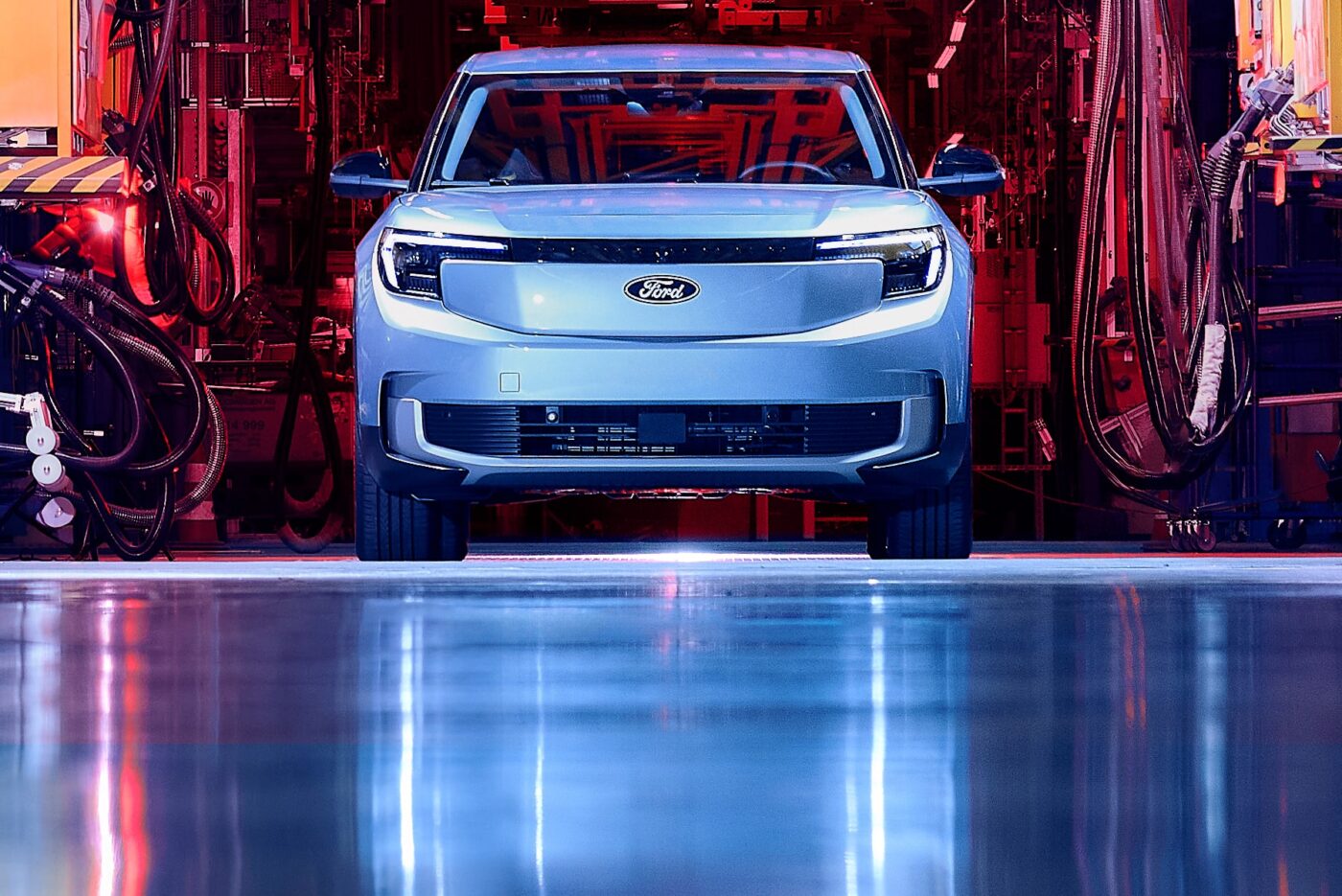
Ford heralds the start of series production of the Explorer
The headquarters in Detroit has invested more than two billion US dollars in the German site to make the Cologne plant fit for the future – specifically, for the production of electric cars. Since the summer of 2023, when the last Fiesta was completed in final assembly, no production vehicle has left the hall. Strictly speaking, you would even have to call it the penultimate Fiesta, because the very last one never left the hall – the vehicle still stands as an exhibit with the signatures of all employees on the edge of the assembly lines.
But not only the assembly of the Fiesta is history in Cologne, the entire site has been and is being remodelled for the Explorer and the second model, which will celebrate its premiere later this year. Transmissions are no longer manufactured in