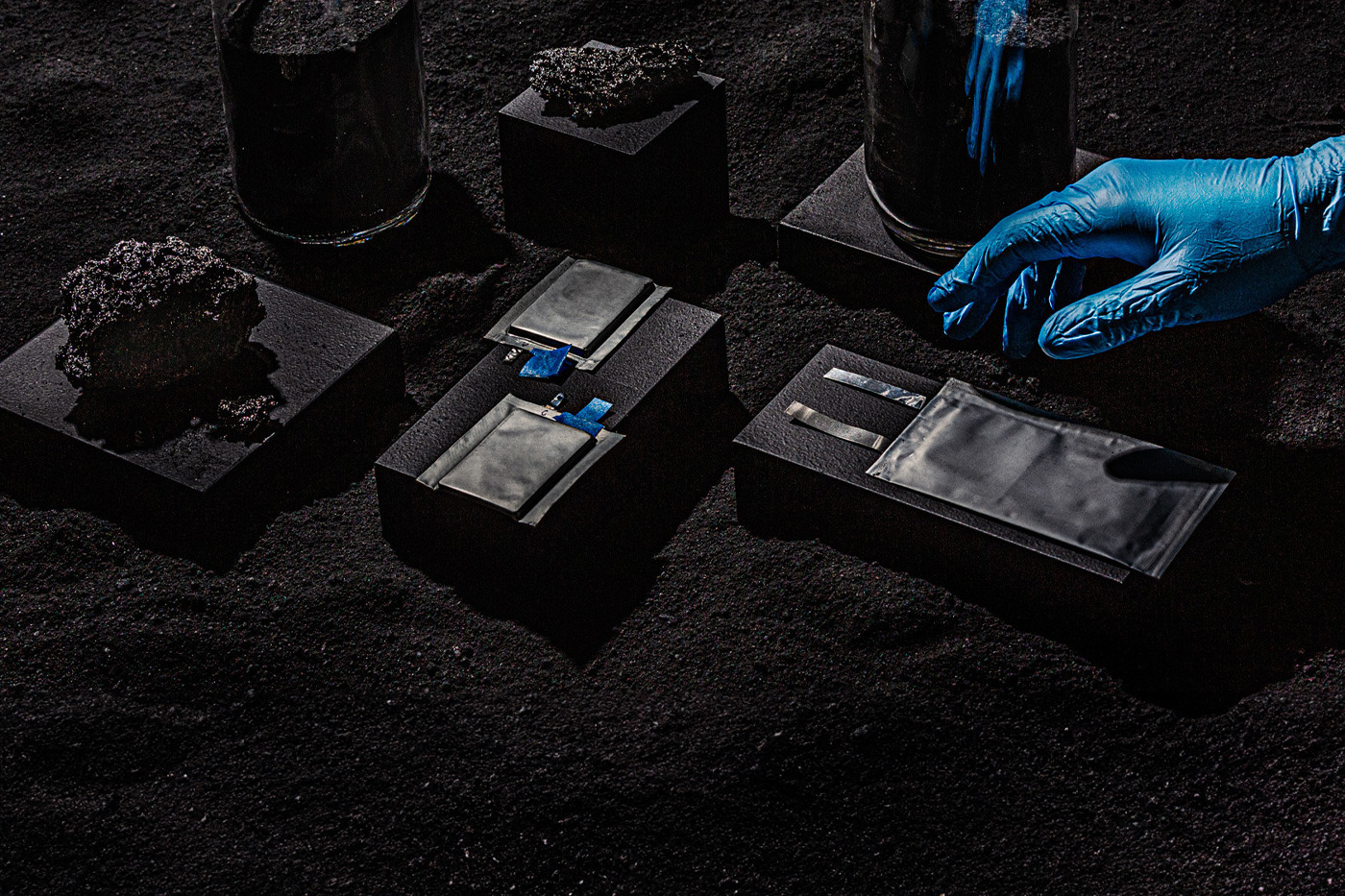
“What supply chain strategies look like” – interview with Grant Ray from Group14
Group14’s flagship product, SCC55, is a stable silicon-carbon composite anode that the company says has five times the capacity of graphite (current anode materials) and affords up to 50 per cent more energy density than conventional graphite for lithium battery anodes.
