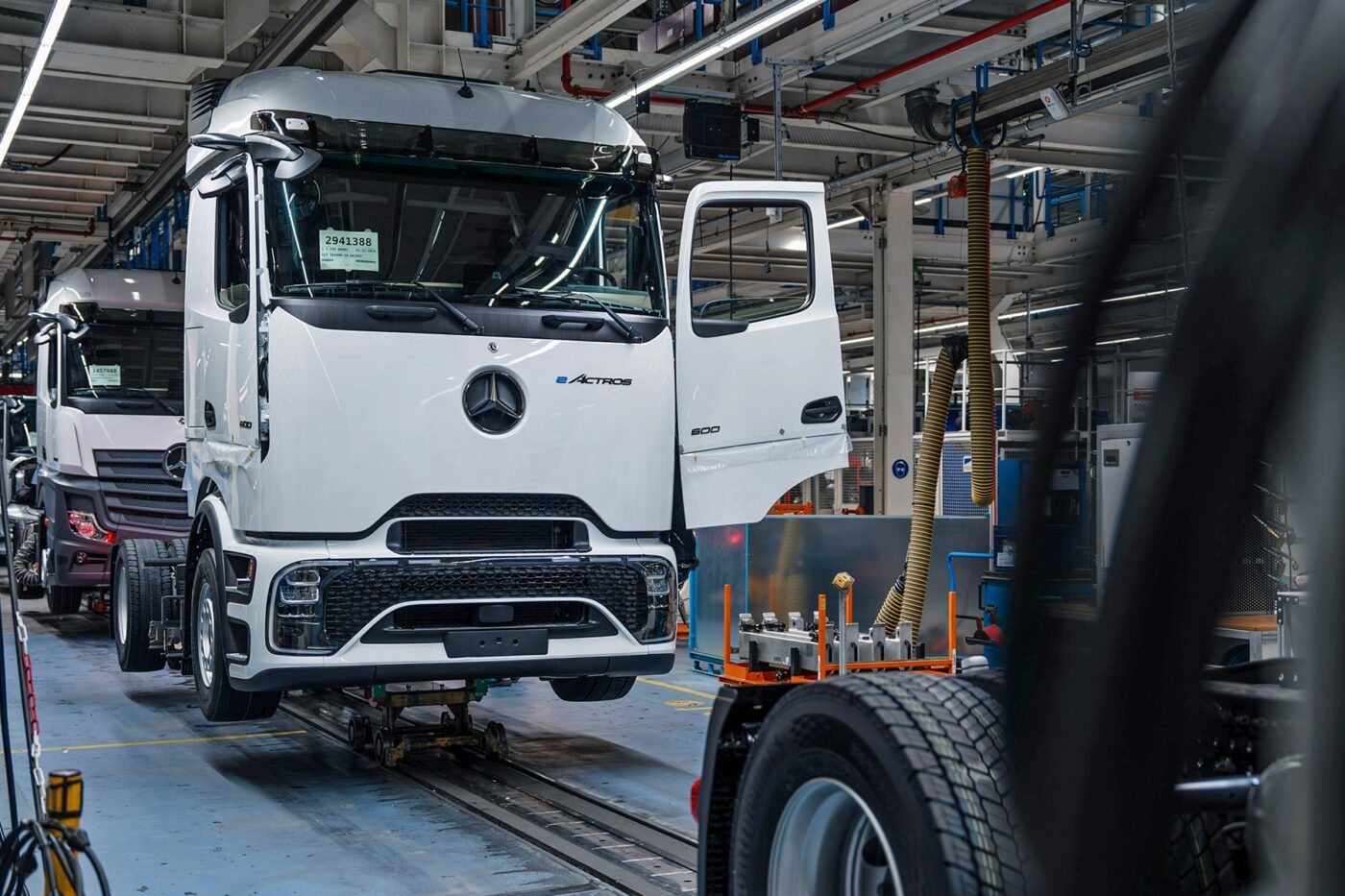
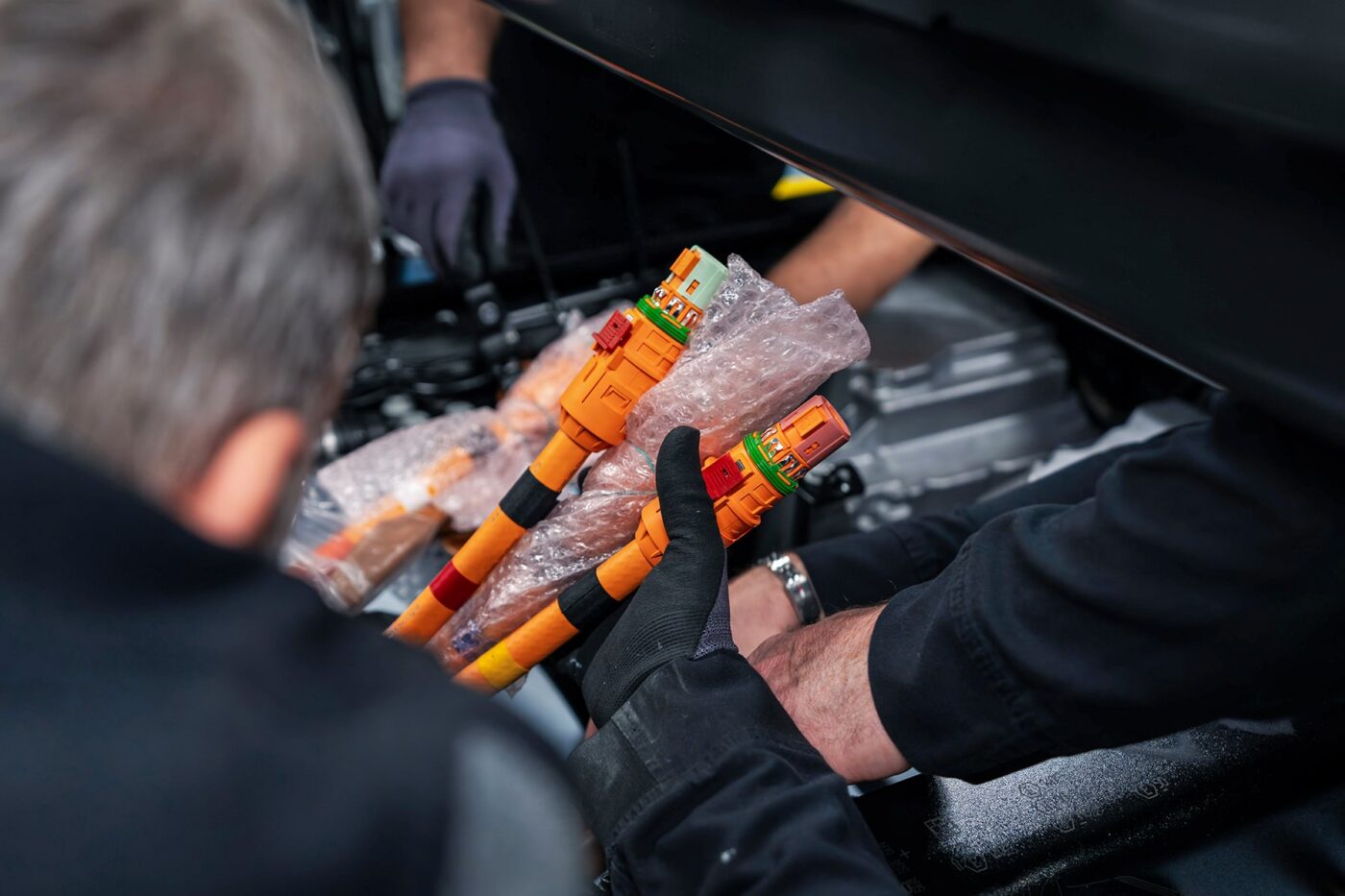
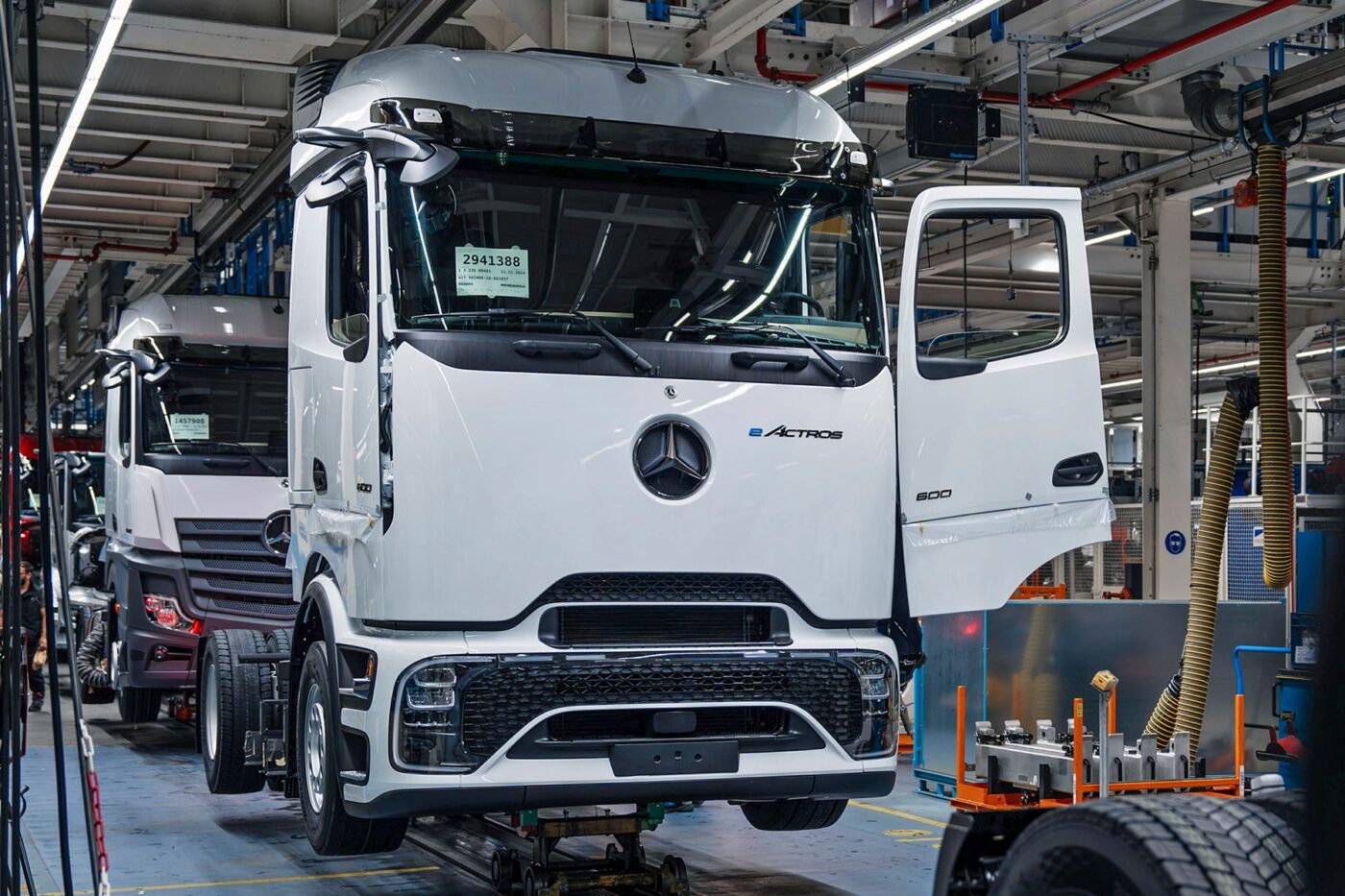
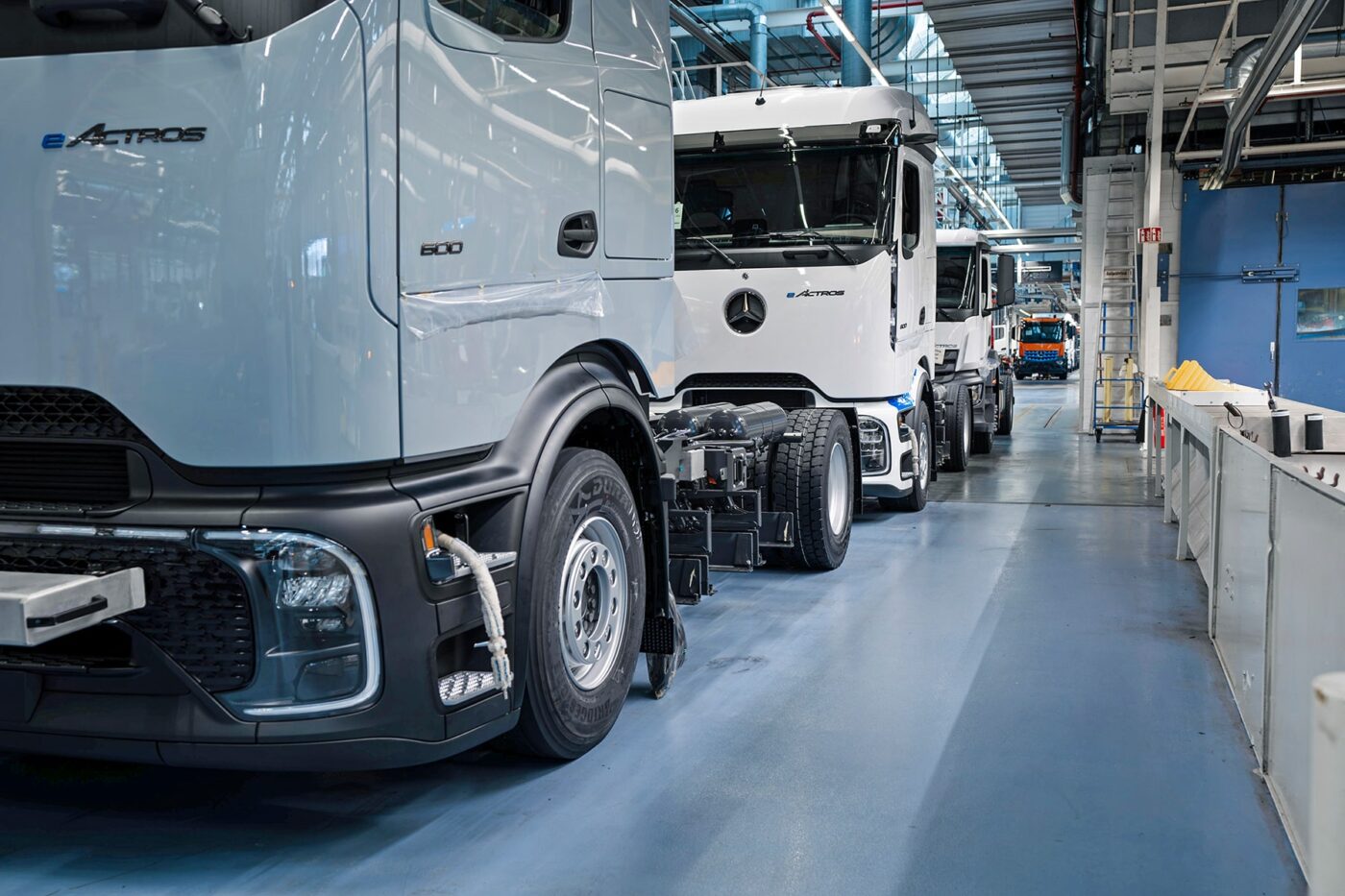
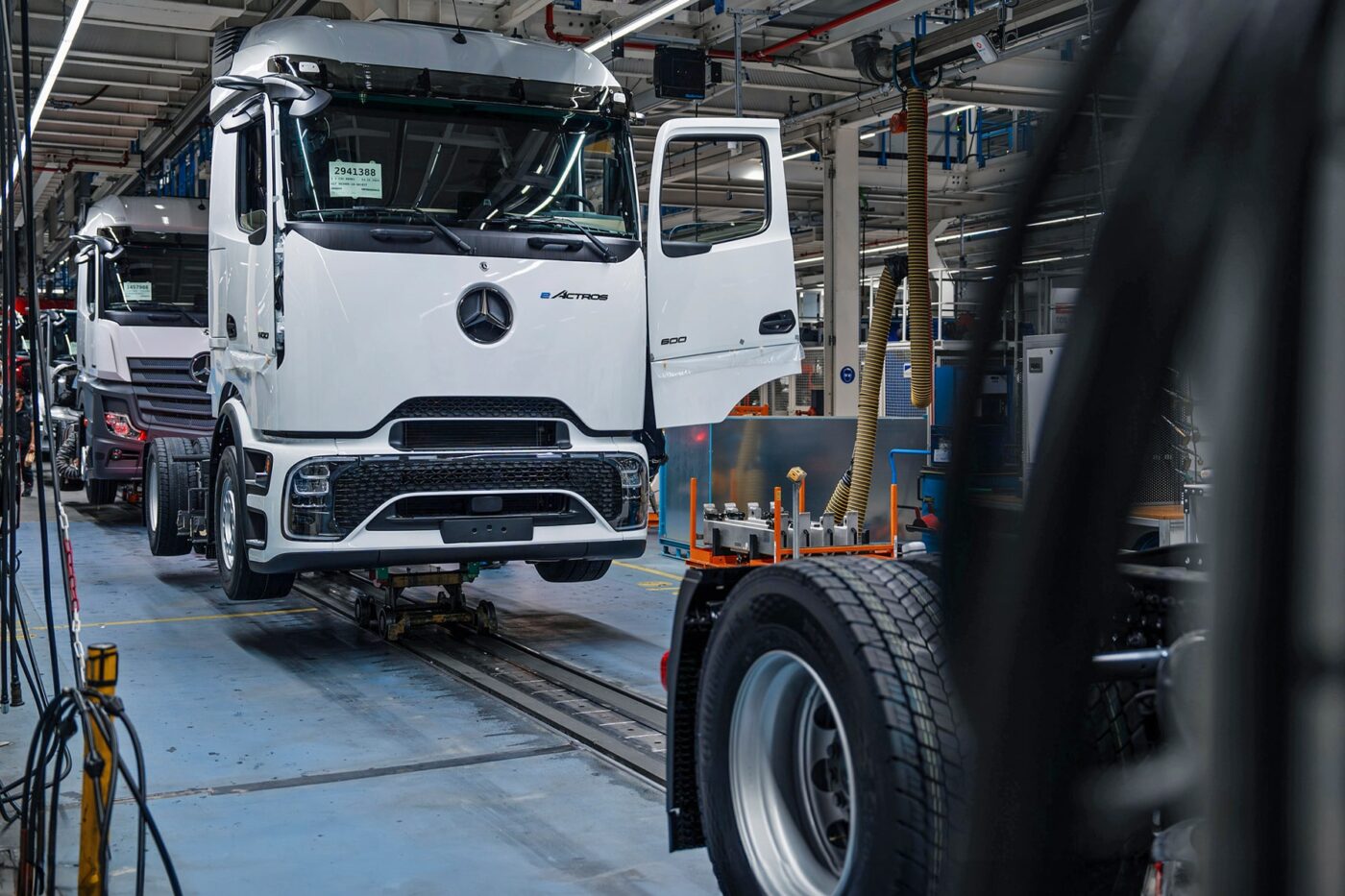
But let’s stick with the battery. For the 600, it comes from CATL and is ready for installation. The new electric intercity bus from Daimler Buses will also use the same battery from the end of 2025, which is in line with the Group’s common parts strategy. Daimler Truck can call up the finished LFP battery systems from a CATL warehouse in Germany. The approach differs greatly from previous procurement. That is because the batteries for the eActros 300/400 and eEconic are assembled at the company’s own component plant in Mannheim – using CATL cells. In principle, Daimler Truck has switched to lithium iron phosphate cell technology for its electric heavyweight for the first time. According to Karin Rådström, CEO of Daimler Truck, that is because of the long service life and more usable energy. The vehicle is expected to cover 1.2 million kilometres in ten years of operation.