Cologne, and the old engine production facility has been demolished. Where three-cylinder engines used to be produced, work is currently still underway on the company’s own battery assembly line. From the summer, Ford intends to assemble the battery packs for the Explorer e-SUV and the sportier electric crossover itself. Until then, the finished battery packs will be delivered completely finished by technology partner VW – specifically from Skoda’s battery assembly plant in Mlada Boleslav.
The European Ford Explorer, not to be confused with the larger US model, is, as is well known, the first model to emerge from the cooperation with Volkswagen – you can find all the technical data on the model in this article. The VW Group provides the technical basis via its MEB electric platform and supplies some components directly to the Ford plant in Cologne, currently the complete battery, the electric motor and individual sheet metal parts for the platform construction itself.
Ford to build only electric cars in Cologne
At the Cologne plant, known as the Cologne Electric Vehicle Centre since its conversion to an all-electric car production facility, Ford assembles these sheet metal parts in the body shop using over 250 robots in a highly automated process. Welding, glueing, soldering – everything is included. The battery and the two axles are later installed in this substructure on a separate line during final assembly.
The actual bodywork is produced just a few metres away in Cologne, without any VW parts. The new Explorer is the first all-electric high-volume model from Ford to be developed in Europe for Europe. When designing the body, the Ford people were inspired by the American brand heritage and, for example, designed the Explorer to be a little wider and more present than