Nissan wants to build first solid-state battery cells in 2025
Nissan did not provide any information on the initial production capacity or the planned ramp-up in the pilot plant in the press release. Instead, it is announced that 100 workers per shift will be employed from the financial year beginning in April 2028 in order to increase production to 100 megawatt-hours per year. Series production of solid-state batteries is currently scheduled to begin in 2029.
The plant in Yokohama is still under construction – in the update, Nissan published pictures of the still empty production rooms. The cells themselves and the production processes are to be improved with the solid-state batteries produced from 2025. For this reason, Nissan does not provide any key data on the current status of cell technology in the short communication but stuck to more general statements instead. According to the Japanese company, solid-state cells “have the potential for approximately twice the energy density of conventional lithium-ion batteries, significantly shorter charging times due to superior charging and discharging performance and lower costs due to less expensive materials”.
According to Nissan, it plans to use solid-state batteries “in a variety of vehicle segments, including pickups, to make its electric vehicles more competitive”. Here, too, the company is not yet going into further detail. However, Nissan has been working on solid electrolyte cell technology for several years. When the pilot plant in Yokohama was announced in 2022, it was still said that it would go into operation in 2024 and that series production would start in 2028 – in both cases, it is now likely to be a year later.
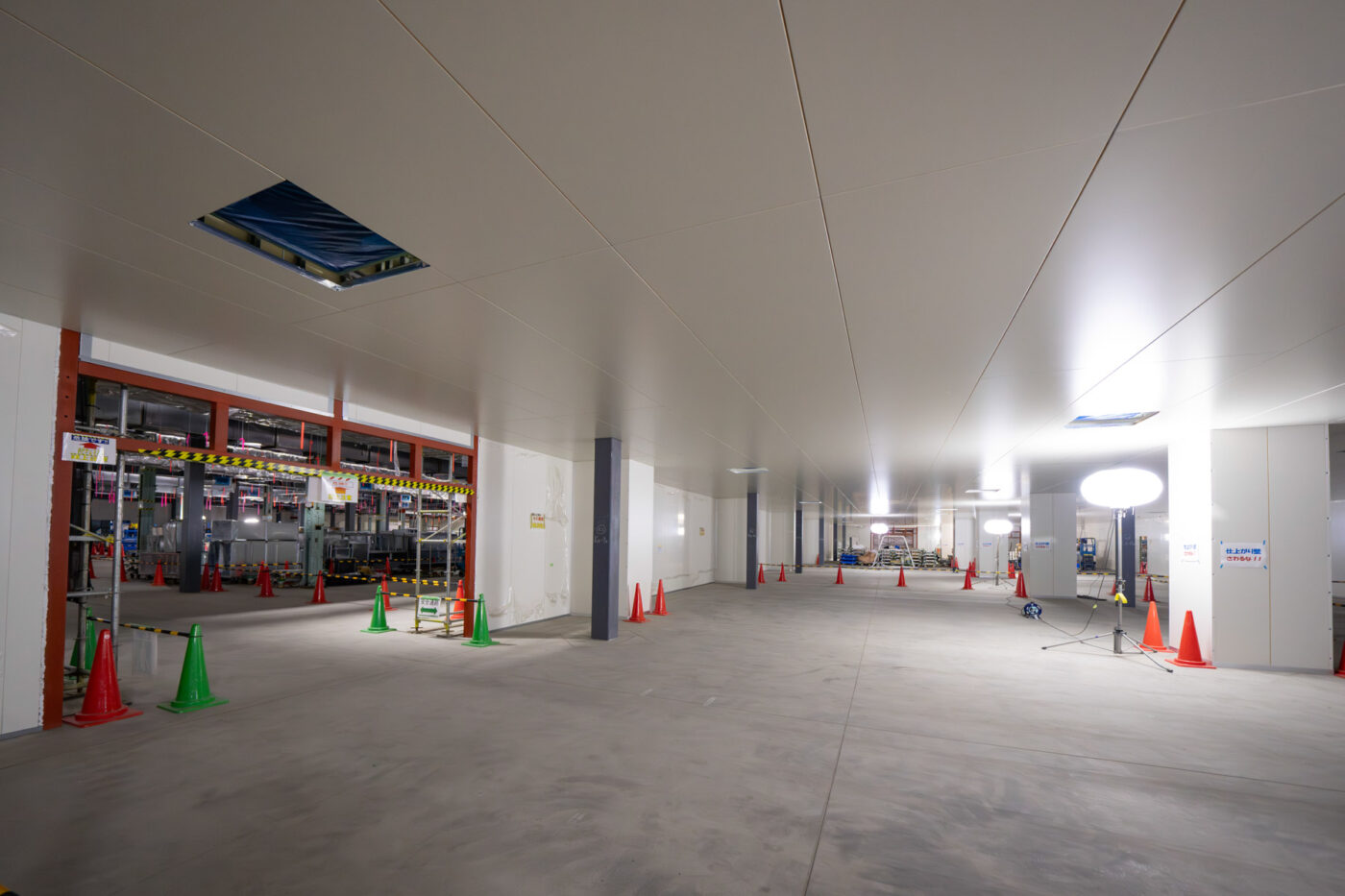
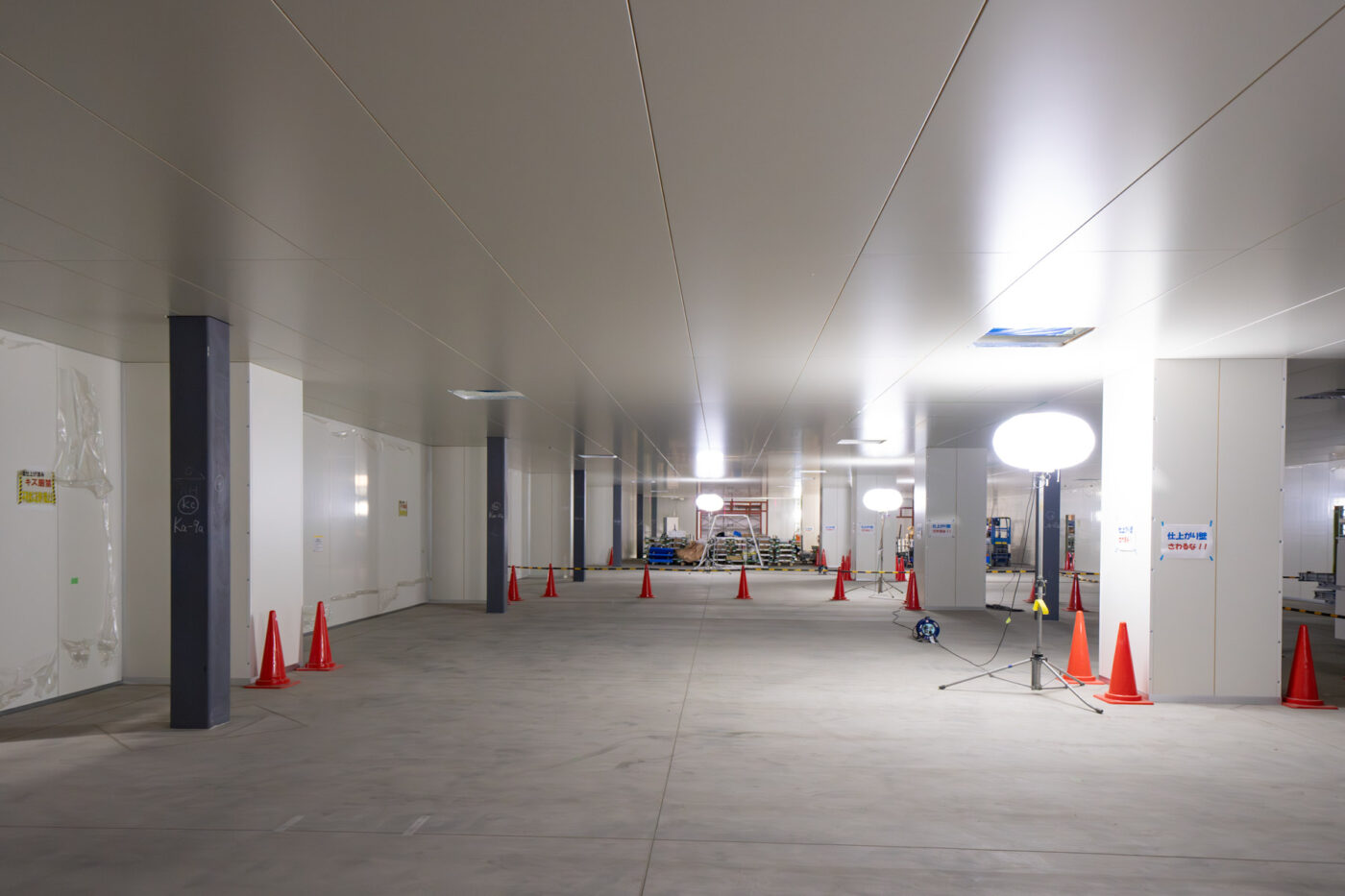
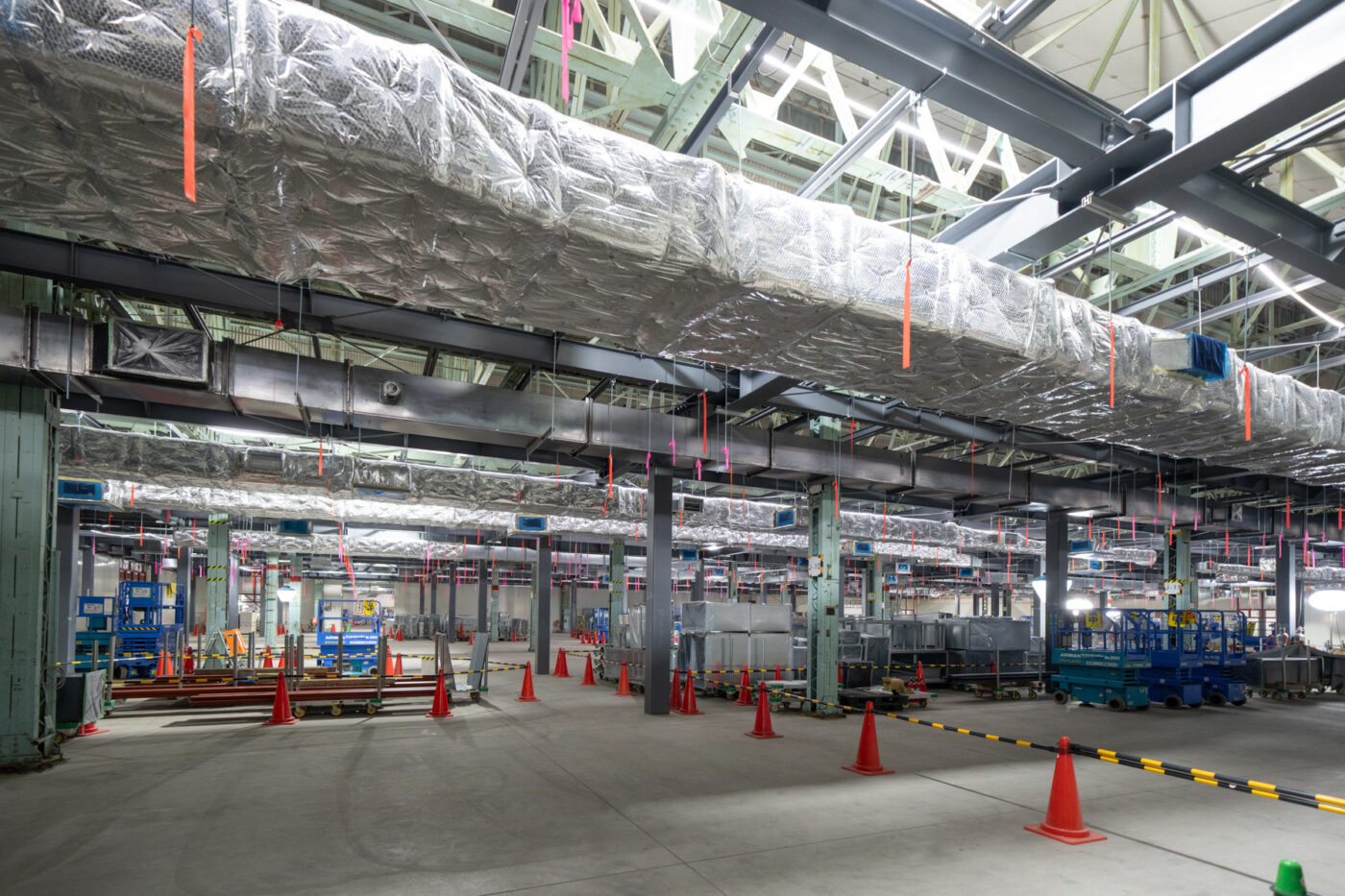
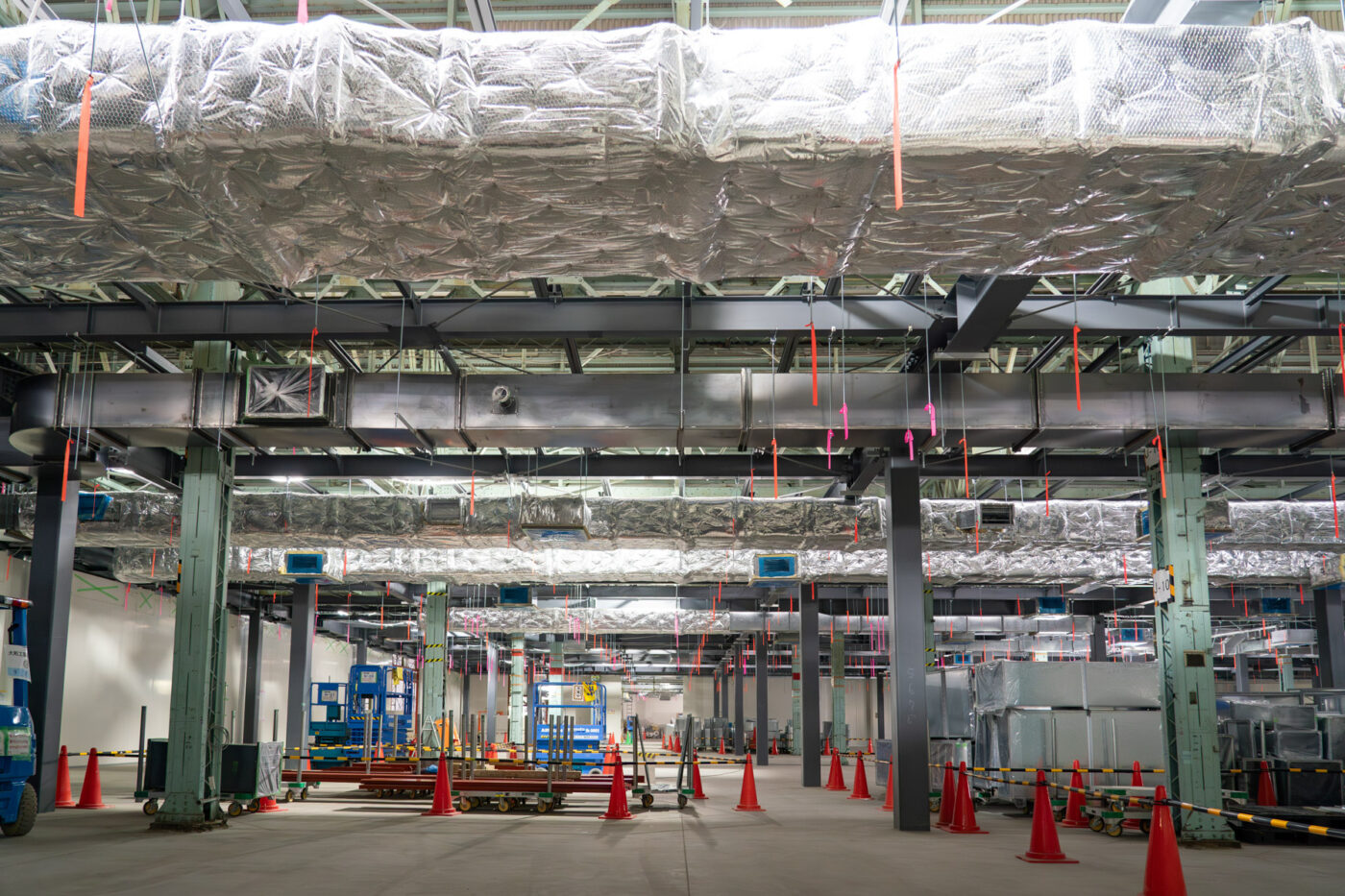
It is not just the batteries for its future electric cars that Nissan wants to reduce costs, however: According to articles from Reuters and Bloomberg, the Japanese company also wants to use the gigacasting process in the production of electric cars – in other words, to produce larger cast parts in one piece. A gigacasting machine weighing over 6,000 tonnes is to be used at the Tochigi plant to produce the rear body structure as an aluminium casting. This should reduce manufacturing costs by ten per cent and the weight of the components by 20 per cent compared to the current production process, in which many individual parts are manufactured and then joined together.
Reuters quotes Hideyuki Sakamoto, the Executive Vice President for Manufacturing and Supply Chain Management, as saying that Nissan “considered various things” for the production of car bodies. In the end, however, the decision was made to opt for the large die-casting machine.
The production of large structural parts from a single mould has been driven by Tesla in particular with its factory suppliers. The advantages (as also mentioned by Nissan) are weight and costs, as many work steps are saved. Production is therefore also faster. One disadvantage is the more expensive repair after an accident: individual frame parts can no longer be replaced so easily if the structure is made from a single casting.
0 Comments