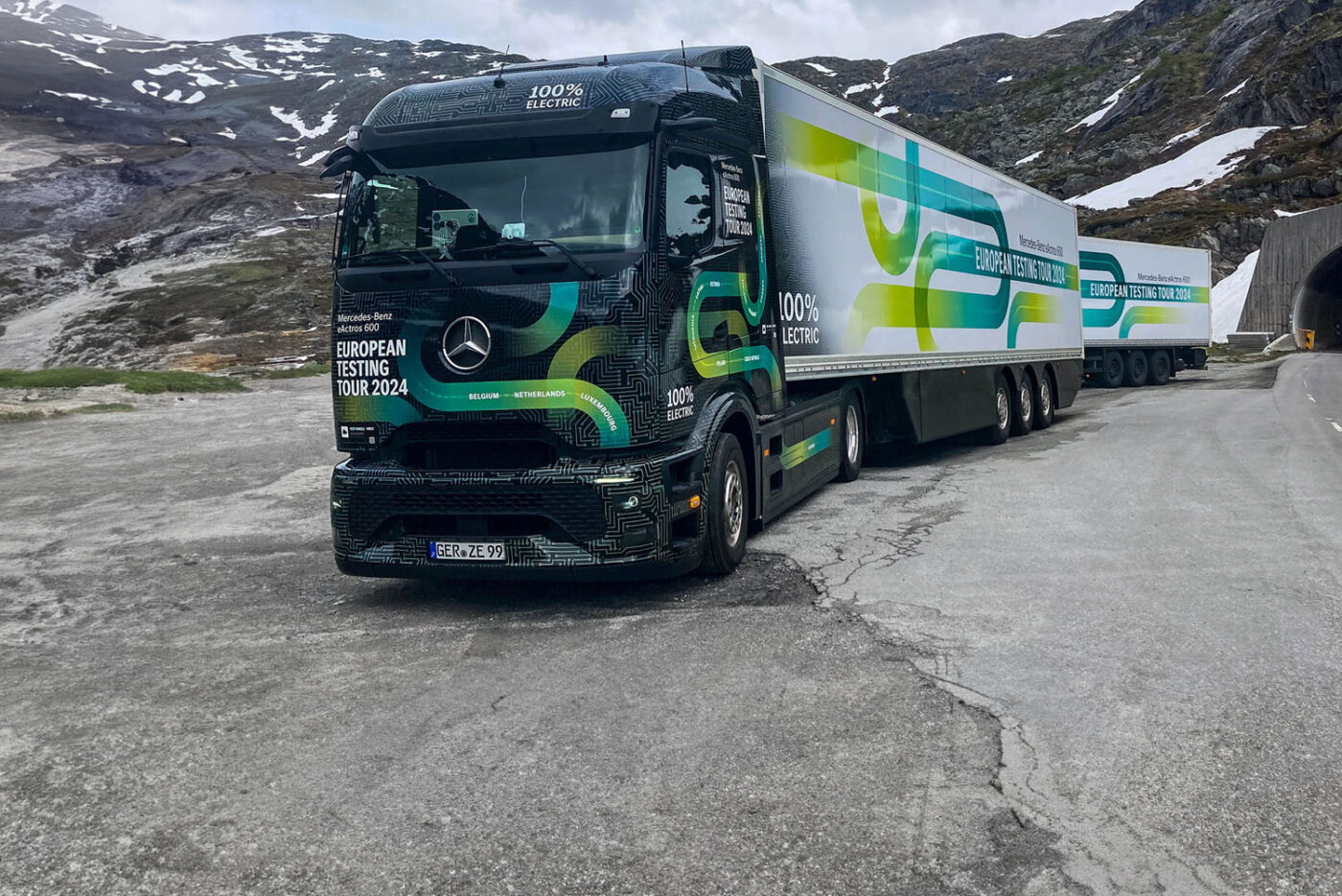
Final test drives with the Mercedes eActros 600 across Norway
Briefly about the tour: In mid-June, two pre-series units of the electric truck set off from Frankfurt am Main on the “eActros 600 European Testing Tour 2024” – initially heading north to the North Cape. From the northernmost point of Europe, they will travel overland to the southernmost point of the continent, to Tarifa in Spain. On the way back from Spain to Frankfurt, the two trucks will take a detour through the Benelux countries. It will take them over 13,000 kilometres through 20 countries – in around five weeks. And only with publicly accessible charging points.
At the beginning of July, the trucks reached the northernmost point of their journey. They had travelled 12 days and 4,436 kilometres – purely electric, of course. We had gotten on board a few days prior. But let’s start at the beginning.
“The vehicle technology for the transformation is ready. Long-distance battery-electric transport in Europe is possible,” said Karin Rådström, CEO of Mercedes-Benz Trucks, at the launch. “Now politicians and the energy sector must work together with the industry to drive the development of public charging infrastructure.” By the way, the CEO personally drove one of the two trucks for the first few metres of the tour.
There was no sign of the splendour or sunshine of the tour’s kick-off in Frankfurt with numerous invited guests when we gots on board a few days later. It was grey and gloomy at the truck park on the EV6 in Biri, not far from Lillehammer. We drove through the drizzle to the two eActros 600s parked there overnight. They had travelled via Hamburg, Fehmarn, Copenhagen and Gothenburg to reach this pitch on the shores of Mjøsa, Norway’s largest lake. From here, they will travel to the fjords on the west coast. 330 kilometres with a challenging topography.
500 kilometres of range – under all conditions?
On paper, it should not be a problem. With three battery packs of 207 kWh each, the eActros 600 is designed for long-distance transport. It would be possible to drive more than 500 kilometres on a single charge when fully loaded – or, to put it in trucker’s terms, you won’t run out of battery within the four-hour driving time. Werner Kempfle set off with a small team and the two pre-series vehicles to test whether this is replicable outside of the laboratory and away from German motorways. Kempfle is a development engineer at Daimler Truck and one of the project managers of the eActros 600. If anyone knows his way around the vehicle, it’s Kempfle.