Around 95 per cent of the anode side of EV batteries are currently made from graphite, making it the most demanded raw material of all battery metals. Over 80 per cent of both synthetic and mined graphite comes from China, which introduced export tariffs on graphite in December 2023. Ivan Lam from Counterpoint Research noted: “We believe that the average price of graphite will continue to rise in the future due to supply and demand imbalances, including Russia, which was one of the major graphite suppliers before the Russia-Ukraine war.” Efforts to ramp up the production of graphite outside of China have intensified.
Not surprisingly, Group14 has grown from a startup eight years ago to a multinational concern now supplying 95% of the world’s battery producers with its products from consumer electronics to high-performance electric vehicles and aviation. Local supply chains in Asia and Europe have been enabled by the production of silicon products in South Korea through a cooperation with SK, and a recent acquisition of Schmid Silicon in Schwarze Pumpe, Germany. Group14 is backed by Porsche as a major investor, and in July 2024, Porsche joint venture CustomCells signed a multi-year supply agreement with Group14. Group14 also supplies StoreDot, which provides batteries for Polestar, and Molicel, which makes batteries for North American electric aviation company Archer.
What has prompted the visit to Germany?
I’m working on what the needs are for our Germany team as we continue to build our presence. Not just in our offices here in Stuttgart, but also for what we’re doing in the Schwarze Pumpe area, as well as business development efforts throughout the EU.
We have started recruiting, so my job is to come here and ensure that we’re supporting the team and the growth that’s happening. And see to some of our more international needs. Being here allows me to give this my full attention.
I gather that the silicon factory in Schwarze Pumpe in Saxony and the deal with CustomCells are the two main foci.
There’s definitely the fantastic news that we’ve recently shared with CustomCells, and our ongoing partnership with Porsche, of course, which includes their suppliers and how they’re ramping up electrification.
What are Porsche’s needs for ramping electrification?
I’d love to talk about that, but it’s behind the curtain. We are making sure that we’re able to meet Porsche’s partners’ needs and make sure that we’re meeting all of their qualification stages as they move towards product rollouts. Timing for those product rollouts is really for Porsche to state.
Apart from those two major things, the CustomCells supply agreement and the new silicon and silane gas plant in Schwarze Pumpe, what are the other factors in Germany and Europe in particular? You talked about this international focus. What’s the strategy here that is also relevant to your visit?
Well, the way to frame that is we look at what electrification could look like over the next horizon. And what supply chain strategies should look like to support energy independence. Having a localised supply chain can free us from challenges related to shipping materials from single sources across the planet.
We look at what decarbonisation efforts and supply chain security look like. As a supplier of silicon battery materials, we can deliver synthetic materials anywhere in the world with localised manufacturing. Our materials can also help radically reshape what performance looks like. With silicon batteries, we see up to 50% more energy density and very fast charging. That changes how we view electrification for anything from EVs to eVTOLs to consumer electronics.
From my understanding, the Group 14 SCC55 product enables far less graphite, but doesn’t eliminate it altogether, is that right?
SCC55(r) can fully replace graphite.
Oh, wow. That’s big. I bet everybody’s very excited about that.
Yes. Battery manufacturers also don’t have to create completely new manufacturing lines. Our silicon battery material can roll straight into the exact same manufacturing processes that they already have. They just have to tweak the formulas because we’re a slightly different chemistry.
Of course, we’re not graphite; we are a silicon carbon composite. Customers can blend it with graphite so they can learn over time. They can say, okay, let’s try 10, let’s try 20, 50%, or full replacement. We can control the pace of their adoption. Some manufacturers are jumping straight into full replacement right now. Some are doing exceptionally high blends, which allows them to think about delivering products that allow engineers to start opening up new ideas for what products can be.
We’ve announced an agreement with CustomCells, which is fantastic. And maybe you’ve seen the announcements that we’ve made about the products coming out of Molicel. Some of their cells are now available in the market. It’s called the P50B, but they’ve also got other products in early stages that allow cells to charge potentially in seconds.
Molicel is based where?
They’re based in Taiwan, and they have a factory in Vancouver, British Columbia. Molicel is considered one of the early players in the lithium-ion battery space and now they’re working on cells that will be moving into EVs and eVTOLs, with high performance possibilities. And that cell is commercially available right now.
What are the main applications for road vehicles?
Consumer cars and vehicles in general. Of course, how OEMs decide to roll out new performance capabilities over time is out of our hands. But we hope to see widespread adoption. That’s really what we’re looking for.
Aviation seems to be a really big market for you guys. Can you tell me a bit about what kind of applications you’re looking at?