its sister models from the Wolfsburg brand empire. ‘The Explorer had to become a real Ford and have its own identity,’ says Ford’s Managing Director of Marketing and Sales in the DACH region, Christian Weingärtner. ‘We didn’t just want to stick our logo on another car. Although the Explorer uses a VW platform, it looks completely different.’
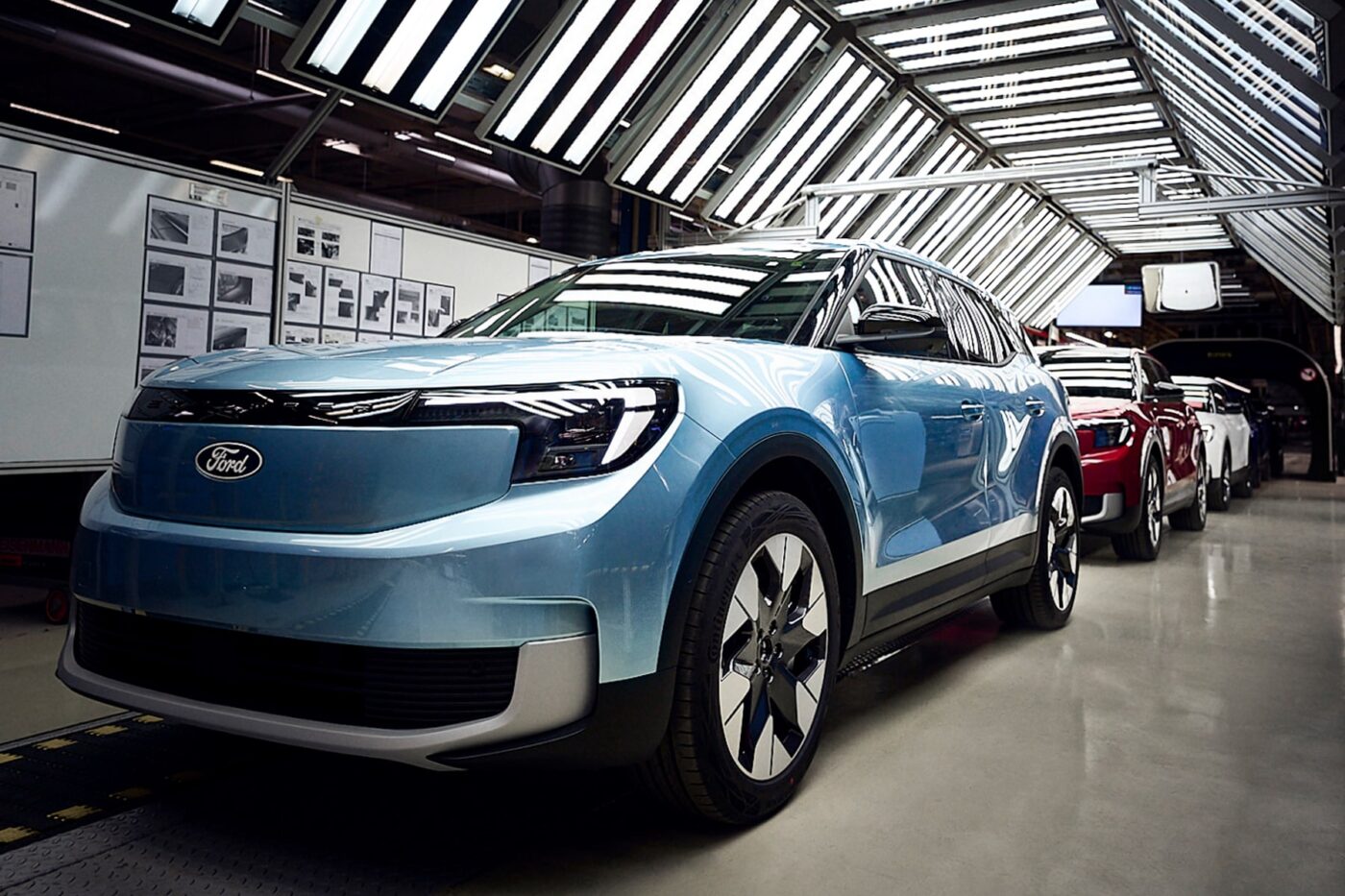
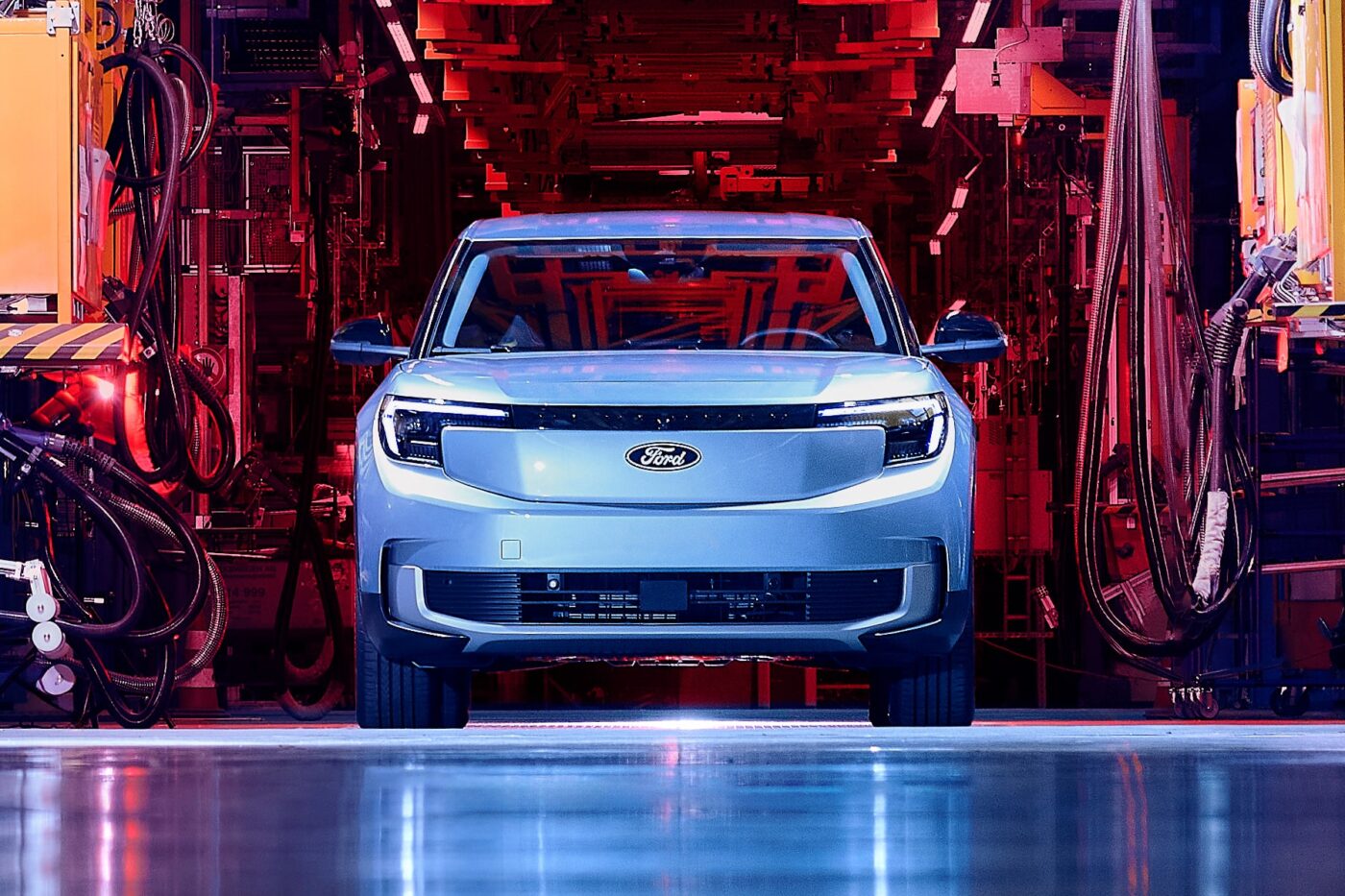
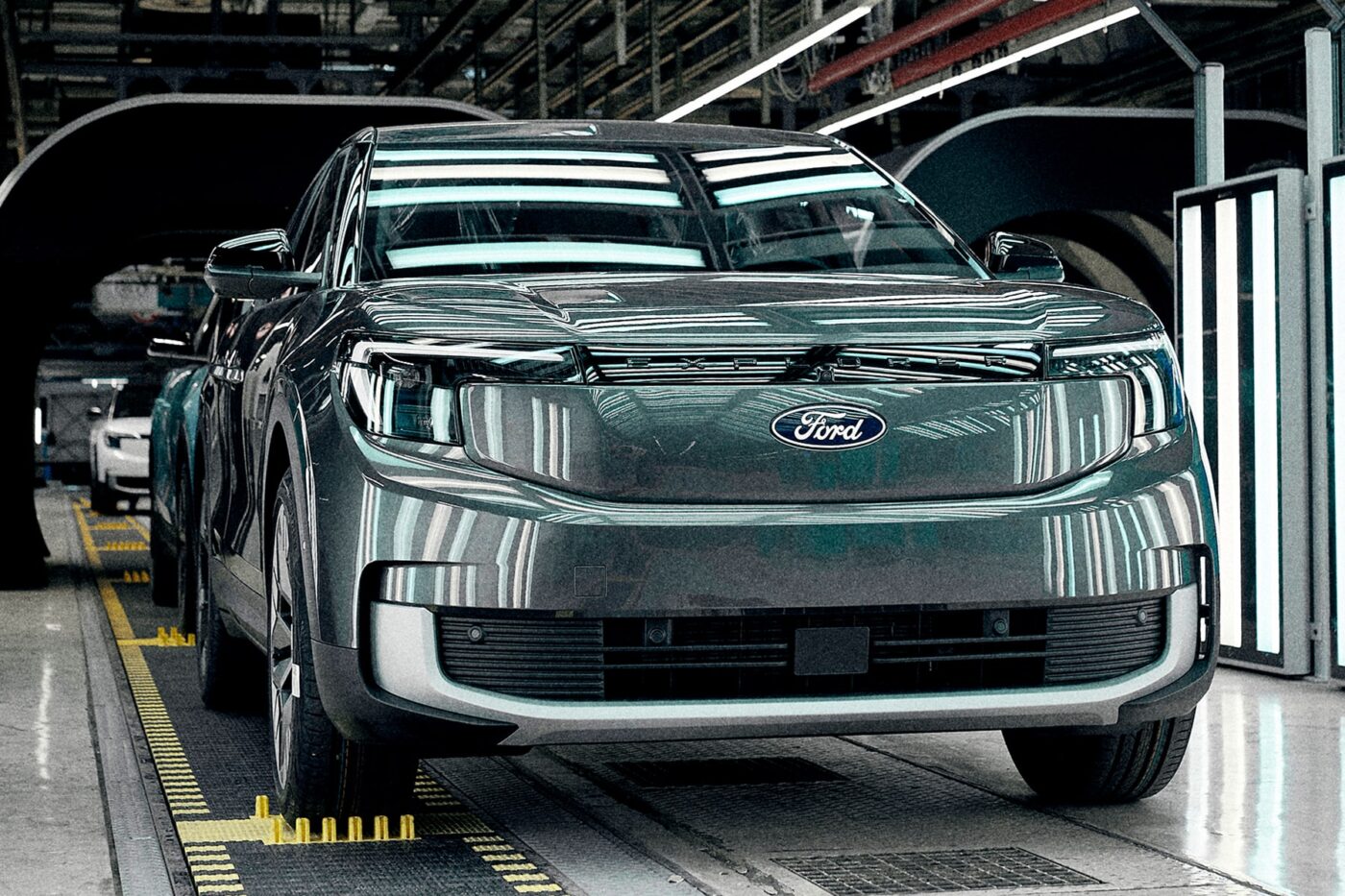
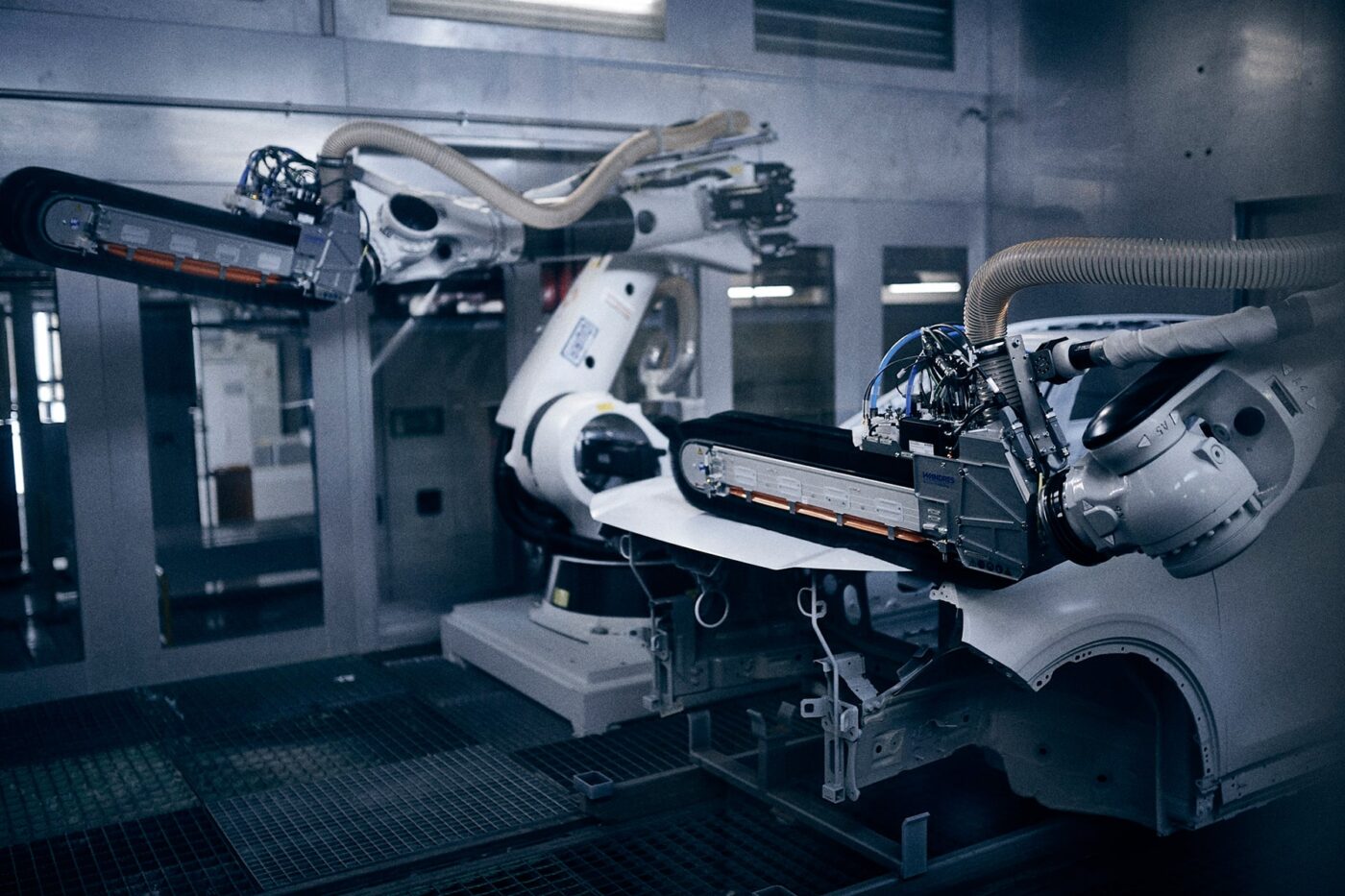
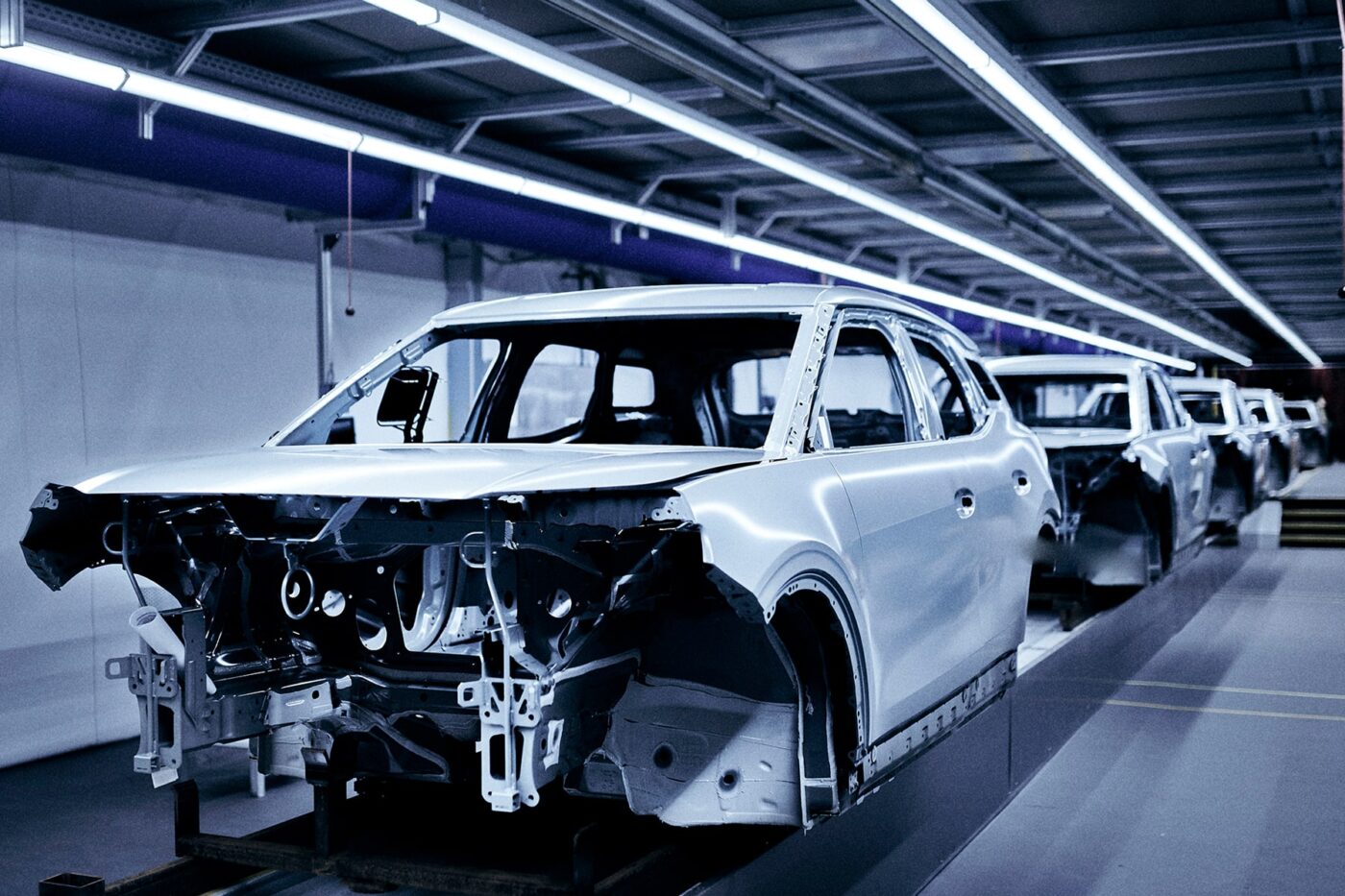
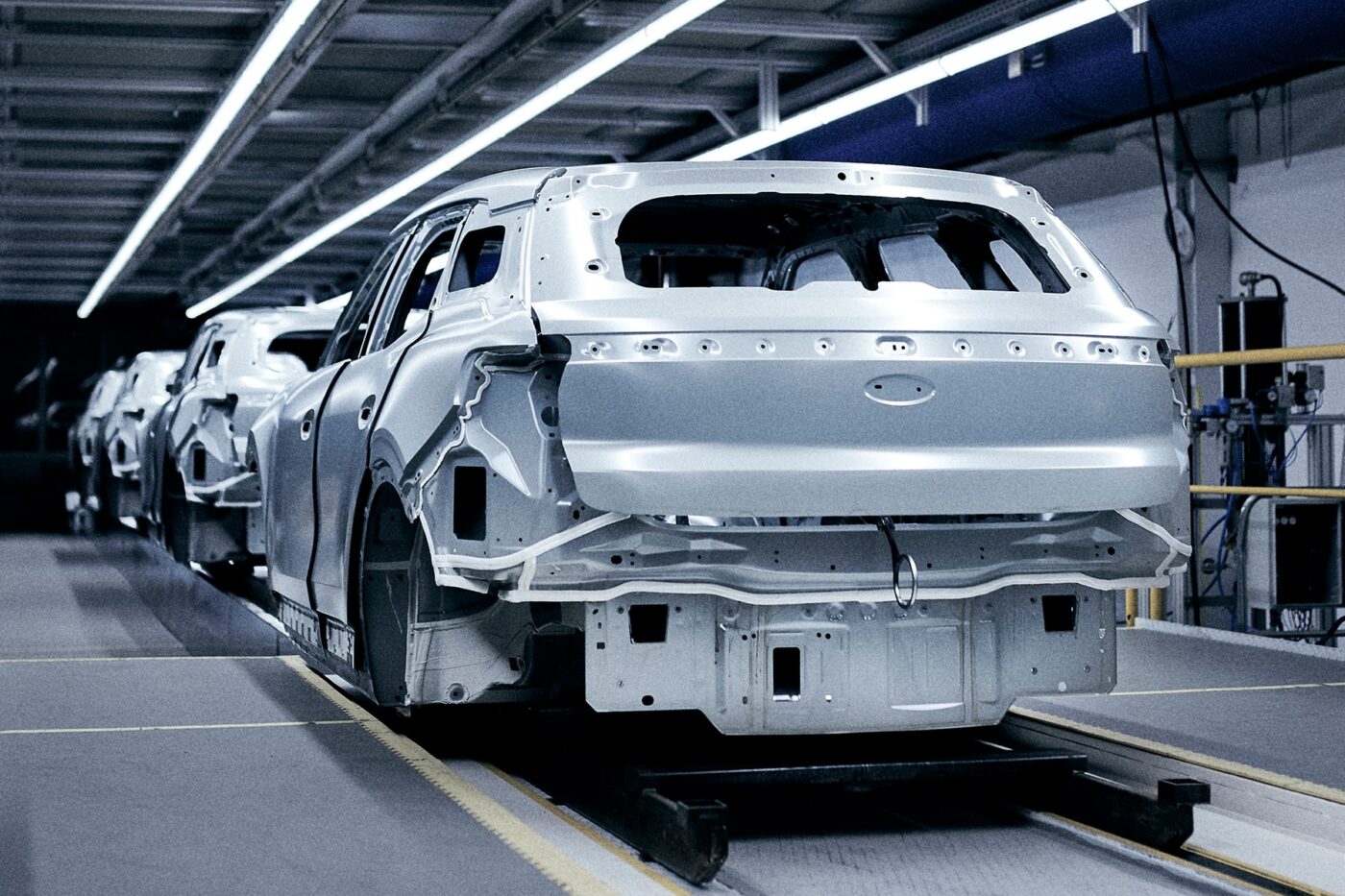
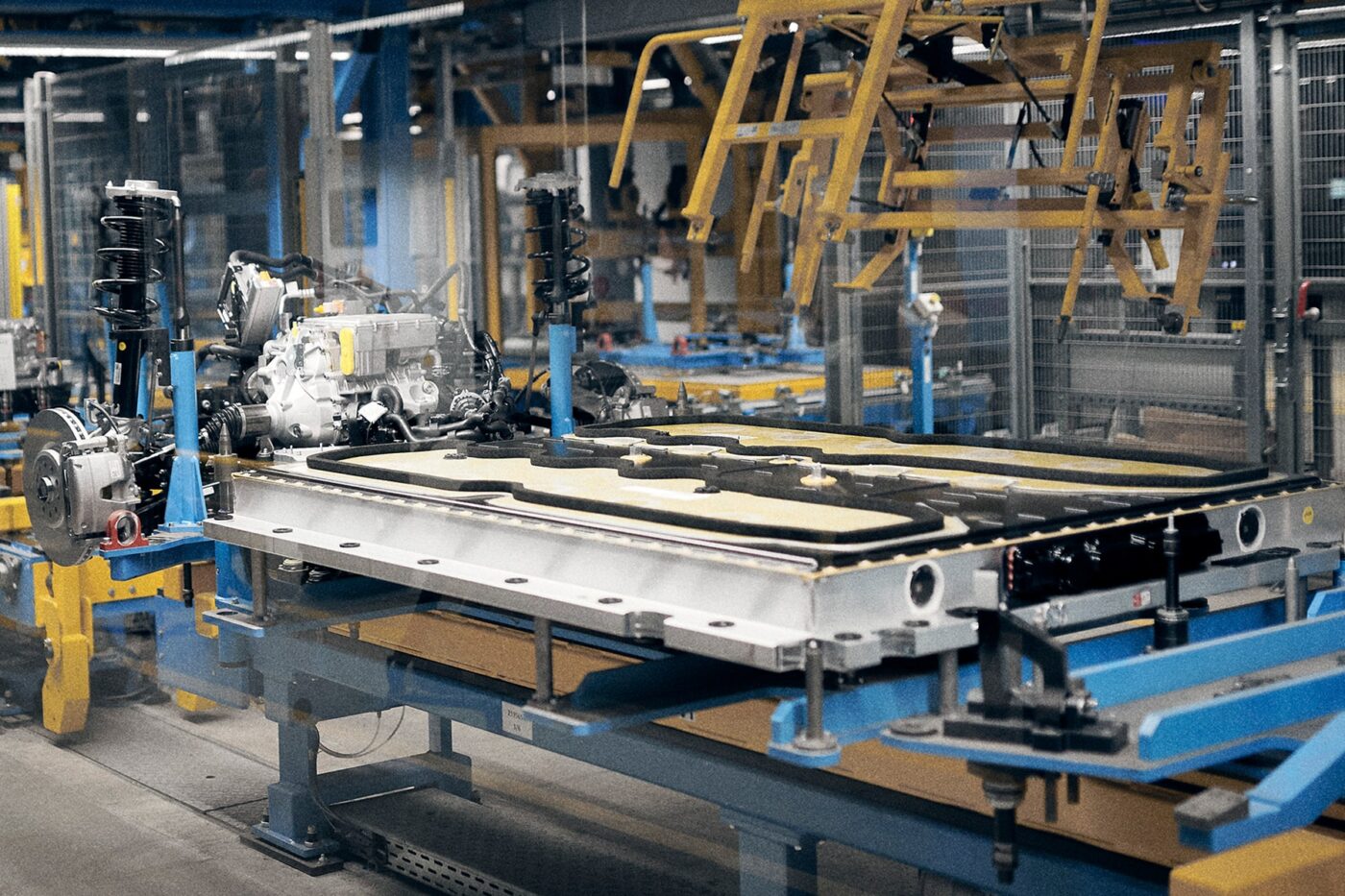
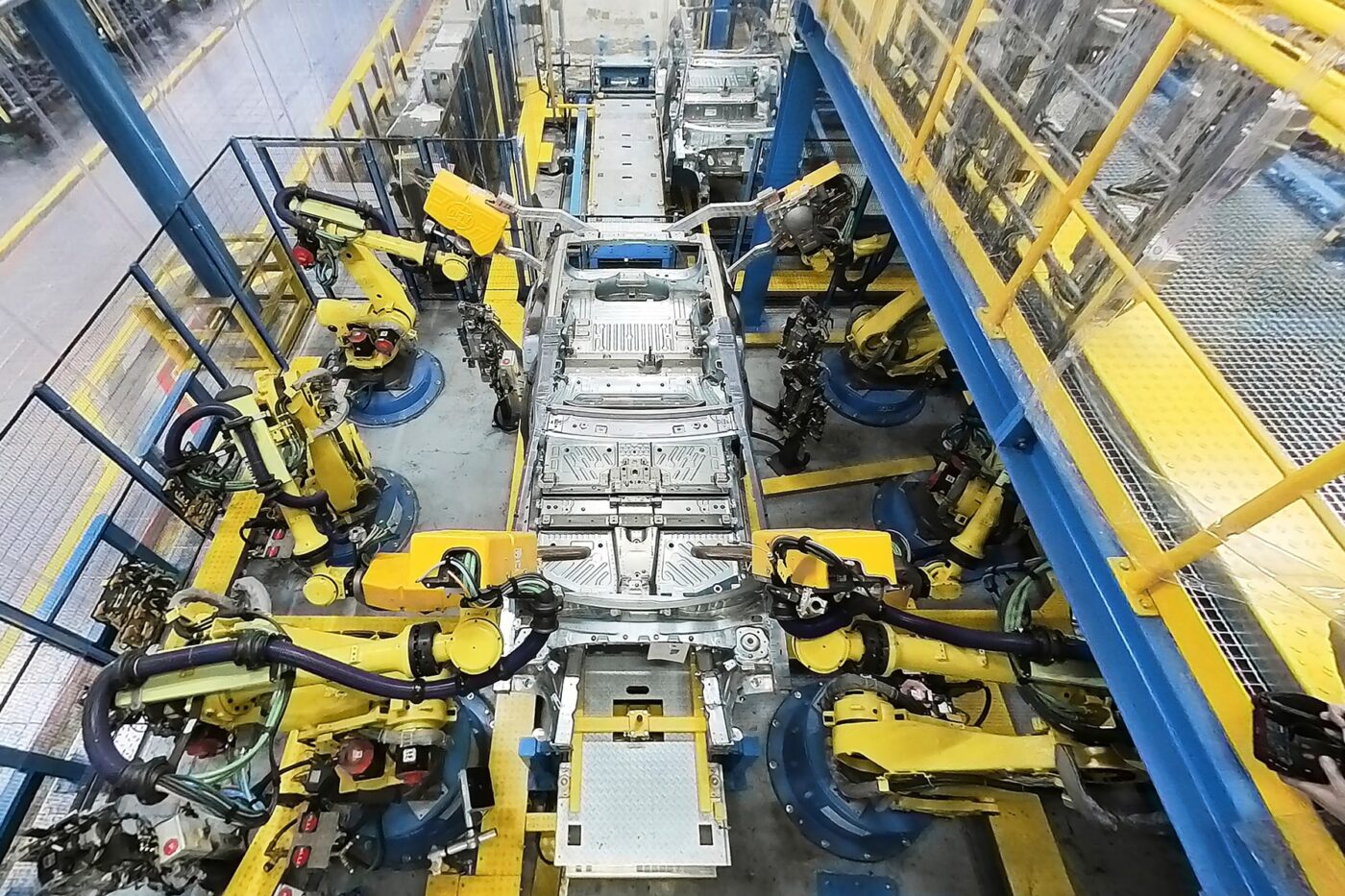
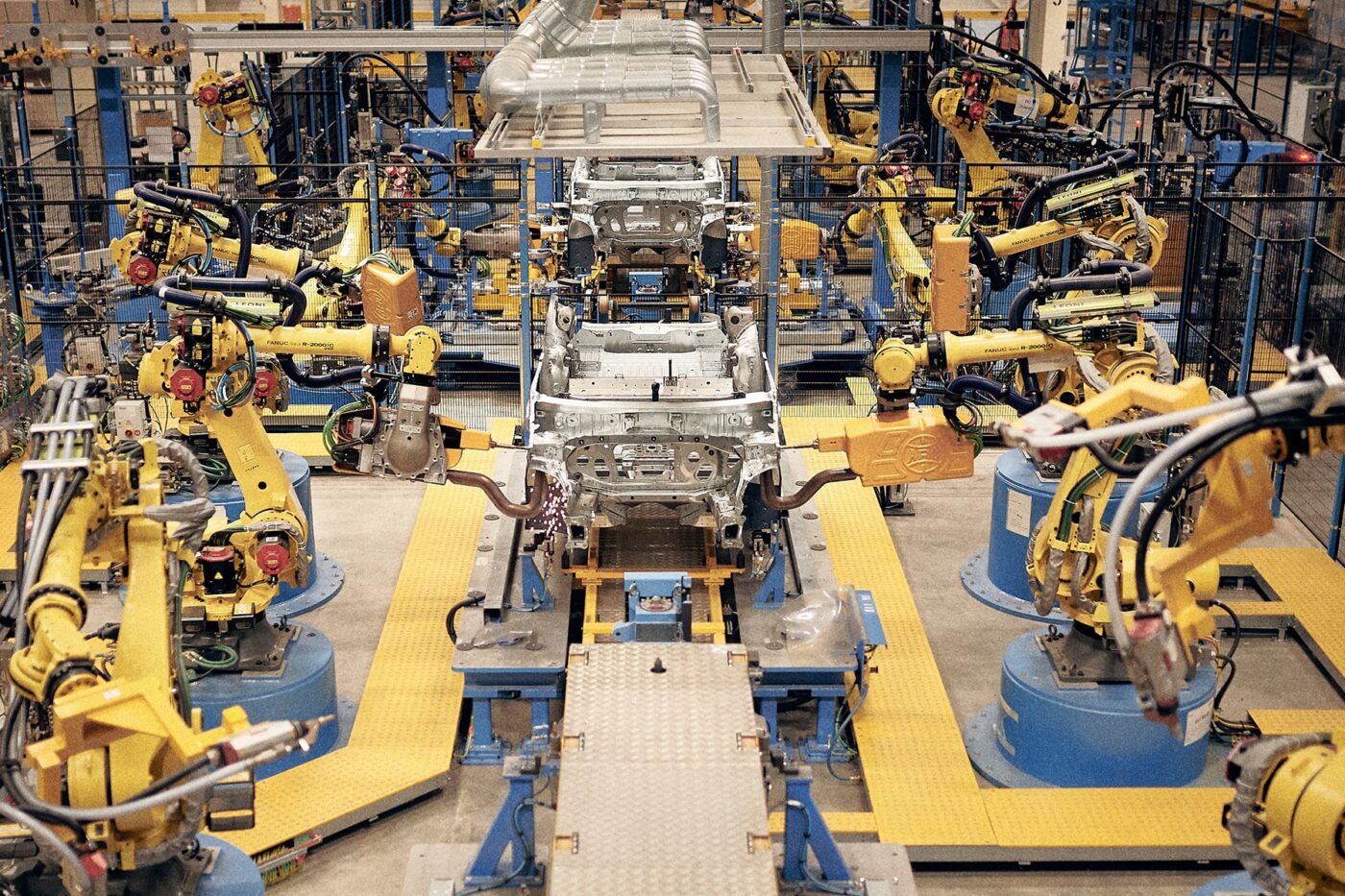
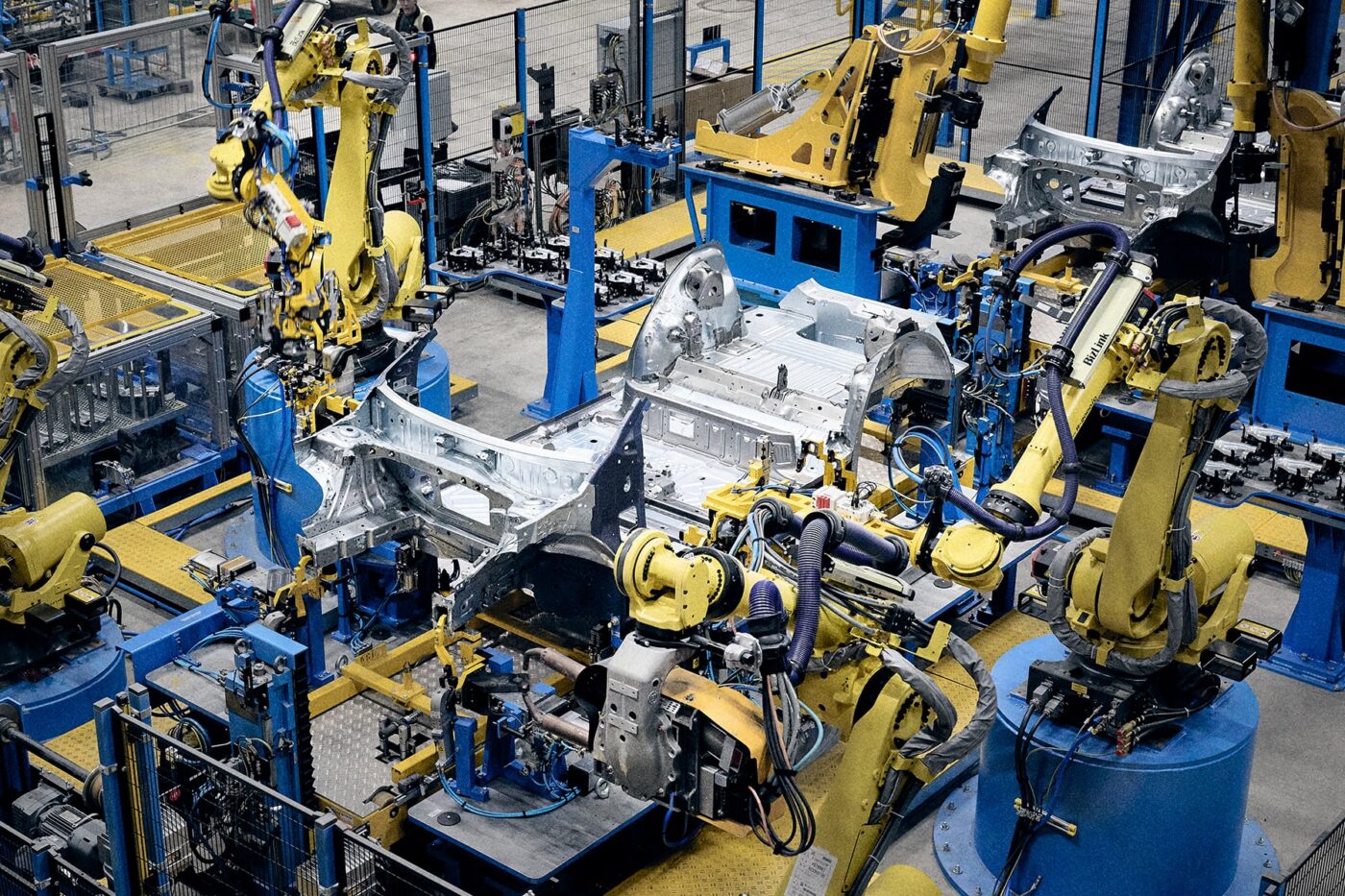
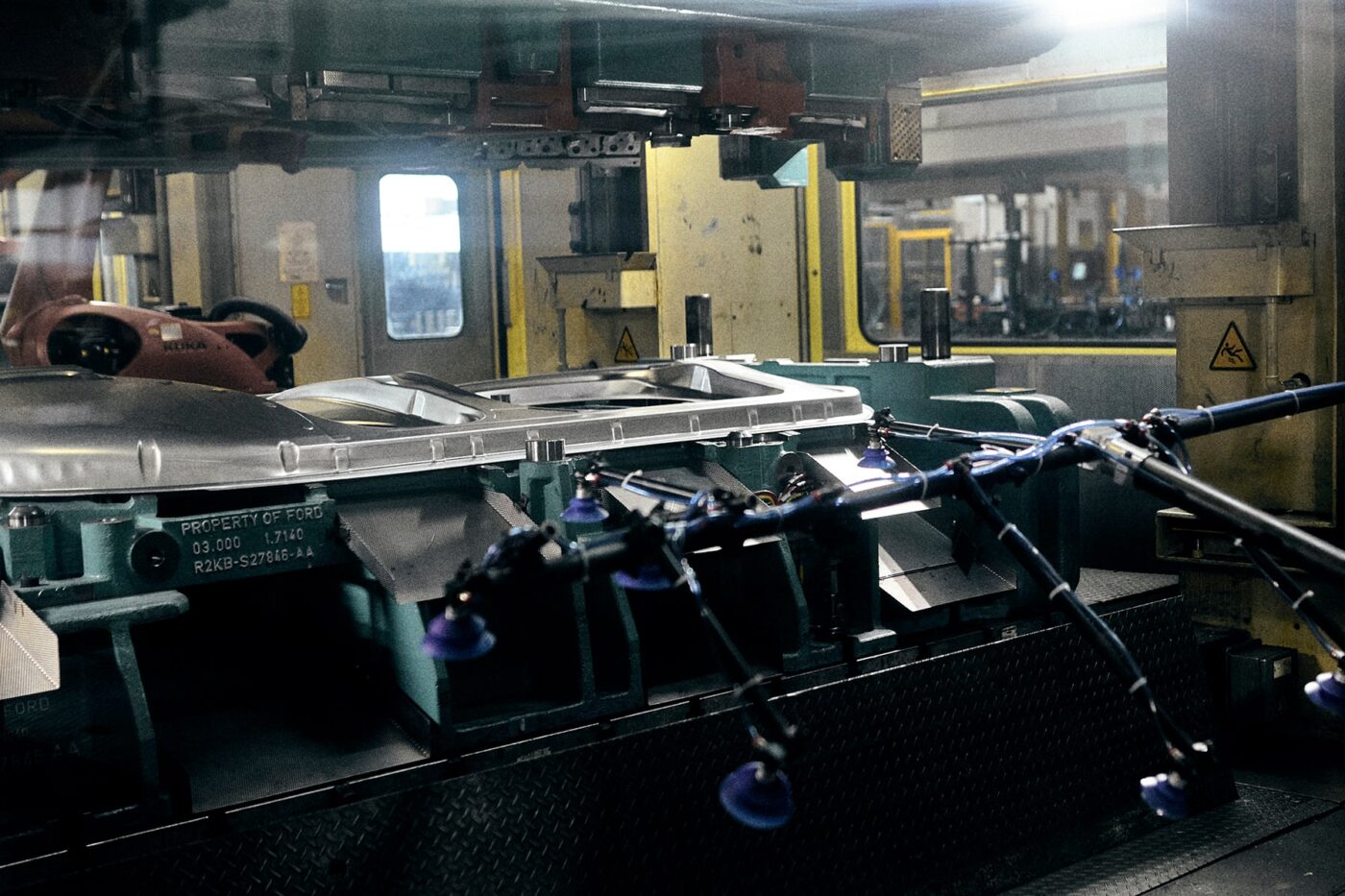
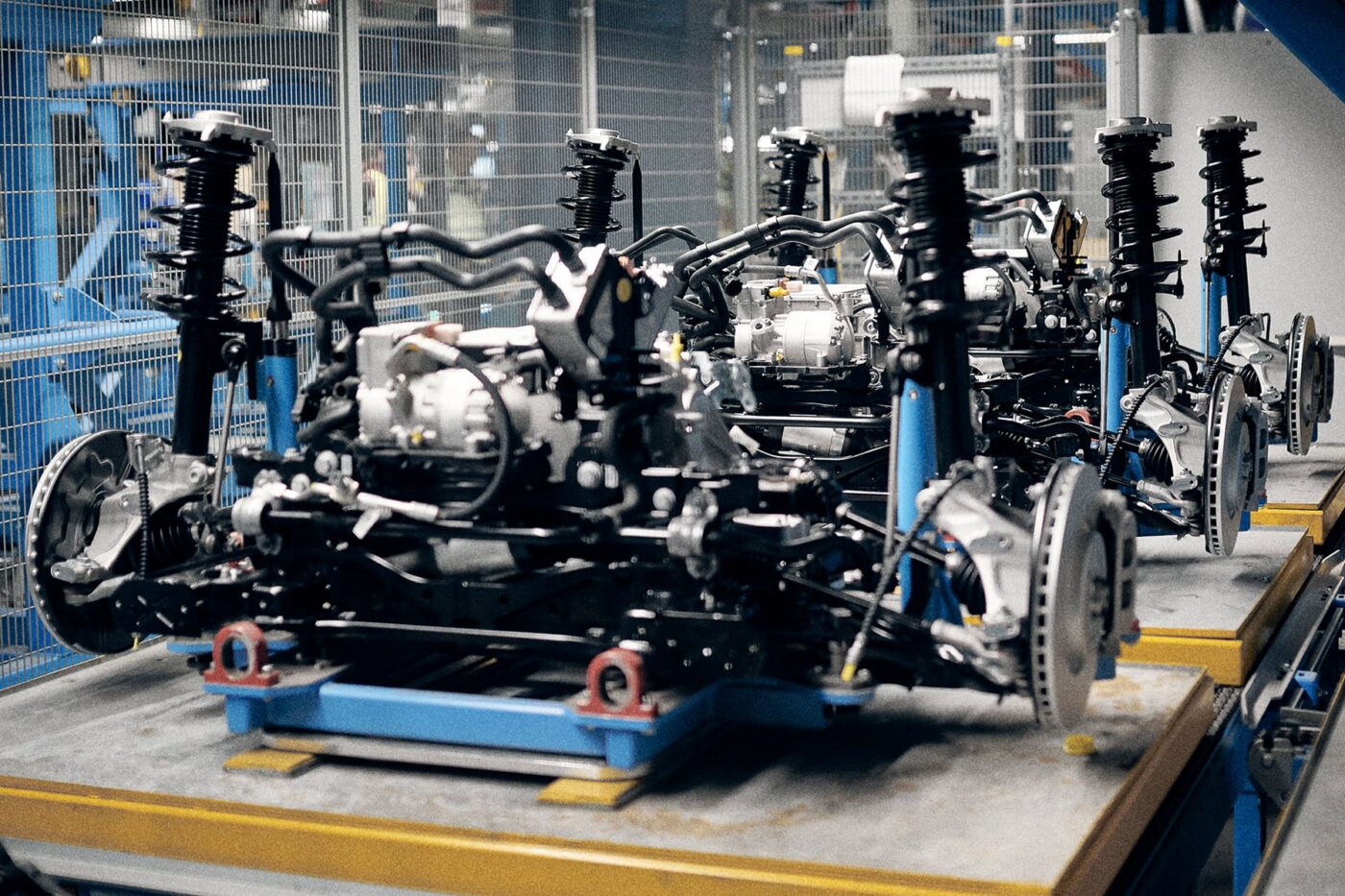
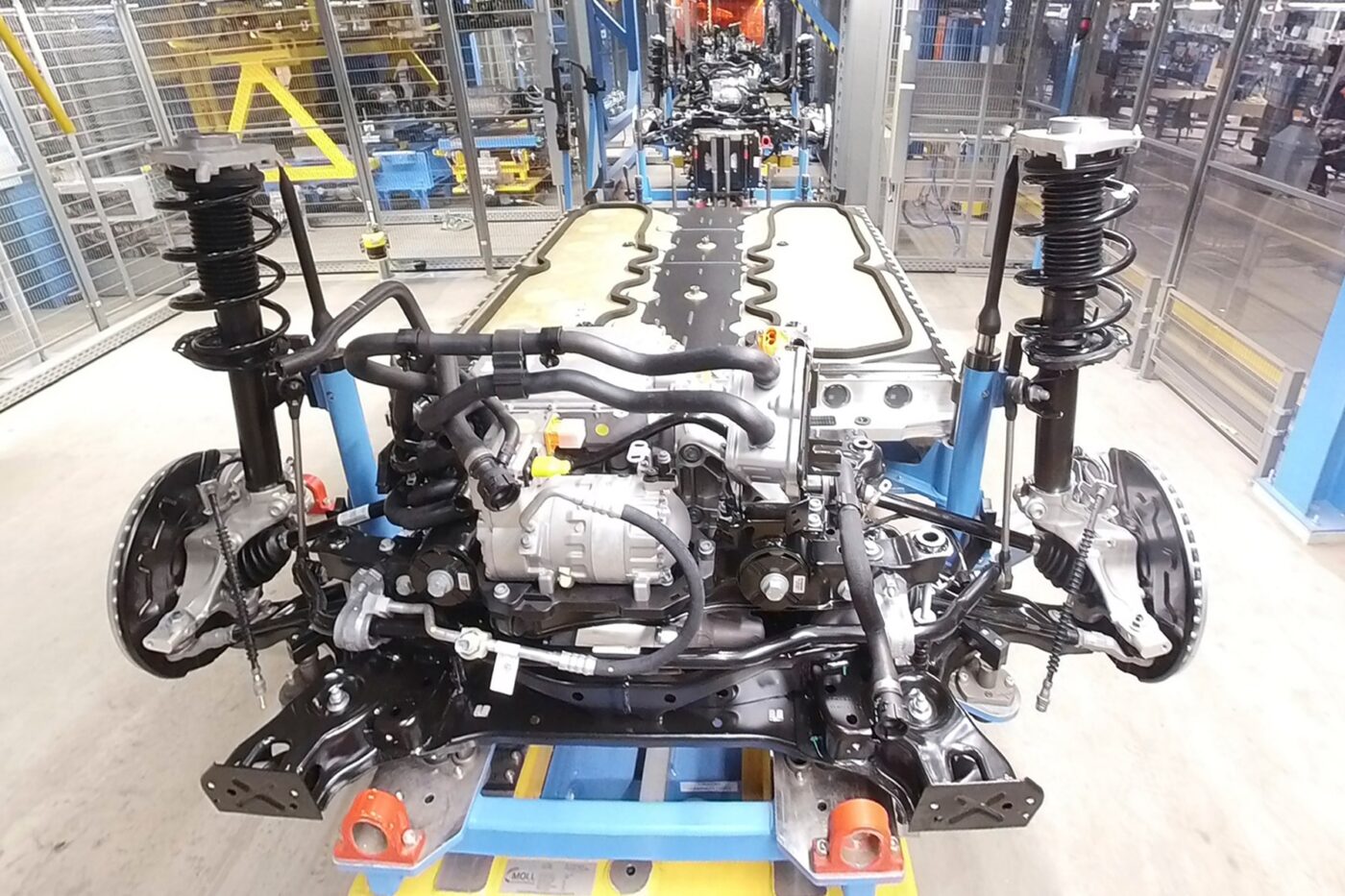
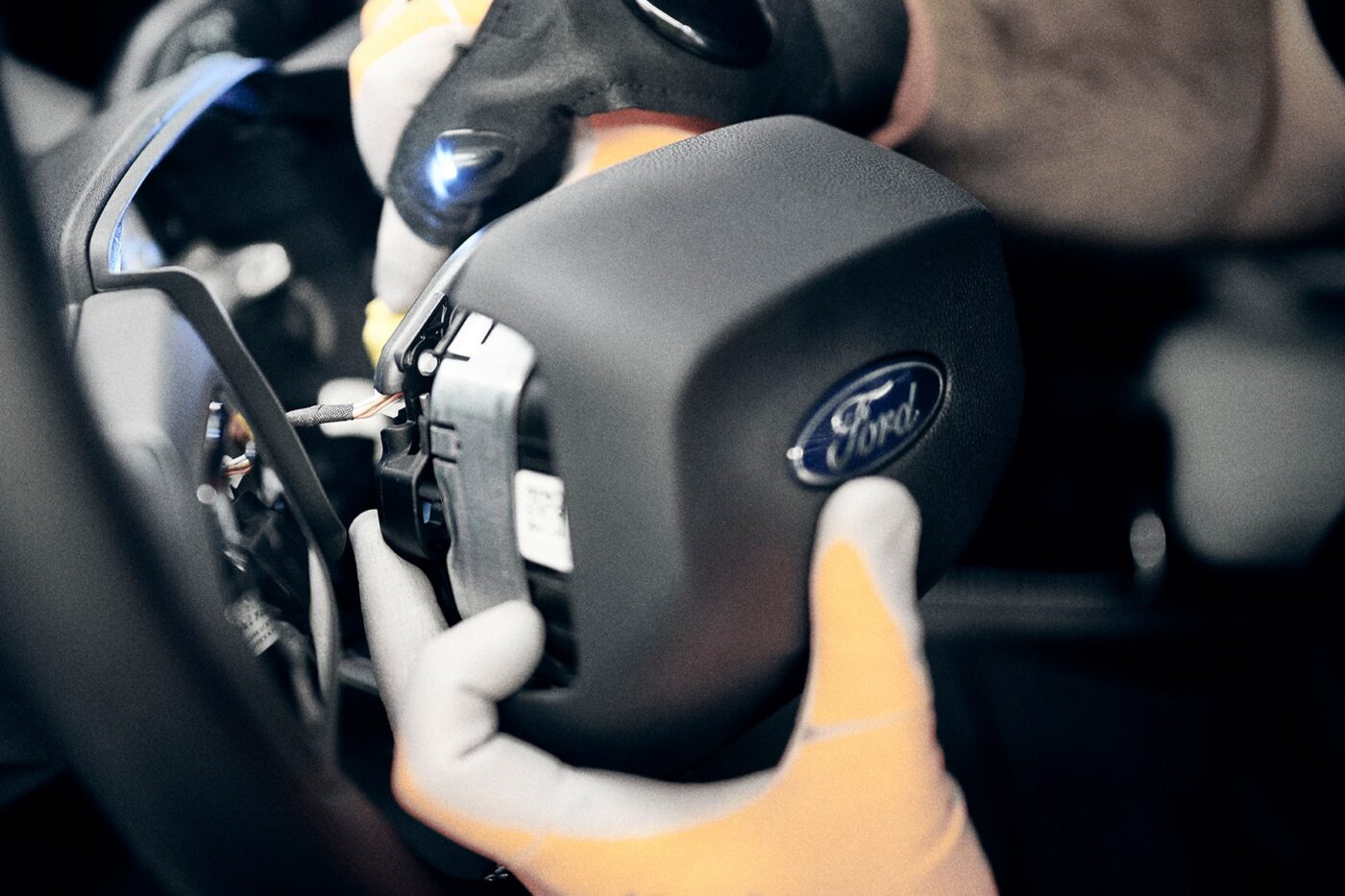