However, of the two pre-series vehicles that set off from Lillehammer, only one was intended to be driven by media representatives. The second truck was at a slightly different stage of development and can be recognised in the pictures by the aerodynamic hubcaps, for example. Details such as the better-integrated steps at the entrance and the LED headlights are also closer to the version that will go into series production at the end of 2024. Two engineers travelled in the vehicle, closely monitoring consumption and energy flows, recording them with additionally installed sensors – it is still a development drive, not a drive with the final production model.
The vehicle that Rådström drove in Frankfurt and in which we travelledin, is also a unique specimen. A few weeks ago, Daimler engineers used this vehicle to demonstrate the first megawatt charging process with the MCS charging standard. On this journey, we will not use the MCS port installed on the driver’s side; we will only use existing CCS charging points. Incidentally, the fact that the vehicle is still a prototype is not only evident from the foiling: the CCS port is neatly covered with a panel. Under the flap for the MCS connection, there is merely a charging socket – the panel with the status LED is still missing. Function clearly took precedence over design.
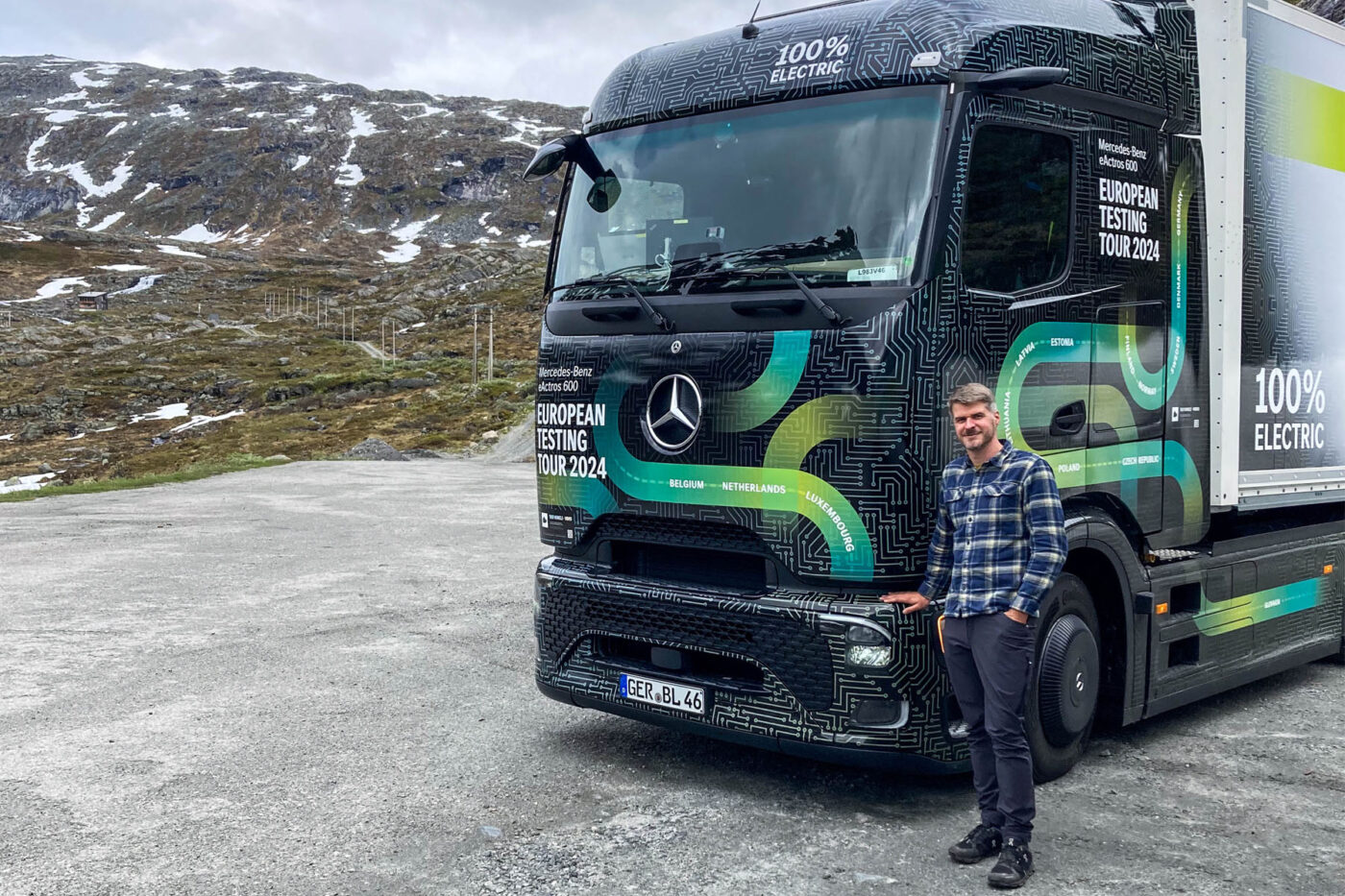
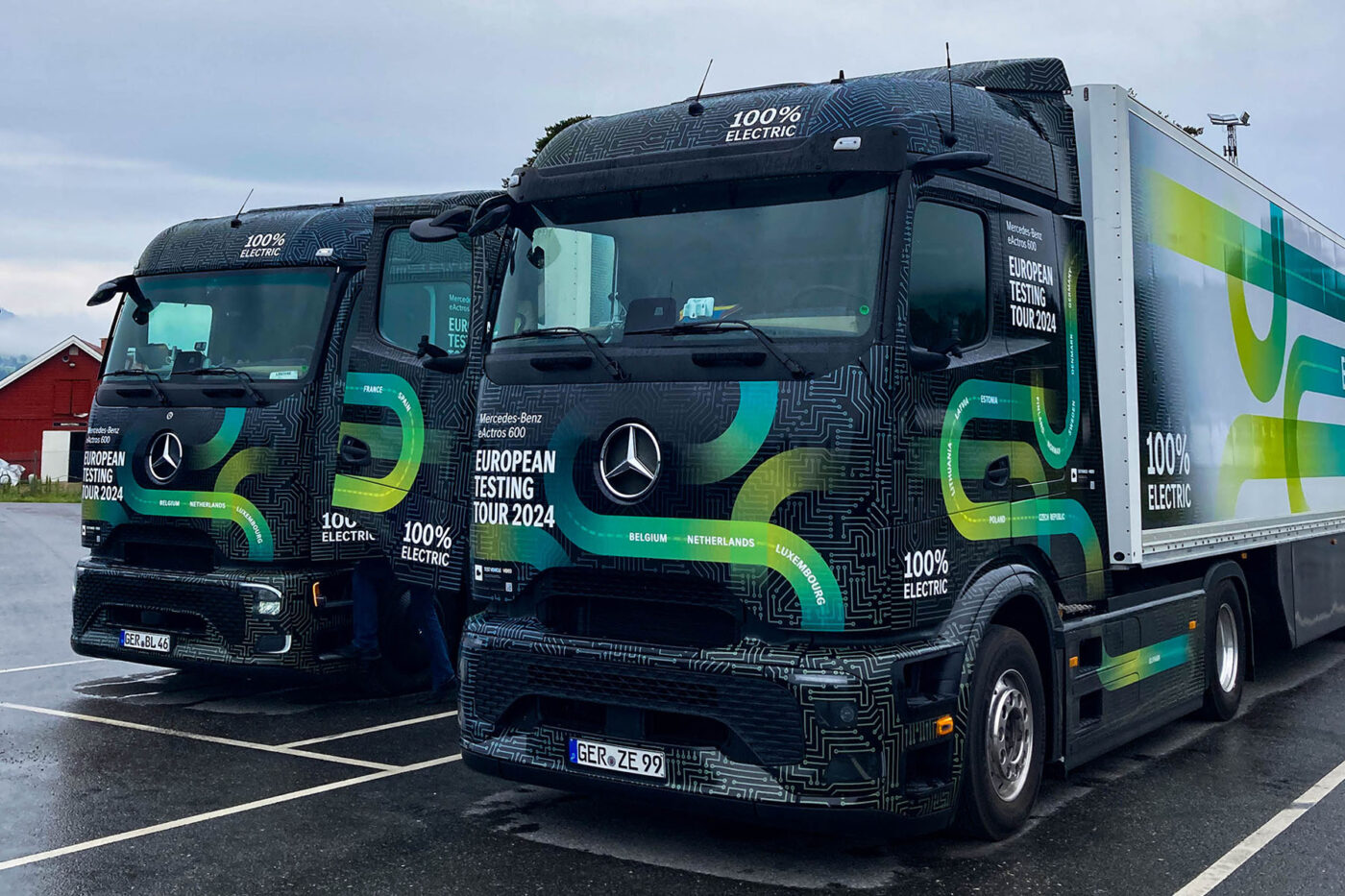
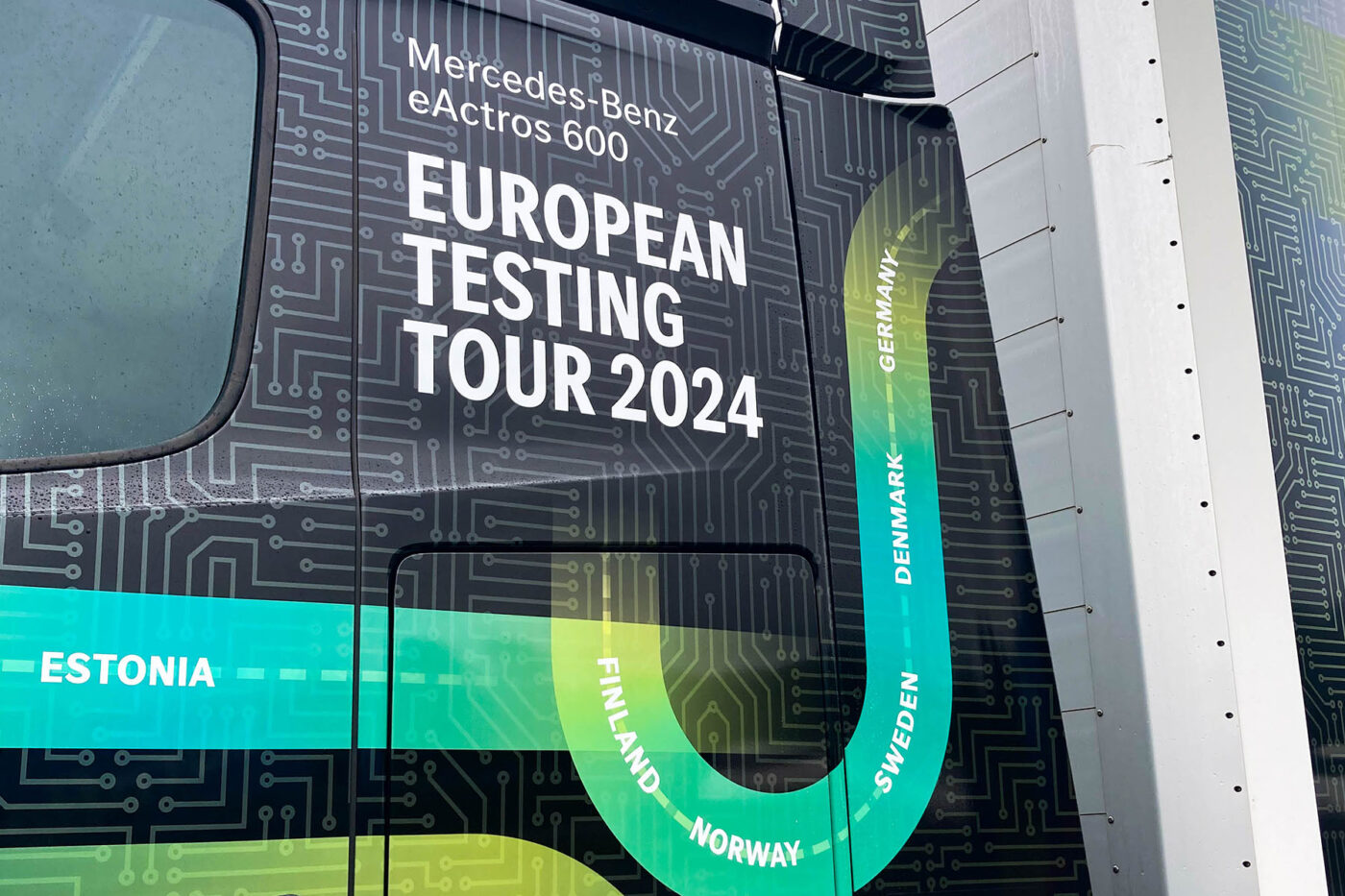
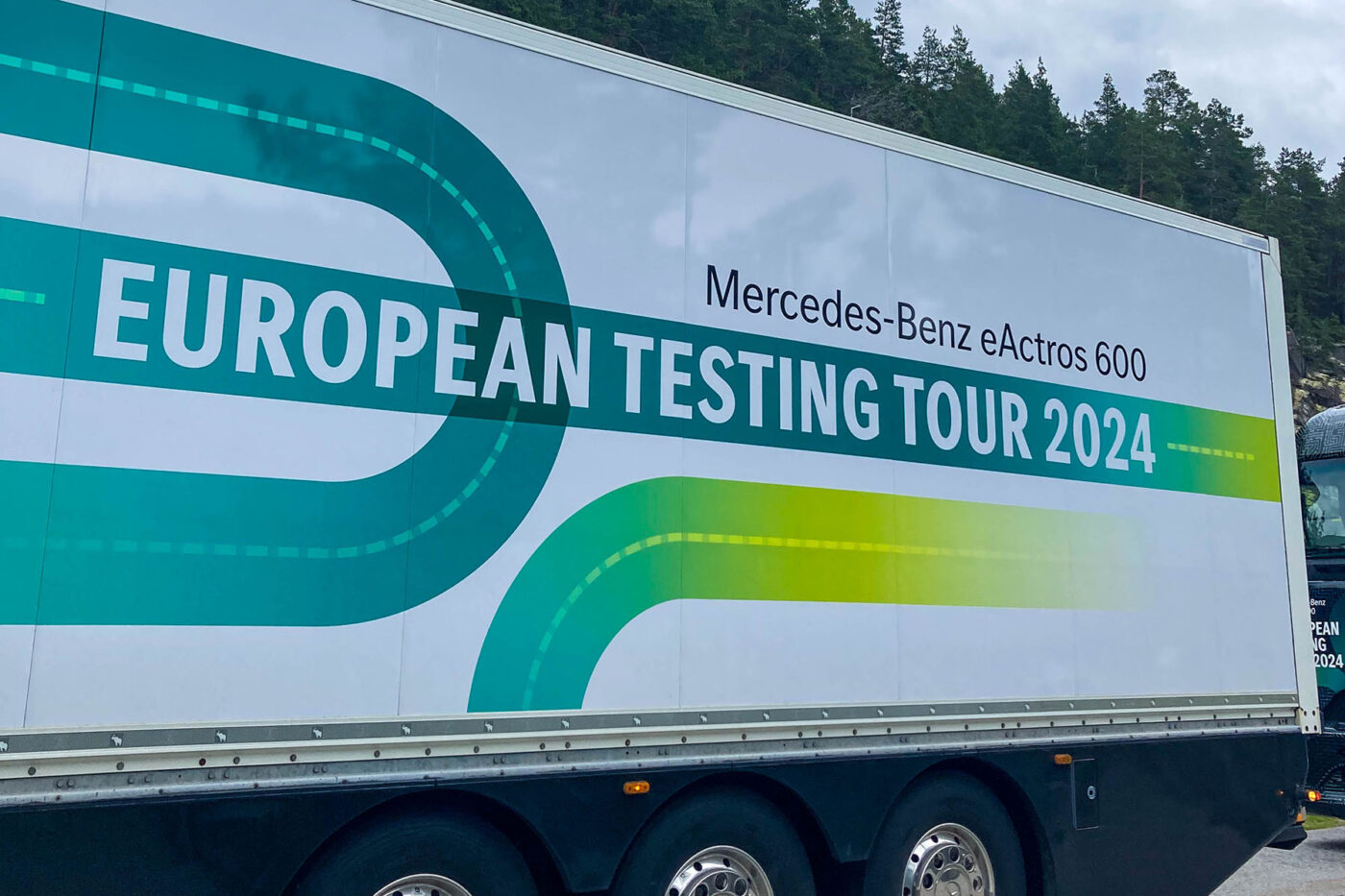

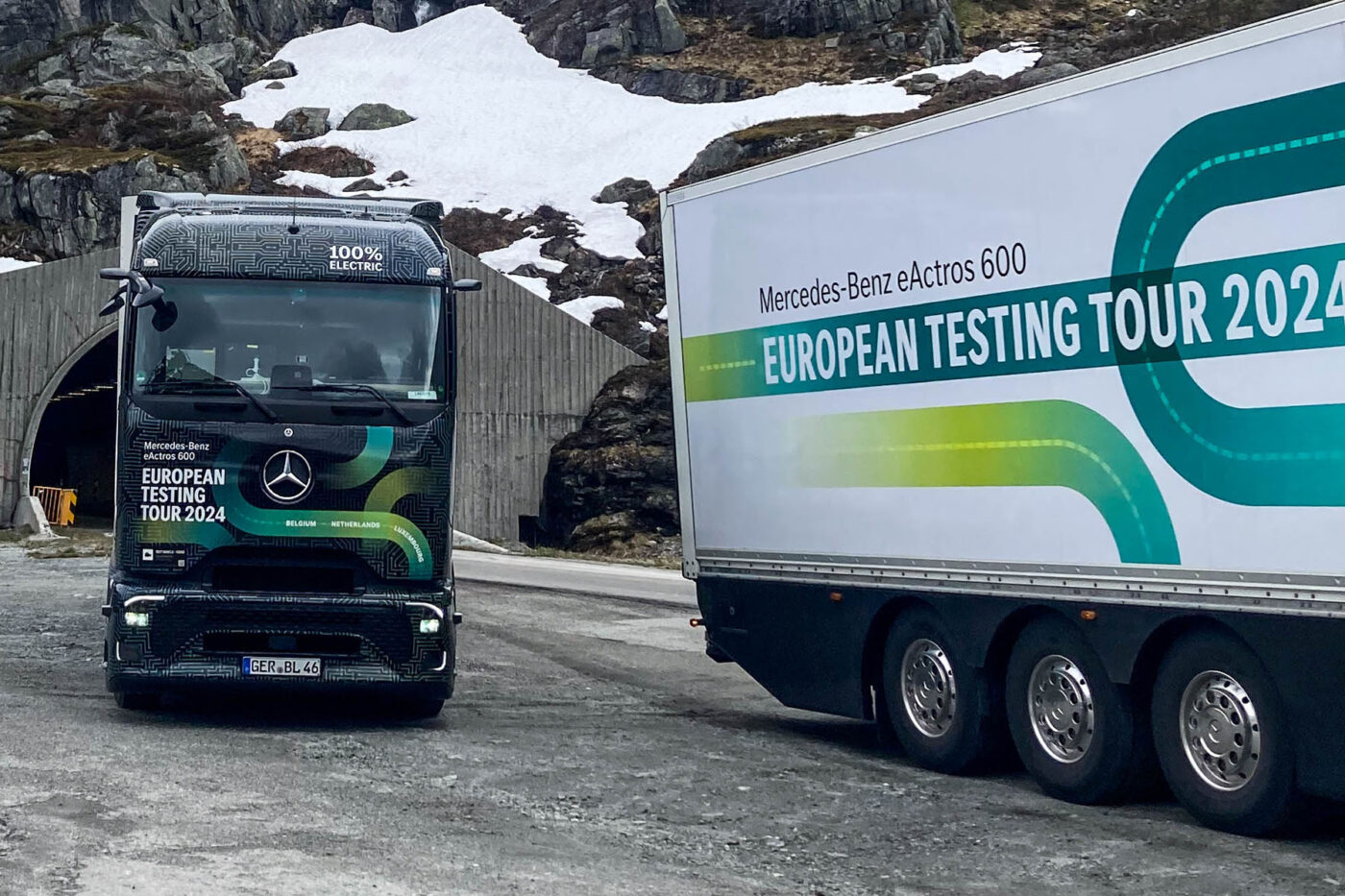
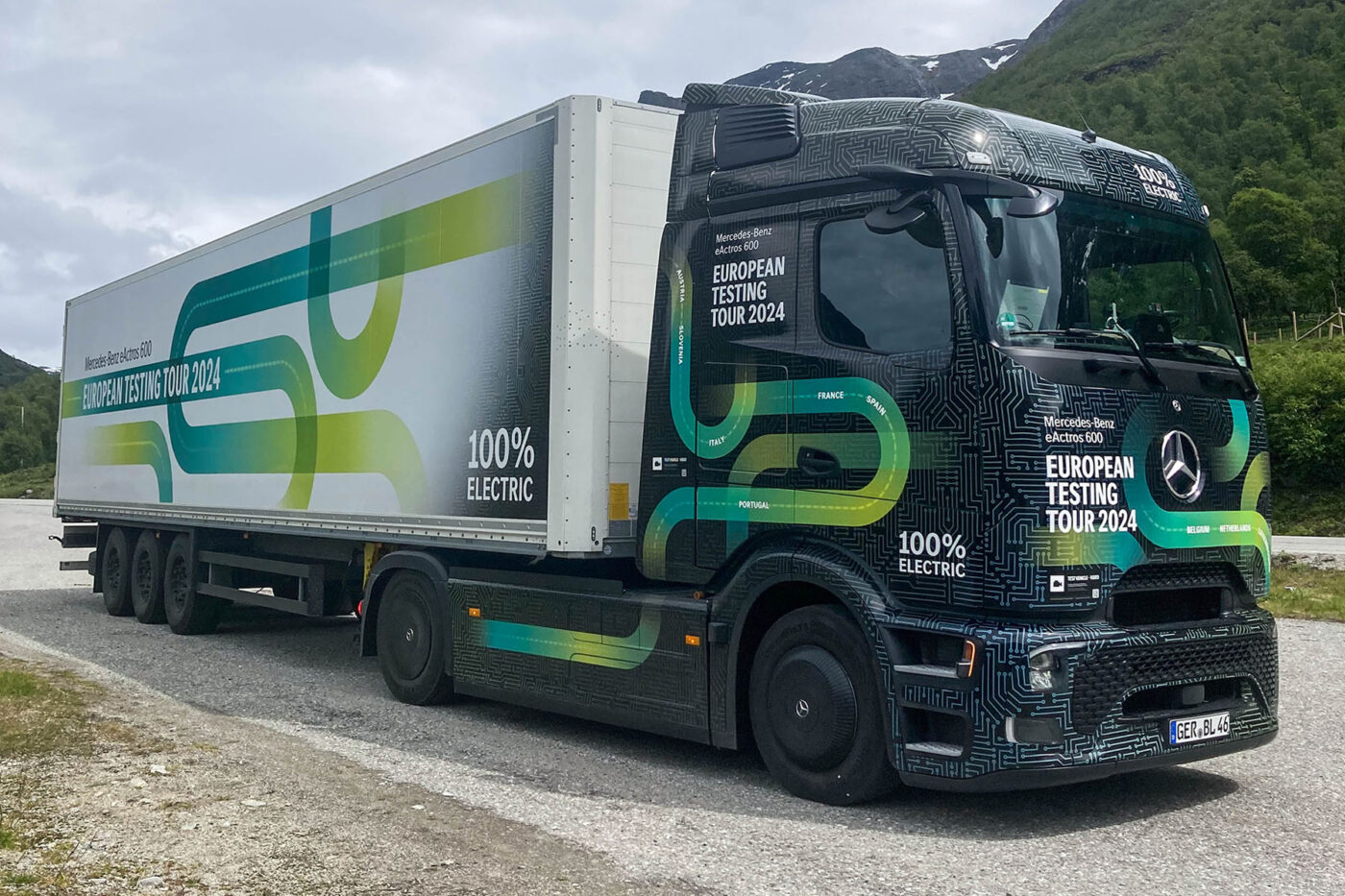

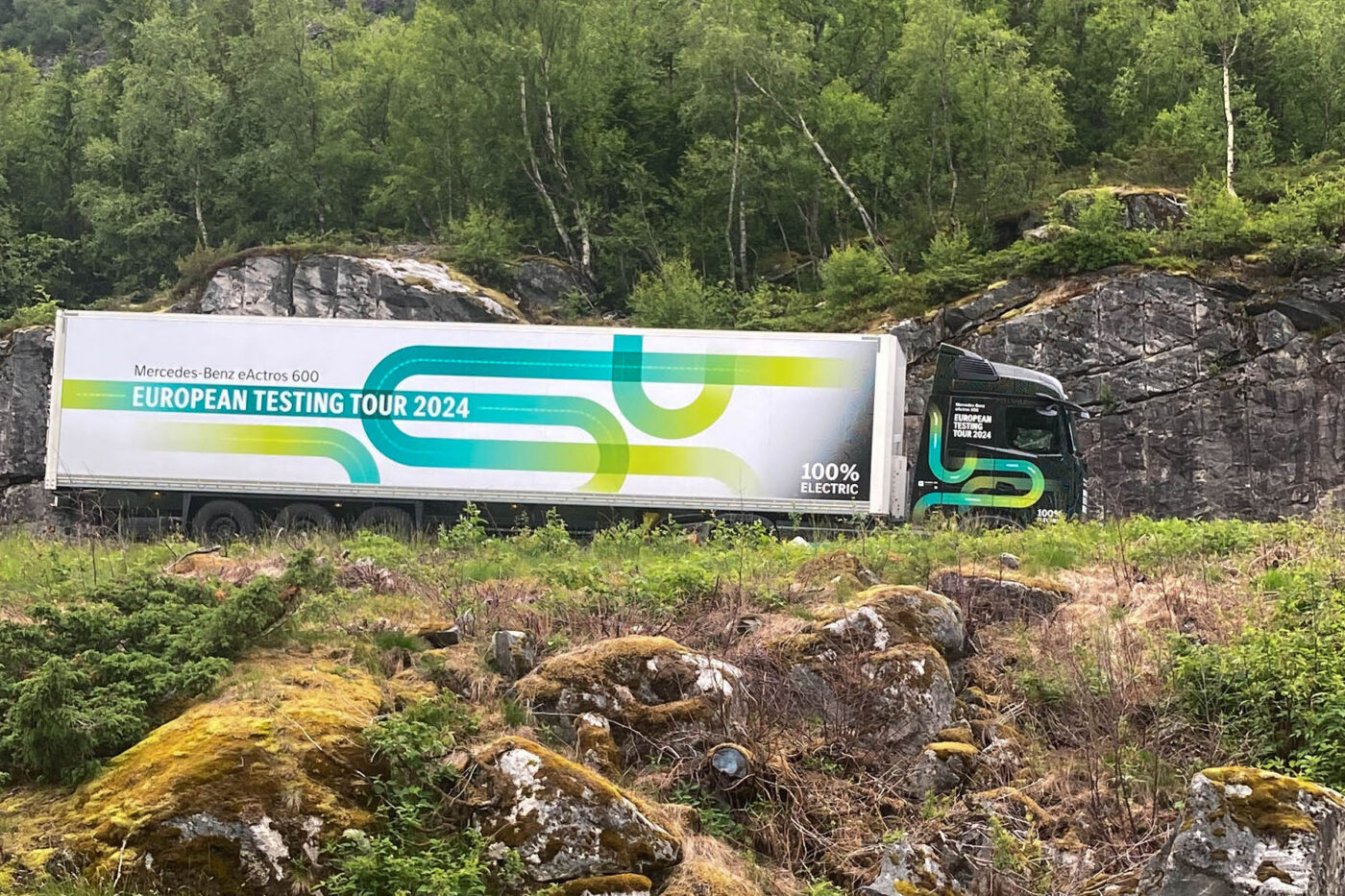
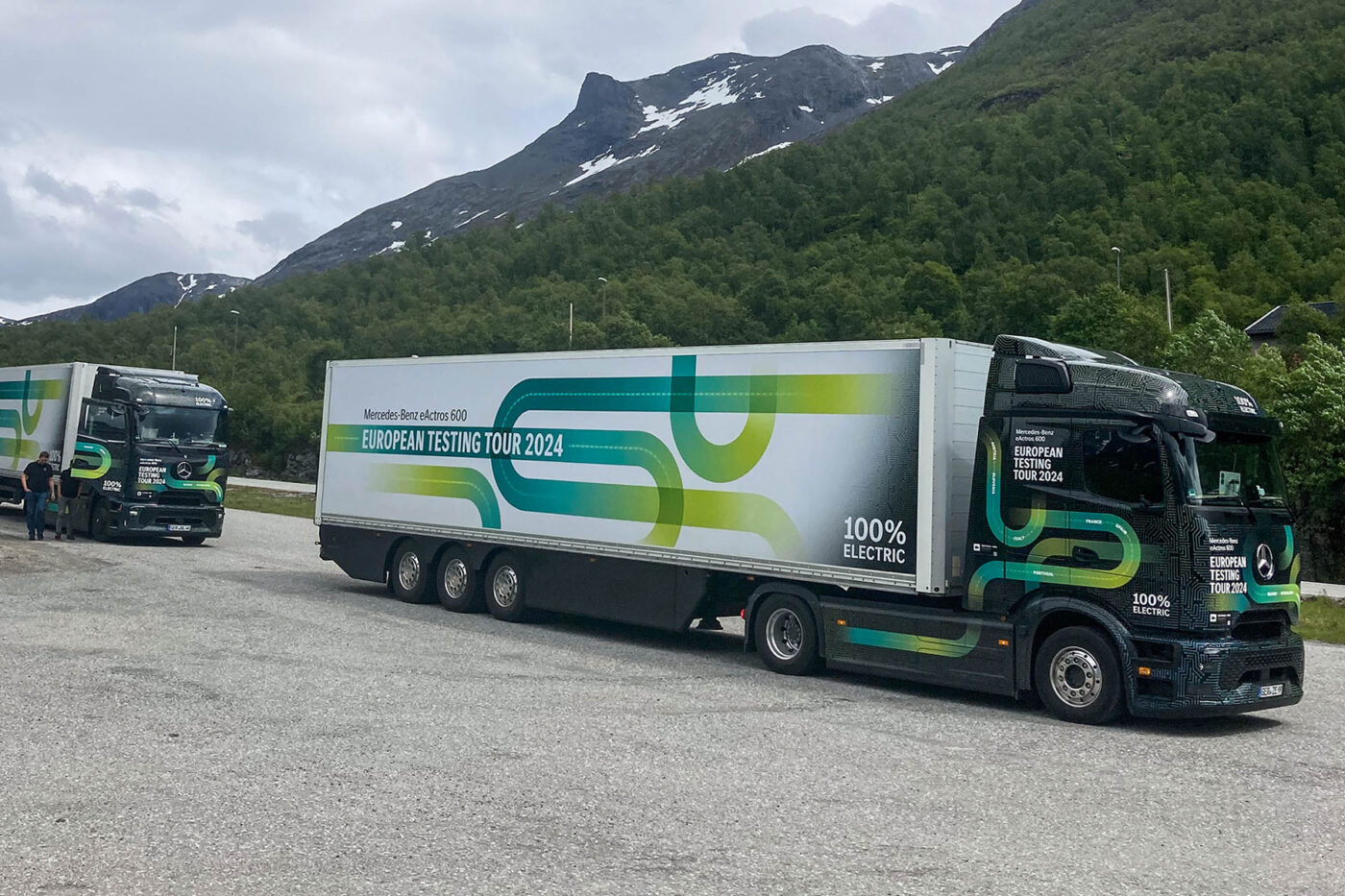
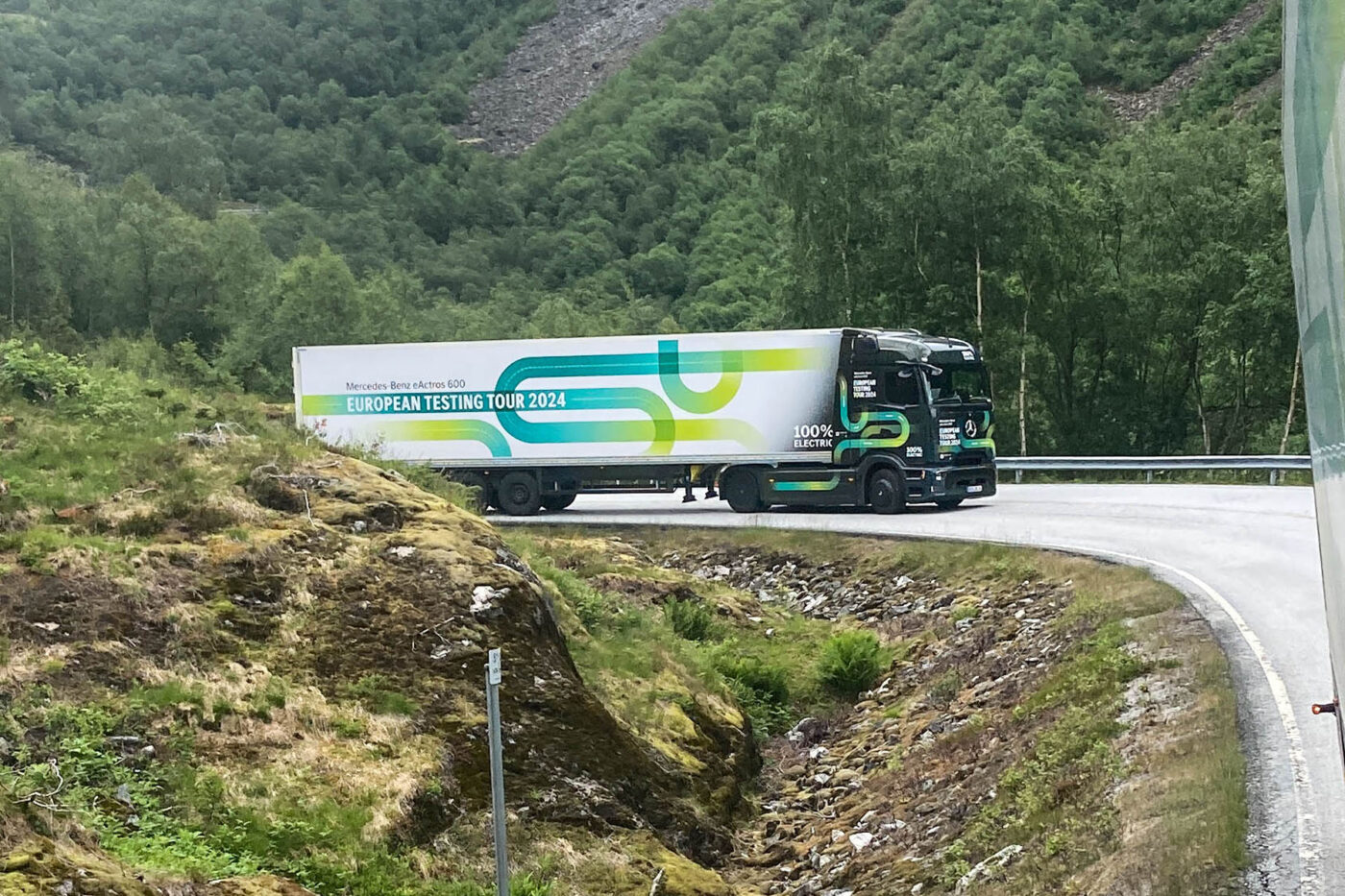
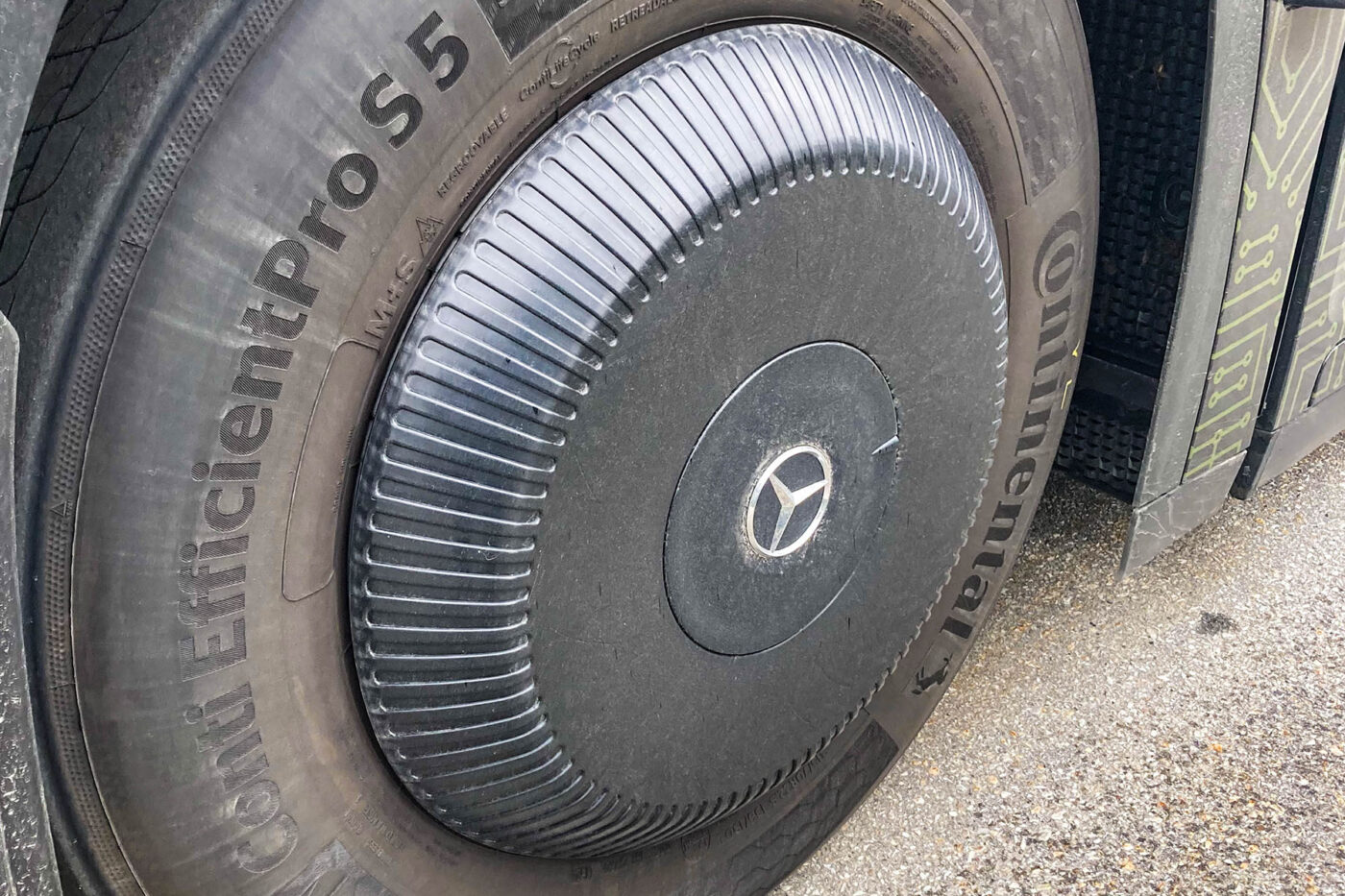
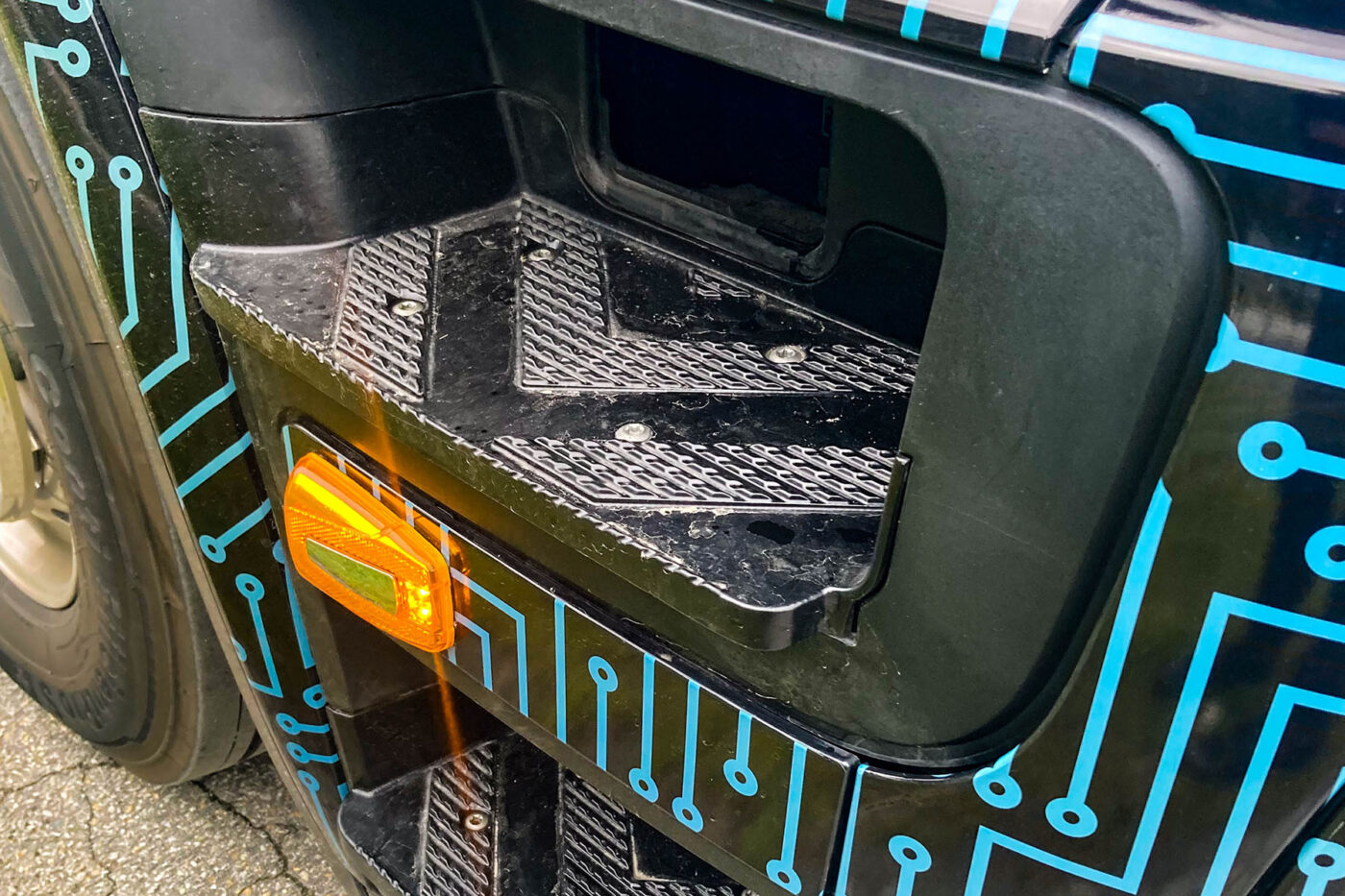
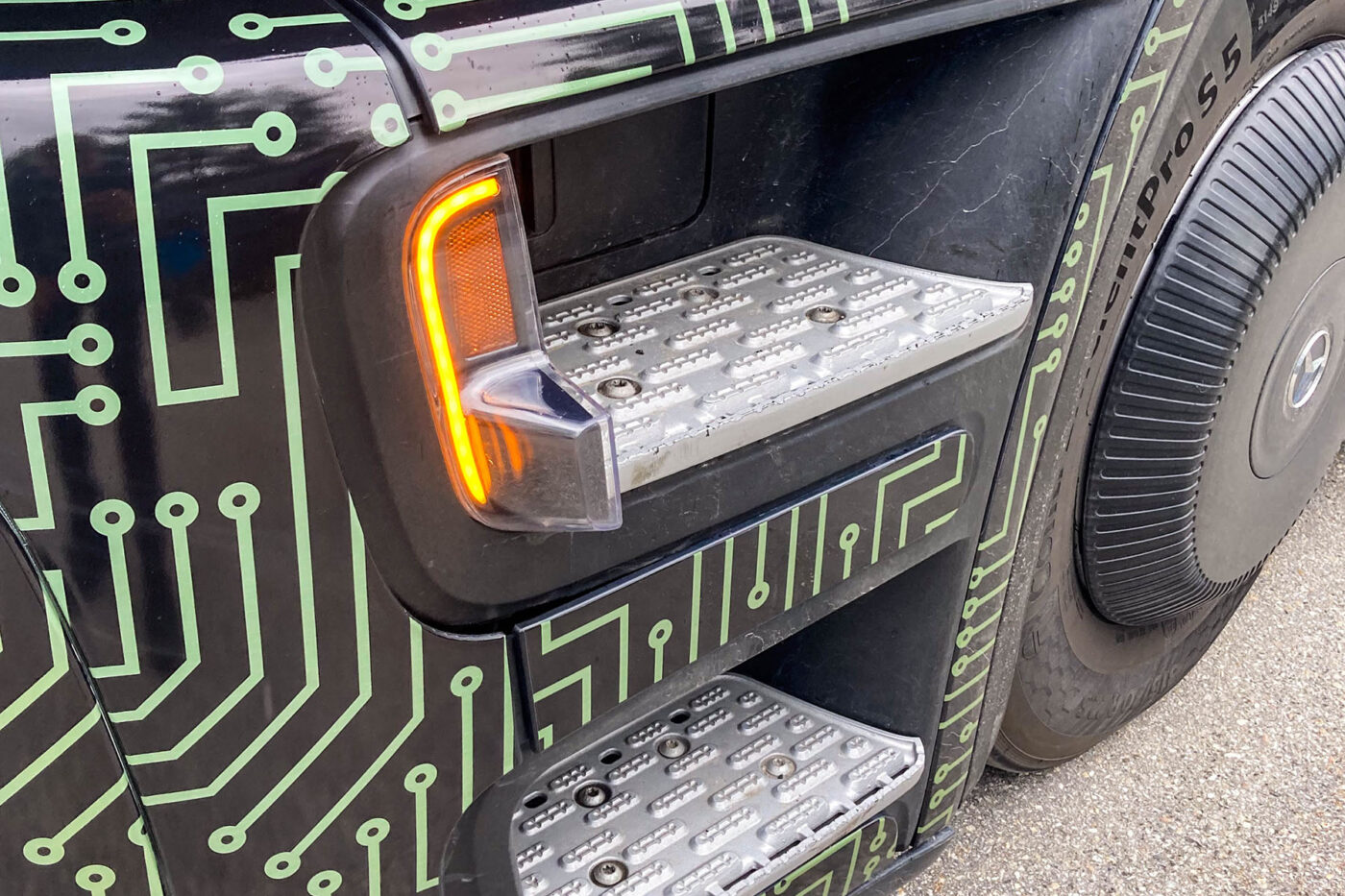
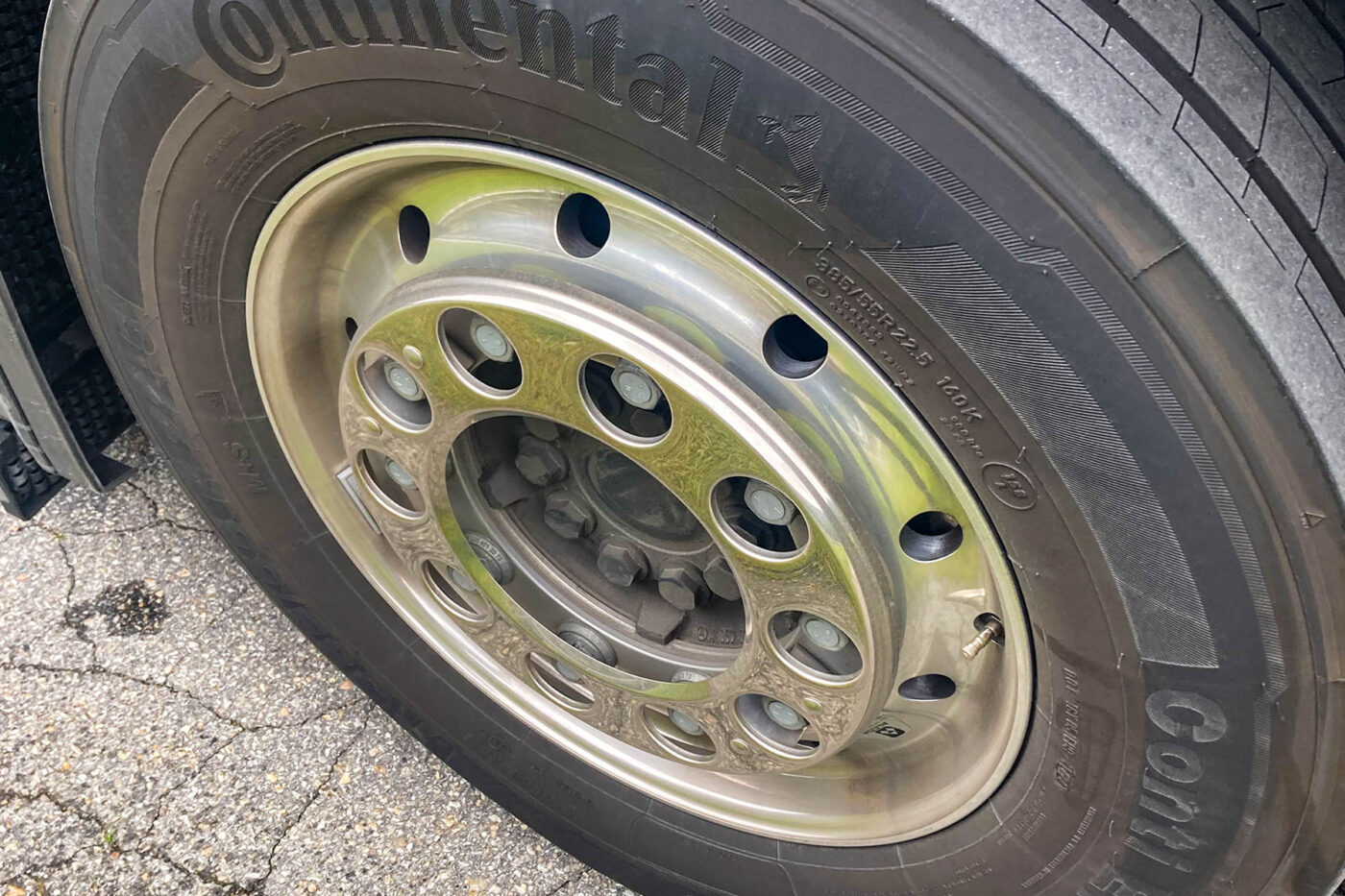
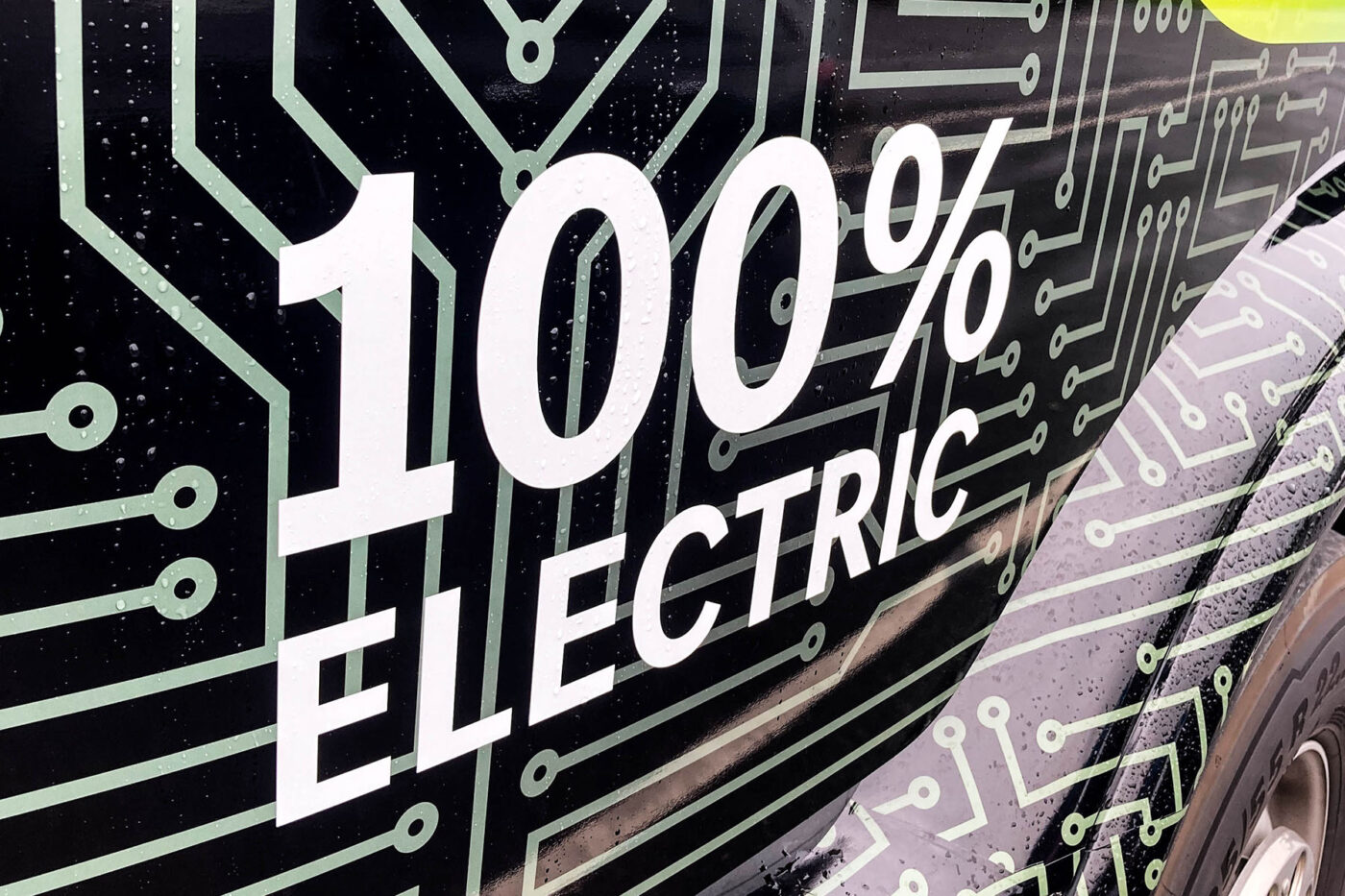
As Kempfle slowly steered the eActros 600 from the car park near Lillehammer and turned onto the E6 heading north, he explained the background of the tour. “Firstly, we want to demonstrate what the product can already do today – across Europe, using only public charging stations in a 40-tonne truck,” said the project manager. “This will clearly show that the vehicles are ready and is now a question of the infrastructure, at