Daimler Truck opens Battery Technology Centre
The opening in Mannheim, Germany, took place around a year after the topping-out ceremony. According to the company, “product and process development for battery electric commercial vehicles is carried out on an area of over 10,000 square meters.” That is precisely where the BTC will help, combining development and production. The project was announced in May 2022 as part of a strategic partnership between Daimler Truck and mechanical engineering company Manz.
The BTC consists of two areas. In the first one, Daimler Truck will produce battery cells specially designed to meet the requirements of heavy commercial vehicles on a pilot basis. In the other, the manufacturer will build prototype battery packs to test them on test benches and in test vehicles. That way, Daimler Truck and the Mannheim site, in particular, are preparing for future series production, which is planned for the second half of the decade as part of the introduction of the next generation of lithium-ion batteries at the plant.
The BTC, still referred to as InnoLab Battery at the topping-out ceremony in 2023, is mainly located in an existing building with the number 18 – until 2020, machining for cylinder crankcases and flywheels took place there. Building 18 was built in 1952 and covers 7,500 square metres. It was gutted, extensively renovated and extended by 3,000 square metres for the conversion to the BTC. “Over 60 new machines and systems are being installed in the BTC, where the relevant processes for the prototypical production of battery cells and systems can be mapped: Coating technologies, welding processes, assembly and adhesive processes,” Daimler Truck specifies.
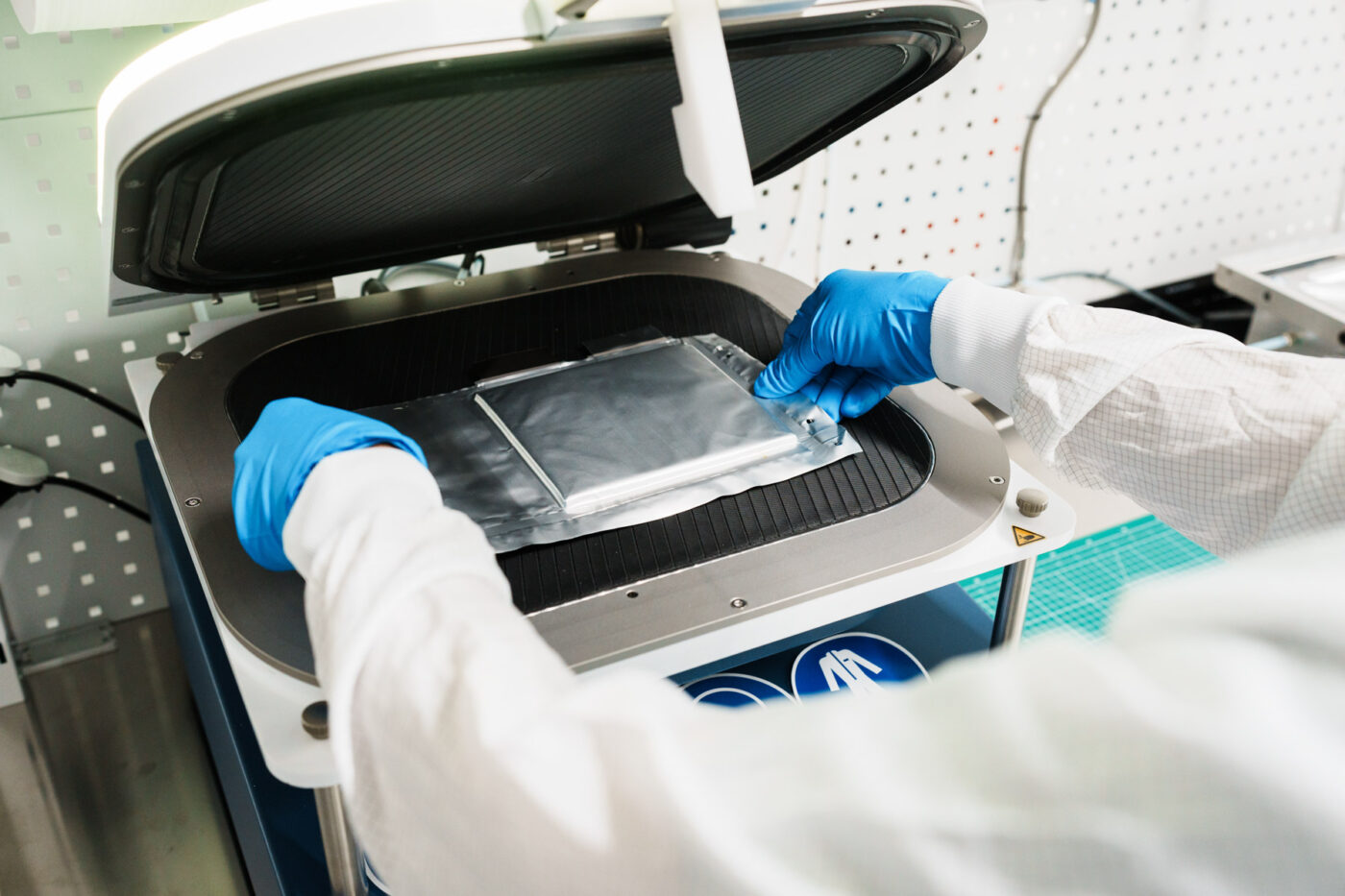
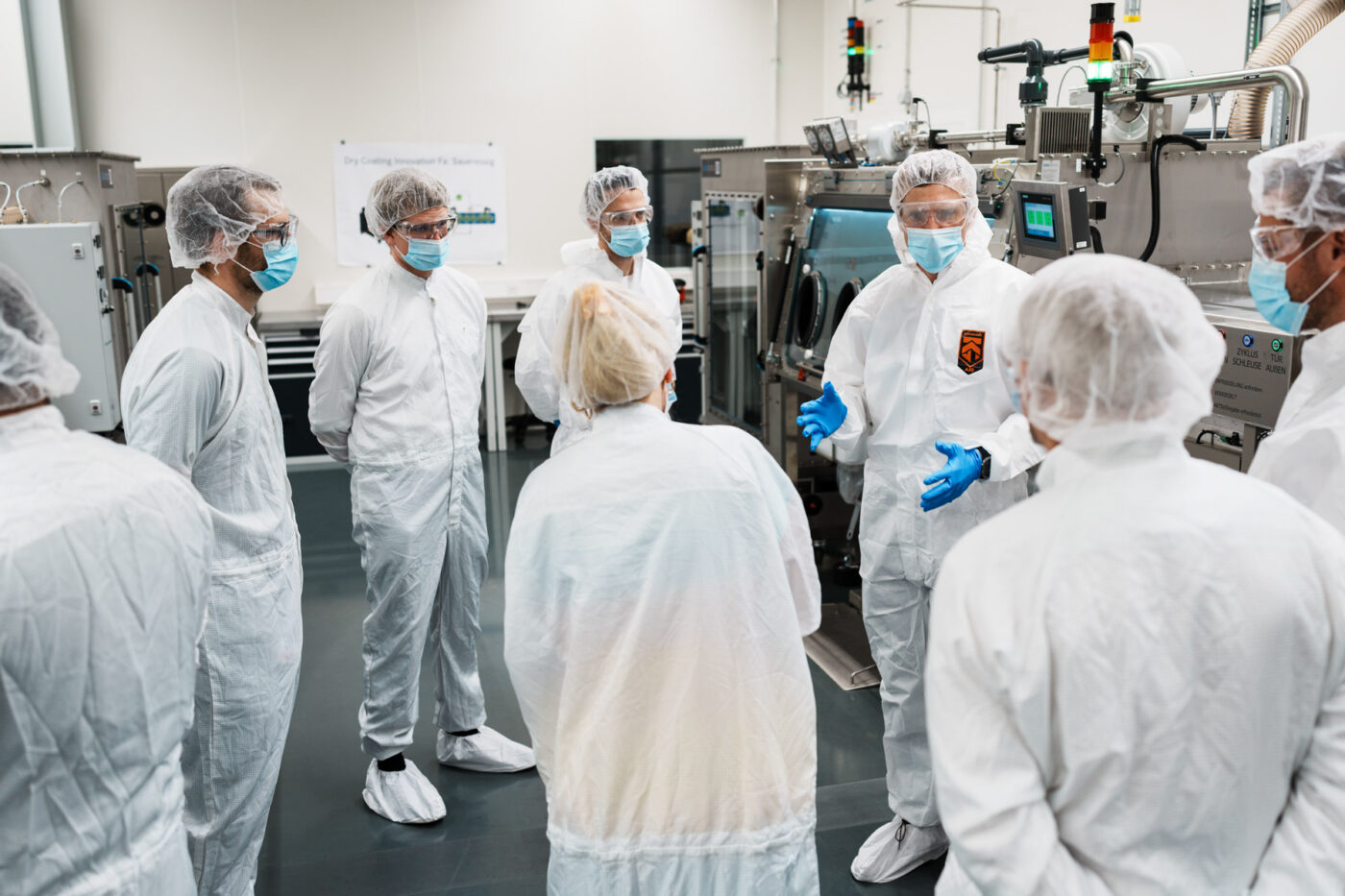
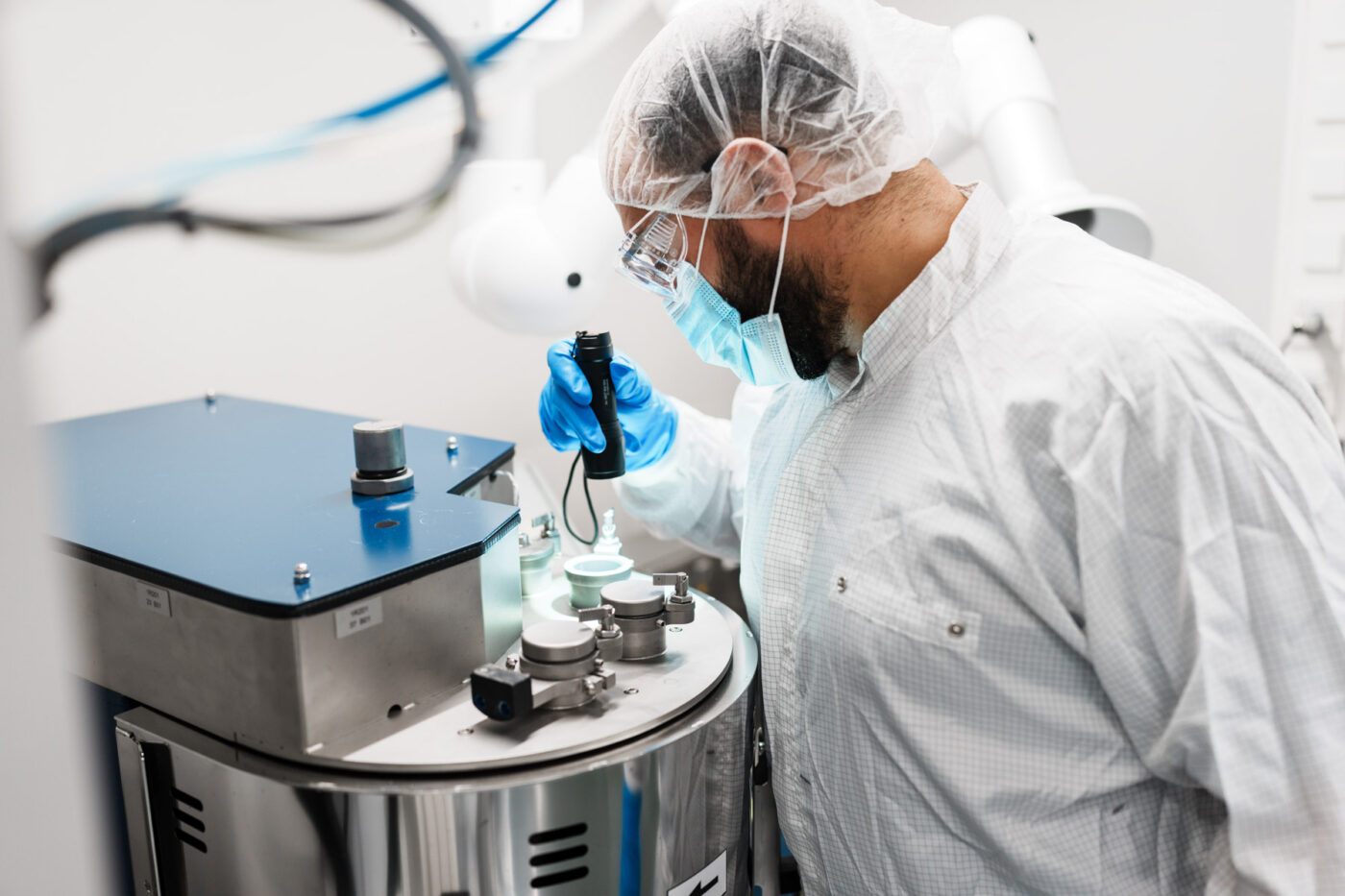
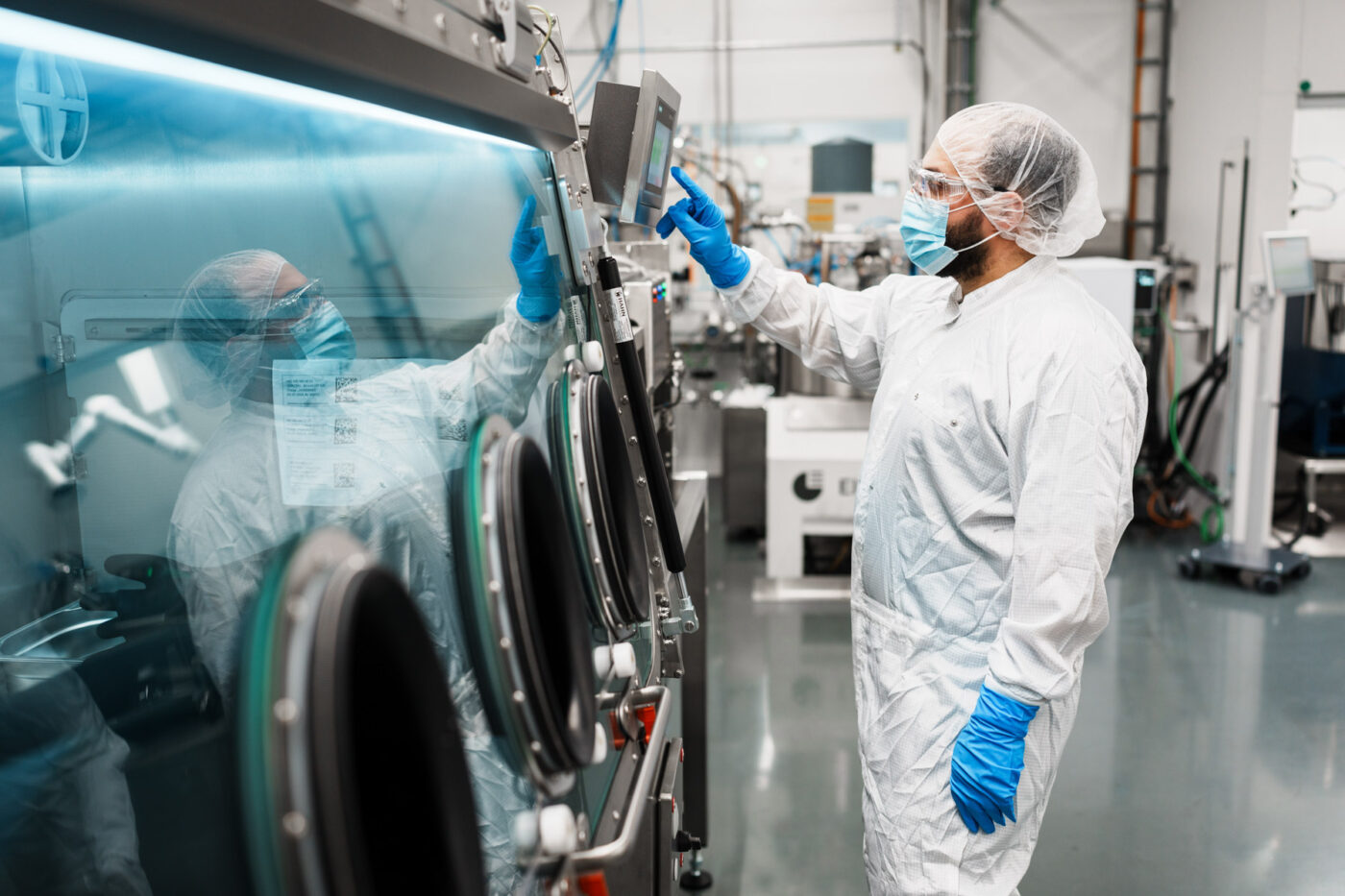
