Mercedes-Benz opens battery recycling factory in Germany
A brief explanation of the terminology: Often, ‘recycling factories’ are simply facilities in which used or defective batteries are discharged, dismantled and crushed. Although materials such as aluminium and copper can be separated in the process, at the end of the process there is only the so-called black mass as a mixture of the valuable active materials. These are then broken down into the actual raw materials in another plant, often at a partner company, which can then be used again for battery production.
Not so in the case of Mercedes-Benz. The Stuttgart-based car manufacturer has built an integrated, mechanical-hydrometallurgical plant in Kuppenheim. This means that the hydrometallurgical process is also used to process the black mass. According to the Mercedes press release, Kuppenheim is ‘the first battery recycling plant in Europe’ to utilise such a process. This makes the company “the first car manufacturer worldwide to close the battery recycling loop with its own in-house facility.”
However, this is happening on a manageable scale for the time being. The battery recycling plant in Kuppenheim has an annual capacity of 2,500 tonnes and, according to Mercedes, enables the reuse of recyclable materials for the production of more than 50,000 battery modules for all-electric models. In the long term, Mercedes-Benz plans to scale up production volumes and further expand recycling capacities – at present, there are simply still too few recyclable used batteries to justify a larger and more expensive plant.
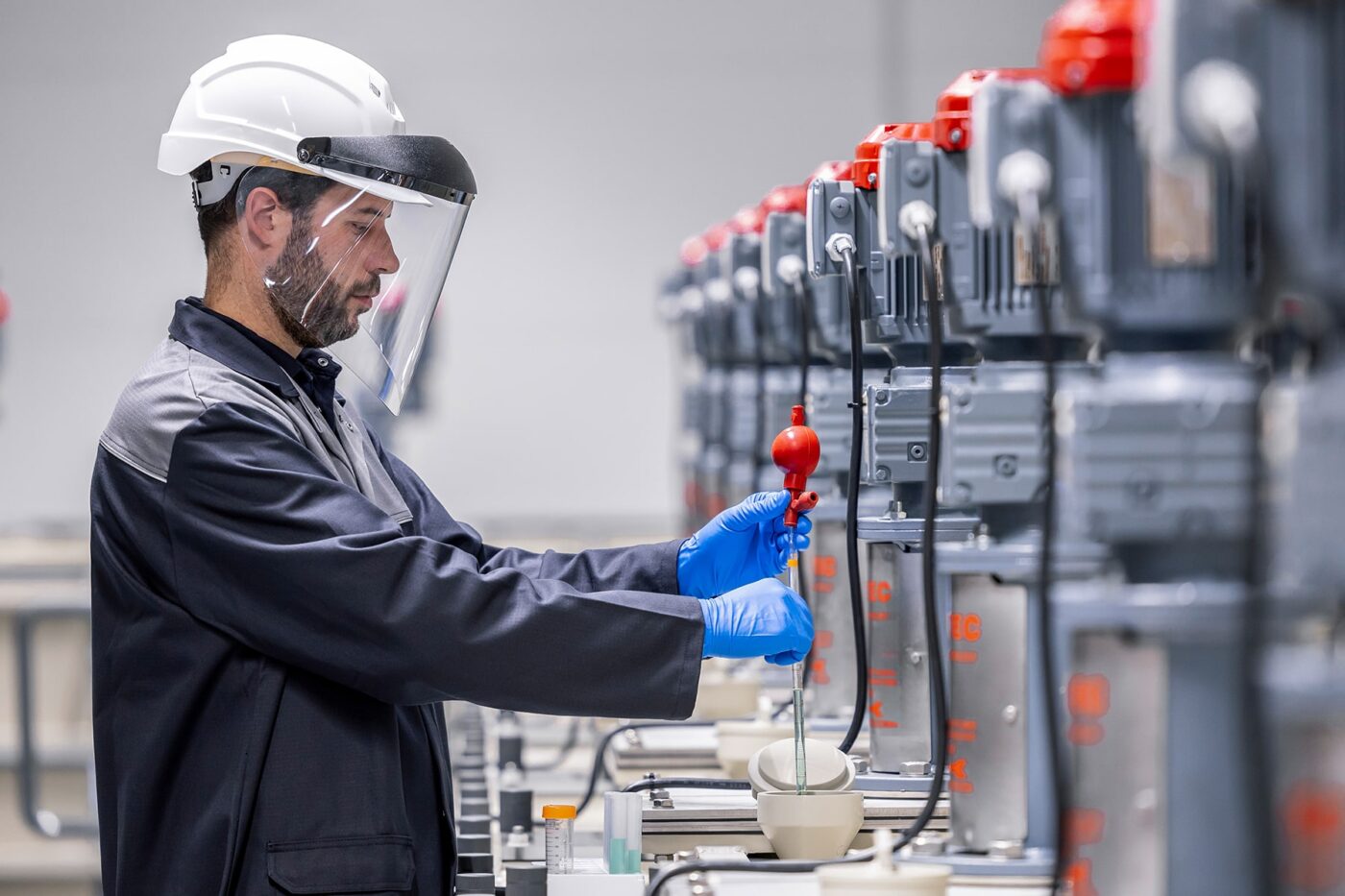
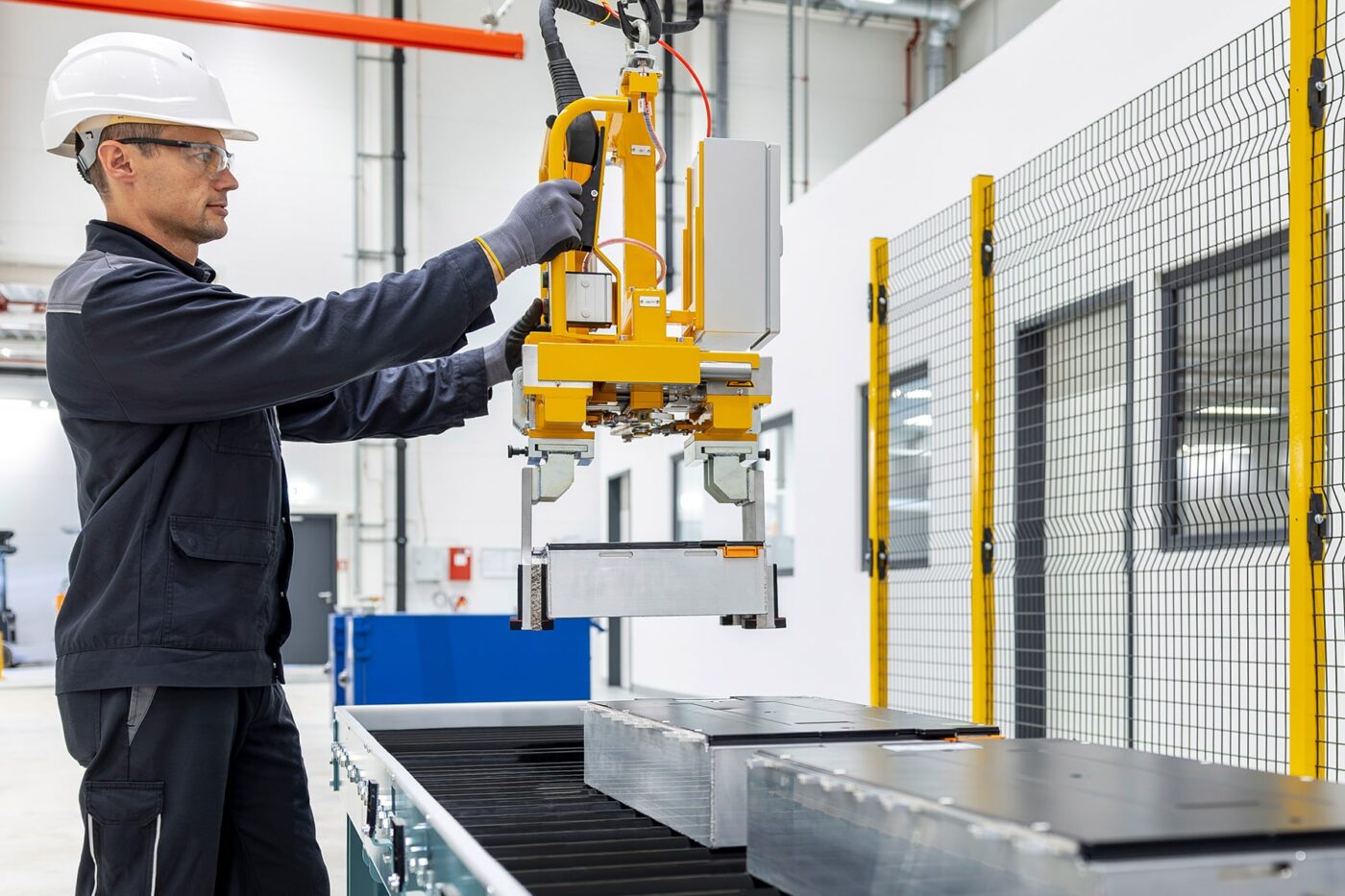
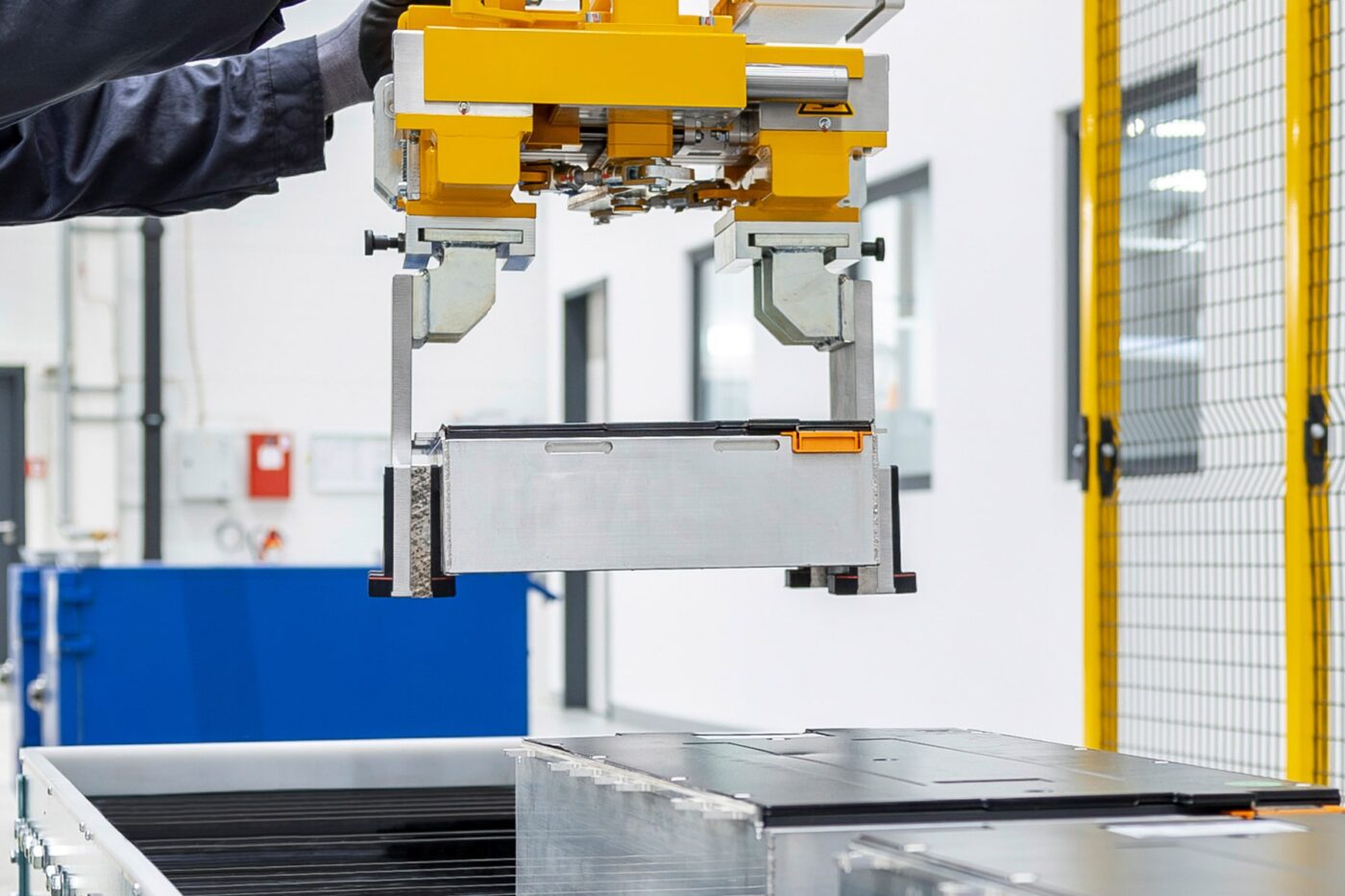
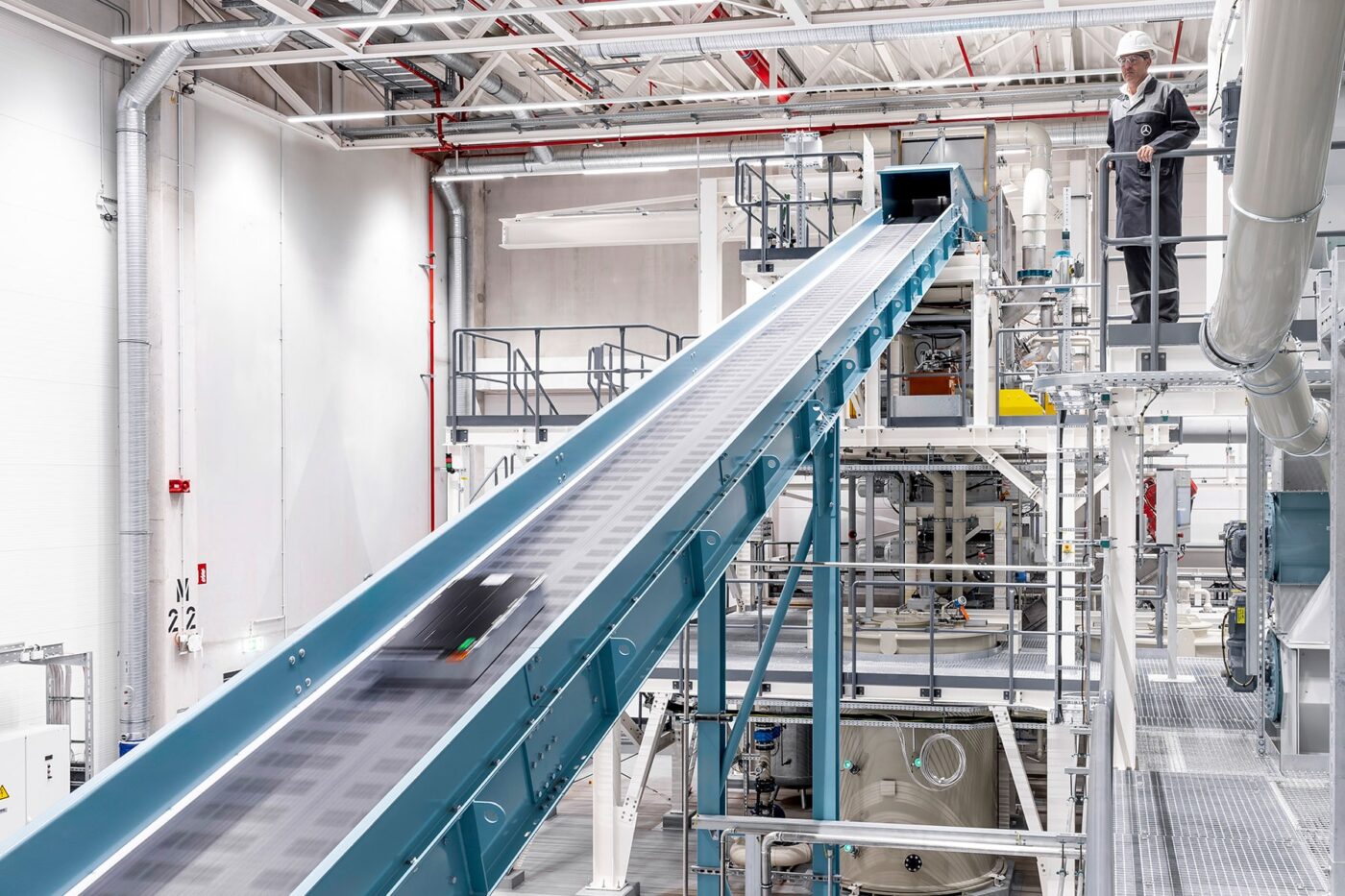
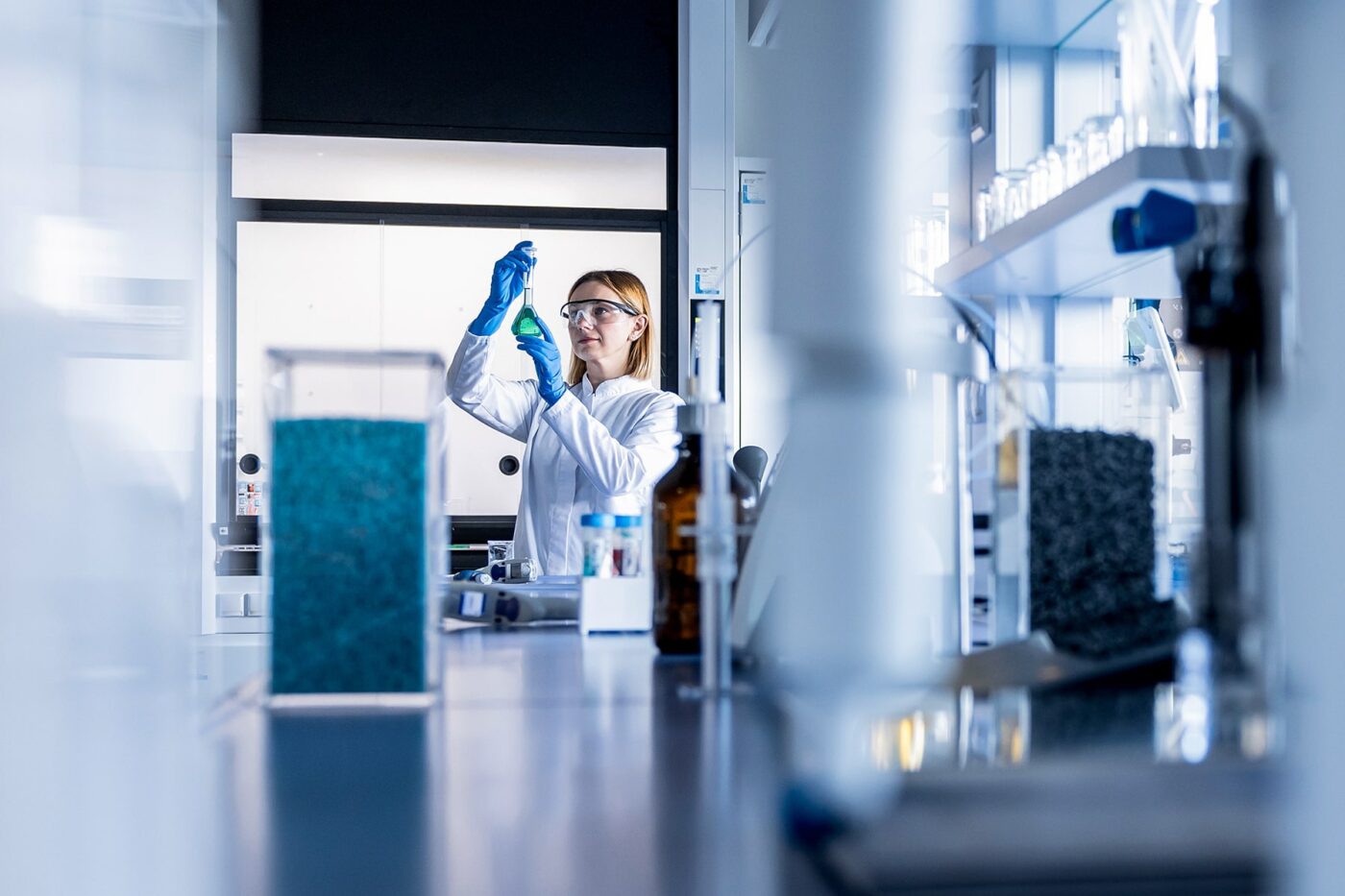
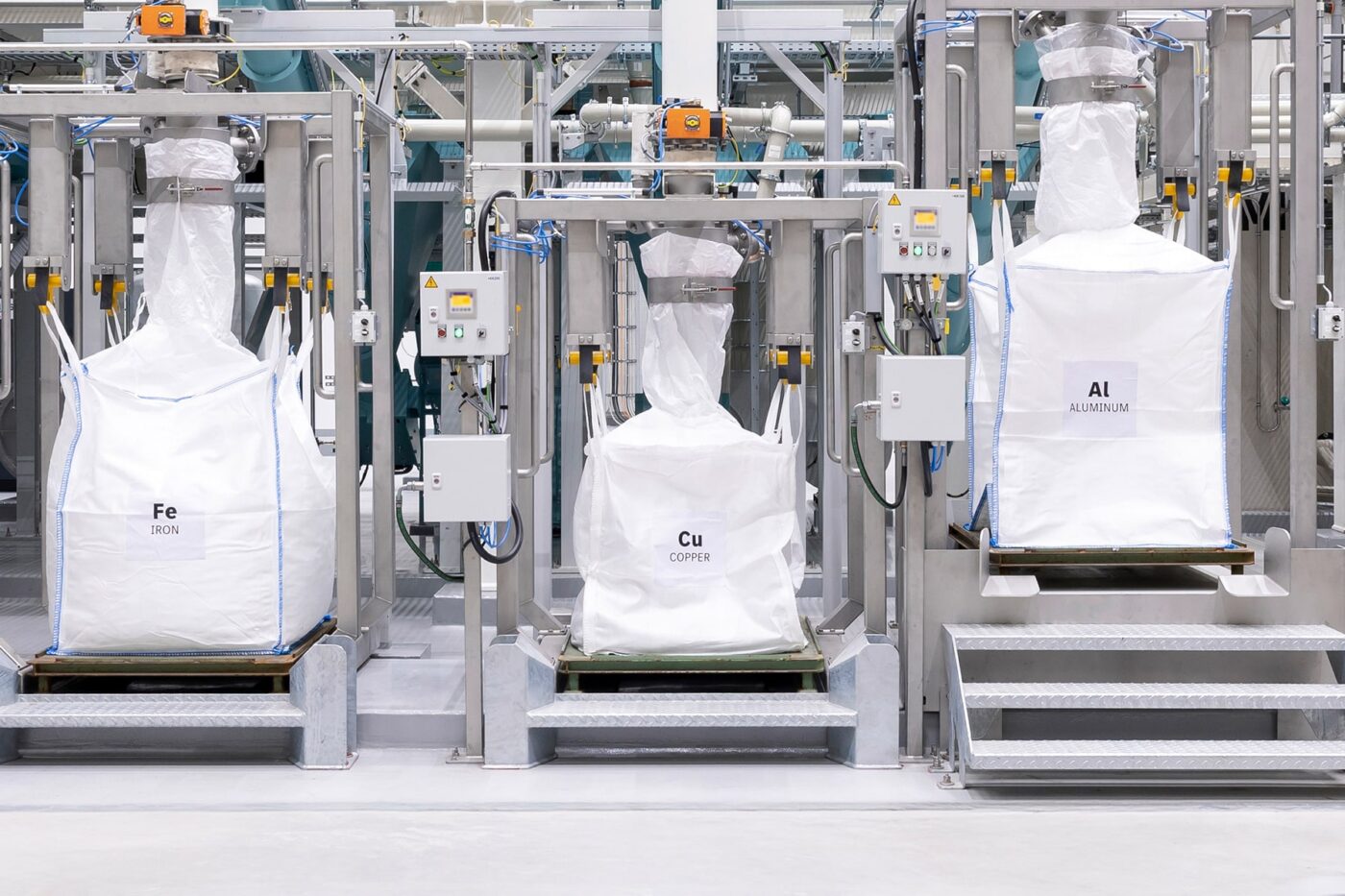
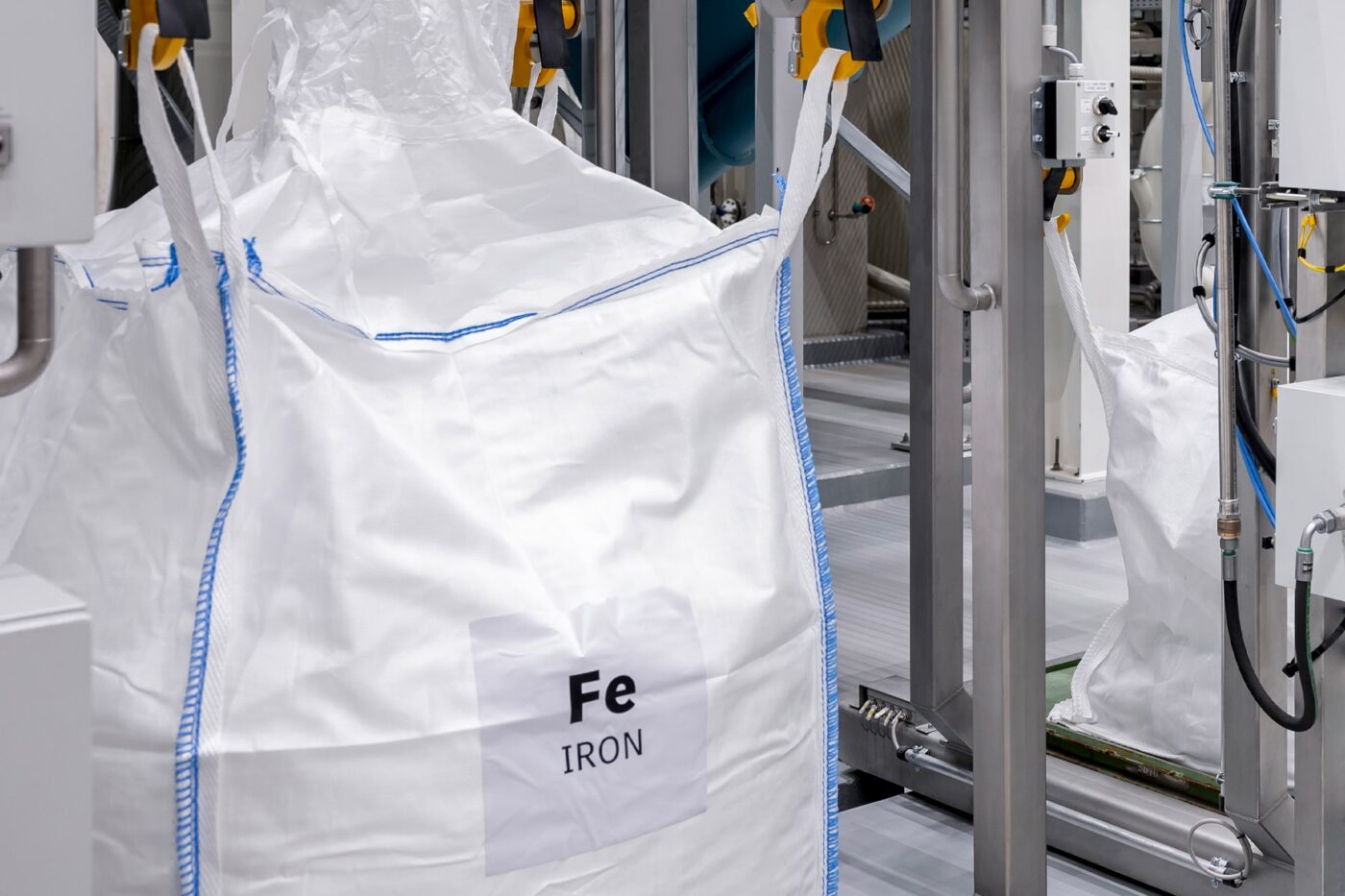
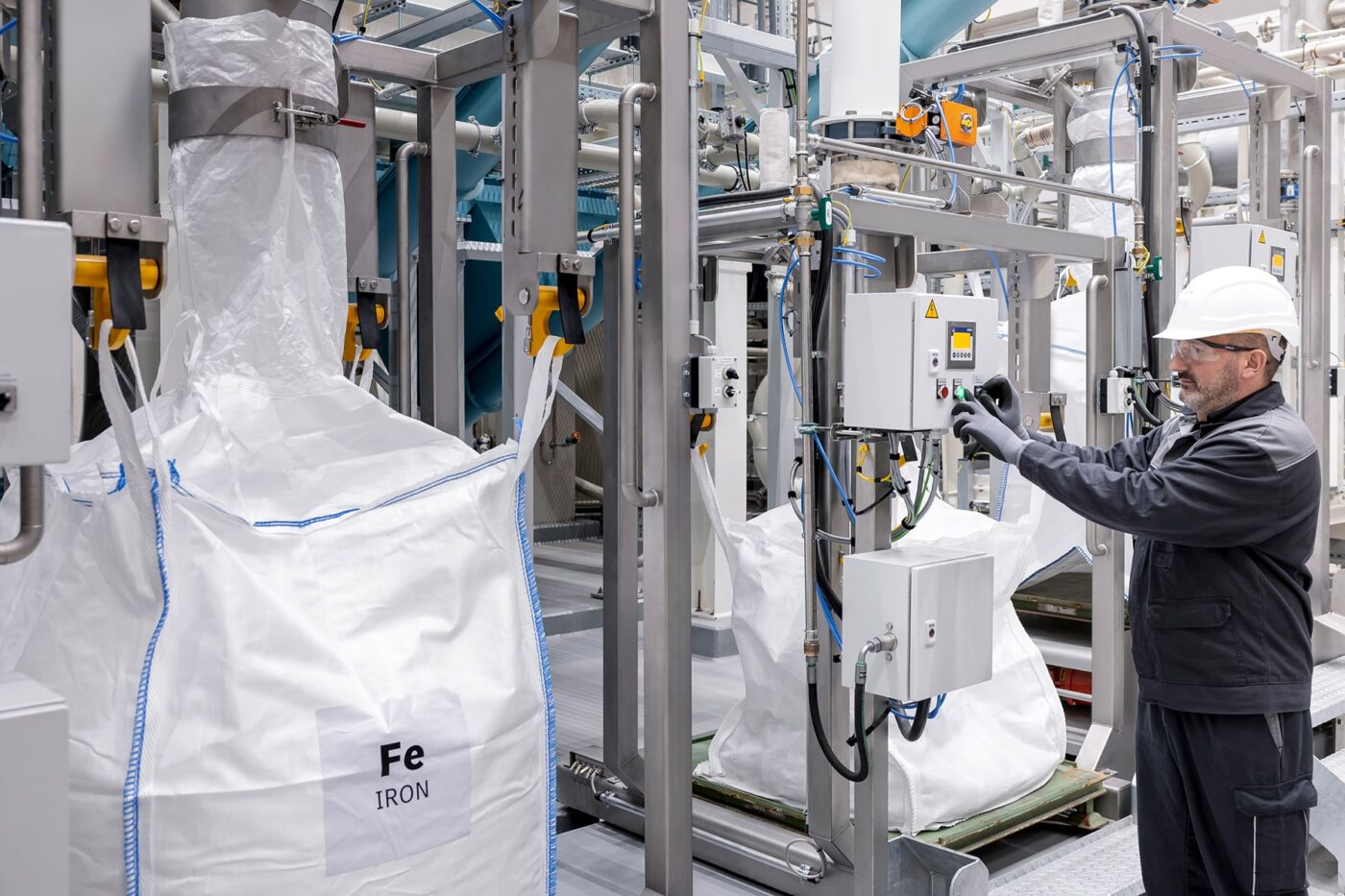
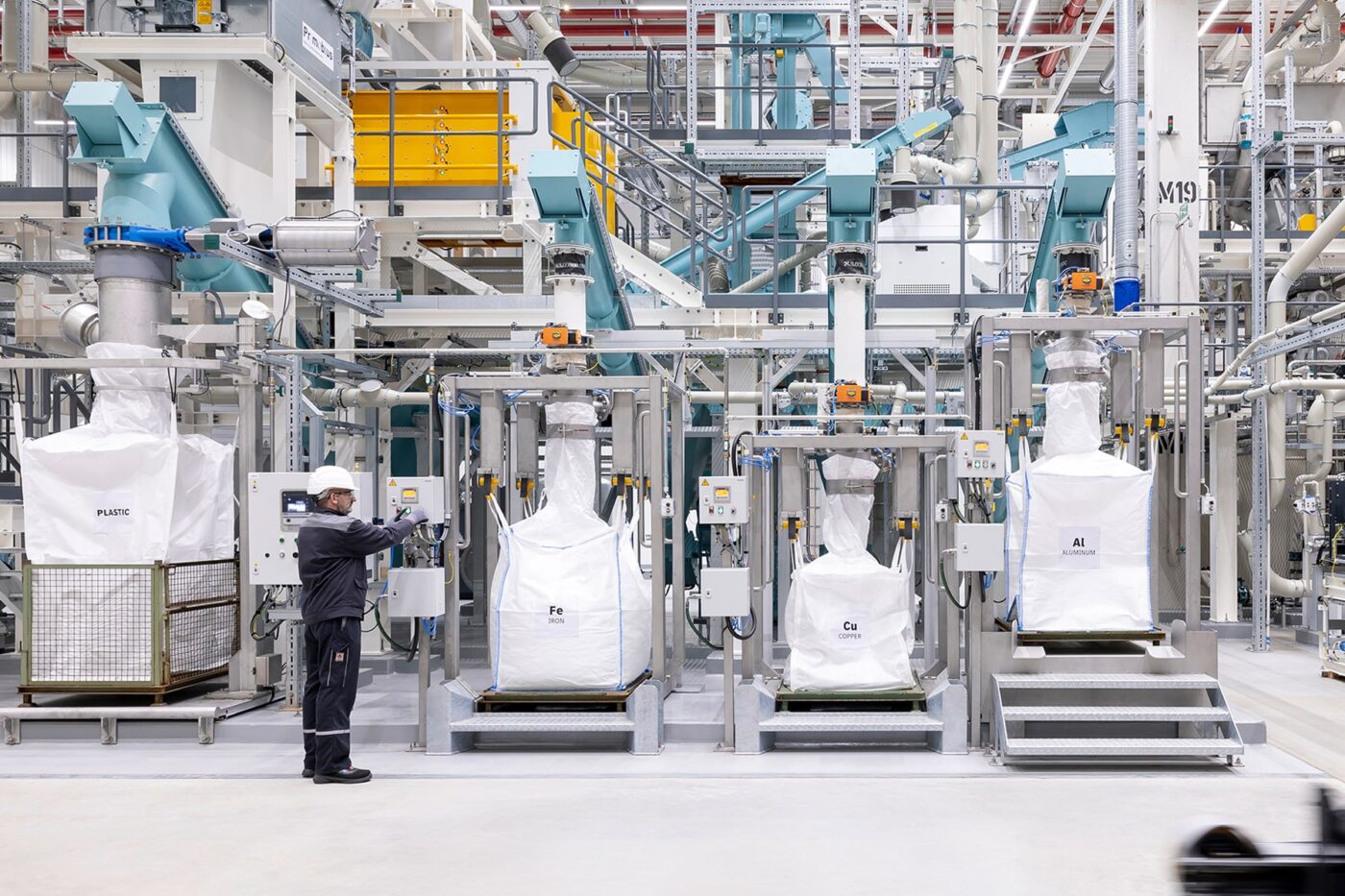
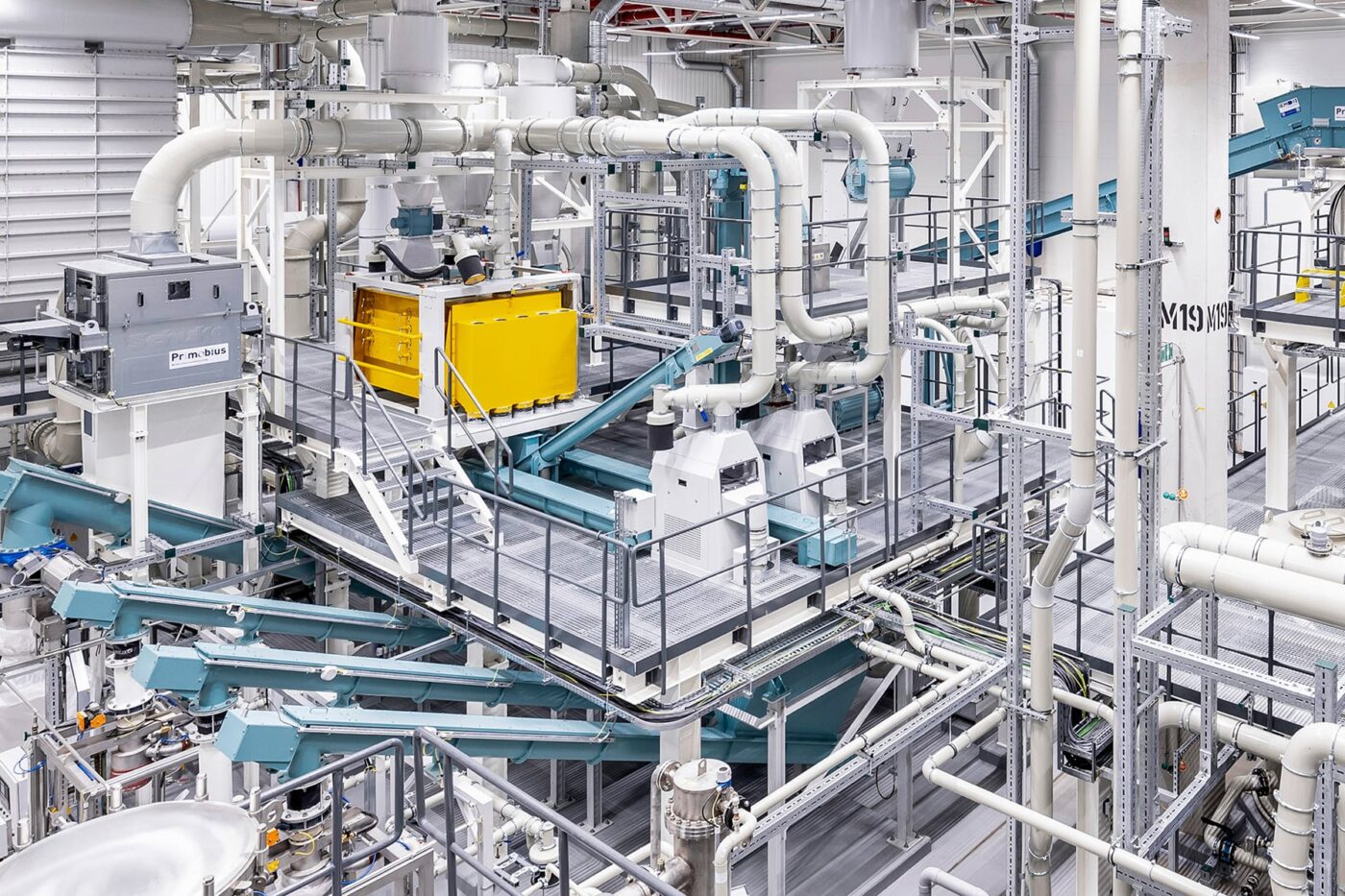
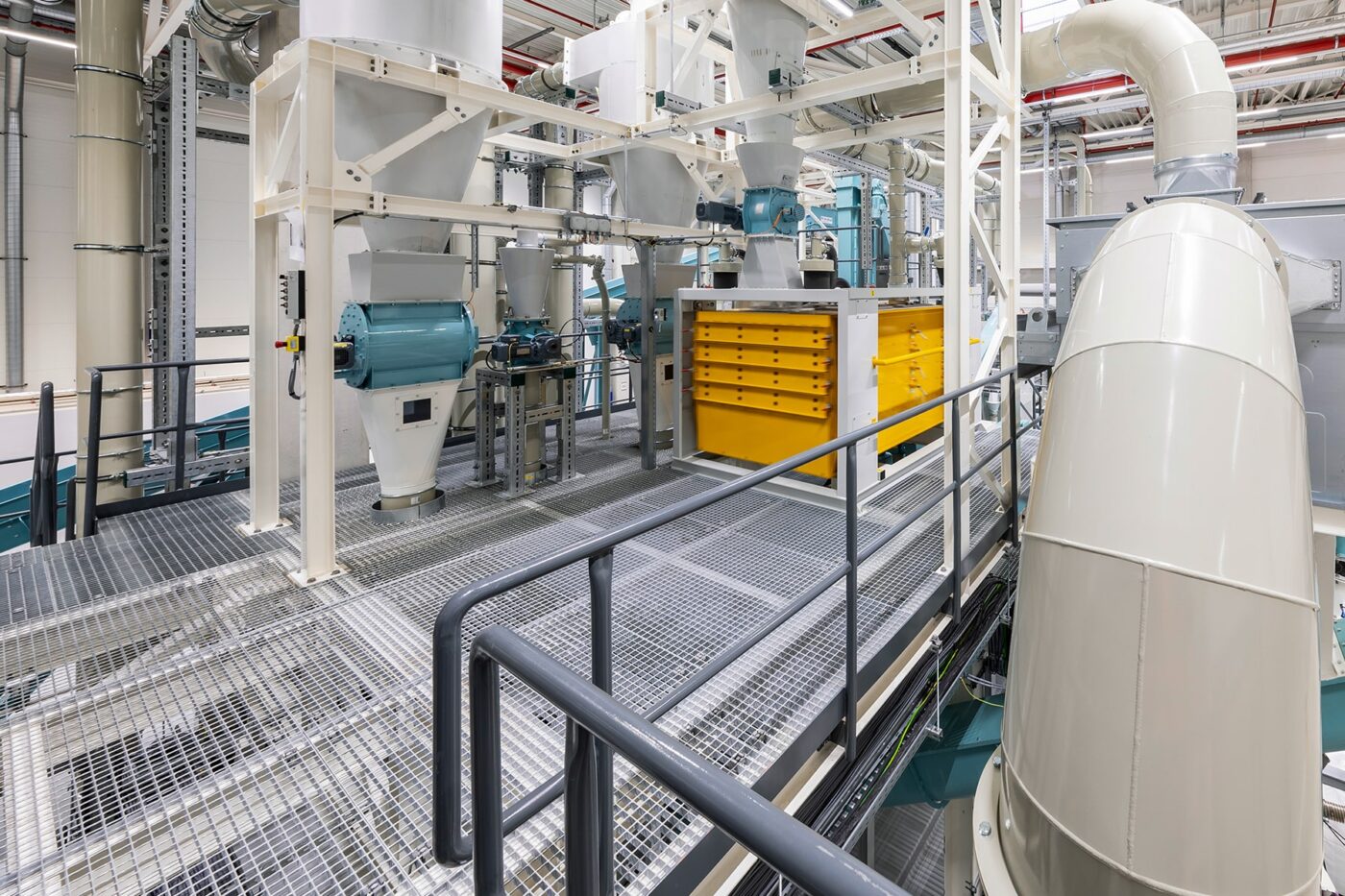
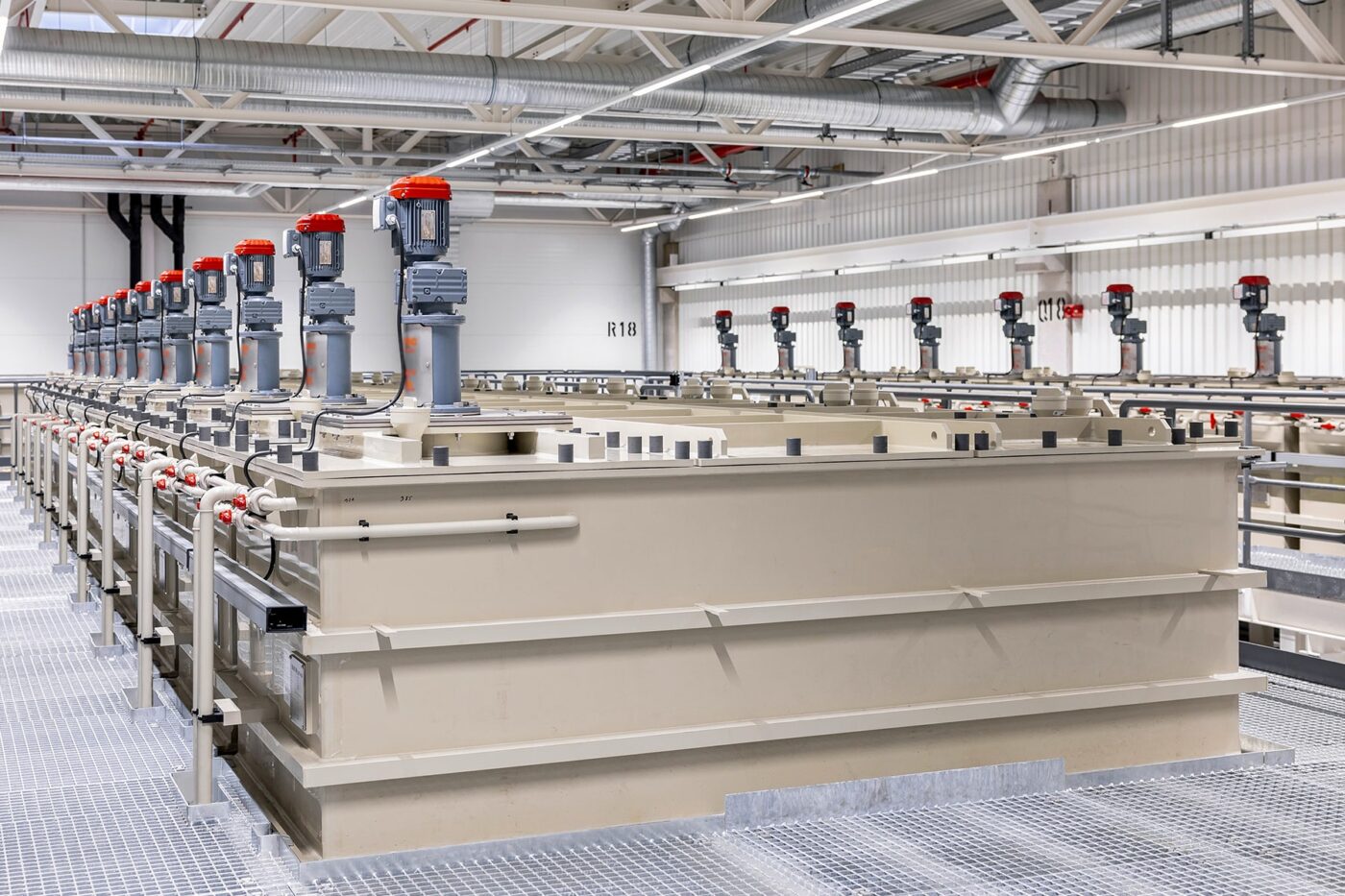
The plant that has now opened has been casting its shadow for quite some time. The first reports that the then Daimler AG was considering such a recycling plant on the site of the press plant in Kuppenheim date back to February 2021. Kuppenheim