least in long-distance transport.” Mercedes-Benz Trucks points out that around 60 per cent of its customers’ long-distance journeys in Europe are shorter than 500 kilometres – which means that the charging infrastructure at the depot and at the loading and unloading points is sufficient for these cases. Only beyond this distance, i.e. in pan-European long-distance transport, are public truck charging stations really necessary.
If you’re wondering what driving an electric truck feels like, it’s like driving an electric car on a train. It’s incredible how the 40-tonne combination accelerates. It reaches 80 kph effortlessly, without shifting jerks, vibrations or a revving diesel engine – quiet, powerful, and impressive pulling power. With air-sprung seats and chassis, the driving experience in the cab is clearly decoupled from the road, especially in the tall, long-distance truck – almost like being on a train. I could only tell that Kempfle had the eActos 600 rolling by looking out the window. You couldn’t feel anything. Of course, not all bumps can be absorbed at cruising speed. But it is always comfortable.
Drivers don’t have to get used to a system
Electric-specific elements such as recuperation were also designed in such a way that drivers do not have to get used to them. When the driver released the electric pedal, the vehicle did not recuperate but accelerated as efficiently as possible. When the driver pressed the brake pedal, the vehicle first decelerated electrically before braking mechanically. Manual recuperation is also possible. Similar to the retarder on the diesel truck, the driver can decelerate in five stages using a lever. At the most powerful level, something like one-pedal driving would even be possible – however, in an electric truck, maximum efficiency should rather be achieved by coasting. And the cruise control with terrain and route recognition usually regulates the speed itself anyway.
Kempfle also told us about his visits to customers. The engineer has been working with electric trucks for five years. He also drives electric vehicles privately and is very familiar with the advantages and prejudices of electric mobility. “When I visited customers with an electric truck, drivers in particular were sceptical, they wanted to stick with their usual diesel,” Kempfle said. “After just one day, they were convinced and told their boss that they didn’t want to drive anything else. In one case, the driver was surrounded by colleagues who wanted to find out more. Although still sceptical himself beforehand, he defended the electric truck!”
