Continuous Extrusion of Cathode and Anode Masses as Well as Separator Films with Technology Solutions from Coperion
To meet the growing demand of batteries, manufacturers are dependent on efficient, reliable and flexible production processes. As a result, continuous extrusion of battery masses and separator films is becoming more important as the industry moves away from traditional batch processes.
Based on years of experience, Coperion and Coperion K-Tron deliver continuous processing solutions with high reliability and long operating times, securing consistent, high product quality for various applications. At the heart of the system are Coperion’s ZSK co-rotating twin screw extruders and Coperion K-Tron’s gravimetric feeders.
ZSK extruders for battery manufacturing are specially developed for applications in the battery industry and can handle toxic and difficult materials. All product-contacting parts of the system are equipped with high wear resistance so as to avoid end product contamination – even when processing heavy-wearing raw materials. Furthermore, Coperion’s ZSK extruder design is based on strict explosion protection regulations.
Another feature is the high flexibility of the ZSK process section where conveying, mixing, homogenizing and devolatilization take place in separate process zones. Process engineering from Coperion configures the process section precisely matching to the application required. Manufacturers of batteries benefit from high throughput rates at a high and reproducible product quality.
While offering broad range of system sizes, important process parameters remain constant across the entire ZSK extruder family. As a result, manufacturers benefit from reliable scale up from laboratory-scale results to production systems.
With the comprehensive process know-how in systems engineering, Coperion rotary valves offer reliable process technology solutions that secure a consistently high product quality.
The rotary valve series ZZB is specifically designed for challenging and hard-to-handle materials in continuous production processes.
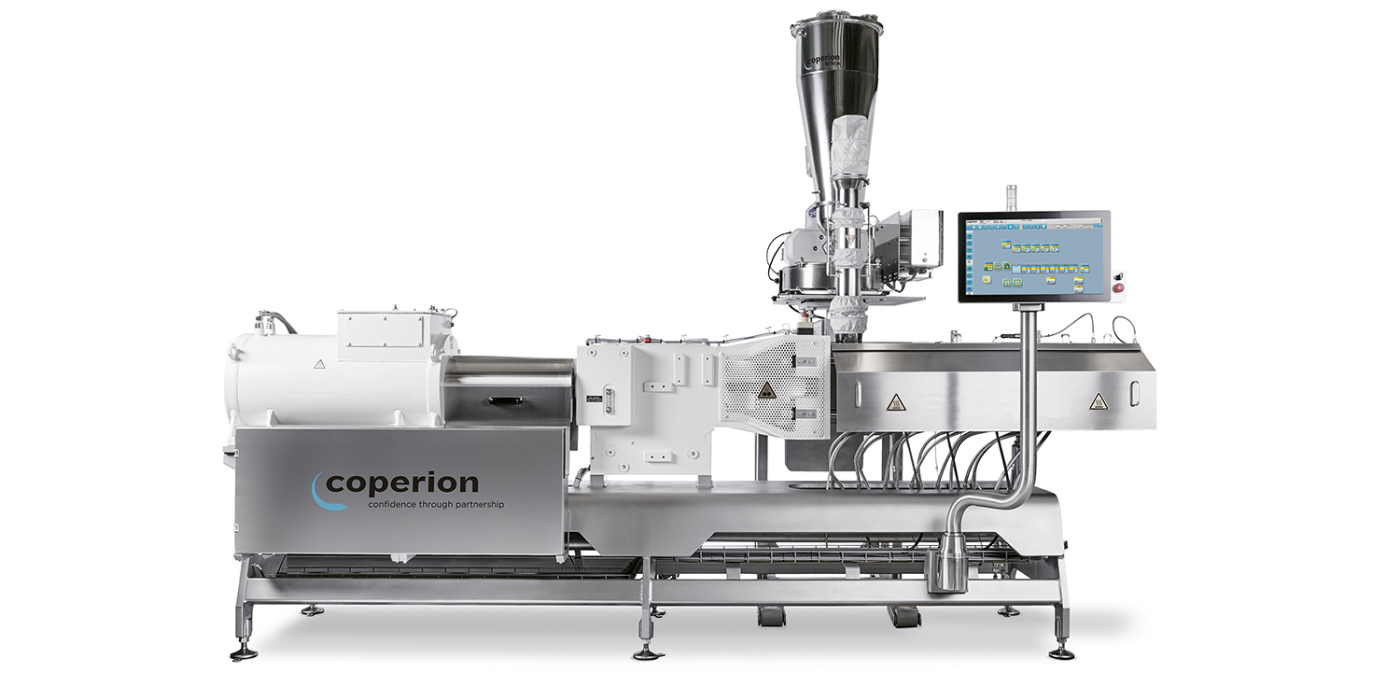
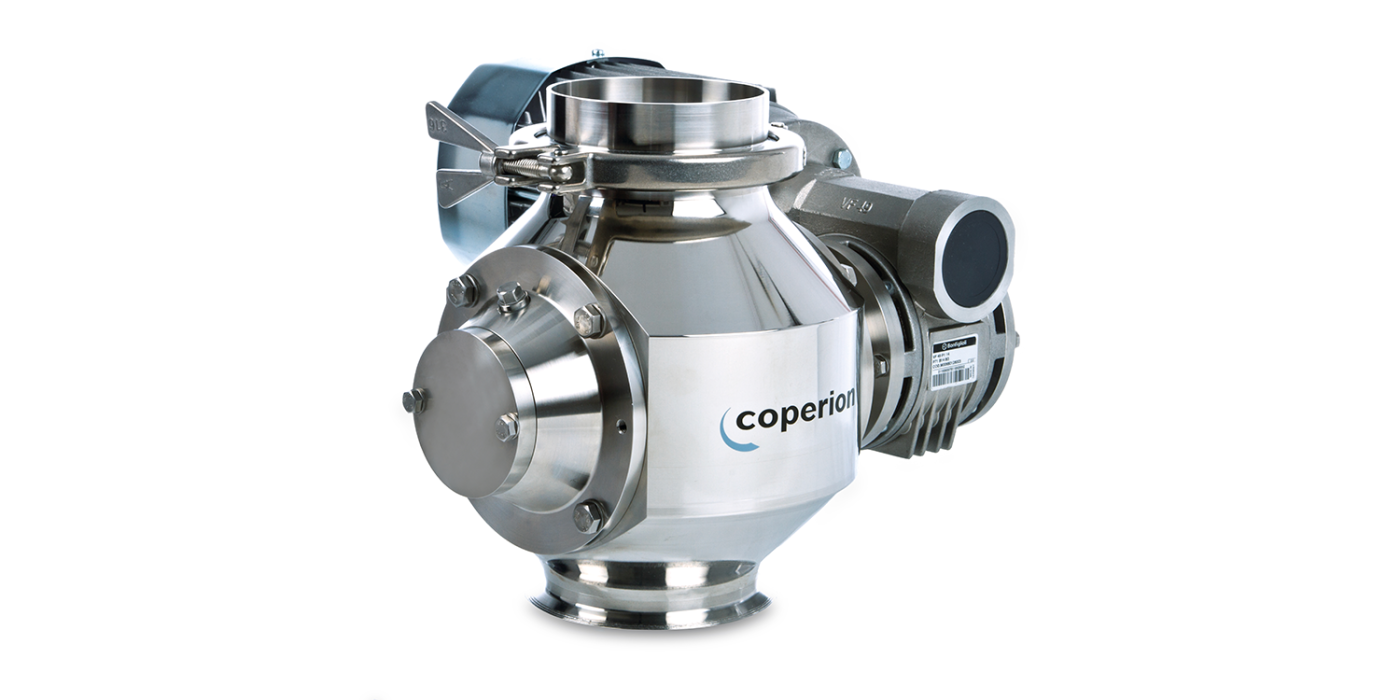
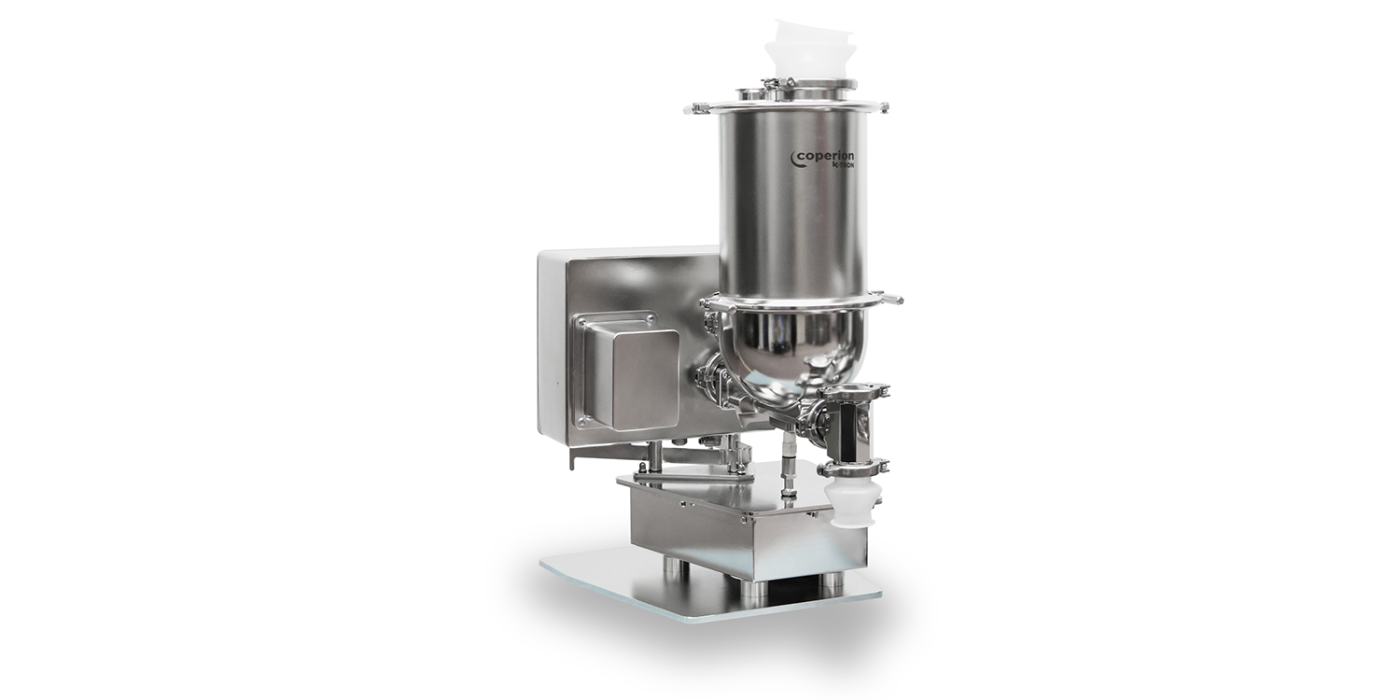
Gravimetric feeders from Coperion K-Tron seamlessly complement the set-up of the system. Raw materials such as active materials, binding agents, conductive carbon blacks and fluids are fed either separately or in the form of premixes into the process section of the extruders. The K3 feeders from Coperion K-Tron are characterized by their high accuracy and high reliability when it comes to hard-to-handle materials. Therefore, they are highly suitable for applications in the battery industry. Dust-proof versions of the feeding and refill systems for the raw materials are also available if required. The QT20 and QT35 twin screw feeders are suited for use with numerous bulk materials, including abrasive or toxic products. Their quick change design facilitates changes in formulation and thanks to the latest weighing and control technologies, they achieve very high feeding accuracy in both continuous and batch processes.
Coperion also offers pneumatic conveying solutions and other peripherals used in the manufacture of battery materials. From delivery of raw materials in sacks or containers to refilling the feeders over the extruder, Coperion can supply complete pneumatic conveying systems.
This article is a paid advertorial. The client is responsible for the content. If you are interested in booking an advertorial, please contact us via advertise@electrive.com.
0 Comments