Production is primarily to be a German affair – the process was designed by the Cologne production team in collaboration with several mechanical and plant engineers. One example: Ford has integrated its own measuring centre into the body shop for the production of the electric models. Countless production steps – including the application of adhesives – are fully monitored in the production process itself. The second the robot applies the adhesive, several lasers check the thickness and position of the material. If there is a deviation, the part is rejected and reworked.
In addition to these ‘in-line’ checks, several workpieces per shift are examined more closely in the measuring centre, sometimes down to a thousandth of a millimetre. Individual components, the platform or even the complete ‘body in white’, i.e. the finished but still unpainted body shell, are precisely recorded using cameras and lasers. If the measured components deviate minimally from the ideal condition – well before the actual production tolerance is reached – the measurement team can record this and pass it on directly to the relevant station in production. This allows readjustments to be made at an early stage, even if it is only a matter of tenths of a millimetre. ‘We monitor every production step, from assembling the first parts to rolling out the finished vehicle, and thus achieve an unprecedented level of quality for our customers,’ explains Rene Wolf, Managing Director Production Ford-Werke GmbH.
Two assembly lines become one
The paint shop, where the bodyshells are cleaned, sealed, primed and painted, is a new building. The Explorer – although slightly shorter than the familiar MEB SUVs at 4.45 metres – is simply bigger than the Fiesta previously built in Cologne. However, it was not easy to integrate a modern paint shop into the site. The Ford plant in Cologne had been built since 1930 and went into operation in 1931 – and the previous conversions were also subject to completely different standards and specifications. So an old warehouse had to make way for a new building 100 metres long, 25 metres wide and 25 metres high. Systems and machines are installed on three floors. The 320,000 litre dip tank for galvanic priming is located on the top floor at a height of 18 metres. Heat exchangers, fans and filters ensure that as much heat as possible remains in the building and can continue to be utilised – some processes take place at up to 60 degrees, while the primer is baked at 165 degrees. Finally, the new plant is said to be one of Ford’s ‘most efficient production facilities worldwide’ – the company has also been able to reduce water consumption.