To limit range anxiety that drivers, distribution employees and even the owners themselves are familiar with from EVs, Kempfle’s team decided to not only show the charge level and remaining range on the display. The on-board computer can also calculate the remaining journey time. On departure with 99 per cent of the battery, it was 510 kilometres or 6:53 hours – more than a driver can cover in one shift.
Where can the electric truck charge?
The sticking point remains charging. If the depot has its own charging station and, in the case of the eActros 600, the route is shorter than 500 kilometres, it can be used without any major problems – provided the costs are feasible. The importance of depot charging for manufacturers was demonstrated last week. That’s when Daimler Truck and Traton brand Scania unveiled their own subsidiaries to help customers build and operate truck charging infrastructure with a complete offering. In the case of Daimler Truck, the provider is called TruckCharge, while Scania has named its new subsidiary Erinion.
When the first eActos 600 are delivered, the vehicle (unlike our pre-series model in Norway) will only allow CCS charging with a maximum of 400 kW. Customers can only order pre-equipment for the MCS. As soon as the MCS technology is available and standardised across manufacturers, it will be possible to retrofit it to these models of the eActros 600 – the MCS is still being officially developed. Therefore, the approximately 30-minute charging time for 20 to 80 per cent SoC is based on an internal simulation.
However, Kemfple was convinced that many customers will not need MCS charging at all. Even with 400 kW at a corresponding CCS charging point, it is possible to recharge enough electricity during the 45-minute mandatory driving break so that the battery cannot be driven empty in the next four-hour driving slot.
Anyone who tends to concern himself more with passenger cars and fears for the battery’s durability when charging with 400 kW or more – like me – will have to get used to the size of truck batteries. Even 400 kW corresponds to a C-rate of 0.64 with the 621 kWh installed in the eActros 600. 