Integration of electric trucks is “a great learning experiment”
According to site manager Andreas Bachhofer, the ramp-up of the electric-powered 40-tonne truck will take place gradually. The final adjustments to the line will be made over Christmas so that employees can keep up with the speed of the line even better with the XXL electric lorries between the combustion engines. Bachhofer sees flexibility as a major advantage, allowing production to be constantly adapted to demand. Many lessons learnt from the eActros 300/400 production have been incorporated. Bachhofer calls the entire electric truck integration project “a great learning experiment.” Those responsible do not want to make any predictions about how the drive mix on Line 2 might develop.
Michael Wolf, technical project manager for the eActros 600, is one of the ‘fathers’ of the new model and is releasing the electrically powered 40-tonne truck into its own production life on this day. In his eyes, the 500-kilometre range is not the end of the line. “The battery continues to develop. We can’t make much more progress in terms of weight, we’re almost at the limit there, but in terms of power density. I personally believe that 800 to 900 kilometres on one battery charge is conceivable in the future.” In the end, it’s all about the right balance – between range and payload (which is measured by the weight of the vehicle), among other things. With a range of 500 km (“calculated rather conservatively”), the 600 has a total permissible mass of 44 tonnes and a payload of around 22 tonnes. Apparently, this is a convincing mix: the manufacturer has recorded 2,000 firm orders so far and a four-digit number of declarations of intent to purchase.
Long-distance transport offers great CO2 leverage
Karin Rådström, recently promoted to head of Daimler Truck, describes the eActros 600 as a “benchmark for the industry.” The competition is still lagging a little behind, be it in the form of existing models that exist but that are, because of their shorter ranges, for distribution traffic. Some have announced long-haul models, but they are not ready for production, as is the case with Volvo Trucks. “The start of series production of our eActros 600 is further proof of our ambition to change the industry,” explains Rådström. The eActros 600 is aimed at the long-haul segment in Europe, which is responsible for two-thirds of CO2 emissions in heavy road haulage. “Our battery-electric long-haul truck will therefore make a real difference.”
In front of a number of invited guests, including representatives from politics and business, Rådström also made it clear that a good product and approximate cost parity between electric trucks and diesel trucks alone are not enough to convince customers. “Charging infrastructure threatens to become a bottleneck.” According to the CEO, around 35,000 fast-charging stations are required for long-distance truck transport in Europe by 2030 for manufacturers to fulfil the EU specifications. That would mean that 400 charging stations would have to be built every week – which is not happening. According to Rådström, she was in Brussels just that morning to draw attention to the fact that the new EU CO2 standards for commercial vehicles and the European Alternative Fuels Infrastructure Regulation, better known as AFIR, “don’t go together.” According to AFIR, only 17,000 fast-charging points would be needed by 2030. ‘The two should at least interlock logically,” says Rådström. Over time, the market would then have to take over. In other words, business models are needed that make the installation of chargers attractive to the private sector.
Meanwhile, Michael Brecht, Chairman of the Daimler Truck General Works Council, emphasises that the eActros 600 is a very important product because thousands of jobs will depend on it in the future. The Wörth plant alone has around 10,000 employees – making it the second largest employer in the German state of Rhineland-Palatinate. And the Wörth-based company wants to lead the way with the continuous use of the eActros 600. The goal is to fully electrify delivery transport by the end of 2026. In this context, Daimler Truck opened a charging park near the factory entrance at Gate 2 just a few days ago. The initiative is part of the Group’s vision to make production CO2-neutral.
1 Comment