is only a few kilometres away from the compact car plant in Rastatt, but east of the A5 motorway and therefore no longer on the territory of Rastatt. Later in 2021, the company confirmed the recycling plans. Some time then passed before the foundation stone was laid, which was in March 2023. At that time, however, construction only began on the first phase, the mechanical shredding.
The second phase, with the all-important hydrometallurgical plant, was only built later on behalf of Mercedes by Primobius. The battery recycling joint venture between the German mechanical engineering company SMS Group and the Australian battery material manufacturer Neometals was awarded the contract at the beginning of this year – the shredder plant was already supplied by Primobius.
Hydrometallurgical processing in Kuppenheim is said to not only achieve a very high recycling rate of 96 per cent, but is also energy-efficient and produces less waste, as Mercedes emphasises – however, pyrometallurgical processes, the energy-intensive melting down of the battery, are used as a comparison in this statement. A comparison with other hydrometallurgical processes is not mentioned. ‘It works with low process temperatures of up to 80 degrees Celsius and therefore consumes less energy. In addition, like all Mercedes-Benz production plants, the recycling plant is operated on a carbon-neutral basis. It is supplied with 100 per cent green electricity,’ says the car manufacturer. The roof area of the 6,800 square metre building is equipped with a photovoltaic system with an output of more than 350 kilowatt peak.