400 kW thus only stresses the battery as little as when a Tesla Model Y Long Range is charged with 50 kW – where a peak of just over 250 kW is possible. Even with the initially planned MCS charging capacities, the battery is not subjected to a particularly high load. Daimler Truck assumes the battery will survive the entire truck service life of 1.2 million kilometres. As is known, it uses LFP cells from CATL. Incidentally, Daimler Truck did not choose the lithium iron phosphate battery because of its lower costs but primarily because of its durability.
While I talked to Kempfle, the journey was mainly uphill. When we stopped at a rest area after around 2.5 hours, the battery was still at 65 per cent SoC. Although we had only covered just under 160 kilometres, the displayed range has dropped by a whopping 200 kilometres – as things stood then, we would have still had 310 kilometres to go – or 5:06 hours of driving time. The consumption according to the on-board computer: 124.0 kWh/100 kilometres. After all, we needed power to move those 40 tonnes uphill.
Driver change after 160 kilometres
Christian Österle took over the wheel from project manager Kempfle at the rest area. Österle is an engineer for the software and function development of thermal management, a feature that should not be underestimated in an electric truck. After all, LFP cells are notorious for not performing so well at low temperatures, at least in electric cars – especially at the charging station.
Österle can disprove this for trucks. “The battery weighs around 4.5 tonnes, which is an enormous thermal mass,” the engineer explained. “Even if the vehicle is parked overnight at temperatures below freezing, once the battery has reached its temperature, it doesn’t cool down so quickly.” If it does cool down, for example, after a Sunday without driving, an electric heater with 12 kW of power can bring it back to temperature. Incidentally, the optimum range is around 20 degrees, even if individual cells can reach 45 degrees during fast charging.
However, switching on the electric battery heater may not even be necessary. That is because it is rare for an electric truck to be parked with an almost empty battery and driven a short distance to the charging station with a cold battery. It is more common for the battery to be charged after arriving at the depot – either for a quick onward journey with a different driver or slowly overnight. Either way, the battery is full and warm on departure. And even if the battery needs to be warmed up during the journey, the eActros 600 can fall back on other heat sources in the vehicle before electricity from the battery is used for heating.