It’s good to look at our partners and who they’re working with. Whether that’s supply agreements for heavy drones, or what you’re starting to see in terms of being able to tip the scales from making things like electric aviation and eVTOL a commercial reality. It’s silicon batteries that are going to drive that. Silicon batteries enable a shift into having these high density, high power, and extreme charging cells that allow the parameters that make eVTOL a reality. And the same goes for shorter and mid-range electric aviation applications. That’s what they need to be able to push them into commercial reality.
In terms of bulk, how much of the company’s attention is focused on aviation?
We love all applications where we can help eradicate this kind of tethered life that we currently have to charging stations. Expect to start seeing pressure come from the big players in aviation. All that will roll out in the next year to five to 10 years.
I gather we are looking at localised supply chains. North America, Europe, Asia, Southeast Asia, I imagine the recycling and reuse loops have got to also be localised. Is that right?
I would hope so, but that lives beyond us with the battery manufacturers. They would be the ones implementing such recycling programs.
Does that mean that when your company does not deal with the recycled material that stays within once you’ve supplied to the battery loop, the silicon product stays within that group in a recycled manner? Is that correct?
We would never take the material back. But there are two major strategies that I’m seeing right now. One is that it is considered end-of-life and goes to, say, Redwood, where they break the cell down and go through their own industrial process to extract materials to be sold. The other strategy is that a single cell has use in multiple products.
I hear from what you’re saying that trying to accelerate the electrification of everything generally is more of a goal. How much does your involvement with Porsche influence that?
That’s an interesting question. Porsche was immediately a simpatico partner in that their push was to always find the edge of what technology and performance could be. So, our cultures are very similar in that sense.
We’re excited about a future powering Porsche EVs, there’s no doubt about that. We are also excited about a future powering all kinds of EVs and all kinds of mobility across the spectrum – that’s not just sedans, but eVTOLs. It puts us into any products with batteries that can be recharged.
About the new factory, how that’s going? It was supplying the solar industry and now the EV industry gives it a new life?
The Silane factory that we acquired in Germany is the world’s most efficient, best technology for silane gas, which is one of the two primary compounds we use to manufacture our silicon battery material SCC55(r). We are in the planning stages of restarting that factory now. This factory gives us an optionality for obtaining a critical precursor to SCC55(r). In addition, having the best technology in the world for silane gas means it can also be taken anywhere in the world.
Wow, have I understood correctly that German plant will be supplying actually initially all locations or where..?
It has potential to, but I can’t quite talk about that yet.
So, the SCC55 materials mean that battery makers can circumnavigate graphite geopolitical problems, basically…?
Yes. But it’s also thinking about where your supply chain challenges are going to be beyond any geopolitical issues. We saw what happened during the pandemic when a single source was cut off. Right now, 95% of graphite for EV batteries comes from China, but if there is another catastrophe that shuts off shipping – all factories cease. So, by delivering some immediate replacements for graphite in regionalised areas, we can help reduce and alleviate that stress point.
I gather that if you’re recruiting or looking at how to build the teams, you’re talking about how many customers and how to scale at this period in the German factory.
Yes, and when one of our closest partners here in Germany is Porsche, we’re going to make sure we take care of our partners.
So, the Moses Lake site in the USA …
That’s a factory that is expected to be online with its first module later this year. And because we’ve got a modular manufacturing process, that site will continue to expand, even after the first module is up and running, because we can add extra modules even as we’re manufacturing SCC55(r). We’re building two modules right now. One is about a quarter or so ahead of the other. Module one is nearing the commissioning phase now and is expected to deliver SCC55(r) later this year.
The expectation is that within this year, we’ll continue to have materials coming out of our Seattle factory, and our second factory – BAM-2 (or battery active materials) which is in the Moses Lake area in Eastern Washington – is expected to be delivering, as well as through the joint venture factory with SK in South Korea. We’re expecting to be at global capacity for delivering SCC55 within the year.
Okay. And the German factory will take longer…
…For delivering silane gas. Yes.
And what timeframe are you looking at there?
Within 18 to 24 months is the expectation for the length of the restart.
In conclusion, the battery markets in Europe are actively ramping up. The race for the best battery materials and technology is still in full swing, as manufacturers are attempting to make their supply chains more efficient. Particularly the ability to eliminate the need for expensive materials such as graphite from its SCC55 material will likely prove an advantage in the race for more efficient and affordable batteries. While new fields of application, such as aviation, are also developing intensely, results are still some years away. We await the coming developments with much anticipation.
Thank you for making time for us in your busy schedule!
0 Comments