The finished painted bodies then go into final assembly. Although this is still the same hall, the inside has been completely remodelled. In the Fiesta days, there were still two identical assembly lines working in parallel. The Explorer and the second model are now only built on one line – but this is divided into a total of six areas.
The fact that an electric car is supposedly easier to build is not directly confirmed by Ford, at least with regard to final assembly. This is because many work steps were previously not part of the final assembly. The air conditioning compressor used to be driven by the V-belt of the combustion engine and therefore arrived in the hall fully assembled together with the engine. With electric cars, on the other hand, a separate air conditioning compressor has to be installed, as does the heat pump, which was previously not present. The complexity and number of cooling systems has also increased, meaning that more hoses and clamps have to be fitted and checked during final assembly. “For us in final assembly, the combustion engine was a black box – it arrived ready and just had to be installed,” explains Jochen Bruckmann, Launch Leader Final Assembly. “The electric car with the battery, the many components such as pumps and so on is more complex for us.”
This has several consequences. As mentioned, there is now only one large production line in the hall instead of two parallel ones. And the team in final assembly has been increased from 780 to over 1,000 people. In total, around 3,300 people work in the various production areas for the two electric cars in Cologne. In addition, a new quality assurance system was set up at the end of the ‘battery line’, where the battery pack and the axles with the drive(s) and the countless cables and cooling lines are installed in the platform. Cameras and lasers check each individual platform here before it is screwed under the body during the ‘marriage’. Artificial intelligence analyses this data and assesses whether everything has been pre-assembled correctly. The system can not only recognise whether a tool has been forgotten on the battery housing, for example, but can also detect whether a plug is really fully inserted or not. This AI-based quality control is intended to prevent the platform and battery having to be disconnected from the vehicle again later for rework.
58 screws on the electric car – six on the Fiesta
And the marriage itself is also more complex than with a combustion engine. In the Explorer, the substructure with battery, drives and chassis is attached to the vehicle with 58 bolts, all of which have to be tightened in the right order with the correct torque. This is so time-consuming that this work step now takes place at five stations, each with four robots tightening the bolts. 20 robots at one station would only get in each other’s way. By comparison, the Fiesta only required six bolts – four for the front axle and two for the rear axle.
The Ford team in Cologne designed the production process themselves. Bruckmann and his team were there from day one when the first Explorer models were assembled by hand. Every move was recorded, evaluated and optimised until the complex sequence of workstations was finalised and the stations themselves were adapted to the possibilities in the existing hall. All of this is now a digital process, and the entire final assembly can also be followed in real time in a meeting room right next to the assembly area via the digital twin.
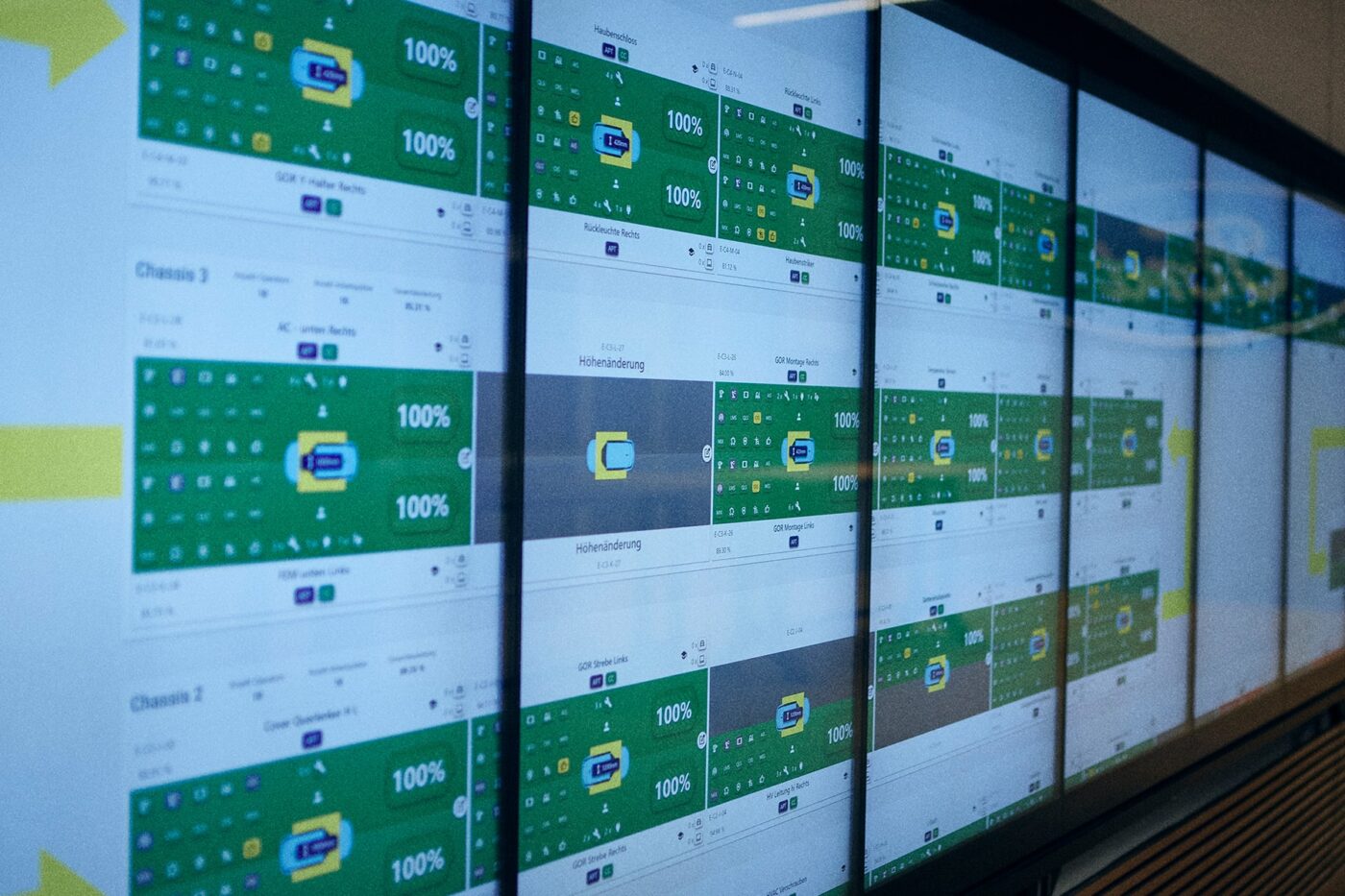
Ford did not buy in a production system, but developed the software behind it itself, as Tobias Sender, Head of Final Assembly, explains in an interview with electrive. Whether via the more than ten metre wide touchscreen arrangement in the meeting room or via smartphone, the status of each station can be tracked – right down to the satisfaction of the employees on site. ‘Satisfied employees deliver good quality,’ says Sender. If staff rate the conditions at a station less favourably, Sender and his team can intervene directly. In future, the specially developed software will also be used outside of final assembly. ‘We will also use the system in the new battery assembly line before rolling it out to other Ford plants worldwide,’ explains the manager.
If everything runs smoothly, up to 250,000 units of the two models could roll off the production line in Cologne every year. At the start of series production, there will of course be even fewer vehicles; Ford is currently aiming for 150 to 250 Explorers per day. After the ramp-up, however, the target is 640 cars per day.
Although Ford’s Managing Director of Marketing and Sales in the DACH region, Christian Weingärtner, does not want to say exactly how many pre-orders there are for the new Explorer, he is basically ‘quite satisfied’. “We have modelled ourselves on the market launch of the Puma, because with the Puma we have also launched a new model series where Ford previously had no offering. And we are currently exceeding the Puma’s figures with the Explorer,” says Weingärtner. However, the manager also emphasises the importance of the timing, because the big push for the Explorer is not expected to come until the vehicle is in the showroom at dealerships.
Small battery to follow this year
Weingärtner sees a “completely different basis in retail than when the Mustang Mach-E was launched.” Everything was still new with Ford’s first electric SUV. However, the Explorer from Cologne is in a price class below this and is intended to appeal to a much larger customer base. The Explorer has been available to order since the end of March at prices starting at €42,500, although the model with the small battery will not be launched on the market at this base price until the end of the year. “In this segment, the majority of customers opt for the larger battery,” explains Weingärtner. “With electric cars, we see that leasing is more important than cash purchases. And the larger battery doesn’t make such a big difference to the leasing instalment.”
However, it will make a big difference for Ford whether the Explorer and the upcoming crossover model hit the market or not. This is because Ford no longer has a combustion engine model with which the plant could be utilised in the event of fluctuating demand for electric vehicles.
0 Comments