The eActros 600 does not have a heat pump
Incidentally, the long-distance truck does not have a heat pump, which is fitted as standard in many electric cars. “It doesn’t offer any advantages on long-distance journeys, but it does in distribution transport with the eActros 300/400,” Österle explained. In long-distance transport, the eActros 600 is ideally on the road for four hours at a time at a constant speed – a completely different scenario to distribution transport, where several customers may be served on one tour and the vehicle’s energy consumption in urban stop-and-go traffic differs.
During the test drives with the eActros 300, engineers found that one component, in particular, generates enough heat: the electric axle with the two electric motors. The heat would actually be discharged via the cooling system. However, with additional valves and an adapted control system, Österle and his colleagues connected the various cooling circuits in such a way that the heat from the electric axle could still be utilised – for example to control the temperature of the battery.
Or even in the interior. On our test drive across Norway, we arrived in the mountains; the E15 leads north of the Jostedalsbreen Nasjonalpark through valleys and tunnels towards the fjords. There was still snow next to the road in some places. Nevertheless, at no time did we use electricity from the battery to heat the interior – we had set the air conditioning to 21 degrees. During the stopover, Österle connected a laptop to the vehicle and called up the live data from the cooling circuits. The approx. 50 degrees of the drive cooling circuit were more than enough to keep the battery and cabin warm. The heating didn’t kick in once.
Consumption of just over 100 kWh/100km
That remained the case until we reached Stryn, our destination on the Innvikfjorden. A glance at the on-board computer showed that after 329 kilometres and 5:44 hours of driving, there is still 38 per cent left in the battery – enough for 220 kilometres or another 3:50 hours on the road. Theoretically, 550 kilometres would have been possible given the not-exactly-flat topography. Daimler Truck itself only speaks of a range of 500 kilometres, which was determined internally “under specific test conditions, after preconditioning with a 4×2 tractor unit with a gross combination weight of 40 tonnes at an outside temperature of 20°C in long-distance transport operations.”