Not only representatives from the Mercedes Board of Management – such as CEO Ola Källenius and Jörg Burzer, the Board Member responsible for supply chains – attended the opening of the plant in Kuppenheim, but also German Chancellor Olaf Scholz and Baden-Württemberg’s Environment Minister Thekla Walker.
“The future of the automobile is electric, and batteries are an essential component of this. To produce batteries in a resource-conserving and sustainable way, recycling is also key,” Scholz is quoted as saying in the Mercedes press release. “The circular economy is a growth engine and, at the same time, an essential building block for achieving our climate targets! I congratulate Mercedes-Benz for its courage and foresight shown by this investment in Kuppenheim. Germany remains a cutting-edge market for new and innovative technologies.”
“As a pioneer in automotive engineering, Europe’s first integrated mechanical-hydrometallurgical battery recycling factory marks a key milestone towards enhancing raw-materials sustainability,” said Källenius. “Together with our partners from industry and science, we are sending a strong signal of innovative strength for sustainable electric mobility and value creation in Germany and Europe.”
Batteries as the raw material mine of tomorrow
Supply Chain Management Board Member Burzer added: “We are systematically deepening our expertise in the battery value chain. Following the opening of the Mercedes-Benz eCampus for development of new battery cell chemistries in Stuttgart-Untertürkheim, we are now sustainably closing the raw materials loop in Kuppenheim. The innovative technology enables us to recover valuable raw materials from the battery with the highest possible degree of purity. This turns today’s batteries into tomorrow’s sustainable mine for raw materials. The new battery recycling plant strengthens the role of the Mercedes-Benz production network with vehicle and drivetrain plants in Europe.”
In July, the company opened the Mercedes-Benz eCampus in Stuttgart-Untertürkheim. The car manufacturer’s battery research is to be pooled there in order to develop innovative high-performance cells and new production processes. The declared aim is to reduce battery costs by more than 30 per cent.
0 Comments