ICPT starts automated production of batteries for electric trucks and buses
The new line has a production capacity of 16,000 batteries per year. With the commissioning, the company has increased its overall production capacity from 0.6 to 1.2 GWh. And it will not stop there, saying that it will ultimately increase capacity to “up to 4 GWh.”
The production facility spans 16,000 square metres, while the total area is 58,000 square metres. The production time for a “complete battery system dedicated to heavy transport” only takes eleven minutes, ICPT states in its press release.
According to Impact, it is the most highly automated production of Li-ion batteries for electric commercial vehicles worldwide. It uses the TS7 conveyor system from Bosch Rexroth, for example. The latter can handle “batteries with dimensions of 1.8 m x 0.5 m x 0.5 m and a maximum weight of up to 1 tonne (the average weight of a single battery is around 300 kg).” Automation also included assembly, batching, bolting, vision inspection and a range of tests to ensure the product’s quality.
Moreover, the manufacturer emphasises that the new line meets the requirements for IATF 16949:2016 certification.
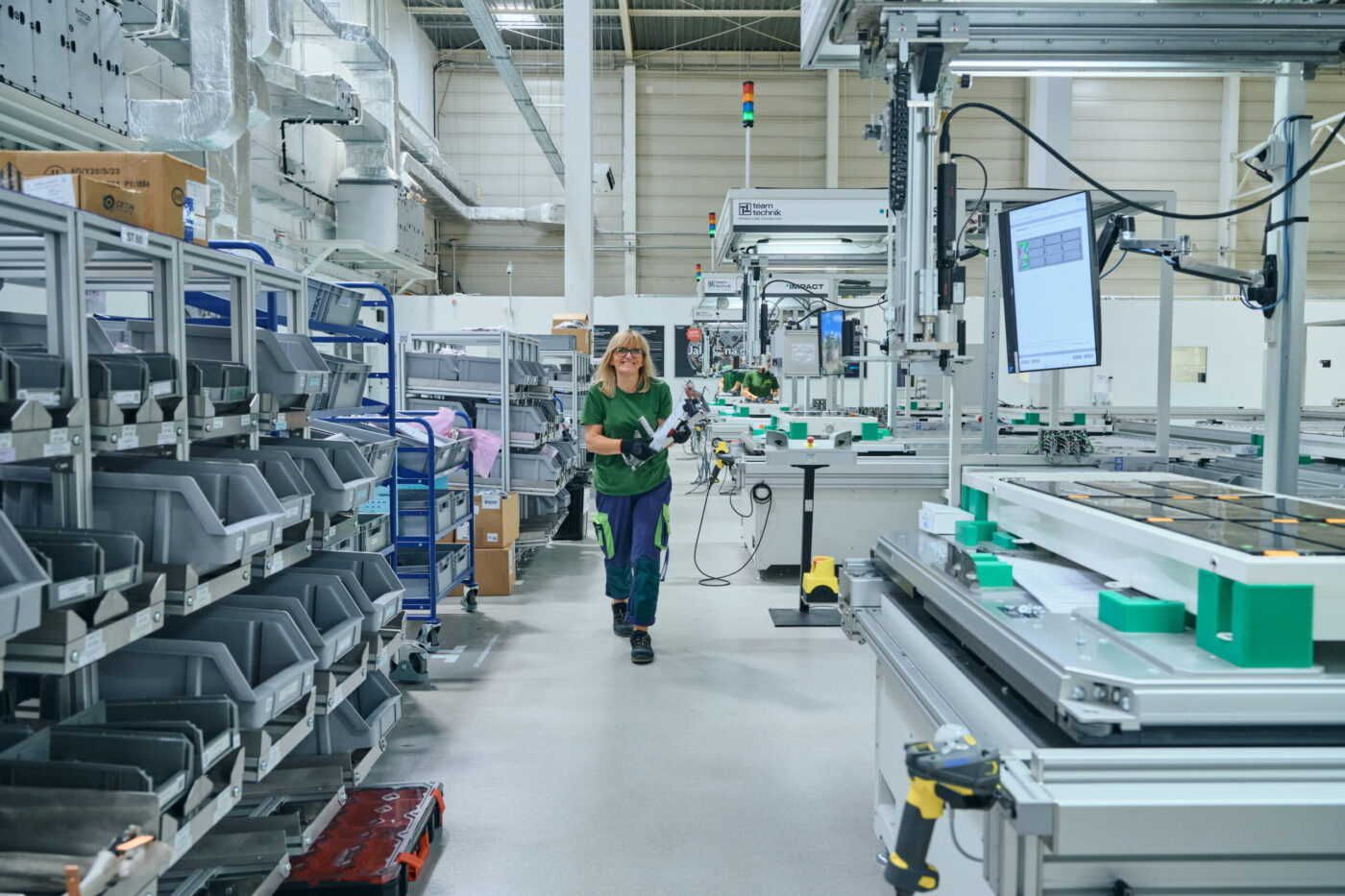
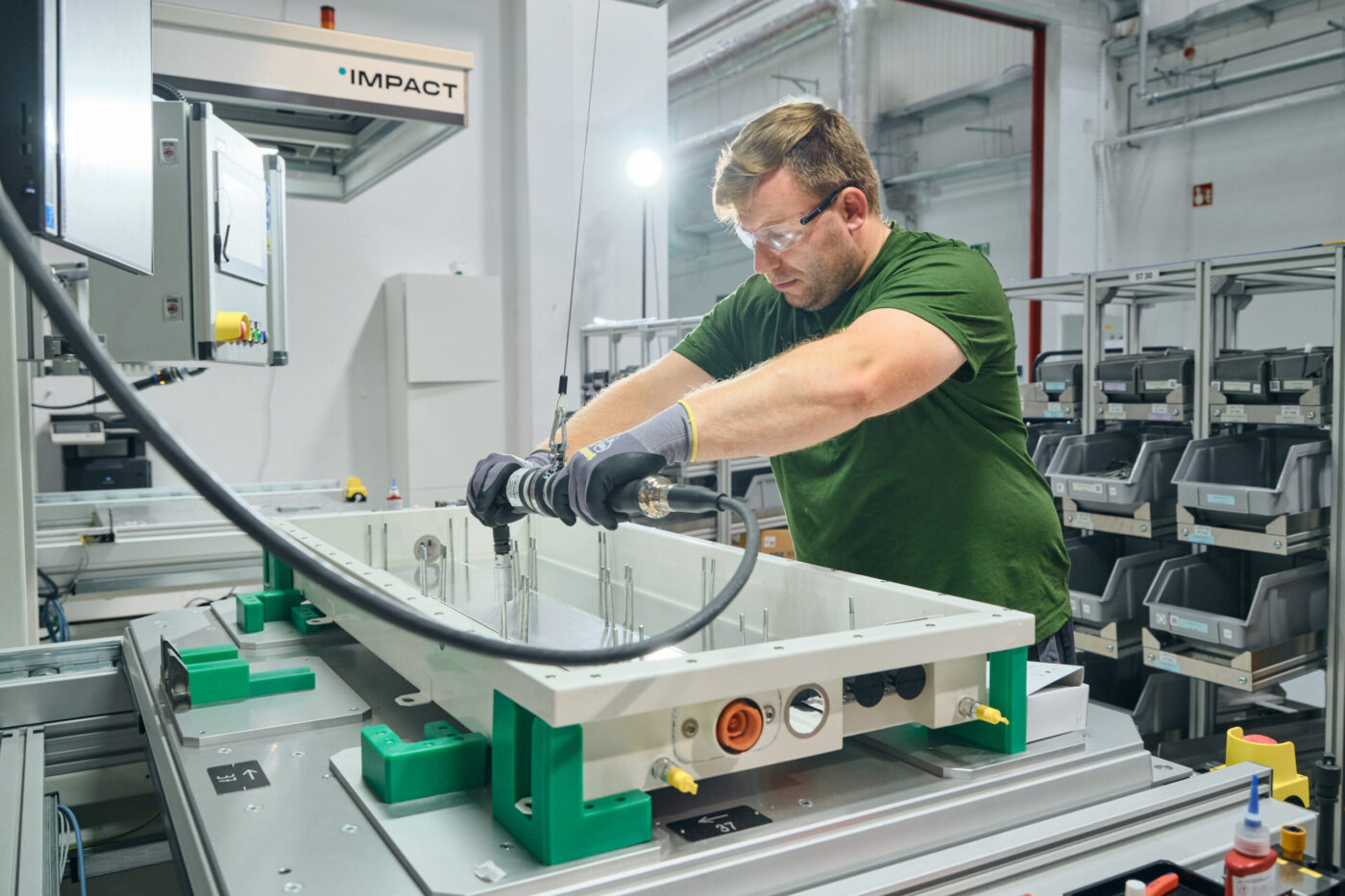
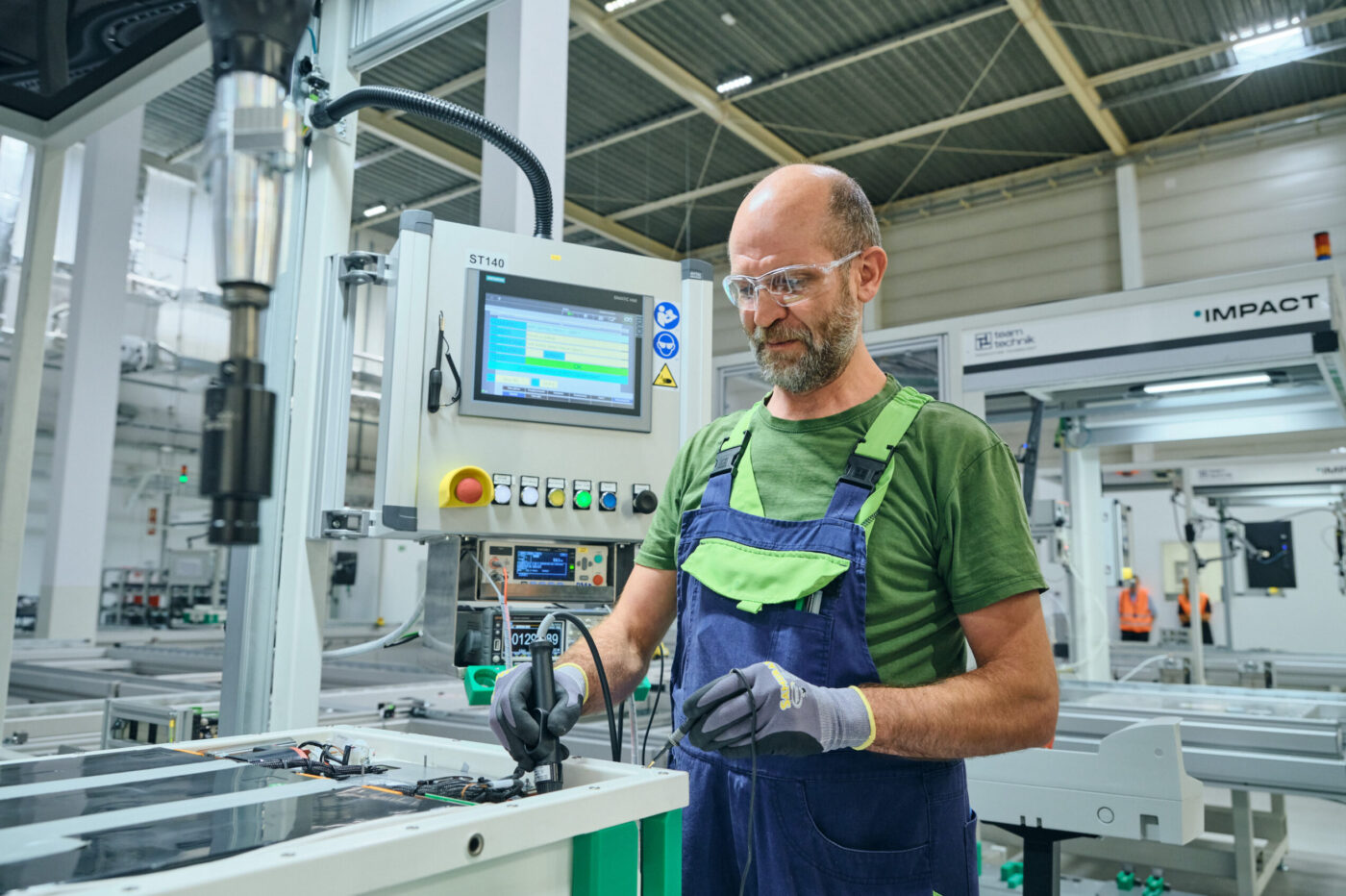
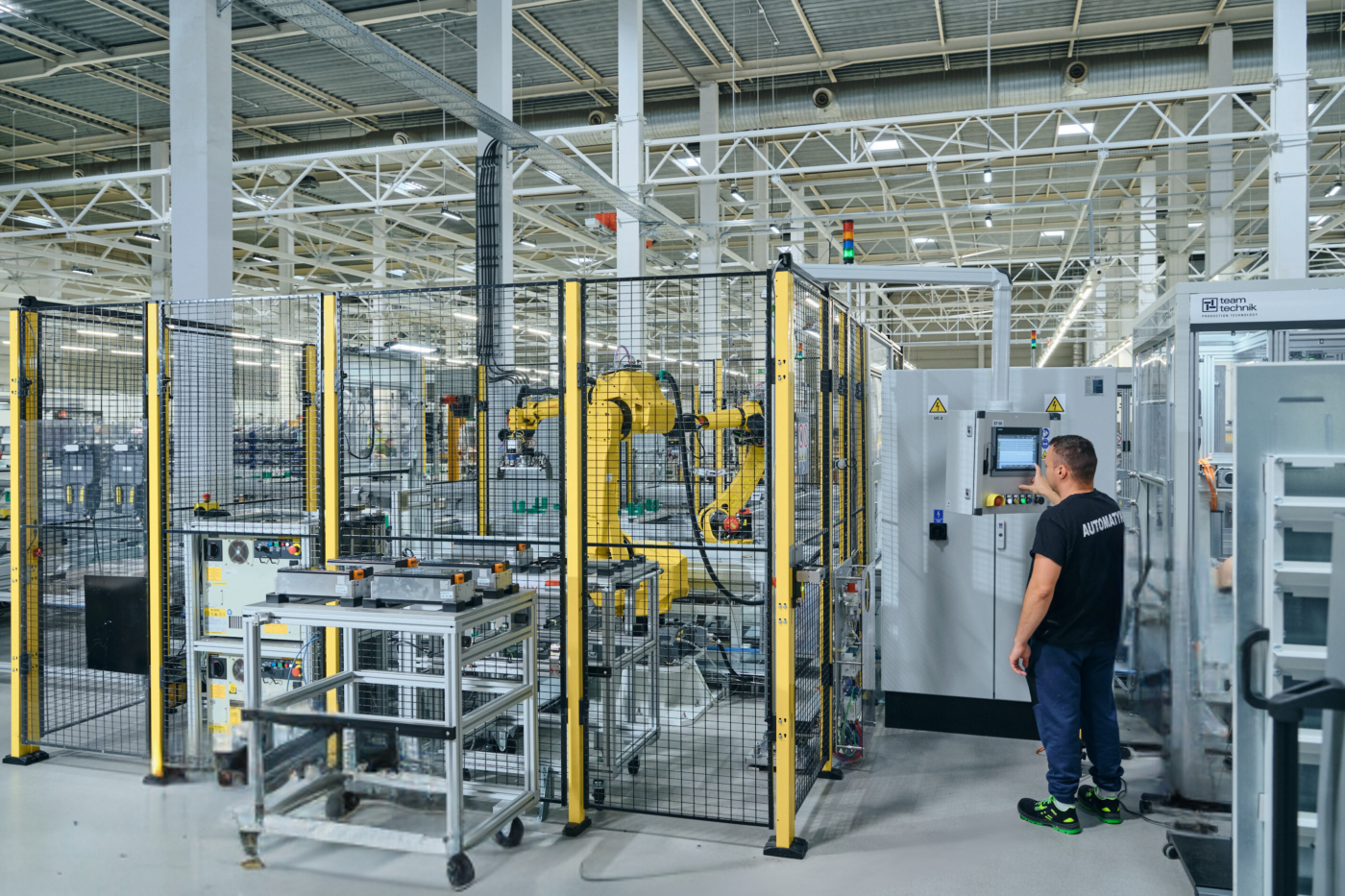
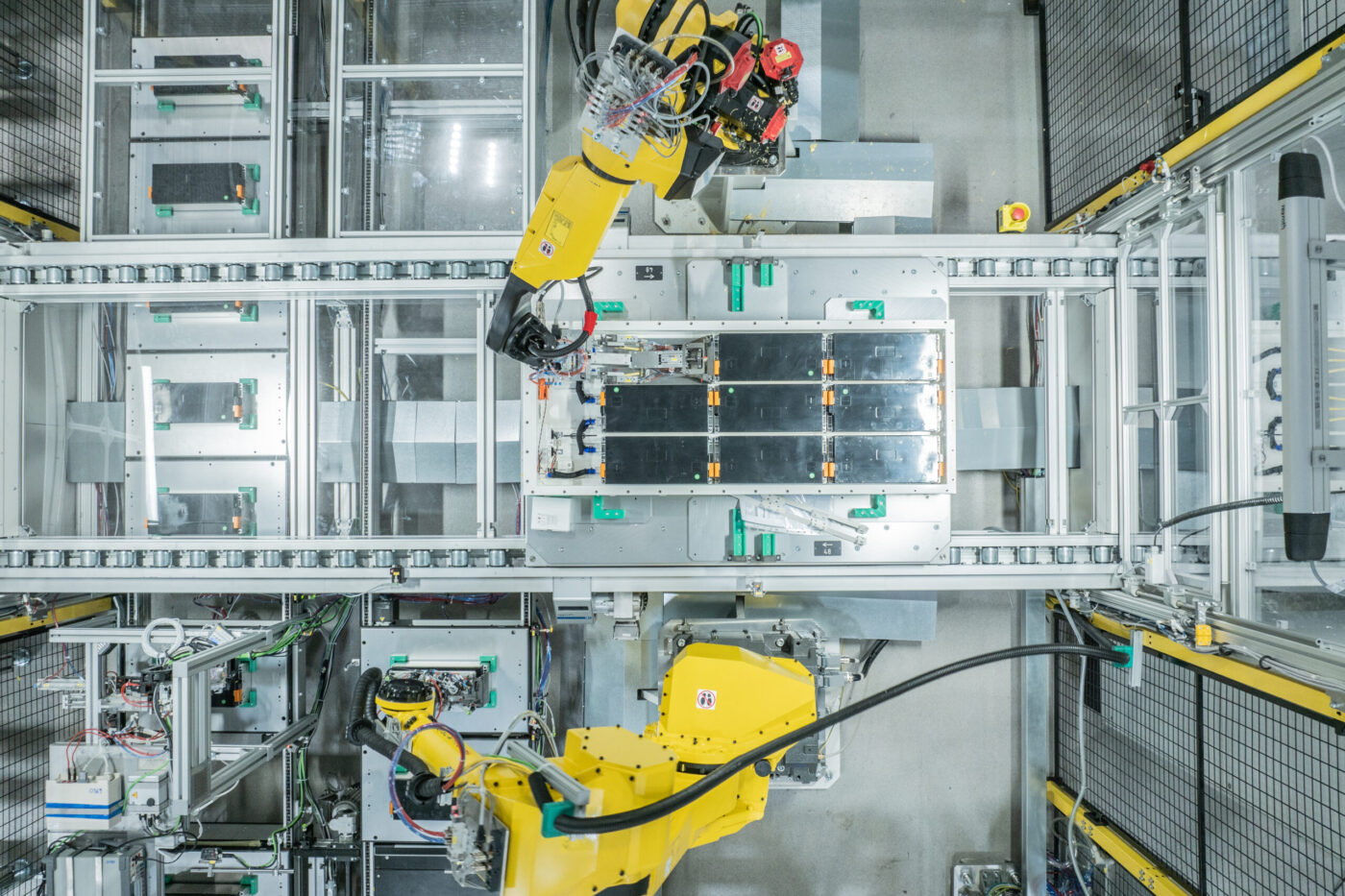
One of ICPT’s biggest customers is the Polish bus manufacturer Solaris. Bartek Kras, Vice President and CTO at Impact, says, “more than 80 per cent of all Solaris buses use our batteries.” Another client is Alexander Dennis. “Today, almost 4,200 buses in Europe use our batteries. That makes us one of the largest bus manufacturers in Europe,” said Kras during our interview at the IAA Transportation.
At the moment, Impact focuses on NMC, LTO and LFP cells, which it mainly gets from LGES. However, Kras emphasises that “the blends are coming.” He names the cathode that mixes NMC and LFP cell technology as an example. The company is also looking at semi-solid-state cells, a pre-stage to solid cells that are “five to six years away,” according to Kras.
Impact uses “classic water cooling ” and projects a lifespan of ten to 12 years or one million kilometres for its batteries. “This is not automotive—that is a completely different world. And here, TCO is the most important parameter.”
Source: Information per mail
0 Comments