As the second part of the stage was downhill again to sea level, the average consumption was 106 kWh/100 km. If you consider that an electric car with two tonnes would probably also have needed 15-20 kWh/100km, consumption in the lower three-digit range for the 40-tonne vehicle suddenly seems very efficient. On the downhill sections, consumption fell to as low as 84 kWh/100 km in some cases. On the steepest sections, the eActros 600 recuperated up to 480 kW – even up to 600 kW would be possible.
Even for journeys of around 300 kilometres like ours, Kempfle considers the larger battery of the eActros 600 to be useful and helpful: If a logistics company uses the electric truck for 300 kilometres each in the day and night shift, a vehicle with a real range of just over 300 kilometres would also be sufficient. But: “Then everything has to fit. A traffic jam or a diversion on the route can disrupt the entire schedule,” said the project manager, recounting a customer visit. “There was a technical problem with the trailer that cost us two hours during the night. So we were back at the depot later for charging and the vehicle could only start the day shift with a delay – because it needed every percentage point of charge.” The eActros 600, on the other hand, would have offered a buffer of 200 kilometres.
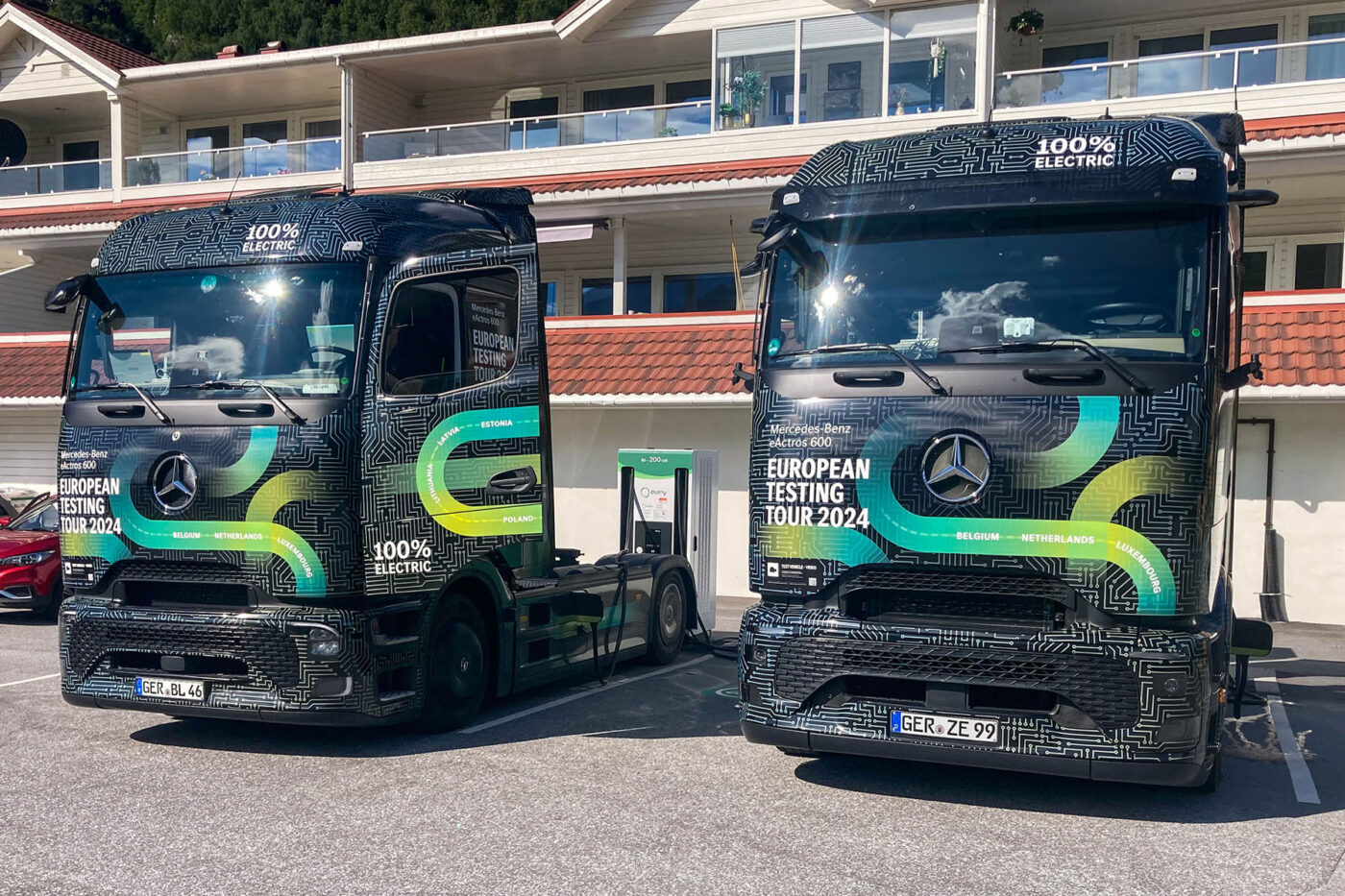
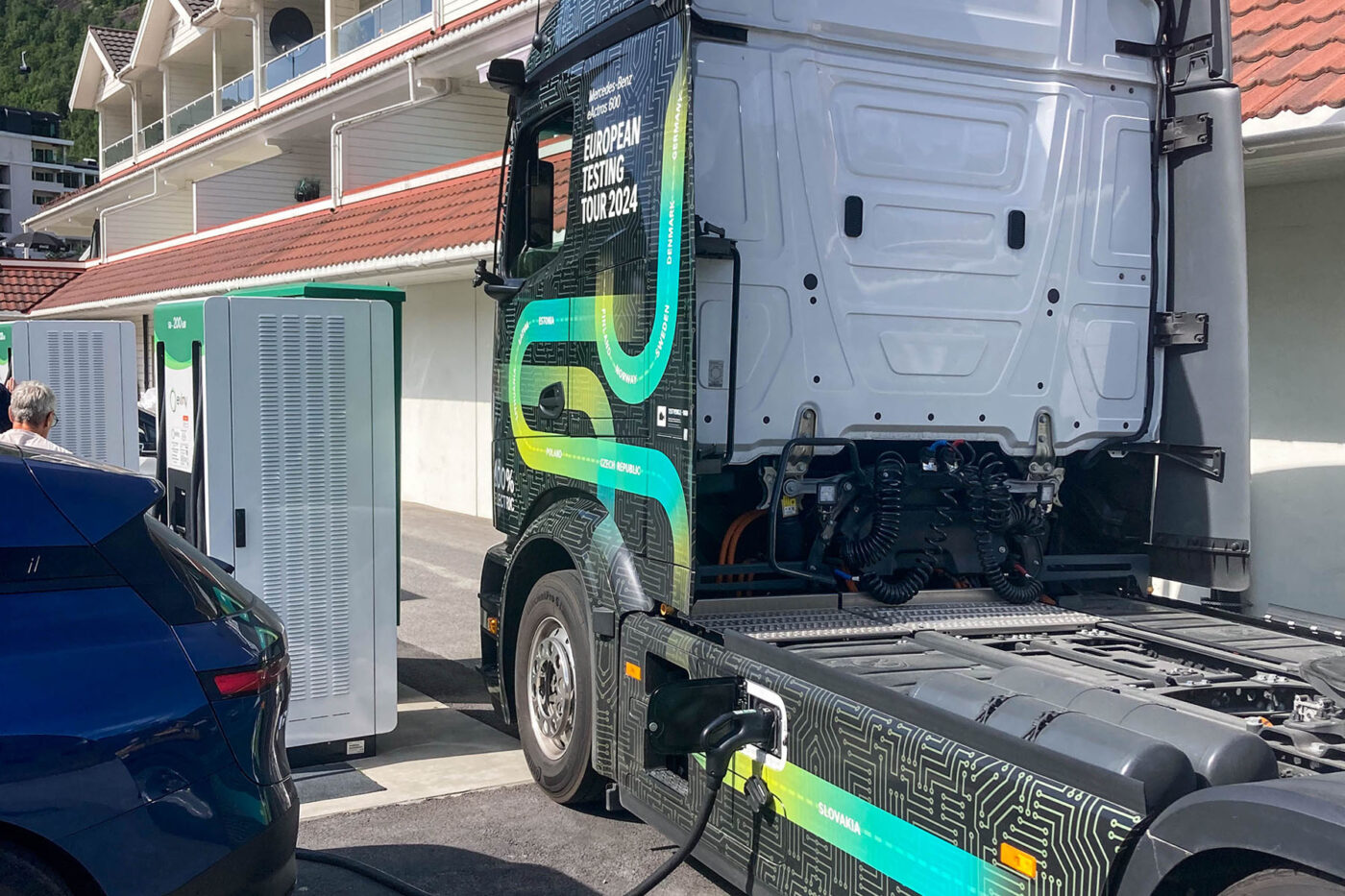

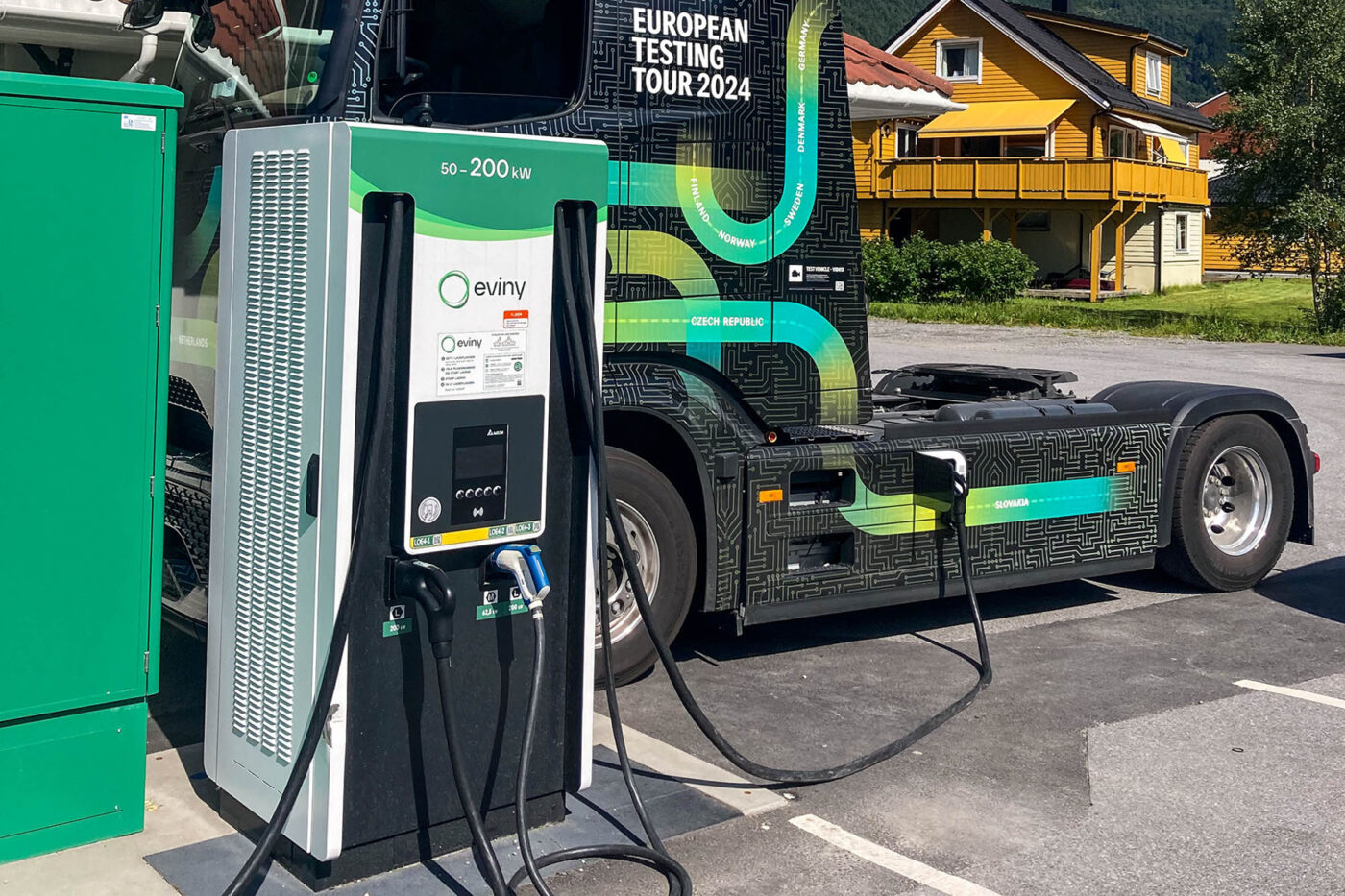
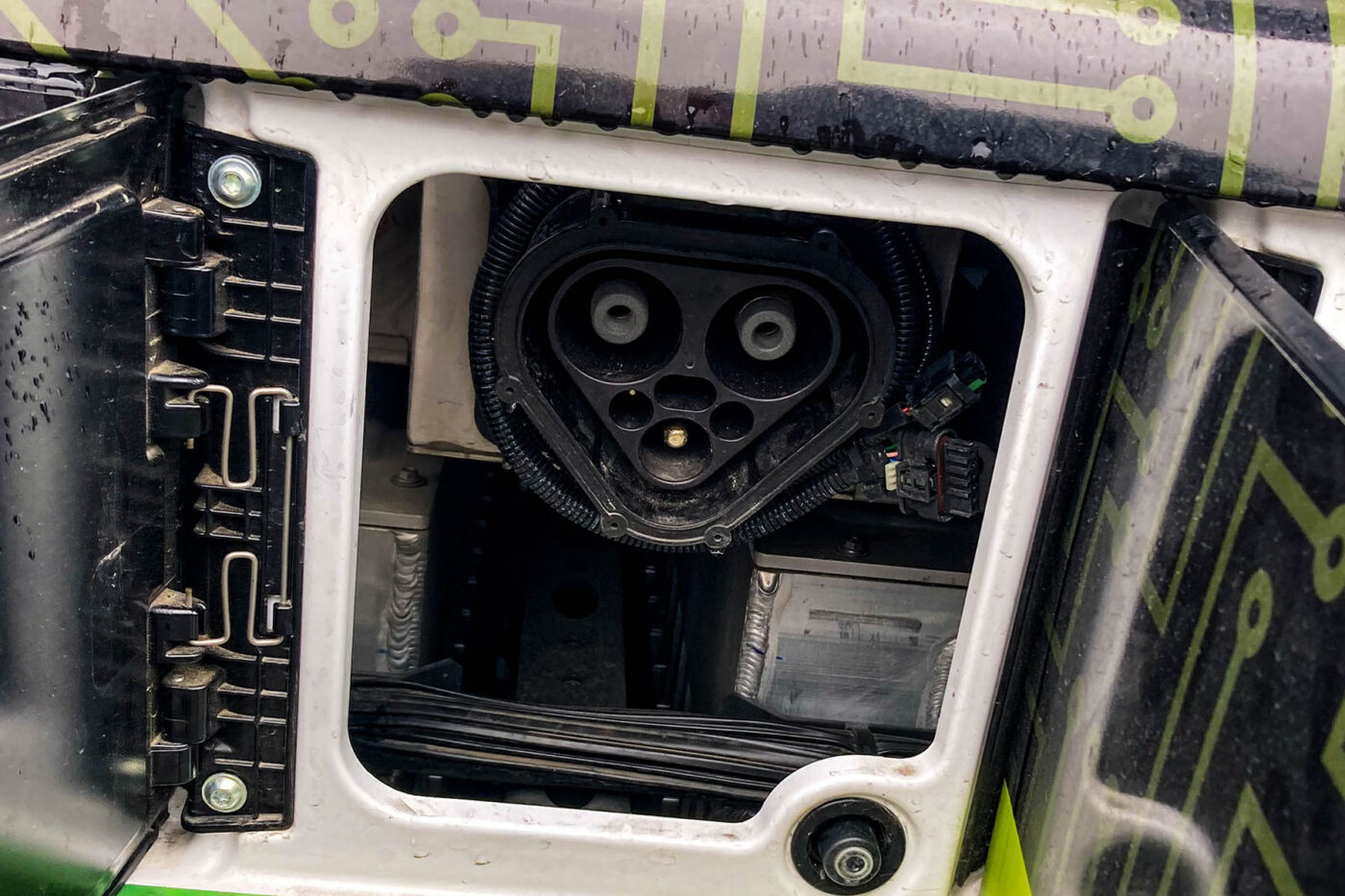
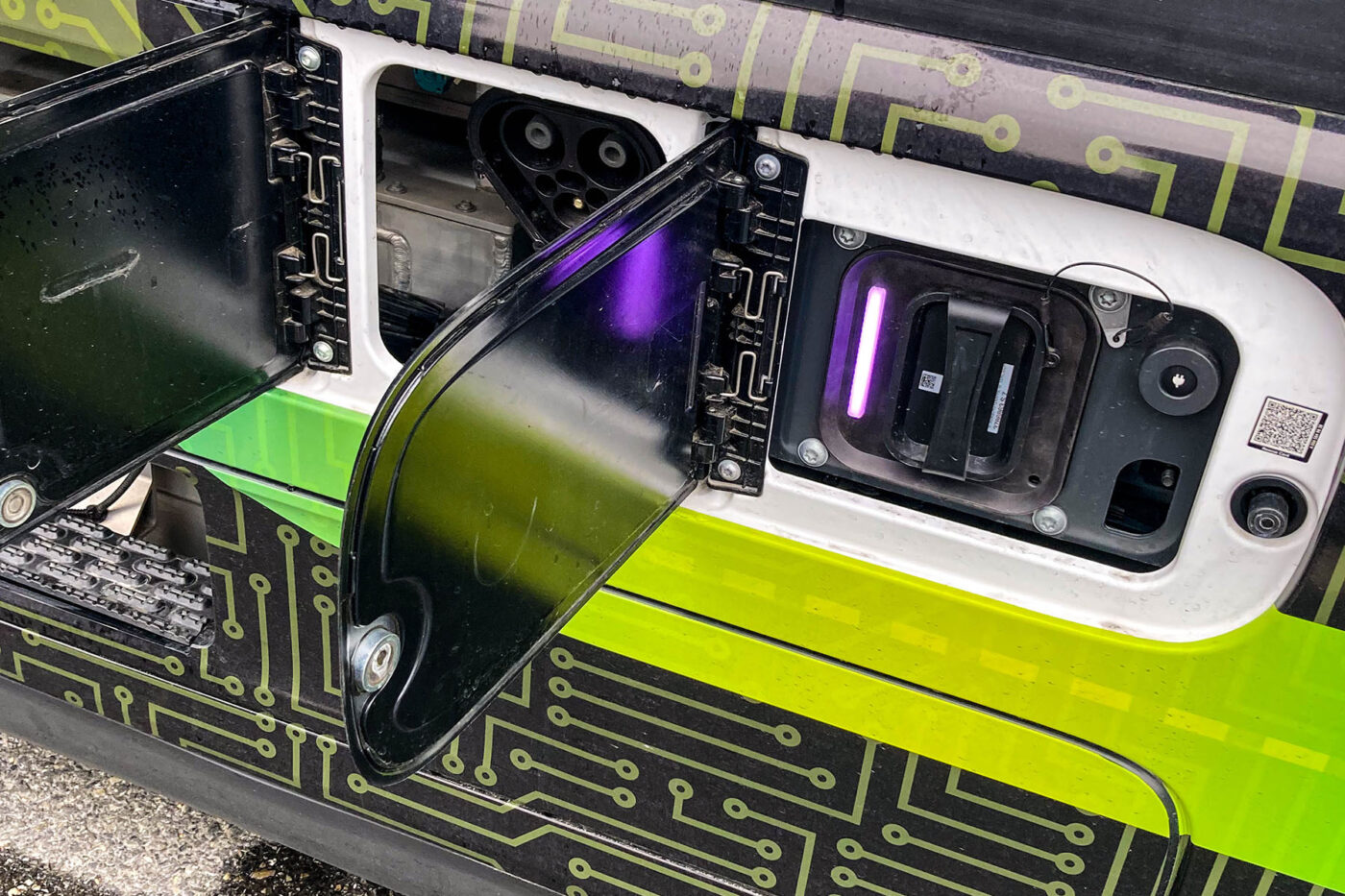
Although not yet completely empty, we headed to the charging station. So far, it had been possible to charge the trucks at all the stations on the tour without any problems – with a little planning, the infrastructure is well enough developed for electric trucks. The situation is different in Stryn and the nearby village of Loen, which are more geared towards tourism than long-distance transport. There are only two EV charging stations, UFC200 from Delta Electronics, to be precise. 200 kW per charging point is possible; if both CCS connections are used, the power is shared. Sufficient for cars but not enough for electric trucks. And the engineers first have to unhitch and secure the trailers at a nearby car park. The parking spaces at the charging station are not designed for 16.88 metre-long trailers. Even with just the eActros 600, it was tight.