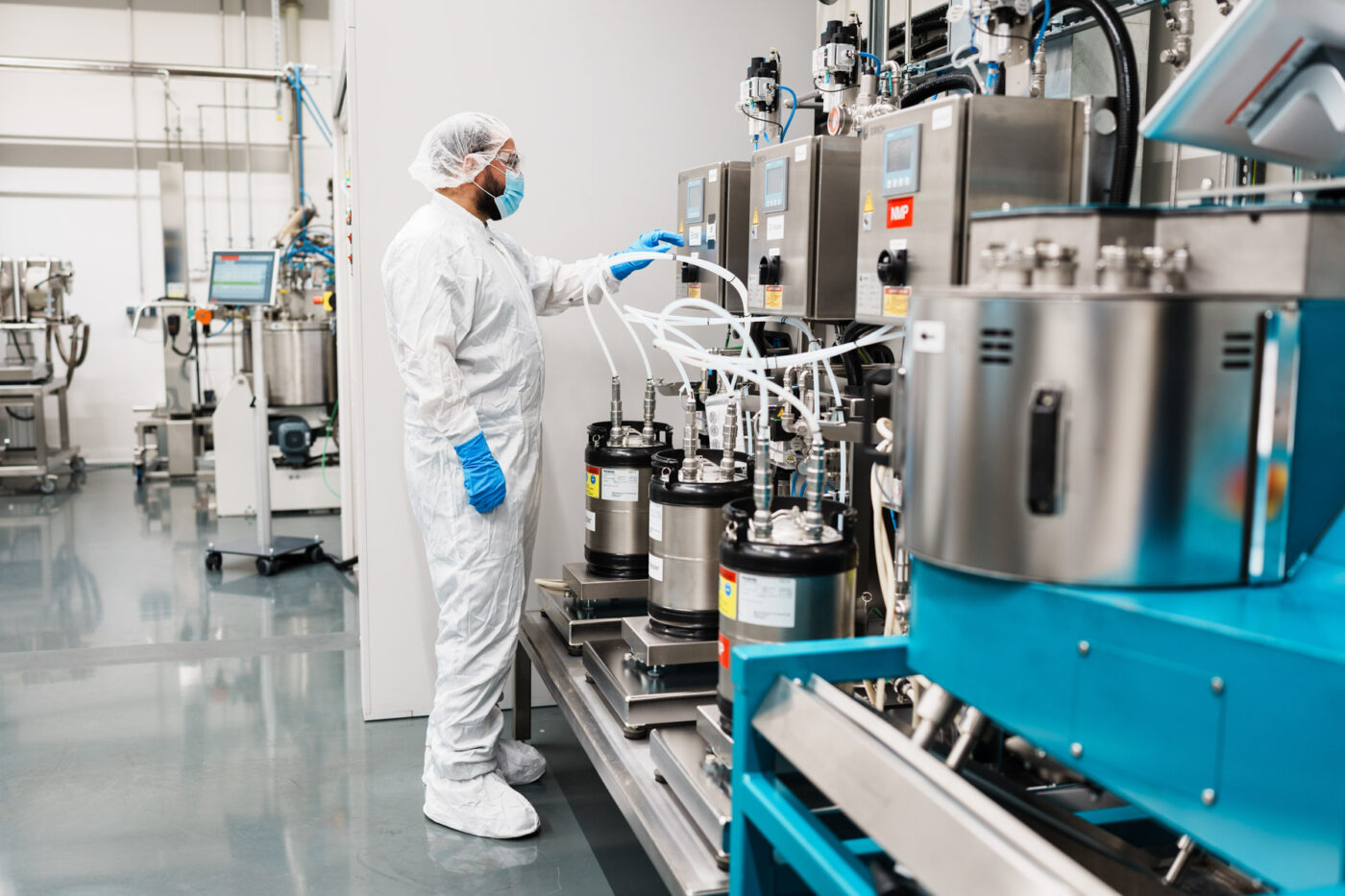
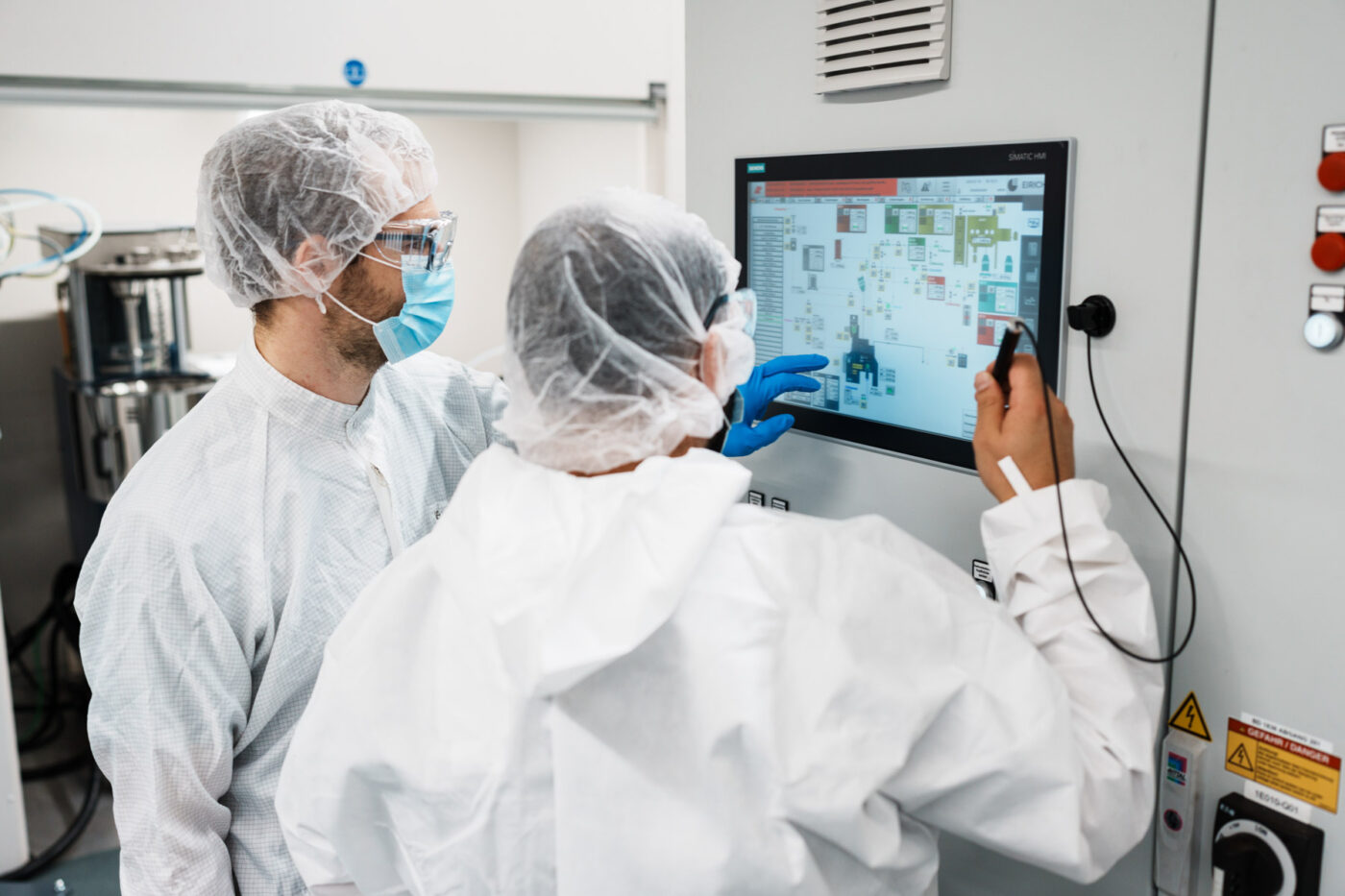
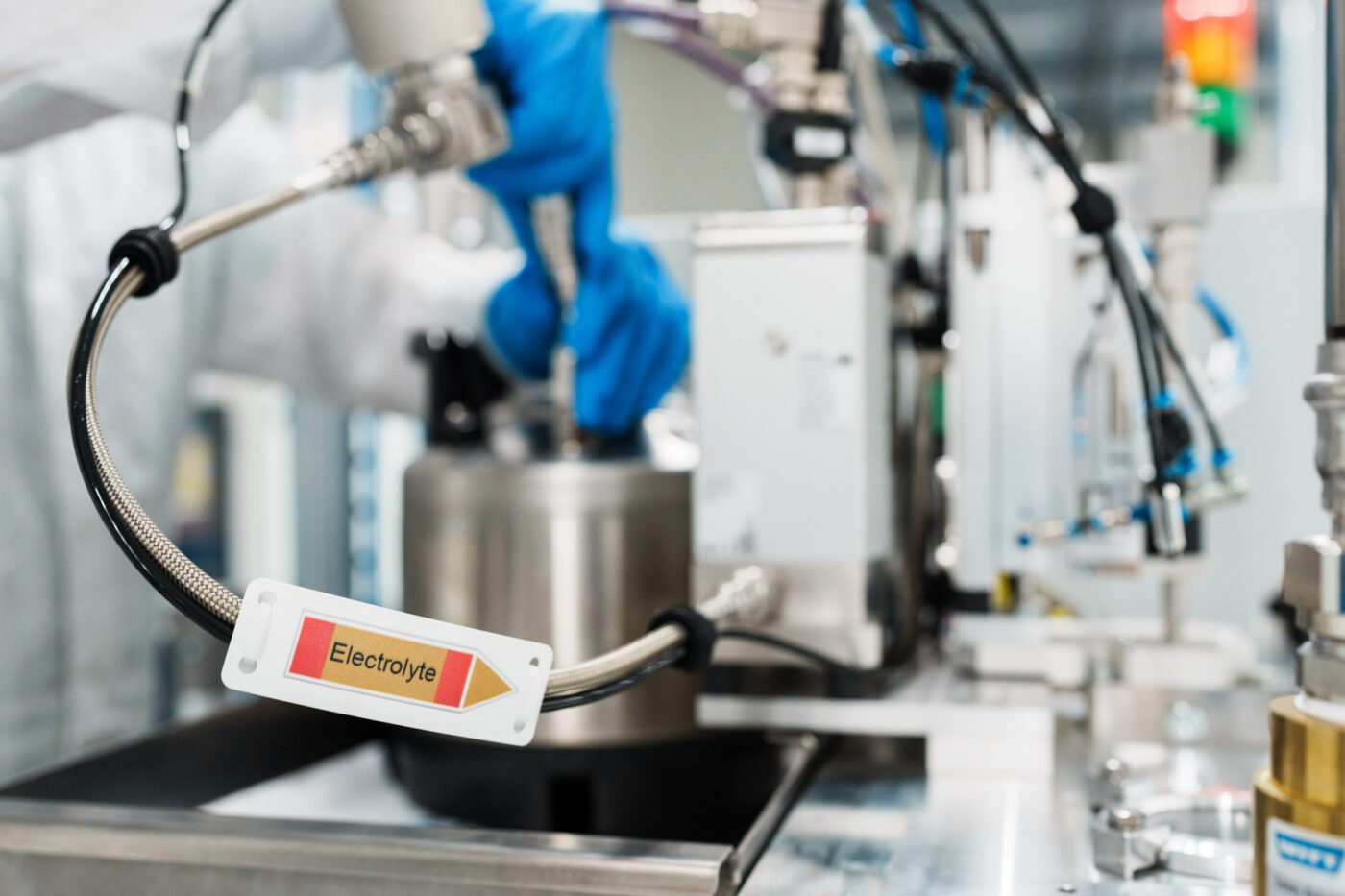
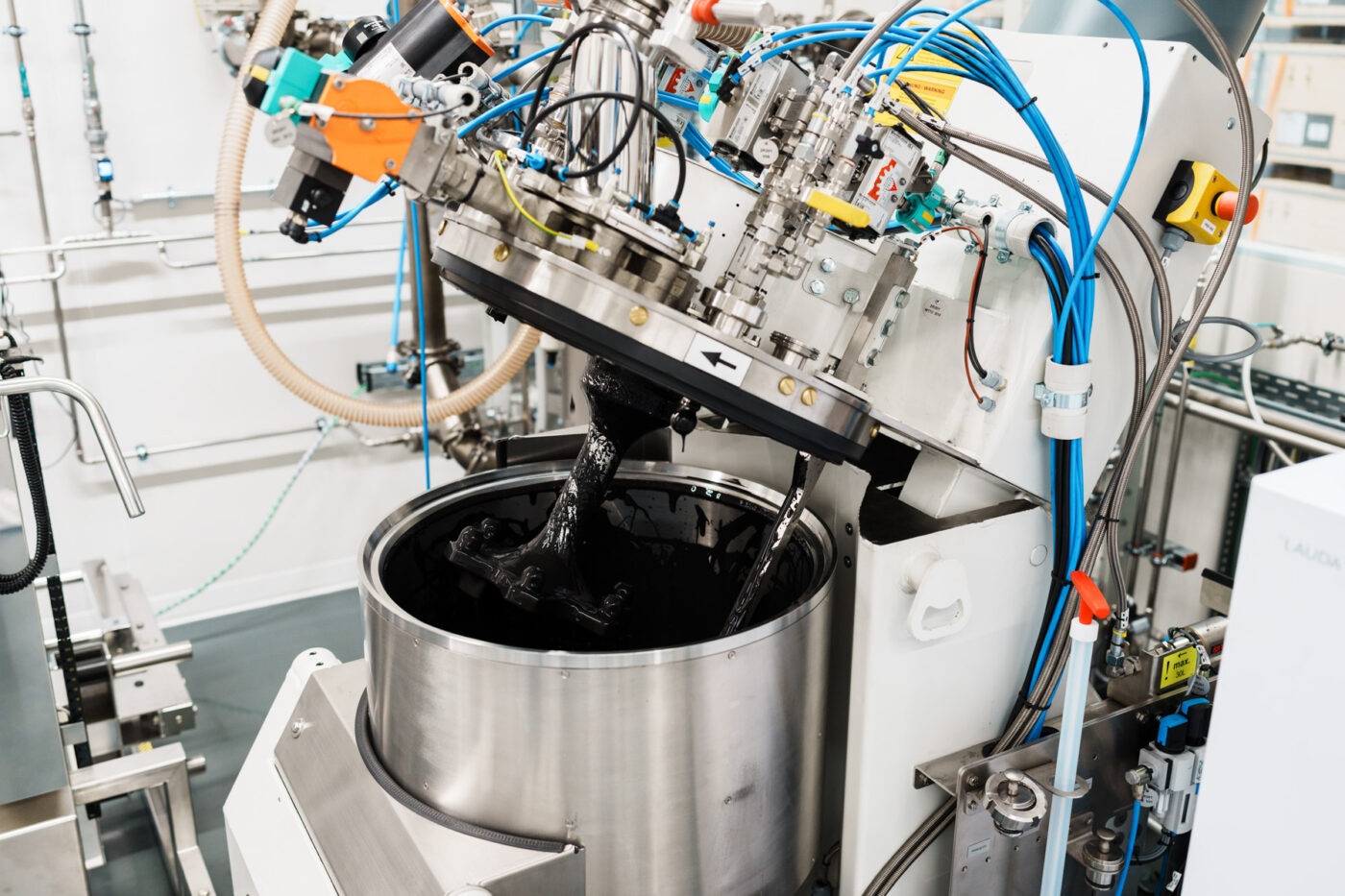
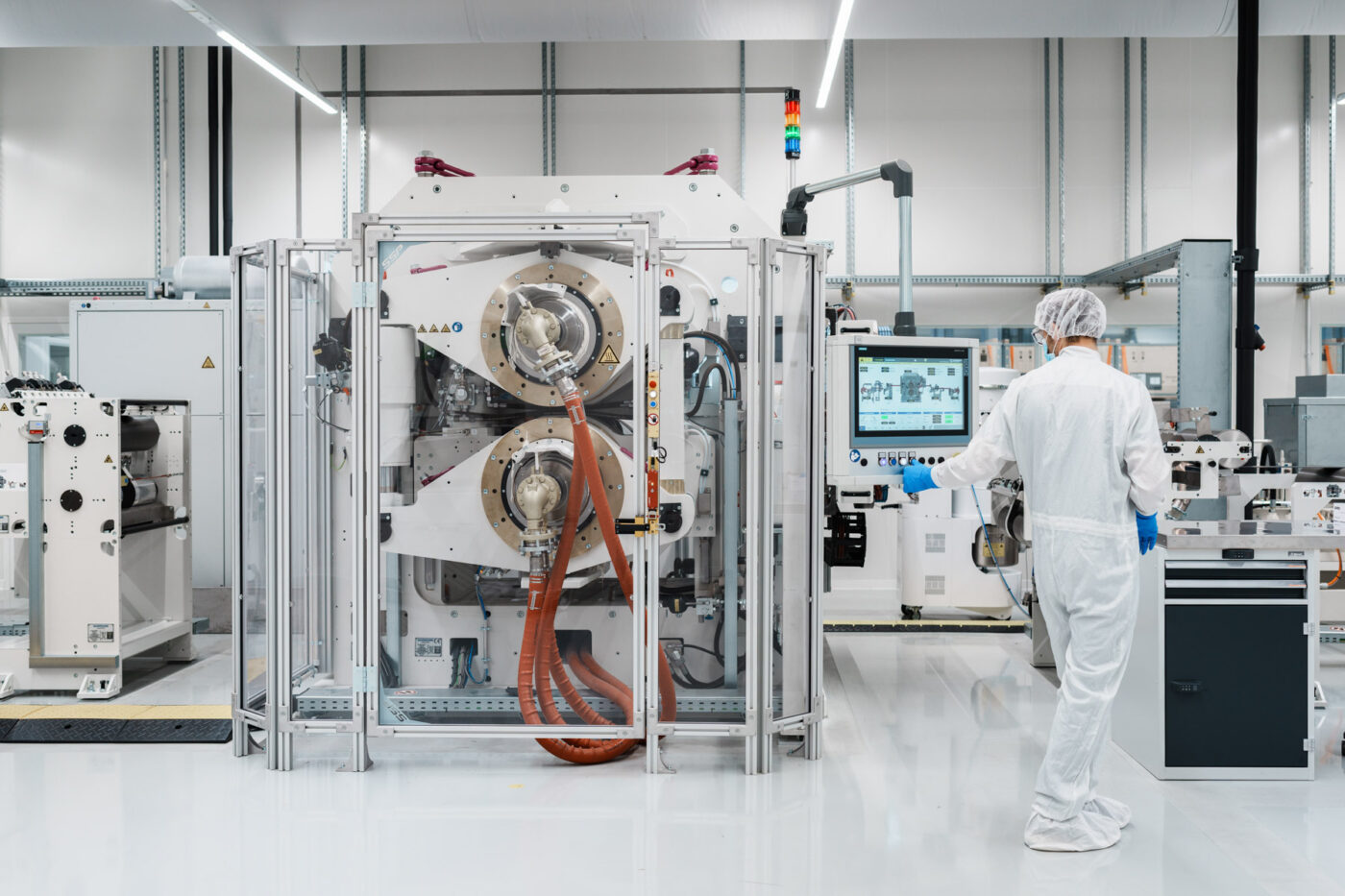
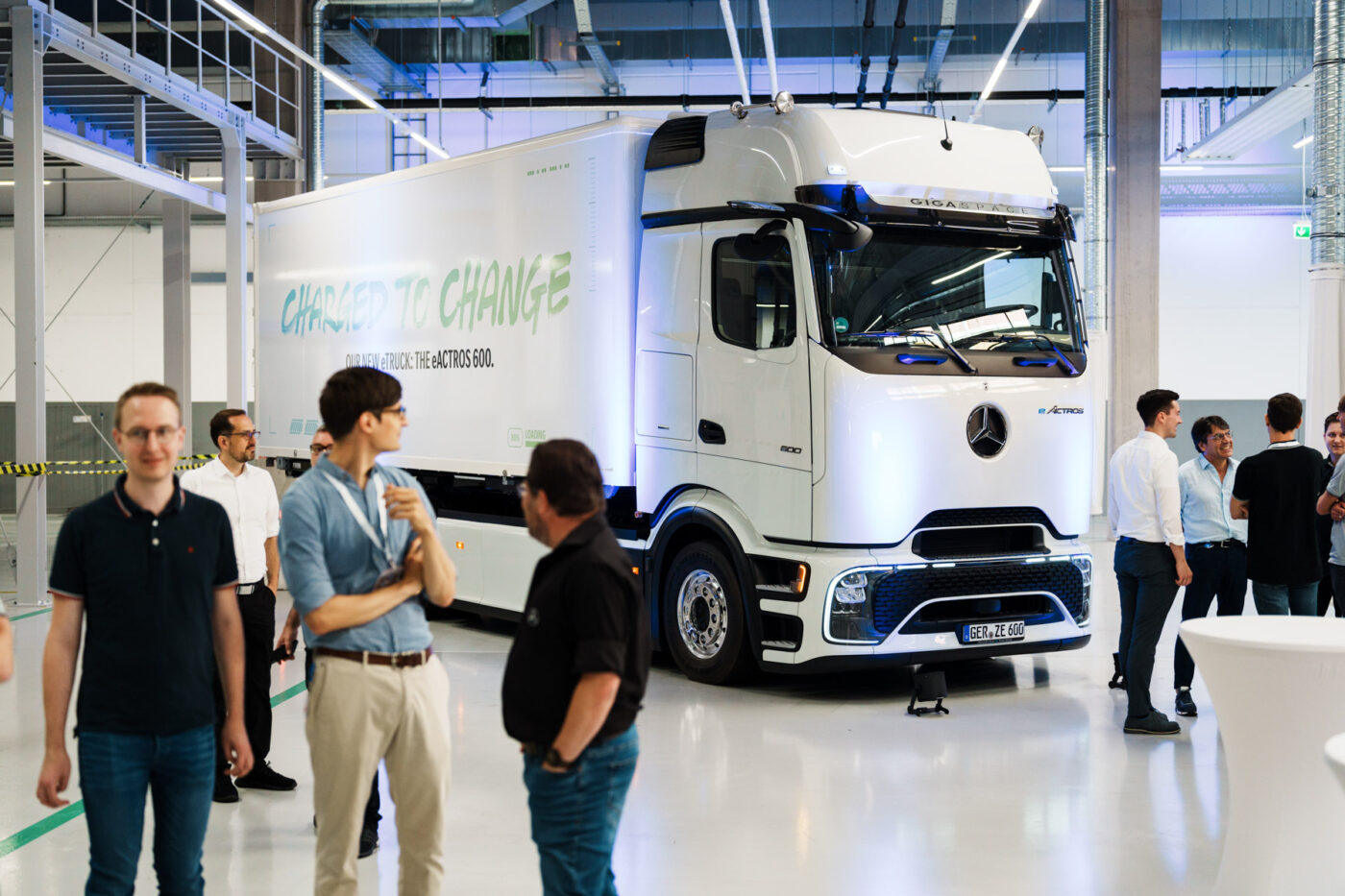
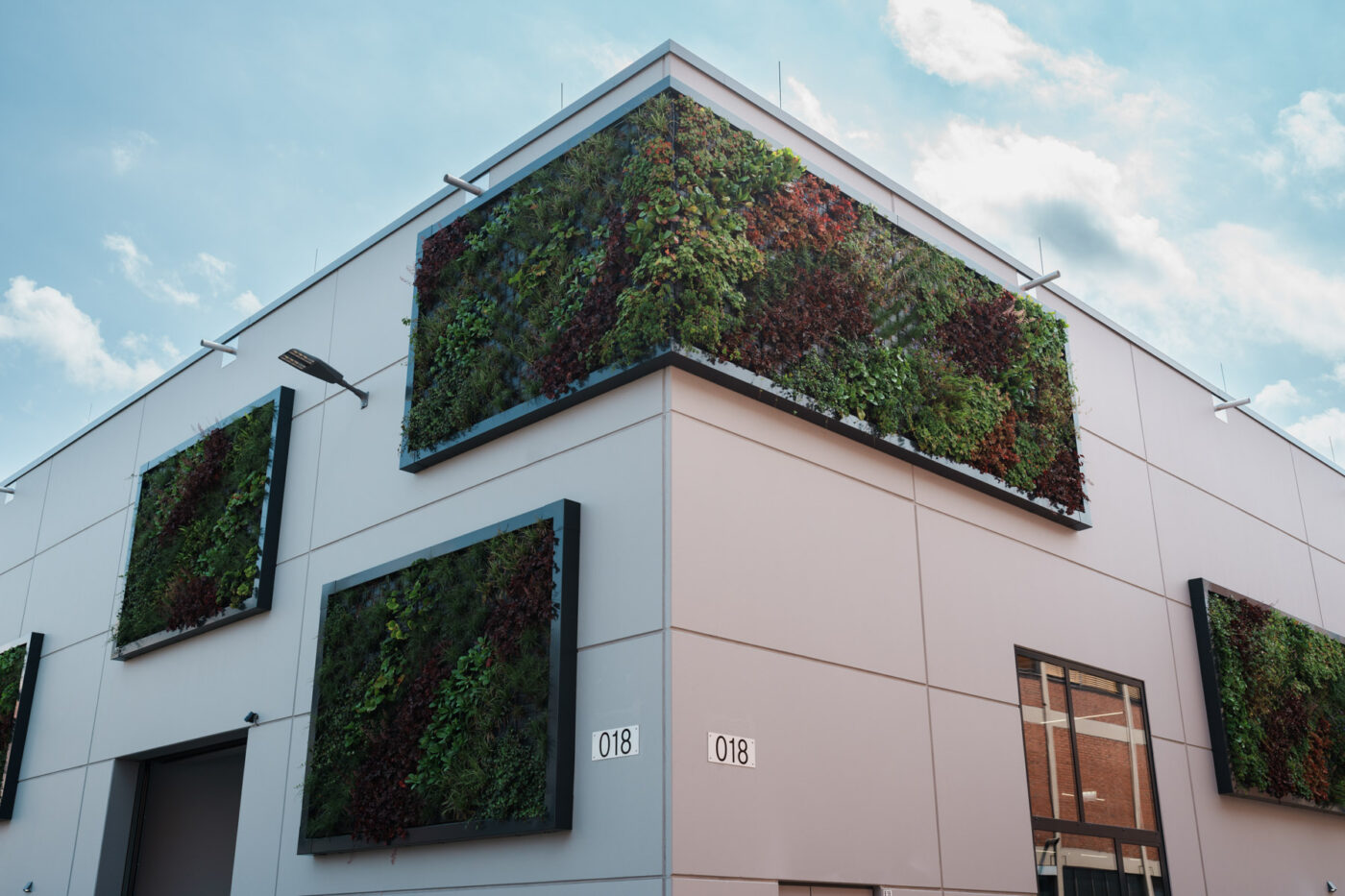
Daimler Truck will not only process supplied pre-products to make battery cells, it also wants to coat the electrodes to gain “extensive knowledge of cell chemistry.” To this end, it will “experiment with different recipes in the production of battery paste.” Both pouch and prismatic cells can be produced from the specially coated electrodes to remain flexible on the one hand and to build up expertise in the manufacturing process and unit scaling on the other.
The required processes will be optimised on the pilot line for battery pack production. The cells (of different designs or cell chemistry) are combined into battery modules, which are then assembled into battery packs that are ultimately installed in the vehicle. Components such as cooling and battery management must also be taken into account.
“The opening of our Battery Technology Center is an important step in terms of electrifying our product portfolio – and yet another milestone in the history of innovation at the Mannheim plant,” says Andreas Gorbach, Member of the Board of Management of Daimler Truck and responsible for Truck Technology. “We have decided to take care of the assembly of the future battery generation ourselves and thus keep important added value in-house. In and for Europe, we will do this at the Mercedes-Benz plant in Mannheim and thereby further strengthen the future of the location.”
Less than a fortnight ago, Daimler Truck opened the ‘Technikum’ development centre for electric motors at the Gaggenau plant. There, too, the manufacturer will develop and build prototypes in order to optimise production processes.
0 Comments