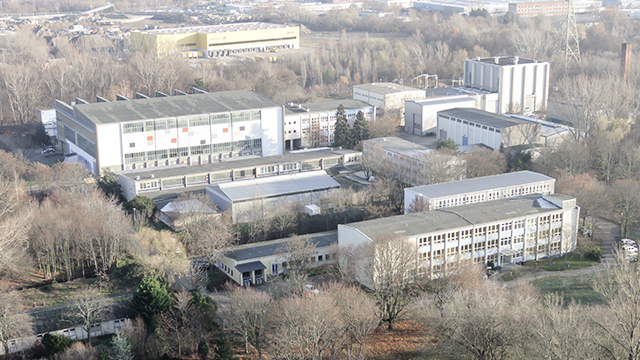
Interview with Stefan Schwanck: Insights into Pyroswitch DC Testing for E-Mobility
Stefan, can you give us an overview of the significance of Pyroswitch DC testing in the e-mobility sector?
As the e-mobility sector grows, the demand for reliable, high-current, high-voltage switching components in EVs increases. Pyroswitches, which disconnect the battery quickly in case of a crash, are vital for preventing fires and ensuring passenger safety. Realistic testing of these components is crucial for the safety and reliability of electric vehicles.
What led to the development of the new test bench for DC components at KEMA Labs?
The idea for the new test bench arose from the need to support the R&D activities of manufacturers who are developing innovative e-mobility components. Traditional test circuits were limited in their ability to simulate the specific conditions found in automotive applications. For instance, the low inductance of circuits in vehicles, often less than 10 μH, posed a challenge. Our usual test circuits have inductances far over 20 μH, which is far above the conditions in an EVs energy distribution system. This gap in testing capabilities prompted us to design a new test bench that could meet these unique requirements.
Can you detail some of the technical challenges faced during the project?
The main challenge was predicting future traction voltage levels and short circuit currents (SCC) in electric vehicles and developing a corresponding test circuit.
The project took about four years from the initial idea to realization and must operate for up to 20 years, making it a complex task.
Currently, the voltage for electric traction in EVs ranges from 400 to 800 volts. To prepare for future developments, we adhered to UNECE R100, which defines voltages up to 1500Vdc.
Additionally, finding a manufacturer to build a test bench capable of 1,500 volts, 35kA SCC with less than 10 μH inductance, and an adjustable resistor matrix was a significant challenge.
What makes the new test bench unique in the market?
These capabilities are essential for testing components like fuses, switches, and connectors under real-world conditions. The test object can be placed in an explosion-proof climatic chamber, simulating temperatures from –50 to 150°C, allowing destructive R&D tests without damaging the chamber.
Another innovative feature is the ability to switch the full current “on” and “off” multiple times without discharging the capacitor bank. We chose a capacitor bank with 2F, consisting of 14 cabinets of 1,500V foil capacitors, to ensure a long current flow duration.
This project benefited from the combined expertise of experienced testers like Mr. Borchert and young experts like Mr. Petersen, supported by our engineers. This system maximizes test throughput, offering clients a cost advantage over other laboratories.
What benefits does this new test bench provide?
It allows rigorous, real-world condition testing for e-mobility components, ensuring safety and performance. This early validation leads to more reliable EV components, supporting the adoption of electric vehicles. Additionally, it can be used in other sectors like aerospace, where high electrical safety and performance are essential.
Conclusion
The development of the new test bench at KEMA Labs represents a significant advancement in the field of e-mobility testing. Under the leadership of Stefan Schwanck and support of his team of testing experts the lab continues to push the boundaries of what’s possible, providing manufacturers with the tools they need to create safer and more efficient electric vehicles. As the e-mobility sector evolves, KEMA Labs remains at the forefront, driving innovation and excellence in electrical testing.
This is a sponsored article and the client is responsible for the content. If you would like to inquire about similar opportunities, please get in touch via advertise@electrive.com.