“The test drive will show what’s possible today – and that’s mostly CCS charging stations,” says Kempfle, who came up with the whole tour – and had to convince CEO Karin Rådström of his plan. “We weren’t interested in getting from A to B as quickly as possible with megawatt charging. It was about experiencing and solving precisely the challenges that our customers face. And that sometimes means unsaddling and manoeuvring.” And unlike many planned PR tours, there is no backup here. The two vehicles are prototypes and are only accompanied by a van with the organisation team. There is no workshop truck and no spare parts. If something breaks down, they have to improvise – or the tour stops.
In Loen, the two large electric trucks were met with great interest at the charging station. The Daimler engineers were not only approached by EV drivers who were charging their cars. Passers-by also asked for photos, and according to Kemfple, even the police wanted to take a snapshot of their patrol car and the two charging trucks at an earlier stop. A local haulier even came to Loen – although it was Saturday afternoon at 5.30 p.m., he had heard about the two prototypes in the neighbouring village and had to stop by for a chat.
A small “problem” just before the end
The drive itself was surprisingly calm. Although still a pre-production model, the eActros 600 is already very mature. When it came to charging, however, it became clear that this was a test and development drive. The charging process didn’t start immediately, and it took three attempts to find a suitable charging card or app to activate the charging station in Loen. The cable had to be plugged in and unplugged several times before the charging process started. Although the current flowed at 200 kW, the status LED on the charging port did not flash green. An error that should not occur in front of the customer – and was immediately reported by the engineers to their colleagues in Germany.
As long as this remains the biggest “problem” on the 13,000-kilometre tour, Kempfle will probably be very relaxed about the start of production at the end of the year.
0 Comments